With our 915MHz transceiver, you can unlock new possibilities in agriculture, environmental monitoring, and industrial control, thanks to their exceptional range and penetration capabilities.
A
A
Hardware Overview
How does it work?
LR 2 Click is based on the RN2903, a low-power, long-range RF technology-based transceiver module from Microchip Technology. It features the Class A LoRaWAN compliant stack, optimized for robust LoRaWAN networking, immune to interferences, and suitable for long-range wireless operation. It offers a long-range spread spectrum communication with high interference immunity. A receiver with a sensitivity of -148dBm combined with the 18.5dBm integrated amplifier allows for extended range links that can achieve up to 15km in an open area (by the module manufacturer specification). This Click board™ offers data rates of 300kbps with FSK modulation and 12500bps with LoRa Technology modulation and is associated with the 915MHz ISM band suitable for applications in the United States, Canada, Australia, and New Zealand. To join a LoRaWAN network, the RN2903 requires a LoRaWAN concentrator/gateway. The endpoint device has to
use a unique endpoint address, an application session key, and a network session key. The first method is called over-the-air activation (OTAA), where these keys are issued after a specific join procedure. The second method is to assign these keys manually, using UART commands. This method is called activation by personalization (ABP) and can be prone to some security issues. In any case, before an end device can communicate on the LoRaWAN network, it must be activated. LR 2 Click communicates with MCU using the UART interface with commonly used UART RX and TX pins, including the hardware flow control pins CTS and RTS (Clear to Send, Ready to Send) at data rates up to 57600bps for the data transfer. There are three groups of commands used to configure and operate the separate layers of the RN2903 (SYSTEM, MAC, and RADIO). Each layer controls a specific area of the module, and every UART command starts with one of the three keywords,
which represent an abbreviation of the layer name they are controlling. The module also has a non-volatile memory (EEPROM) for storing the configuration settings and some additional data. Also, this Click board™ can be reset through the Hardware Reset pin, labeled as RST on the mikroBUS™ socket, by setting this pin to a low logic state. LR 2 Click features the SMA antenna connector with an impedance of 50Ω, so it can be equipped with the appropriate 915MHz compliant antenna that MIKROE offers. This Click board™ can operate with either 3.3V or 5V logic voltage levels selected via the VCC SEL jumper. This way, both 3.3V and 5V capable MCUs can use the communication lines properly. Also, this Click board™ comes equipped with a library containing easy-to-use functions and an example code that can be used as a reference for further development.
Features overview
Development board
PIC32MZ Clicker is a compact starter development board that brings the flexibility of add-on Click boards™ to your favorite microcontroller, making it a perfect starter kit for implementing your ideas. It comes with an onboard 32-bit PIC32MZ microcontroller with FPU from Microchip, a USB connector, LED indicators, buttons, a mikroProg connector, and a header for interfacing with external electronics. Thanks to its compact design with clear and easy-recognizable silkscreen markings, it provides a fluid and immersive working experience, allowing access anywhere and under
any circumstances. Each part of the PIC32MZ Clicker development kit contains the components necessary for the most efficient operation of the same board. In addition to the possibility of choosing the PIC32MZ Clicker programming method, using USB HID mikroBootloader, or through an external mikroProg connector for PIC, dsPIC, or PIC32 programmer, the Clicker board also includes a clean and regulated power supply module for the development kit. The USB Micro-B connection can provide up to 500mA of current, which is more than enough to operate all onboard
and additional modules. All communication methods that mikroBUS™ itself supports are on this board, including the well-established mikroBUS™ socket, reset button, and several buttons and LED indicators. PIC32MZ Clicker is an integral part of the Mikroe ecosystem, allowing you to create a new application in minutes. Natively supported by Mikroe software tools, it covers many aspects of prototyping thanks to a considerable number of different Click boards™ (over a thousand boards), the number of which is growing every day.
Microcontroller Overview
MCU Card / MCU
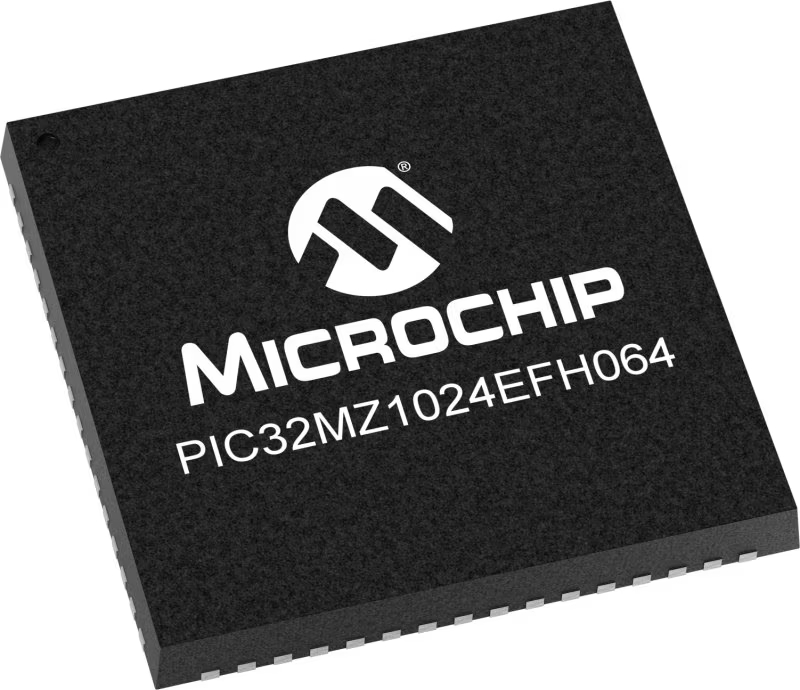
Architecture
PIC32
MCU Memory (KB)
1024
Silicon Vendor
Microchip
Pin count
64
RAM (Bytes)
524288
You complete me!
Accessories
Rubber Antenna GSM/GPRS Right Angle is the perfect companion for all GSM Click boards™ in our extensive lineup. This specialized antenna is designed to optimize your wireless connectivity with impressive features. With a wide frequency range spanning 824-894/1710-1990MHz or 890-960/1710-1890MHz, it can handle various frequency bands, ensuring a seamless and reliable connection. The antenna boasts an impedance of 50 Ohms and a gain of 2dB, enhancing signal reception and transmission. Its 70/180MHz bandwidth provides flexibility for diverse applications. The vertical polarization further enhances its performance. With a maximum input power capacity of 50W, this antenna ensures robust communication even under demanding conditions. Measuring a compact 50mm in length and featuring an SMA male connector, the Rubber Antenna GSM/GPRS Right Angle is a versatile and compact solution for your wireless communication needs.
Used MCU Pins
mikroBUS™ mapper
Take a closer look
Click board™ Schematic
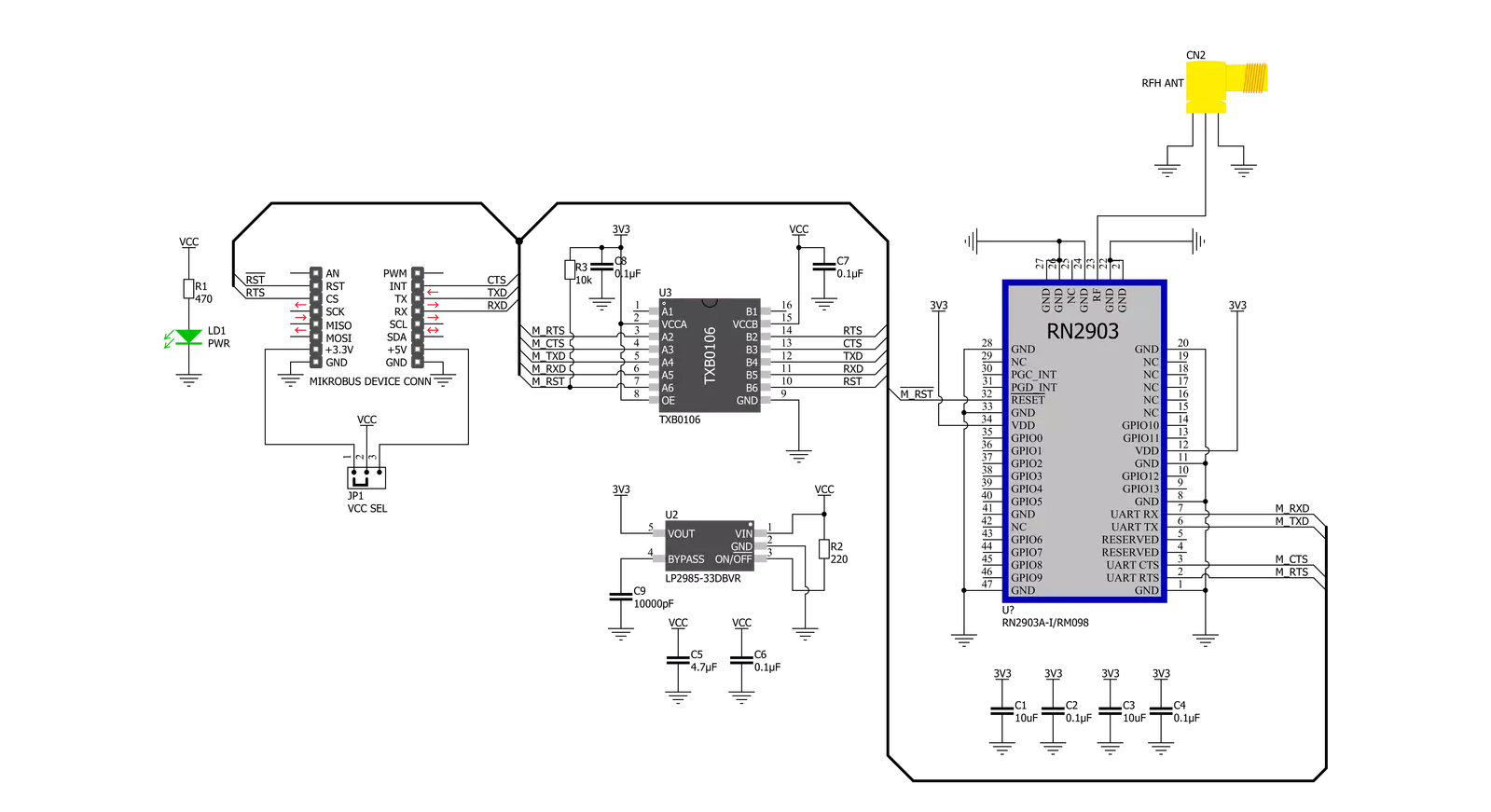
Step by step
Project assembly
Track your results in real time
Application Output
1. Application Output - In Debug mode, the 'Application Output' window enables real-time data monitoring, offering direct insight into execution results. Ensure proper data display by configuring the environment correctly using the provided tutorial.
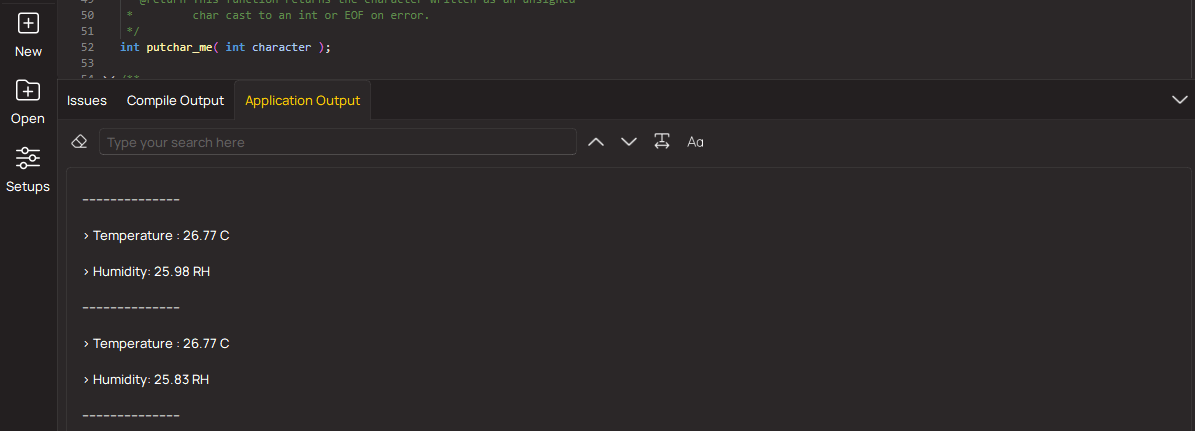
2. UART Terminal - Use the UART Terminal to monitor data transmission via a USB to UART converter, allowing direct communication between the Click board™ and your development system. Configure the baud rate and other serial settings according to your project's requirements to ensure proper functionality. For step-by-step setup instructions, refer to the provided tutorial.
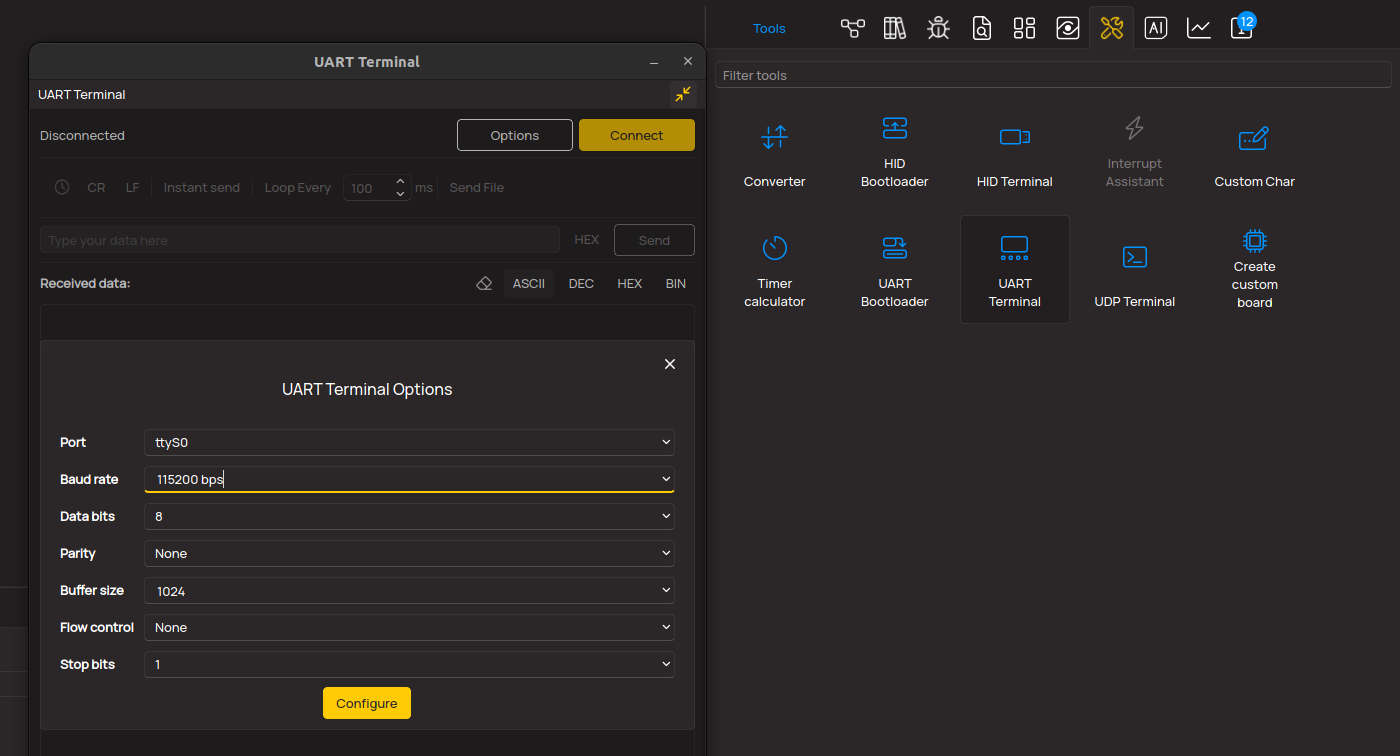
3. Plot Output - The Plot feature offers a powerful way to visualize real-time sensor data, enabling trend analysis, debugging, and comparison of multiple data points. To set it up correctly, follow the provided tutorial, which includes a step-by-step example of using the Plot feature to display Click board™ readings. To use the Plot feature in your code, use the function: plot(*insert_graph_name*, variable_name);. This is a general format, and it is up to the user to replace 'insert_graph_name' with the actual graph name and 'variable_name' with the parameter to be displayed.
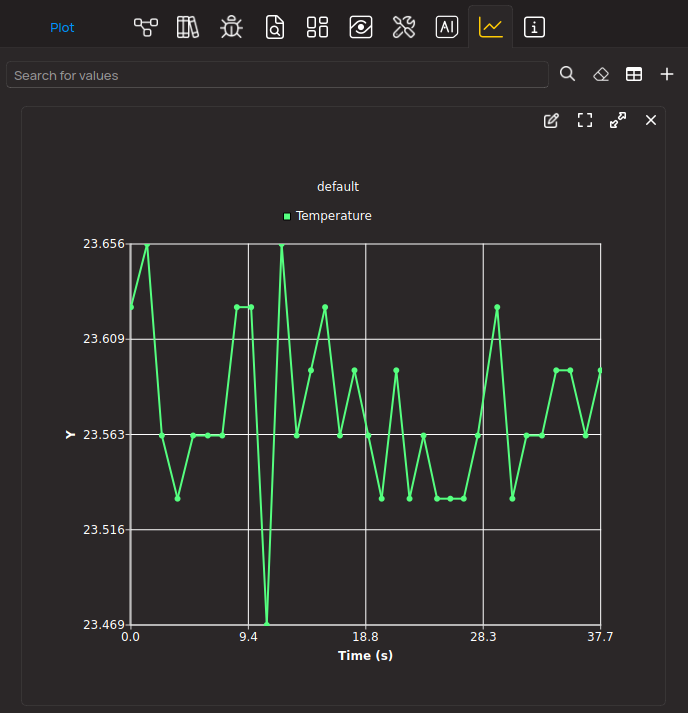
Software Support
Library Description
This library contains API for LR 2 Click driver.
Key functions:
lr_mac_tx
- Function for writing mac parameterslr_join
- Function for setting join modelr_tick_conf
- Timer Configuration
Open Source
Code example
The complete application code and a ready-to-use project are available through the NECTO Studio Package Manager for direct installation in the NECTO Studio. The application code can also be found on the MIKROE GitHub account.
/*!
* @file main.c
* @brief LR Click Example.
*
* # Description
* This example reads and processes data from LR clicks.
*
* The demo application is composed of two sections :
*
* ## Application Init
* Initializes driver init and LR init.
*
* ## Application Task
* Transmitter mode - sends one by one byte sequence of the desired message each second and
* checks if it is sent successfully.
* Receiver mode - displays all the received characters on USB UART.
*
* ## Additional Functions
* - lr_process ( ) - The general process of collecting data the module sends.
* - bool is_digit ( char c ) - Checks if input is a digit
* - hex_to_int ( char* origin, uint8_t* result ) - Converts hexadecimal to int value.
*
* @author Stefan Ilic
*
*/
#include "board.h"
#include "log.h"
#include "lr.h"
#include "string.h"
#include "conversions.h"
#define PROCESS_COUNTER 5
#define PROCESS_RX_BUFFER_SIZE 300
// ------------------------------------------------------------------ VARIABLES
#define DEMO_APP_RECEIVER
//#define DEMO_APP_TRANSMITTER
static lr_t lr;
static log_t logger;
uint8_t cnt;
uint8_t send_data;
int8_t int_data;
uint8_t rx_state;
uint8_t tx_state;
char send_hex[ 50 ];
char tmp_txt[ 50 ];
uint8_t send_message[ 9 ] = { 'M', 'i', 'k', 'r', 'o', 'E', 13, 10, 0 };
// ------------------------------------------------------- ADDITIONAL FUNCTIONS
static void lr_process ( void ) {
int32_t rsp_size;
char uart_rx_buffer[ PROCESS_RX_BUFFER_SIZE ] = { 0 };
uint8_t check_buf_cnt;
uint8_t process_cnt = PROCESS_COUNTER;
while ( process_cnt != 0 ) {
rsp_size = lr_generic_read( &lr, &uart_rx_buffer, PROCESS_RX_BUFFER_SIZE );
if ( rsp_size > 0 ) {
// Validation of the received data
for ( check_buf_cnt = 0; check_buf_cnt < rsp_size; check_buf_cnt++ ) {
lr_put_char( &lr, uart_rx_buffer[ check_buf_cnt ] );
lr_isr_process( &lr );
}
// Clear RX buffer
memset( uart_rx_buffer, 0, PROCESS_RX_BUFFER_SIZE );
} else {
process_cnt--;
// Process delay
Delay_ms( 100 );
}
}
}
bool is_digit ( char c ) {
if ( c >= '0' && c <= '9' ) {
return true;
}
return false;
}
void hex_to_int ( char* origin, uint8_t* result ) {
uint8_t len = strlen( origin );
uint8_t idx, ptr, factor;
if ( len > 0 ) {
*result = 0;
factor = 1;
for ( idx = len - 1; idx >= 0; idx-- ) {
if ( is_digit( *( origin + idx ) ) ) {
*result += ( *( origin + idx ) - '0' ) * factor;
} else {
if ( *( origin + idx ) >= 'A' && *( origin + idx ) <= 'Z' ) {
ptr = ( *( origin + idx ) - 'A' ) + 10;
} else {
return;
}
*result += ( ptr * factor );
}
factor *= 16;
}
}
}
void lr_cbk( char* response ) {
}
// ------------------------------------------------------ APPLICATION FUNCTIONS
void application_init ( void ) {
log_cfg_t log_cfg;
lr_cfg_t cfg;
/**
* Logger initialization.
* Default baud rate: 115200
* Default log level: LOG_LEVEL_DEBUG
* @note If USB_UART_RX and USB_UART_TX
* are defined as HAL_PIN_NC, you will
* need to define them manually for log to work.
* See @b LOG_MAP_USB_UART macro definition for detailed explanation.
*/
LOG_MAP_USB_UART( log_cfg );
log_init( &logger, &log_cfg );
log_info( &logger, "---- Application Init ----" );
// Click initialization.
lr_cfg_setup( &cfg );
LR_MAP_MIKROBUS( cfg, MIKROBUS_1 );
lr_init( &lr, &cfg );
lr_default_cfg( &lr, 0, &lr_cbk );
lr_cmd( &lr, LR_CMD_SYS_GET_VER, &tmp_txt[ 0 ] );
lr_cmd( &lr, LR_CMD_MAC_PAUSE, &tmp_txt[ 0 ] );
log_printf( &logger, "mac pause\r\n" );
for ( cnt = 0; cnt < 10; cnt++ ) {
log_printf( &logger, "%c", tmp_txt[ cnt ] );
}
log_printf( &logger, "\r\n" );
lr_cmd( &lr, LR_CMD_RADIO_SET_WDT, &tmp_txt[ 0 ] );
log_printf( &logger, "radio set wdt 0\r\n" );
log_printf( &logger, "%s\r\n", &tmp_txt[ 0 ] );
}
void application_task ( void ) {
char *ptr;
lr_process( );
#ifdef DEMO_APP_RECEIVER
rx_state = lr_rx( &lr, LR_ARG_0, &tmp_txt[ 0 ] );
if ( rx_state == 0 ) {
tmp_txt[ 12 ] = 0;
ptr = ( char* )&int_data;
hex_to_int( &tmp_txt[ 10 ], ptr );
log_printf( &logger, "%c", int_data );
}
#endif
#ifdef DEMO_APP_TRANSMITTER
for ( cnt = 0; cnt < 9; cnt++ ) {
send_data = send_message[ cnt ] ;
int8_to_hex( send_data, send_hex );
tx_state = lr_tx( &lr, &send_hex[ 0 ] );
if ( tx_state == 0 ) {
log_printf( &logger, " Response : %s\r\n", &tmp_txt[ 0 ] );
}
Delay_ms( 1000 );
}
#endif
}
void main ( void ) {
application_init( );
for ( ; ; ) {
application_task( );
}
}
// ------------------------------------------------------------------------ END