Revolutionize your data communication projects with the USB to UART magic – a compact and efficient solution that connects your devices swiftly and flawlessly.
A
A
Hardware Overview
How does it work?
USB UART 5 Click is based on the CP2110, a single-chip HID USB to UART bridge controller from Silicon Labs. A USB function controller in the CP2110 is a USB 2.0-compliant, full-speed device with an integrated USB transceiver, one-time programmable ROM, and an asynchronous serial data bus (UART) in one compact package. The UART capabilities of the CP2110 include baud rate support from 300 to 1Mbps, hardware flow control, RS-485 support, and GPIO signals that are user-defined for status and control information. The USB function controller manages all data transfers between USB and UART, command requests generated by the USB host controller, and commands for controlling the function of the UARTs and GPIO pins. The CP2110 uses the standard USB HID device class, natively supported by most operating systems. A custom driver does
not need to be installed for this device. In addition, the CP2110 also supports USB Suspend and Resume modes for power management purposes. The CP2110 enters Suspend mode when Suspend signaling is detected on the bus using the SPD pin of the mikroBUS™ socket. Upon entering Suspend mode, the SPD signal is asserted, but it can also be asserted after a reset condition (RST pin) until device configuration during USB Enumeration is complete. SPD pin detects logic high level when the device is in the Suspend state and logic low when the device is in Normal mode, which is also visually indicated via red LED labeled as CONNECTED. This Click board™ also features 8 GPIO signals, located on unpopulated headers, that are user-defined for status and control information. Four GPIO signals support alternate features, including a configurable clock output
(CLK) from 24MHz to 47kHz, RS-485 transceiver control, and TX and RX LED toggle features. Also, the USB UART 5 Click can work in a USB-powered configuration thanks to the ability of the CP2110 to provide adequate power to all its parts with the help of an internal regulator using the USB bus voltage. To select this mode of operation, it is necessary to switch the jumper PWR SEL to the position marked with VBUS. This Click board™ can be operated only with a 3.3V logic voltage level. The board must perform appropriate logic voltage level conversion before using MCUs with different logic levels. Also, it comes equipped with a library containing functions and an example code that can be used as a reference for further development.
Features overview
Development board
UNI-DS v8 is a development board specially designed for the needs of rapid development of embedded applications. It supports a wide range of microcontrollers, such as different STM32, Kinetis, TIVA, CEC, MSP, PIC, dsPIC, PIC32, and AVR MCUs regardless of their number of pins, and a broad set of unique functions, such as the first-ever embedded debugger/programmer over WiFi. The development board is well organized and designed so that the end-user has all the necessary elements, such as switches, buttons, indicators, connectors, and others, in one place. Thanks to innovative manufacturing technology, UNI-DS v8 provides a fluid and immersive working experience, allowing access anywhere and under any
circumstances at any time. Each part of the UNI-DS v8 development board contains the components necessary for the most efficient operation of the same board. An advanced integrated CODEGRIP programmer/debugger module offers many valuable programming/debugging options, including support for JTAG, SWD, and SWO Trace (Single Wire Output)), and seamless integration with the Mikroe software environment. Besides, it also includes a clean and regulated power supply module for the development board. It can use a wide range of external power sources, including a battery, an external 12V power supply, and a power source via the USB Type-C (USB-C) connector. Communication options such as USB-UART, USB
HOST/DEVICE, CAN (on the MCU card, if supported), and Ethernet is also included. In addition, it also has the well-established mikroBUS™ standard, a standardized socket for the MCU card (SiBRAIN standard), and two display options for the TFT board line of products and character-based LCD. UNI-DS v8 is an integral part of the Mikroe ecosystem for rapid development. Natively supported by Mikroe software tools, it covers many aspects of prototyping and development thanks to a considerable number of different Click boards™ (over a thousand boards), the number of which is growing every day.
Microcontroller Overview
MCU Card / MCU
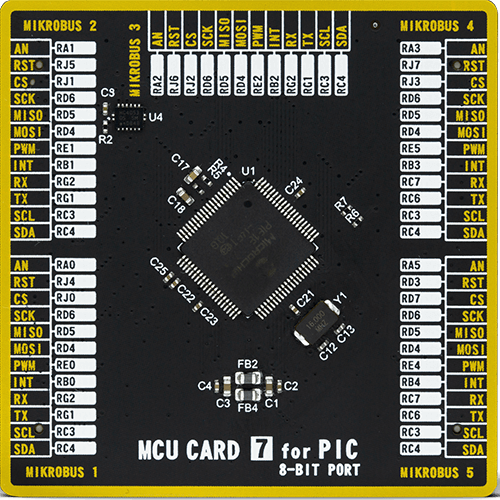
Type
8th Generation
Architecture
PIC
MCU Memory (KB)
64
Silicon Vendor
Microchip
Pin count
80
RAM (Bytes)
3904
Used MCU Pins
mikroBUS™ mapper
Take a closer look
Click board™ Schematic
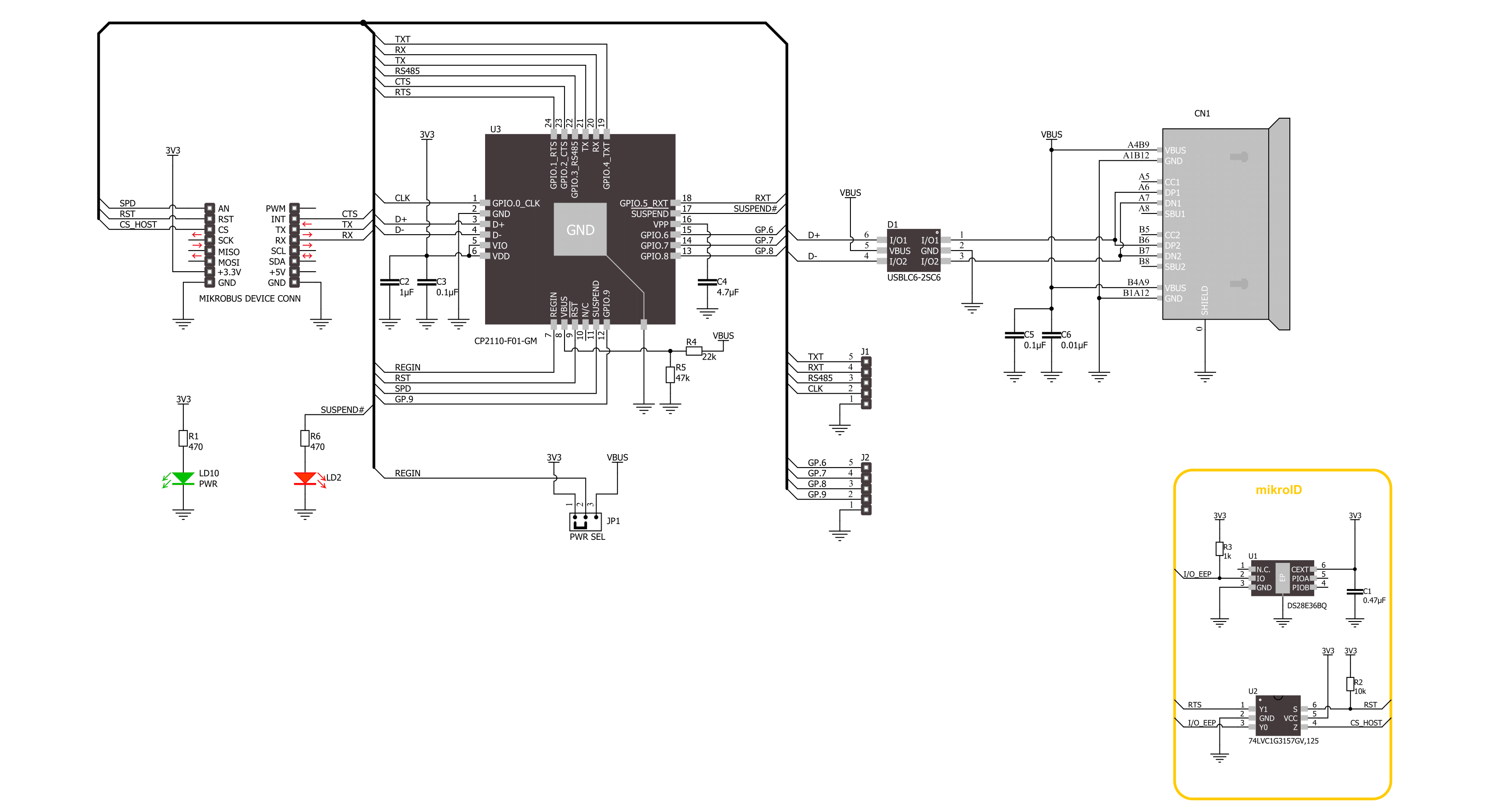
Step by step
Project assembly
Track your results in real time
Application Output
1. Application Output - In Debug mode, the 'Application Output' window enables real-time data monitoring, offering direct insight into execution results. Ensure proper data display by configuring the environment correctly using the provided tutorial.
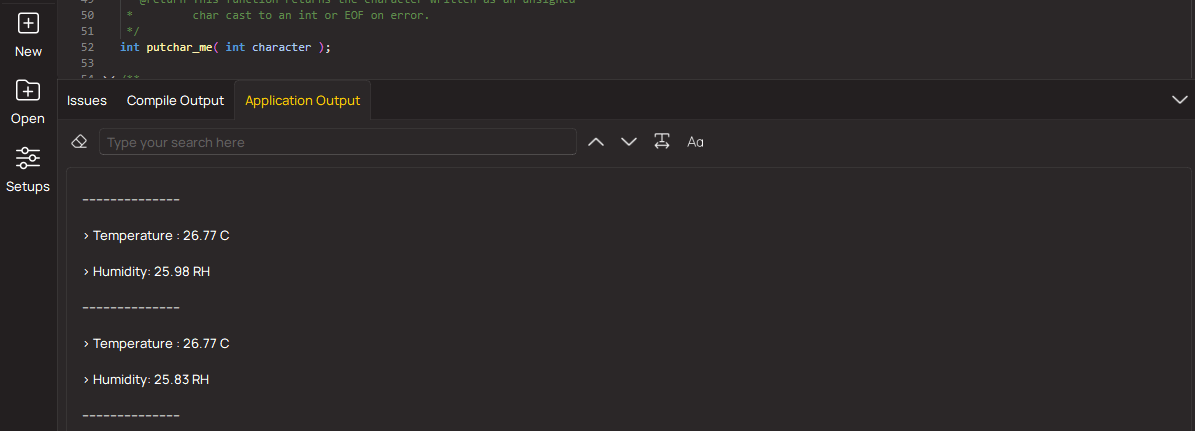
2. UART Terminal - Use the UART Terminal to monitor data transmission via a USB to UART converter, allowing direct communication between the Click board™ and your development system. Configure the baud rate and other serial settings according to your project's requirements to ensure proper functionality. For step-by-step setup instructions, refer to the provided tutorial.
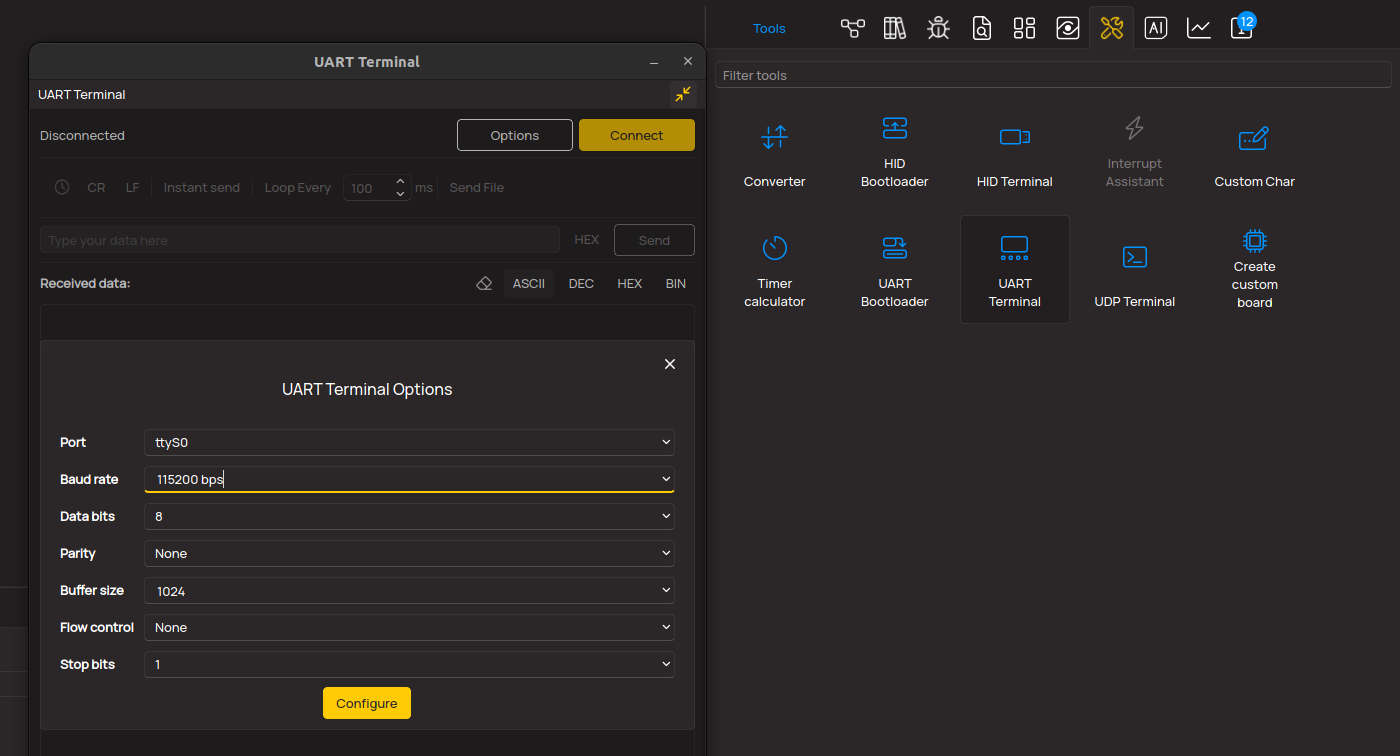
3. Plot Output - The Plot feature offers a powerful way to visualize real-time sensor data, enabling trend analysis, debugging, and comparison of multiple data points. To set it up correctly, follow the provided tutorial, which includes a step-by-step example of using the Plot feature to display Click board™ readings. To use the Plot feature in your code, use the function: plot(*insert_graph_name*, variable_name);. This is a general format, and it is up to the user to replace 'insert_graph_name' with the actual graph name and 'variable_name' with the parameter to be displayed.
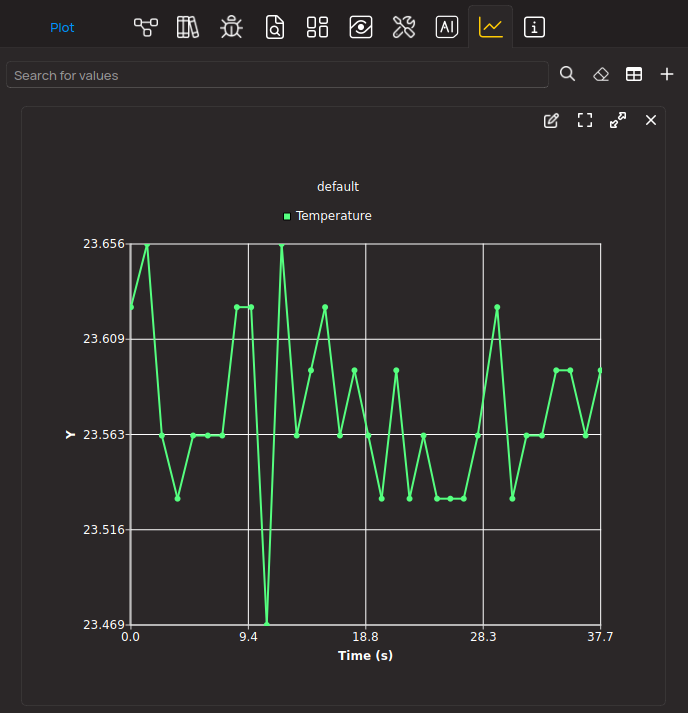
Software Support
Library Description
This library contains API for USB UART 5 Click driver.
Key functions:
usbuart5_generic_write
- USB UART 5 data writing function.usbuart5_generic_read
- USB UART 5 data reading function.usbuart5_reset_device
- USB UART 5 reset the device function.
Open Source
Code example
The complete application code and a ready-to-use project are available through the NECTO Studio Package Manager for direct installation in the NECTO Studio. The application code can also be found on the MIKROE GitHub account.
/*!
* @file main.c
* @brief USB UART 5 Click Example.
*
* # Description
* This example reads and processes data from USB UART 5 Click board™.
* The library initializes and defines the UART bus drivers
* to transmit or receive data.
*
* The demo application is composed of two sections :
*
* ## Application Init
* Initializes driver, wake-up module, and performs the default configuration.
*
* ## Application Task
* Any data which the host PC sends via HidUartExample
* will be sent over USB to the Click board and then it will be read and
* echoed back by the MCU to the PC where the terminal program will display it.
* Results are being sent to the UART Terminal, where you can track their changes.
*
* @note
* Make sure to download and install
* CP2110/4 Software package for Windows/Mac/Linux on the host PC.
*
* @author Nenad Filipovic
*
*/
#include "board.h"
#include "log.h"
#include "usbuart5.h"
static usbuart5_t usbuart5;
static log_t logger;
void application_init ( void )
{
log_cfg_t log_cfg; /**< Logger config object. */
usbuart5_cfg_t usbuart5_cfg; /**< Click config object. */
/**
* Logger initialization.
* Default baud rate: 115200
* Default log level: LOG_LEVEL_DEBUG
* @note If USB_UART_RX and USB_UART_TX
* are defined as HAL_PIN_NC, you will
* need to define them manually for log to work.
* See @b LOG_MAP_USB_UART macro definition for detailed explanation.
*/
LOG_MAP_USB_UART( log_cfg );
log_init( &logger, &log_cfg );
log_info( &logger, " Application Init " );
// Click initialization.
usbuart5_cfg_setup( &usbuart5_cfg );
USBUART5_MAP_MIKROBUS( usbuart5_cfg, MIKROBUS_1 );
if ( UART_ERROR == usbuart5_init( &usbuart5, &usbuart5_cfg ) )
{
log_error( &logger, " Communication init." );
for ( ; ; );
}
usbuart5_default_cfg ( &usbuart5 );
log_info( &logger, " Application Task " );
}
void application_task ( void )
{
char rx_data = 0;
if ( usbuart5_generic_read ( &usbuart5, &rx_data, 1 ) )
{
if ( usbuart5_generic_write ( &usbuart5, &rx_data, 1 ) )
{
log_printf( &logger, "%c", rx_data );
}
}
}
int main ( void )
{
/* Do not remove this line or clock might not be set correctly. */
#ifdef PREINIT_SUPPORTED
preinit();
#endif
application_init( );
for ( ; ; )
{
application_task( );
}
return 0;
}
// ------------------------------------------------------------------------ END