Ideal for sectors requiring long-distance, low-power communication, such as smart metering, supply chain and logistics, home automation, and security systems
A
A
Hardware Overview
How does it work?
LR 9 Click is based on the RA-08, a LoRaWAN module from Ai-Thinker Technology. This module is made for ultra-long-range spread spectrum communication tasks powered by the ASR6601. The ASR6601, an LPWAN wireless communication system-on-chip (SoC), combines RF transceivers, modems, and a 32-bit RISC microcontroller (MCU). The embedded MCU, leveraging an ARM core, operates at a frequency of 48MHz. The RA-08 is designed to work with LoRa modulation and the conventional (G)FSK modulation within the LPWAN domain. Furthermore, it supports BPSK and (G)MSK modulation for transmission, with the receiver accommodating (G)MSK modulation. Designed for LPWAN applications, the RA-08 module delivers long-distance, ultra-low power connectivity. It finds its applications in various sectors, including smart metering, supply chain and logistics management, building automation for homes, security systems, and remote-controlled
irrigation systems. Diving deeper into the specifics, the module supports a frequency range from 410MHz to 525MHz and can transmit at a maximum power of +22dBm. It boasts embedded storage with 128KB of FLASH and 16KB of SRAM, alongside support for several sleep modes, with a deep sleep current as low as 0.9uA. Additional functionalities of the LR 9 Click include communication capabilities with the host MCU via a UART interface, set by default to a baud rate of 115200bps. A switch on the board allows the selection of the UART interface's function—either as the main serial communication port for exchanging AT commands (in the LPRX position) or as a serial port for firmware flashing (in the RX position). Moreover, for developers looking to build their software from scratch, the module also includes I2C communication capabilities. The board does not limit itself to UART and I2C interface pins; it also features pins like the RST pin for module
resetting (which can also be achieved through a RESET button) and a BT pin for firmware flashing (accessible through a BOOT button). This frees programming and software development through the SWD interface pins on the board's right side. Also, an RGB LED serves as a module status indicator and is configurable by the user. LR 9 Click also features the SMA antenna connector with an impedance of 50Ω, compatible with various antennas available from MIKROE, like the Rubber Antenna 433MHz, to enhance its connectivity. This Click board™ can be operated only with a 3.3V logic voltage level. The board must perform appropriate logic voltage level conversion before using MCUs with different logic levels. Also, it comes equipped with a library containing functions and an example code that can be used as a reference for further development.
Features overview
Development board
Clicker 2 for Kinetis is a compact starter development board that brings the flexibility of add-on Click boards™ to your favorite microcontroller, making it a perfect starter kit for implementing your ideas. It comes with an onboard 32-bit ARM Cortex-M4F microcontroller, the MK64FN1M0VDC12 from NXP Semiconductors, two mikroBUS™ sockets for Click board™ connectivity, a USB connector, LED indicators, buttons, a JTAG programmer connector, and two 26-pin headers for interfacing with external electronics. Its compact design with clear and easily recognizable silkscreen markings allows you to build gadgets with unique functionalities and
features quickly. Each part of the Clicker 2 for Kinetis development kit contains the components necessary for the most efficient operation of the same board. In addition to the possibility of choosing the Clicker 2 for Kinetis programming method, using a USB HID mikroBootloader or an external mikroProg connector for Kinetis programmer, the Clicker 2 board also includes a clean and regulated power supply module for the development kit. It provides two ways of board-powering; through the USB Micro-B cable, where onboard voltage regulators provide the appropriate voltage levels to each component on the board, or
using a Li-Polymer battery via an onboard battery connector. All communication methods that mikroBUS™ itself supports are on this board, including the well-established mikroBUS™ socket, reset button, and several user-configurable buttons and LED indicators. Clicker 2 for Kinetis is an integral part of the Mikroe ecosystem, allowing you to create a new application in minutes. Natively supported by Mikroe software tools, it covers many aspects of prototyping thanks to a considerable number of different Click boards™ (over a thousand boards), the number of which is growing every day.
Microcontroller Overview
MCU Card / MCU
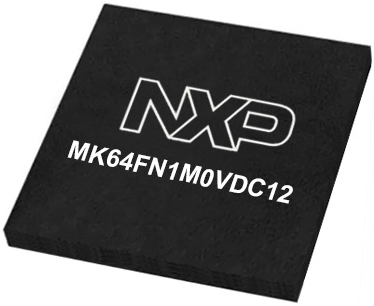
Architecture
ARM Cortex-M4
MCU Memory (KB)
1024
Silicon Vendor
NXP
Pin count
121
RAM (Bytes)
262144
You complete me!
Accessories
Right angle 433MHz rubber antenna boasts a frequency range of 433MHz, ensuring optimal performance within this spectrum. With a 50Ohm impedance, it facilitates efficient signal transmission. The antenna's vertical polarization enhances signal reception in a specific orientation. Featuring a 1.5dB gain, it can improve signal strength to some extent. The antenna can handle a maximum input power of 50W, making it suitable for various applications. Its compact 50mm length minimizes spatial requirements. Equipped with an SMA male connector, it easily interfaces with compatible devices. This antenna is an adaptable solution for wireless communication needs, particularly when vertical polarization is crucial.
Used MCU Pins
mikroBUS™ mapper
Take a closer look
Click board™ Schematic
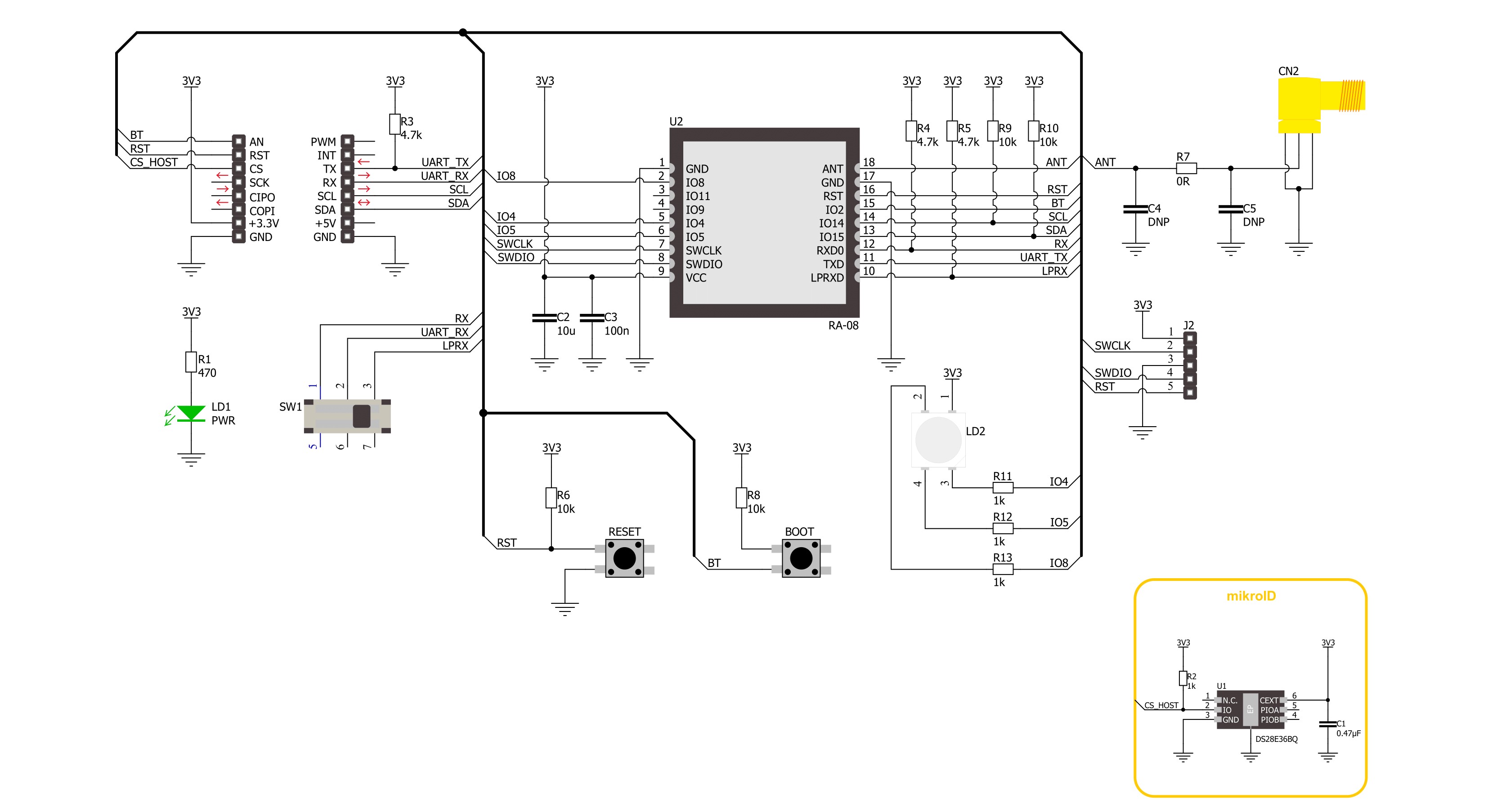
Step by step
Project assembly
Track your results in real time
Application Output
1. Application Output - In Debug mode, the 'Application Output' window enables real-time data monitoring, offering direct insight into execution results. Ensure proper data display by configuring the environment correctly using the provided tutorial.
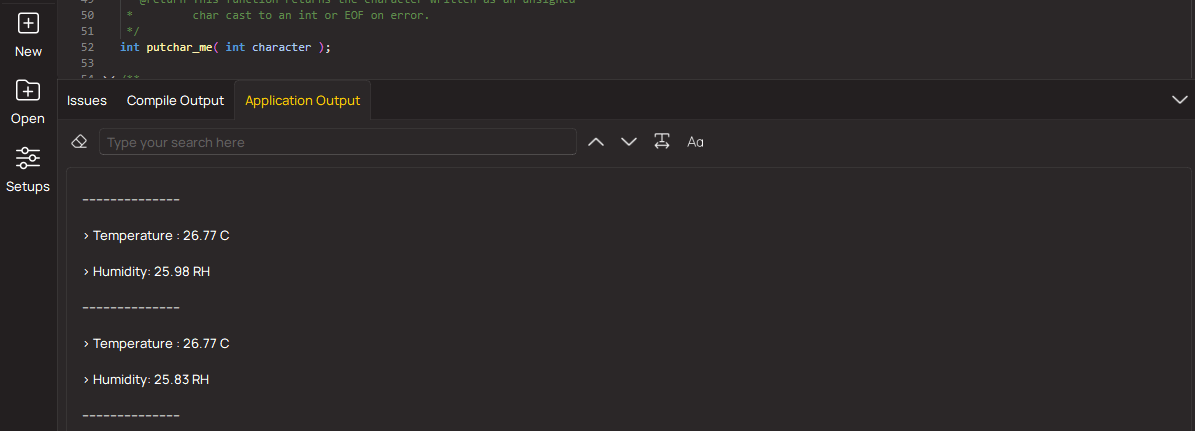
2. UART Terminal - Use the UART Terminal to monitor data transmission via a USB to UART converter, allowing direct communication between the Click board™ and your development system. Configure the baud rate and other serial settings according to your project's requirements to ensure proper functionality. For step-by-step setup instructions, refer to the provided tutorial.
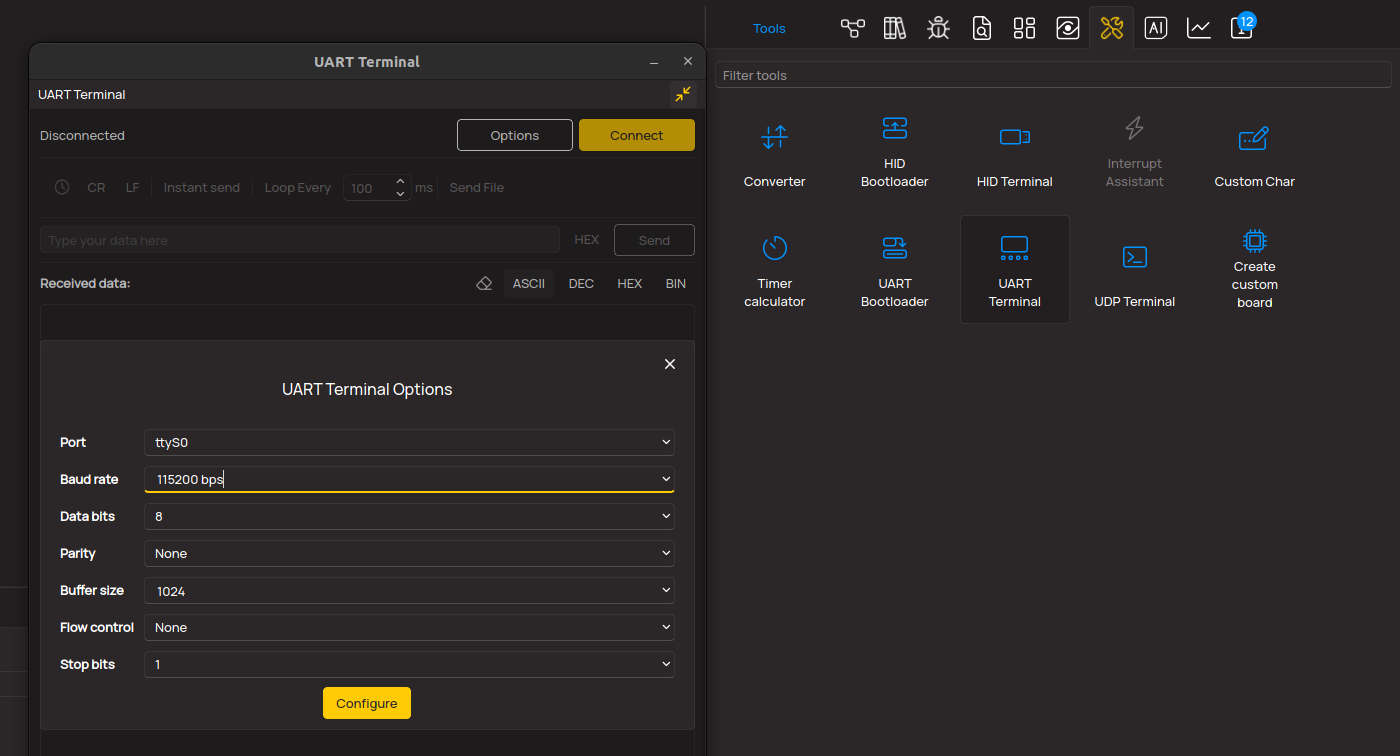
3. Plot Output - The Plot feature offers a powerful way to visualize real-time sensor data, enabling trend analysis, debugging, and comparison of multiple data points. To set it up correctly, follow the provided tutorial, which includes a step-by-step example of using the Plot feature to display Click board™ readings. To use the Plot feature in your code, use the function: plot(*insert_graph_name*, variable_name);. This is a general format, and it is up to the user to replace 'insert_graph_name' with the actual graph name and 'variable_name' with the parameter to be displayed.
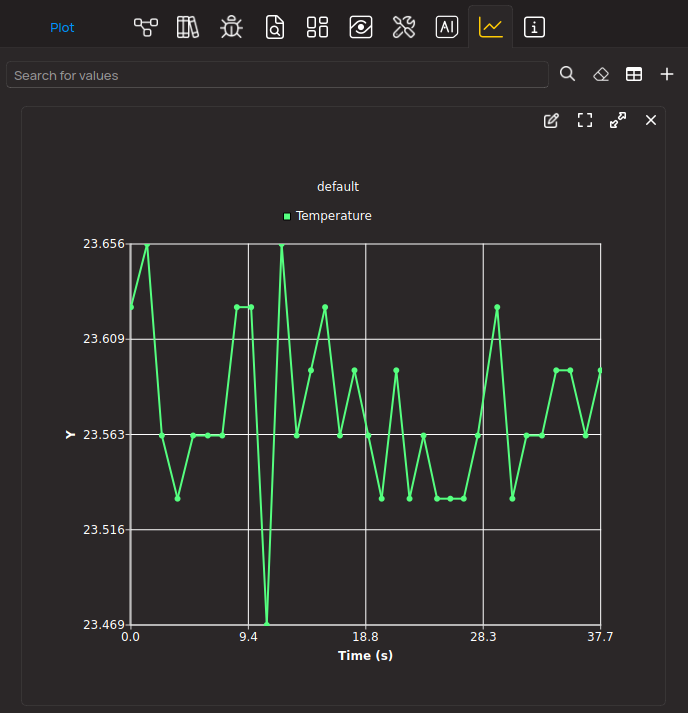
Software Support
Library Description
This library contains API for LR 9 Click driver.
Key functions:
lr9_send_data_frame
- This function sends the desired data frame by using the UART serial interfacelr9_inquire_command
- Using the UART serial interface, this function writes the desired query command with or without the included equals symbollr9_write_command
- This function writes a desired command and parameter by using the UART serial interface
Open Source
Code example
The complete application code and a ready-to-use project are available through the NECTO Studio Package Manager for direct installation in the NECTO Studio. The application code can also be found on the MIKROE GitHub account.
/*!
* @file main.c
* @brief LR 9 Click Example.
*
* # Description
* This example demonstrates the use of LR 9 Click board by processing
* the incoming data and displaying them on the USB UART.
*
* The demo application is composed of two sections :
*
* ## Application Init
* Initializes the driver and performs a hardware reset of the device.
*
* ## Application Task
* Depending on the selected mode, the application demo
* receives and processes all incoming data or sends the LoRa packet demo string.
* Results are being sent to the UART Terminal, where you can track their changes.
*
* ## Additional Function
* - static void lr9_clear_app_buf ( void )
* - static void lr9_log_app_buf ( void )
* - static void lr9_log_receiver ( void )
* - static void lr9_log_response ( void )
* - static err_t lr9_process ( lr9_t *ctx )
*
* @author Nenad Filipovic
*
*/
#include "board.h"
#include "log.h"
#include "lr9.h"
#include "conversions.h"
// Comment the line below to switch application mode to receiver
#define DEMO_APP_TRANSMITTER
// Default RF configuration
#define LR9_RF_CFG_DEFAULT_TX "433000000,1,1,1,22,1"
#define LR9_RF_CFG_DEFAULT_RX "433000000,1,1,1,1"
#define LR9_DEMO_STRING "MikroE"
// Receiver string sequences
#define PROCESS_START_RECEIVE "Recv:"
#define PROCESS_ATDTRX "AT"
// Response timeout
#define RESPONSE_TIMEOUT 100000
// Application buffer size
#define APP_BUFFER_SIZE 500
#define PROCESS_BUFFER_SIZE 200
static lr9_t lr9;
static log_t logger;
static uint8_t app_buf[ APP_BUFFER_SIZE ] = { 0 };
static int32_t app_buf_len = 0;
/**
* @brief LR 9 clearing application buffer.
* @details This function clears memory of application buffer and reset its length.
* @note None.
*/
static void lr9_clear_app_buf ( void );
/**
* @brief LR 9 log application buffer.
* @details This function logs data from application buffer to USB UART.
* @note None.
*/
static void lr9_log_app_buf ( void );
/**
* @brief LR 9 log receiver data.
* @details This function logs data from receiver application buffer to USB UART.
* @note None.
*/
static void lr9_log_receiver ( void );
/**
* @brief LR 9 log response.
* @details This function reads data from device and
* concatenates and logs data to application buffer to USB UART.
* @note None.
*/
static void lr9_log_response ( void );
/**
* @brief LR 9 data reading function.
* @details This function reads data from device and concatenates data to application buffer.
* @param[in] ctx : Click context object.
* See #lr9_t object definition for detailed explanation.
* @return @li @c 0 - Read some data.
* @li @c -1 - Nothing is read.
* See #err_t definition for detailed explanation.
* @note None.
*/
static err_t lr9_process ( lr9_t *ctx );
void application_init ( void )
{
log_cfg_t log_cfg; /**< Logger config object. */
lr9_cfg_t lr9_cfg; /**< Click config object. */
/**
* Logger initialization.
* Default baud rate: 115200
* Default log level: LOG_LEVEL_DEBUG
* @note If USB_UART_RX and USB_UART_TX
* are defined as HAL_PIN_NC, you will
* need to define them manually for log to work.
* See @b LOG_MAP_USB_UART macro definition for detailed explanation.
*/
LOG_MAP_USB_UART( log_cfg );
log_init( &logger, &log_cfg );
log_info( &logger, " Application Init " );
// Click initialization.
lr9_cfg_setup( &lr9_cfg );
LR9_MAP_MIKROBUS( lr9_cfg, MIKROBUS_1 );
if ( UART_ERROR == lr9_init( &lr9, &lr9_cfg ) )
{
log_error( &logger, " Communication init." );
for ( ; ; );
}
lr9_hw_reset( &lr9 );
Delay_ms ( 500 );
lr9_inquire_command( &lr9, LR9_CMD_CTXADDRSET, LR9_EQUAL_ENABLE );
lr9_log_response( );
Delay_ms ( 500 );
lr9_inquire_command( &lr9, LR9_CMD_CADDRSET, LR9_EQUAL_ENABLE );
lr9_log_response( );
Delay_ms ( 500 );
#ifdef DEMO_APP_TRANSMITTER
log_printf( &logger, " > Transmitter < \r\n" );
lr9_write_command( &lr9, LR9_CMD_CTX , LR9_RF_CFG_DEFAULT_TX );
lr9_log_response( );
Delay_ms ( 500 );
#else
log_printf( &logger, " > Receiver < \r\n" );
lr9_write_command( &lr9, LR9_CMD_CRXS , LR9_RF_CFG_DEFAULT_RX );
lr9_log_response( );
Delay_ms ( 500 );
#endif
lr9_log_response( );
Delay_ms ( 500 );
}
void application_task ( void )
{
#ifdef DEMO_APP_TRANSMITTER
lr9_send_data_frame( &lr9, LR9_DTRX_CONFIG_DATA, LR9_NB_TRIALS_2, LR9_DEMO_STRING );
lr9_log_response( );
Delay_ms ( 1000 );
Delay_ms ( 1000 );
#else
lr9_log_receiver( );
#endif
}
int main ( void )
{
/* Do not remove this line or clock might not be set correctly. */
#ifdef PREINIT_SUPPORTED
preinit();
#endif
application_init( );
for ( ; ; )
{
application_task( );
}
return 0;
}
static void lr9_clear_app_buf ( void )
{
memset( app_buf, 0, app_buf_len );
app_buf_len = 0;
}
static void lr9_log_app_buf ( void )
{
for ( int32_t buf_cnt = 0; buf_cnt < app_buf_len; buf_cnt++ )
{
log_printf( &logger, "%c", app_buf[ buf_cnt ] );
}
}
static void lr9_log_receiver ( void )
{
uint32_t timeout_cnt = 0;
lr9_clear_app_buf( );
lr9_process( &lr9 );
while ( 0 == strstr( app_buf, PROCESS_START_RECEIVE ) )
{
lr9_process( &lr9 );
if ( timeout_cnt++ > RESPONSE_TIMEOUT )
{
lr9_clear_app_buf( );
log_printf( &logger, " Timeout\r\n" );
break;
}
Delay_ms ( 1 );
}
lr9_process( &lr9 );
if ( strstr( app_buf, PROCESS_ATDTRX ) )
{
log_printf( &logger, " Receive: " );
for ( int32_t buf_cnt = 15; buf_cnt < 15 + strlen( LR9_DEMO_STRING ); buf_cnt++ )
{
log_printf( &logger, "%c", app_buf[ buf_cnt ] );
}
log_printf( &logger, "\r\n" );
}
lr9_clear_app_buf( );
}
static void lr9_log_response ( void )
{
if ( LR9_OK == lr9_process( &lr9 ) )
{
lr9_log_app_buf( );
lr9_clear_app_buf( );
}
}
static err_t lr9_process ( lr9_t *ctx )
{
uint8_t rx_buf[ PROCESS_BUFFER_SIZE ] = { 0 };
int32_t overflow_bytes = 0;
int32_t rx_cnt = 0;
int32_t rx_size = lr9_generic_read( ctx, rx_buf, PROCESS_BUFFER_SIZE );
if ( ( rx_size > 0 ) && ( rx_size <= APP_BUFFER_SIZE ) )
{
if ( ( app_buf_len + rx_size ) > APP_BUFFER_SIZE )
{
overflow_bytes = ( app_buf_len + rx_size ) - APP_BUFFER_SIZE;
app_buf_len = APP_BUFFER_SIZE - rx_size;
memmove ( app_buf, &app_buf[ overflow_bytes ], app_buf_len );
memset ( &app_buf[ app_buf_len ], 0, overflow_bytes );
}
for ( rx_cnt = 0; rx_cnt < rx_size; rx_cnt++ )
{
if ( rx_buf[ rx_cnt ] )
{
app_buf[ app_buf_len++ ] = rx_buf[ rx_cnt ];
}
}
return LR9_OK;
}
return LR9_ERROR;
}
// ------------------------------------------------------------------------ END