Accurately track and measure movements and orientations of an object by detecting how fast and in which direction it's moving or tilting
A
A
Hardware Overview
How does it work?
6DOF IMU 22 Click is based on the ICM-42670-P, a state-of-the-art 6-axis MEMS MotionTracking IMU from TDK InvenSense. This central component incorporates both a 3-axis gyroscope and a 3-axis accelerometer, making it an exceptional tool for precise motion tracking. It has a versatile host interface compatible with I2C and SPI serial communication protocols, a sizeable 2.25Kbytes FIFO, and two customizable interrupts supporting a wake-on-motion feature to reduce power consumption significantly. The gyroscope and accelerometer offer a range of programmable full-scale range settings, ensuring flexibility across various applications. The gyroscope supports four programmable full-scale range settings from ±250dps to ±2000dps, and the accelerometer supports four programmable full-scale range
settings from ±2g to ±16g. The ICM-42670-P stands out in its class for having the lowest noise levels and unparalleled stability under temperature fluctuations, physical shocks, or offsets caused by soldering or bending. It also offers protection against noise from vibrations outside its frequency band. Adding to its impressive feature set are an on-board APEX Motion Processing engine for advanced gesture and step recognition, programmable digital filters, and an integrated temperature sensor, making it ideally suited for creating wearables, smart home devices, robotics, and immersive AR/VR experiences. 6DOF IMU 22 Click supports both I2C and SPI interfaces, enabling communication at speeds up to 1MHz and 24MHz, respectively. Users can select the desired communication protocol by placing SMD jumpers
on the COMM SEL section, ensuring all jumpers align on the same side to avoid potential issues. For I2C usage, the device allows the adjustment of its I2C slave address's least significant bit via an SMD jumper marked as ADDR SEL. Additionally, the board features a data frame sync input pin routed to the FSY pin on the mikroBUS™ socket and two interrupt pins linked to the INT and IT2 pins, enabling the host MCU to detect user-specified events through the I2C/SPI interface. This Click board™ can be operated only with a 3.3V logic voltage level. The board must perform appropriate logic voltage level conversion before using MCUs with different logic levels. Also, it comes equipped with a library containing functions and an example code that can be used as a reference for further development.
Features overview
Development board
Clicker 2 for STM32 is a compact starter development board that brings the flexibility of add-on Click boards™ to your favorite microcontroller, making it a perfect starter kit for implementing your ideas. It comes with an onboard 32-bit ARM Cortex-M4 microcontroller, the STM32F407VGT6 from STMicroelectronics, two mikroBUS™ sockets for Click board™ connectivity, a USB connector, LED indicators, buttons, a JTAG programmer connector, and two 26-pin headers for interfacing with external electronics. Its compact design with clear and easily recognizable silkscreen markings allows you to build gadgets with unique functionalities and features quickly. Each part of the Clicker 2 for
STM32 development kit contains the components necessary for the most efficient operation of the same board. In addition to the possibility of choosing the Clicker 2 for STM32 programming method, using a USB HID mikroBootloader, an external mikroProg connector for STM32 programmer, or through an external ST-LINK V2 programmer, the Clicker 2 board also includes a clean and regulated power supply module for the development kit. It provides two ways of board-powering; through the USB Mini-B cable, where onboard voltage regulators provide the appropriate voltage levels to each component on the board or using a Li-Polymer battery via an onboard battery
connector. All communication methods that mikroBUS™ itself supports are on this board, including the well-established mikroBUS™ socket, reset button, and several user-configurable buttons and LED indicators. Clicker 2 for STM32 is an integral part of the Mikroe ecosystem, allowing you to create a new application in minutes. Natively supported by Mikroe software tools, it covers many aspects of prototyping thanks to a considerable number of different Click boards™ (over a thousand boards), the number of which is growing every day.
Microcontroller Overview
MCU Card / MCU
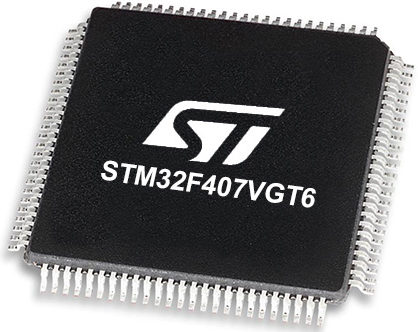
Architecture
ARM Cortex-M4
MCU Memory (KB)
10
Silicon Vendor
STMicroelectronics
Pin count
100
RAM (Bytes)
100
Used MCU Pins
mikroBUS™ mapper
Take a closer look
Click board™ Schematic
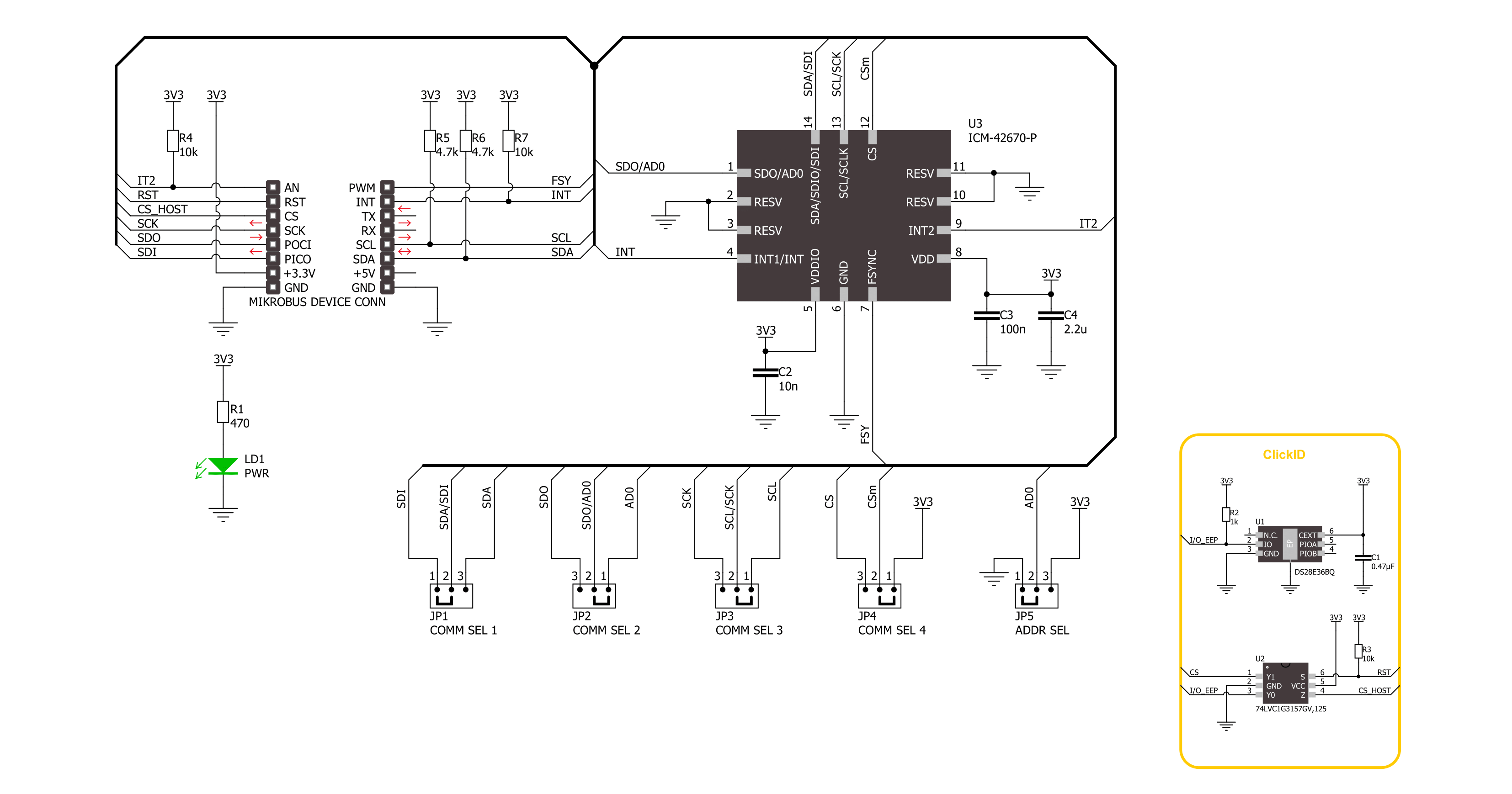
Step by step
Project assembly
Track your results in real time
Application Output
1. Application Output - In Debug mode, the 'Application Output' window enables real-time data monitoring, offering direct insight into execution results. Ensure proper data display by configuring the environment correctly using the provided tutorial.
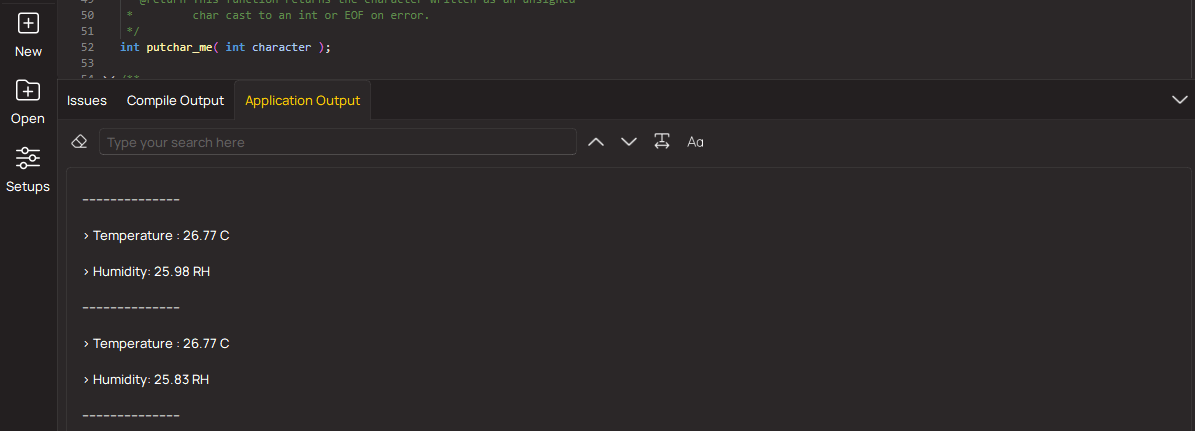
2. UART Terminal - Use the UART Terminal to monitor data transmission via a USB to UART converter, allowing direct communication between the Click board™ and your development system. Configure the baud rate and other serial settings according to your project's requirements to ensure proper functionality. For step-by-step setup instructions, refer to the provided tutorial.
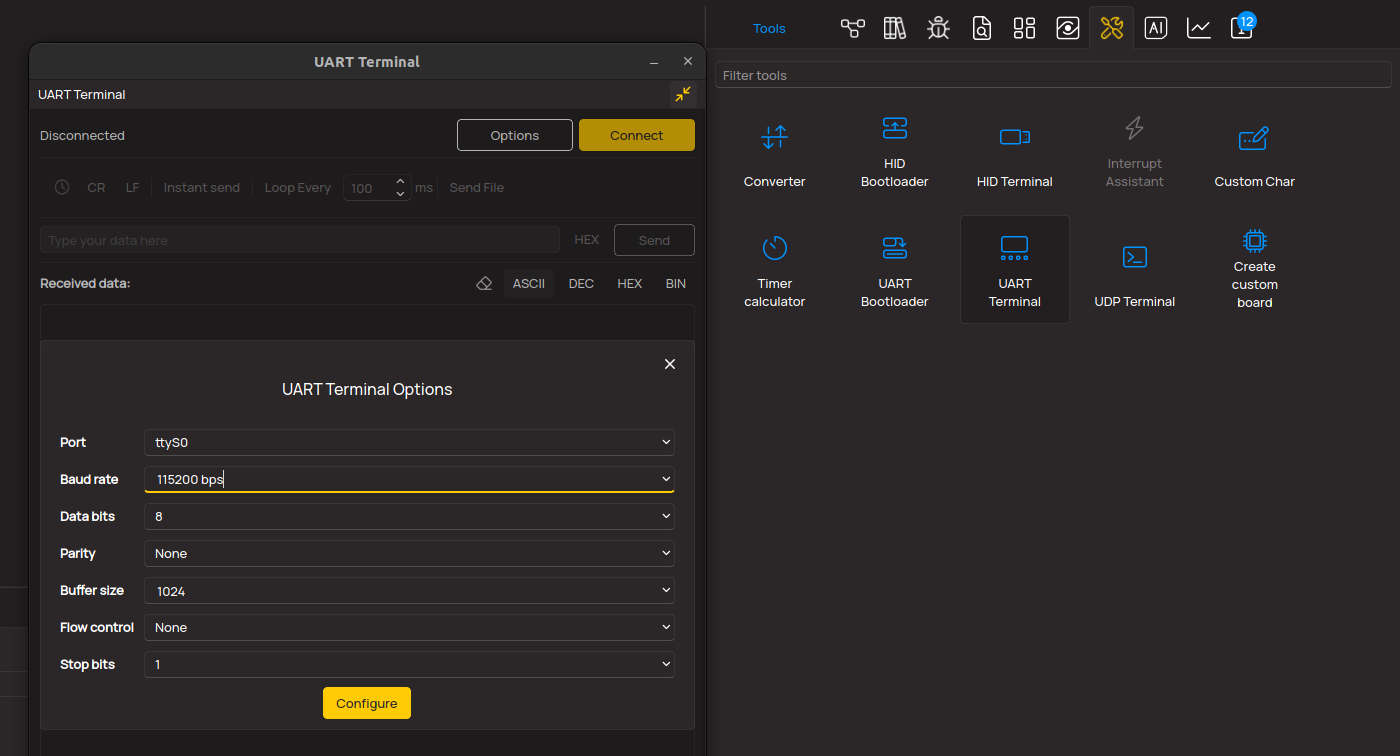
3. Plot Output - The Plot feature offers a powerful way to visualize real-time sensor data, enabling trend analysis, debugging, and comparison of multiple data points. To set it up correctly, follow the provided tutorial, which includes a step-by-step example of using the Plot feature to display Click board™ readings. To use the Plot feature in your code, use the function: plot(*insert_graph_name*, variable_name);. This is a general format, and it is up to the user to replace 'insert_graph_name' with the actual graph name and 'variable_name' with the parameter to be displayed.
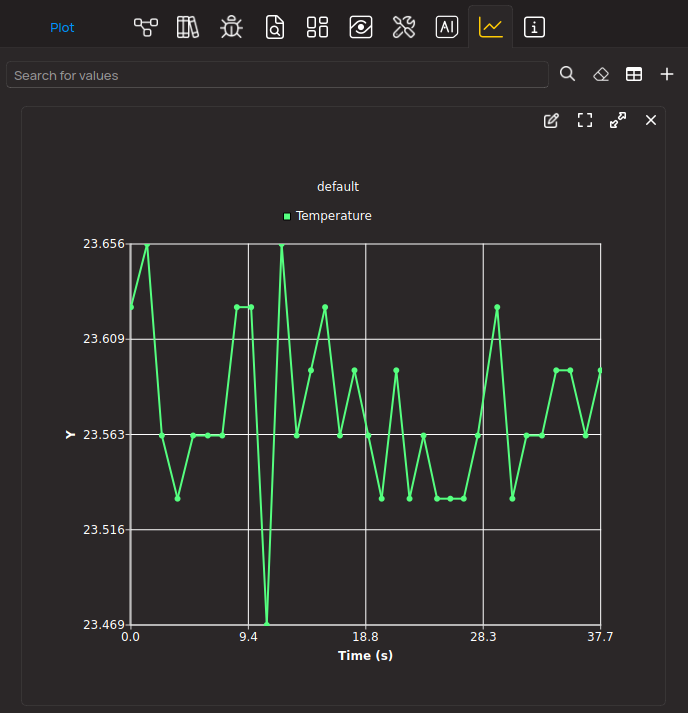
Software Support
Library Description
This library contains API for 6DOF IMU 22 Click driver.
Key functions:
c6dofimu22_read_data
- This function reads the accelerometer, gyroscope, and temperature measurement datac6dofimu22_get_int1_pin
- This function returns the INT1 pin logic statec6dofimu22_clear_data_ready
- This function clears the data ready interrupt by reading the INT_STATUS_DRDY register
Open Source
Code example
The complete application code and a ready-to-use project are available through the NECTO Studio Package Manager for direct installation in the NECTO Studio. The application code can also be found on the MIKROE GitHub account.
/*!
* @file main.c
* @brief 6DOF IMU 22 Click example
*
* # Description
* This example demonstrates the use of 6DOF IMU 22 Click board by reading and displaying
* the accelerometer and gyroscope data (X, Y, and Z axis) as well as a temperature measurement
* in degrees Celsius.
*
* The demo application is composed of two sections :
*
* ## Application Init
* Initializes the driver and performs the Click default configuration.
*
* ## Application Task
* Waits for a data ready indication and then reads the accelerometer, gyroscope, and temperature
* measurements. The results are displayed on the USB UART every 80ms as per the accel and gyro
* output data rate which is set to 12.5 Hz.
*
* @author Stefan Filipovic
*
*/
#include "board.h"
#include "log.h"
#include "c6dofimu22.h"
static c6dofimu22_t c6dofimu22;
static log_t logger;
void application_init ( void )
{
log_cfg_t log_cfg; /**< Logger config object. */
c6dofimu22_cfg_t c6dofimu22_cfg; /**< Click config object. */
/**
* Logger initialization.
* Default baud rate: 115200
* Default log level: LOG_LEVEL_DEBUG
* @note If USB_UART_RX and USB_UART_TX
* are defined as HAL_PIN_NC, you will
* need to define them manually for log to work.
* See @b LOG_MAP_USB_UART macro definition for detailed explanation.
*/
LOG_MAP_USB_UART( log_cfg );
log_init( &logger, &log_cfg );
log_info( &logger, " Application Init " );
// Click initialization.
c6dofimu22_cfg_setup( &c6dofimu22_cfg );
C6DOFIMU22_MAP_MIKROBUS( c6dofimu22_cfg, MIKROBUS_1 );
err_t init_flag = c6dofimu22_init( &c6dofimu22, &c6dofimu22_cfg );
if ( ( I2C_MASTER_ERROR == init_flag ) || ( SPI_MASTER_ERROR == init_flag ) )
{
log_error( &logger, " Communication init." );
for ( ; ; );
}
if ( C6DOFIMU22_ERROR == c6dofimu22_default_cfg ( &c6dofimu22 ) )
{
log_error( &logger, " Default configuration." );
for ( ; ; );
}
log_info( &logger, " Application Task " );
}
void application_task ( void )
{
static c6dofimu22_data_t meas_data;
if ( !c6dofimu22_get_int1_pin ( &c6dofimu22 ) )
{
c6dofimu22_clear_data_ready ( &c6dofimu22 );
if ( C6DOFIMU22_OK == c6dofimu22_read_data ( &c6dofimu22, &meas_data ) )
{
log_printf ( &logger, " Accel X: %.2f g\r\n", meas_data.accel.x );
log_printf ( &logger, " Accel Y: %.2f g\r\n", meas_data.accel.y );
log_printf ( &logger, " Accel Z: %.2f g\r\n", meas_data.accel.z );
log_printf ( &logger, " Gyro X: %.1f dps\r\n", meas_data.gyro.x );
log_printf ( &logger, " Gyro Y: %.1f dps\r\n", meas_data.gyro.y );
log_printf ( &logger, " Gyro Z: %.1f dps\r\n", meas_data.gyro.z );
log_printf ( &logger, " Temperature: %.2f C\r\n\n", meas_data.temperature );
}
}
}
int main ( void )
{
/* Do not remove this line or clock might not be set correctly. */
#ifdef PREINIT_SUPPORTED
preinit();
#endif
application_init( );
for ( ; ; )
{
application_task( );
}
return 0;
}
// ------------------------------------------------------------------------ END