Our 6DoF IMU solution is designed to revolutionize motion tracking, offering unparalleled accuracy and responsiveness for a wide range of applications
A
A
Hardware Overview
How does it work?
6DOF IMU 12 Click is based on the BMI270, an ultra-low-power IMU optimized for wearable applications from Bosch Sensortec. The IMU combines precise acceleration and angular rate measurement with intelligent on-chip motion-triggered interrupt features. The 6-axis sensor combines a 16-bit triaxial gyroscope and a 16-bit triaxial accelerometer in a compact 2.5x3.0x0.8mm LGA package. BMI270 is a member of Bosch Sensortec’s BMI260 family of IMUs, targeting fast and accurate inertial sensing in wearable applications. It also features Bosch’s automotive-proven gyroscope technology with an improved accelerometer. Significant improvements in BMI270 include, but are not restricted to, the overall accelerometer performance, i.e. an extremely low zero-g offset and sensitivity error, low temperature drifts, robustness over PCB strain and a low noise density. It also features the industry’s first self-calibrating gyroscope using motionless CRT (Component Re-Trimming) functionality to compensate MEMS typical soldering drifts, ensuring post-soldering sensitivity
errors down to ± 0.4%. BMI270 includes intuitive gesture, context and activity recognition with an integrated plug-and-play step counter/detector, which is optimized for accurate step counting in wrist-worn devices. The IMU is also well suited for other types of wearable devices, such as hearables, smart clothes, smart shoes, smart glasses and ankle bands. The smart IMU has a wide range for VDD and VDDIO supply voltages. The performance and current consumption are stable over the entire supply range. Typical current draw for BMI270’s accelerometer and gyroscope at full ODR of 6.4 kHz is under 700μA. By enabling high output data rates with low current consumption, wearable manufacturers can avoid an unpleasant aliasing effect – an effect that causes different signals to become indistinguishable when sampled at lower ODRs. Bosch Sensortec’s ultra-low-power IMU BMI270 provides an intelligent power management system enabling motion-triggered always-on features to run inside the ultra-low-power domain of the IMU. BMI270 significantly extends system battery life by
handling multiple activity tracking, step counting and gesture recognition functions independently of the main system processor, without having to wake it up. The processor-independent functions include tasks such as sending an interrupt when a certain number of steps is reached, or geofencing to activate GPS when the user stands up and starts walking. The device features I2C and SPI serial interfaces, a VDD operating range from 1.71V to 3.6V, and a separate digital IO supply (VDDIO) from 1.2V to 3.6V. Communication with all registers of the device can be performed using either SPI at 10MHz or I2C at up to 1MHz. 6DOF IMU 12 Click supports both SPI and I2C communication interfaces, allowing it to be used with a wide range of different MCUs. The communication interface can be selected by moving SMD jumpers grouped under the COM SEL to an appropriate position (SPI or I2C). The slave I2C address can also be configured by an SMD jumper when the Click board™ is operated in the I2C mode. An SMD jumper labeled as ADD SEL is used to set the least significant bit (LSB) of the I2C address.
Features overview
Development board
Fusion for TIVA v8 is a development board specially designed for the needs of rapid development of embedded applications. It supports a wide range of microcontrollers, such as different 32-bit ARM® Cortex®-M based MCUs from Texas Instruments, regardless of their number of pins, and a broad set of unique functions, such as the first-ever embedded debugger/programmer over a WiFi network. The development board is well organized and designed so that the end-user has all the necessary elements, such as switches, buttons, indicators, connectors, and others, in one place. Thanks to innovative manufacturing technology, Fusion for TIVA v8 provides a fluid and immersive working experience, allowing access
anywhere and under any circumstances at any time. Each part of the Fusion for TIVA v8 development board contains the components necessary for the most efficient operation of the same board. An advanced integrated CODEGRIP programmer/debugger module offers many valuable programming/debugging options, including support for JTAG, SWD, and SWO Trace (Single Wire Output)), and seamless integration with the Mikroe software environment. Besides, it also includes a clean and regulated power supply module for the development board. It can use a wide range of external power sources, including a battery, an external 12V power supply, and a power source via the USB Type-C (USB-C) connector.
Communication options such as USB-UART, USB HOST/DEVICE, CAN (on the MCU card, if supported), and Ethernet is also included. In addition, it also has the well-established mikroBUS™ standard, a standardized socket for the MCU card (SiBRAIN standard), and two display options for the TFT board line of products and character-based LCD. Fusion for TIVA v8 is an integral part of the Mikroe ecosystem for rapid development. Natively supported by Mikroe software tools, it covers many aspects of prototyping and development thanks to a considerable number of different Click boards™ (over a thousand boards), the number of which is growing every day.
Microcontroller Overview
MCU Card / MCU
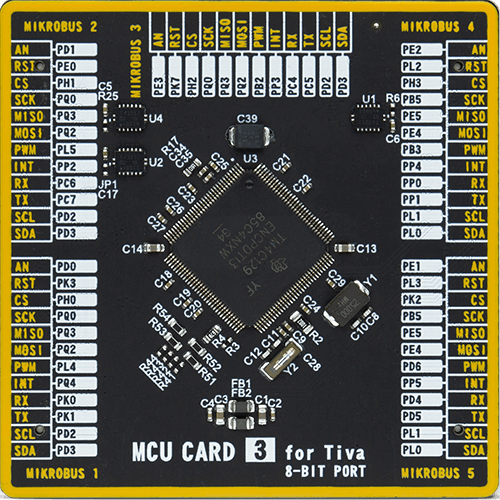
Type
8th Generation
Architecture
ARM Cortex-M4
MCU Memory (KB)
1024
Silicon Vendor
Texas Instruments
Pin count
128
RAM (Bytes)
262144
Used MCU Pins
mikroBUS™ mapper
Take a closer look
Click board™ Schematic
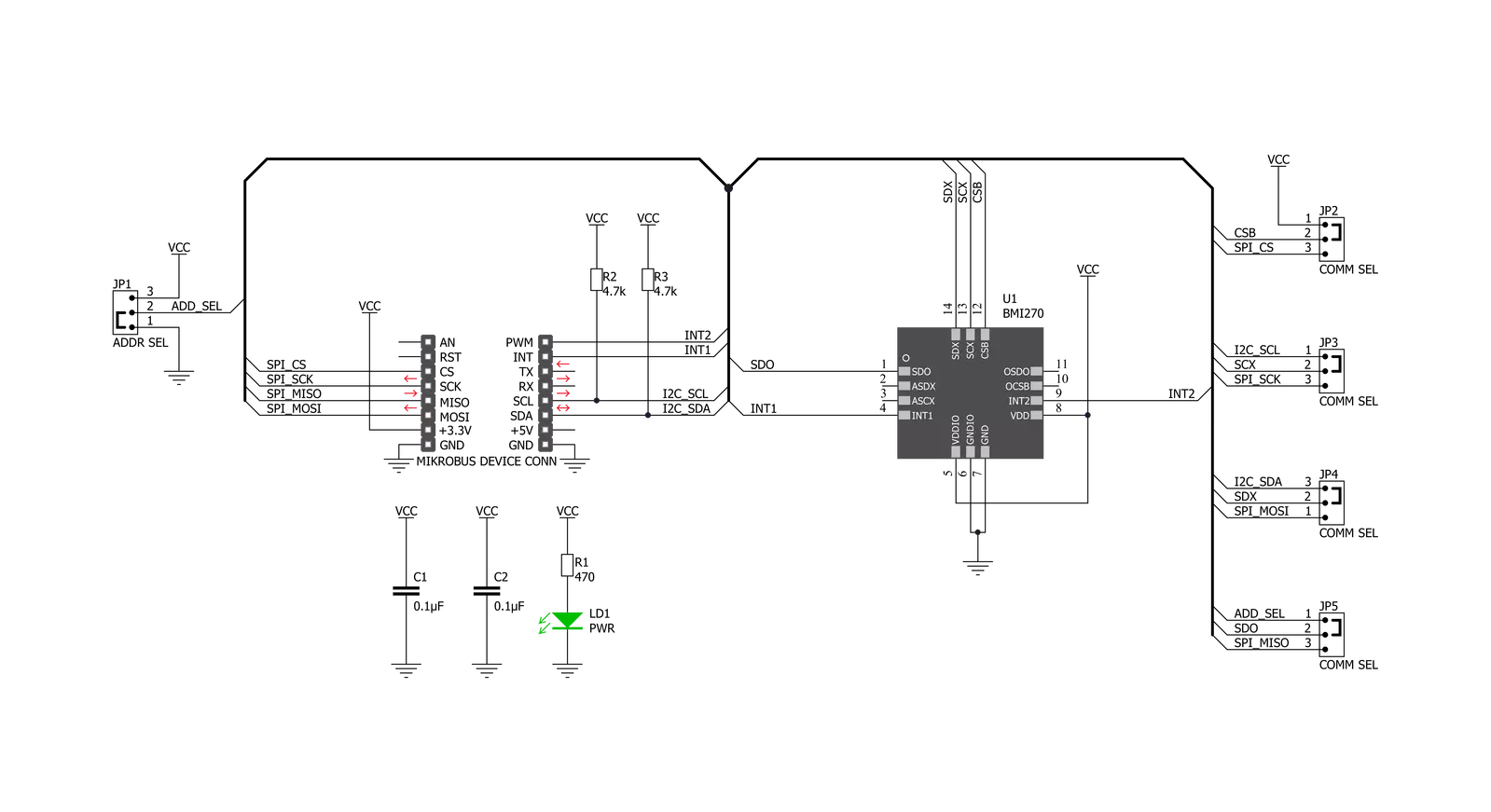
Step by step
Project assembly
Track your results in real time
Application Output
1. Application Output - In Debug mode, the 'Application Output' window enables real-time data monitoring, offering direct insight into execution results. Ensure proper data display by configuring the environment correctly using the provided tutorial.
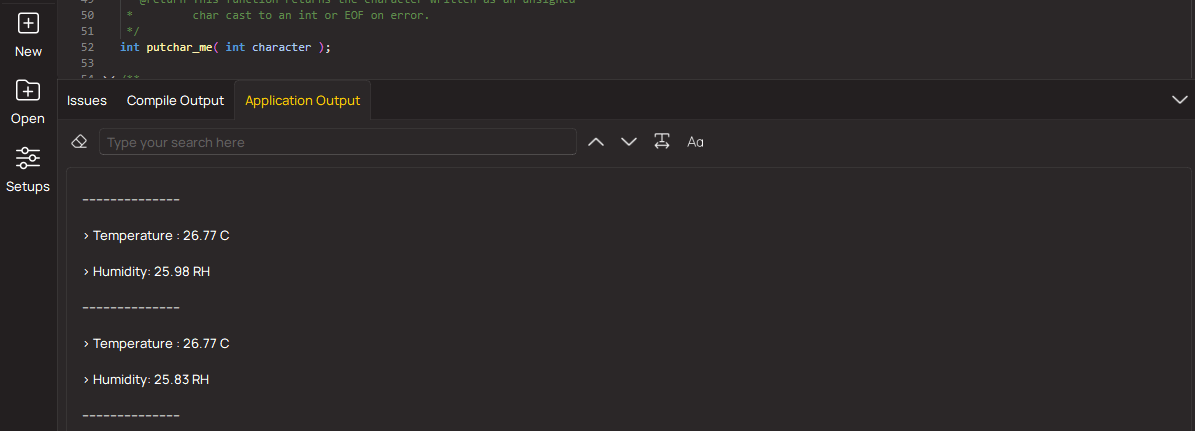
2. UART Terminal - Use the UART Terminal to monitor data transmission via a USB to UART converter, allowing direct communication between the Click board™ and your development system. Configure the baud rate and other serial settings according to your project's requirements to ensure proper functionality. For step-by-step setup instructions, refer to the provided tutorial.
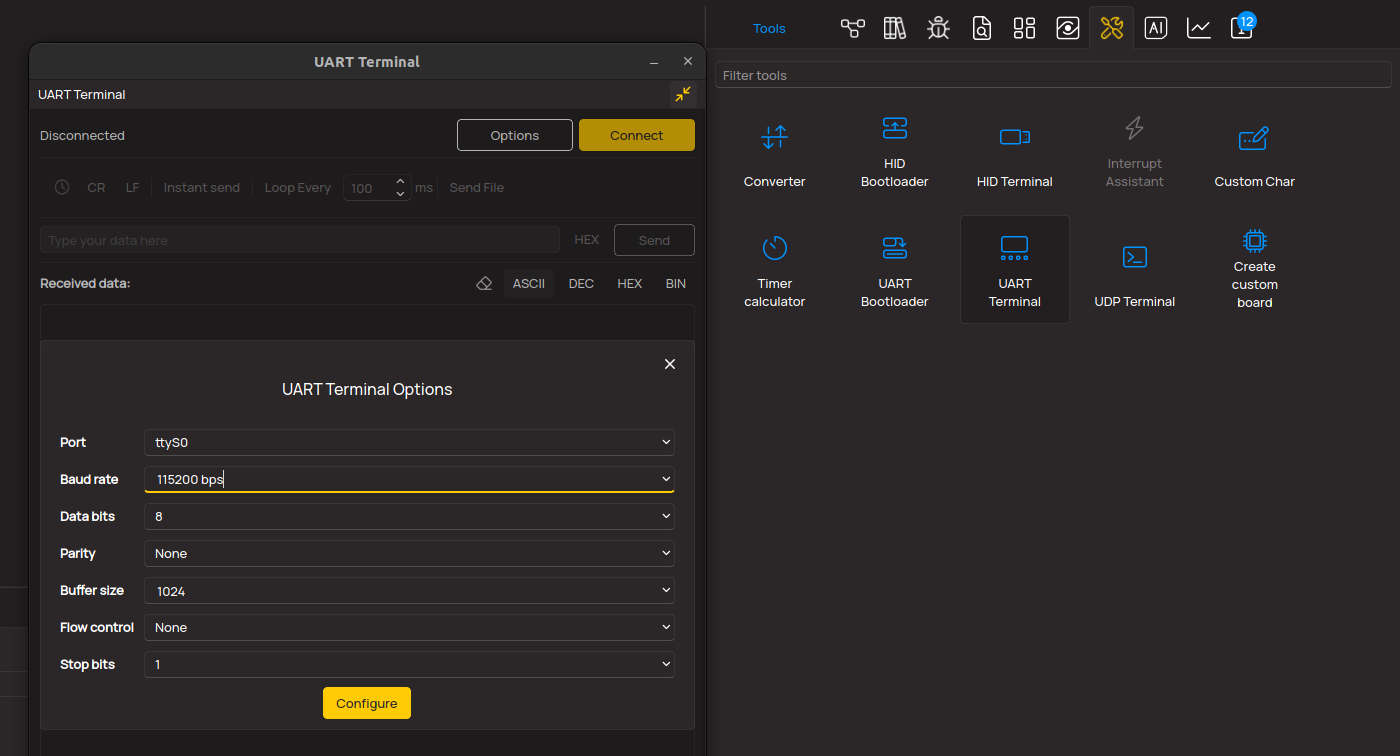
3. Plot Output - The Plot feature offers a powerful way to visualize real-time sensor data, enabling trend analysis, debugging, and comparison of multiple data points. To set it up correctly, follow the provided tutorial, which includes a step-by-step example of using the Plot feature to display Click board™ readings. To use the Plot feature in your code, use the function: plot(*insert_graph_name*, variable_name);. This is a general format, and it is up to the user to replace 'insert_graph_name' with the actual graph name and 'variable_name' with the parameter to be displayed.
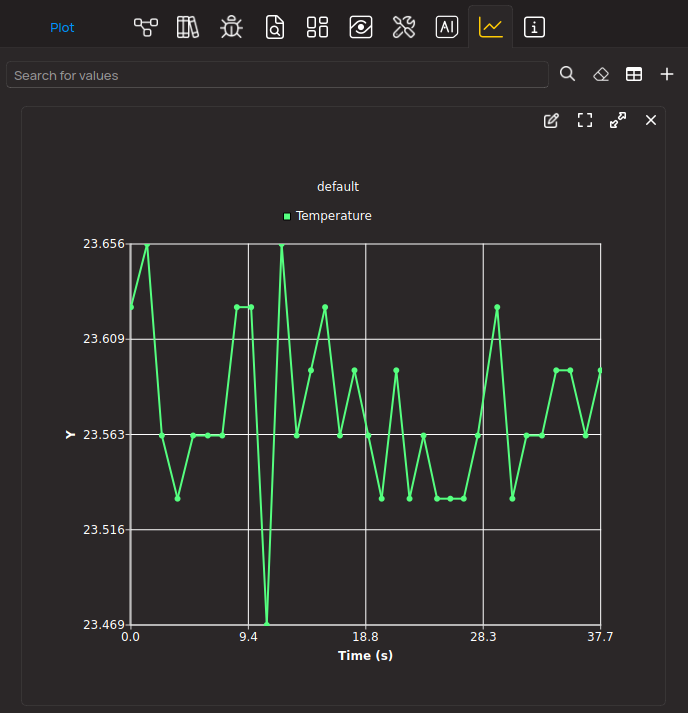
Software Support
Library Description
This library contains API for 6DOF IMU 12 Click driver.
Key functions:
c6dofimu12_check_id
- Function check status initialization of the device of BMI270 6-axis, smart, low-power Inertial Measurement on 6DOF IMU 12 Clickc6dofimu12_check_init_status
- Function check status initialization of the device of BMI270 6-axis, smart, low-power Inertial Measurement on 6DOF IMU 12 Clickc6dofimu12_get_data
- Function reads Accel and Gyro 16-bit ( signed ) X-axis, Y-axis data and Z-axis data from the 12 targeted starts from C6DOFIMU12_REG_ACC_X_LSB_ADDR register address of BMI270 6-axis, smart, low-power Inertial Measurement on 6DOF IMU 12 Click
Open Source
Code example
The complete application code and a ready-to-use project are available through the NECTO Studio Package Manager for direct installation in the NECTO Studio. The application code can also be found on the MIKROE GitHub account.
/*!
* \file
* \brief C6DofImu12 Click example
*
* # Description
* This example demonstrates the use of 6DOF IMU 12 Click board.
*
* The demo application is composed of two sections :
*
* ## Application Init
* Initializes the driver and checks the communication then initializes the device
* and sets the device default configuration.
*
* ## Application Task
* Measures acceleration and gyroscope data and displays the results on USB UART each second.
*
* \author MikroE Team
*
*/
// ------------------------------------------------------------------- INCLUDES
#include "board.h"
#include "log.h"
#include "c6dofimu12.h"
#include "c6dofimu12_config.h"
// ------------------------------------------------------------------ VARIABLES
static c6dofimu12_t c6dofimu12;
static c6dofimu12_accel_t c6dofimu12_accel;
static c6dofimu12_gyro_t c6dofimu12_gyro;
static log_t logger;
// ------------------------------------------------------ APPLICATION FUNCTIONS
void application_init ( void )
{
uint8_t tx_buf;
log_cfg_t log_cfg;
c6dofimu12_cfg_t cfg;
/**
* Logger initialization.
* Default baud rate: 115200
* Default log level: LOG_LEVEL_DEBUG
* @note If USB_UART_RX and USB_UART_TX
* are defined as HAL_PIN_NC, you will
* need to define them manually for log to work.
* See @b LOG_MAP_USB_UART macro definition for detailed explanation.
*/
LOG_MAP_USB_UART( log_cfg );
log_init( &logger, &log_cfg );
log_info( &logger, "---- Application Init ----" );
// Click initialization.
c6dofimu12_cfg_setup( &cfg );
C6DOFIMU12_MAP_MIKROBUS( cfg, MIKROBUS_1 );
c6dofimu12_init( &c6dofimu12, &cfg );
Delay_ms ( 100 );
log_printf( &logger, " Driver init done \r\n" );
log_printf( &logger, "----------------------------------\r\n");
if ( c6dofimu12_check_id( &c6dofimu12 ) == C6DOFIMU12_SUCCESS )
{
log_printf( &logger, " Communication OK\r\n" );
log_printf( &logger, "----------------------------------\r\n");
}
else
{
log_printf( &logger, " Communication ERROR\r\n" );
log_printf( &logger, " Reset the device\r\n" );
log_printf( &logger, "----------------------------------\r\n");
for ( ; ; );
}
tx_buf = C6DOFIMU12_PWR_CONF_ADV_PWR_SAVE_DISABLED |
C6DOFIMU12_FIFO_READ_DISABLED |
C6DOFIMU12_FAST_PWR_UP_DISABLED;
c6dofimu12_generic_write( &c6dofimu12, C6DOFIMU12_REG_PWR_CONF_ADDR, &tx_buf, 1 );
Delay_ms ( 100 );
tx_buf = C6DOFIMU12_CMD_INITIALIZATION_START;
c6dofimu12_generic_write( &c6dofimu12, C6DOFIMU12_REG_INIT_CTRL_ADDR, &tx_buf, 1 );
Delay_ms ( 100 );
c6dofimu12_generic_write( &c6dofimu12, C6DOFIMU12_REG_INIT_DATA_ADDR, bmi270_config_file, 8192 );
Delay_ms ( 100 );
tx_buf = C6DOFIMU12_CMD_INITIALIZATION_STOP;
c6dofimu12_generic_write( &c6dofimu12, C6DOFIMU12_REG_INIT_CTRL_ADDR, &tx_buf, 1 );
Delay_ms ( 100 );
if ( c6dofimu12_check_init_status( &c6dofimu12 ) == C6DOFIMU12_SUCCESS )
{
log_printf( &logger, " Initialization completed\r\n" );
log_printf( &logger, "----------------------------------\r\n");
}
else
{
log_printf( &logger, " Initialization ERROR\r\n" );
log_printf( &logger, " Reset the device\r\n" );
log_printf( &logger, "----------------------------------\r\n");
for( ; ; );
}
c6dofimu12_default_cfg( &c6dofimu12 );
Delay_ms ( 100 );
}
void application_task ( void )
{
c6dofimu12_get_data( &c6dofimu12, &c6dofimu12_accel, &c6dofimu12_gyro );
log_printf( &logger, " Accel X: %d | Gyro X: %d\r\n", c6dofimu12_accel.x, c6dofimu12_gyro.x );
log_printf( &logger, " Accel Y: %d | Gyro Y: %d\r\n", c6dofimu12_accel.y, c6dofimu12_gyro.y );
log_printf( &logger, " Accel Z: %d | Gyro Z: %d\r\n", c6dofimu12_accel.z, c6dofimu12_gyro.z );
log_printf( &logger, "----------------------------------\r\n");
Delay_ms ( 1000 );
}
int main ( void )
{
/* Do not remove this line or clock might not be set correctly. */
#ifdef PREINIT_SUPPORTED
preinit();
#endif
application_init( );
for ( ; ; )
{
application_task( );
}
return 0;
}
// ------------------------------------------------------------------------ END