Discover how sensor fusion with 13 degrees of freedom opens up endless opportunities for creating smarter, more responsive devices and systems.
A
A
Hardware Overview
How does it work?
13DOF Click is based on the BME680 and the BMM150 sensor ICs. Also, the click contains BMI088 - a small, versatile 6DoF sensor module from Bosch Sensortec. Altogether, this Click board™ integrates a triaxial accelerometer, triaxial gyroscope, triaxial geomagnetic, gas, humidity, pressure and temperature sensors on the single board. This allows very high integration and very small dimensions, at an affordable cost. The output of each MEMS is processed, digitized and available through the I2C communication interface. The data can be oversampled by the sensor ICs by themselves, in order to achieve as reliable data readings as possible. As already mentioned, the features of this click are numerous. The BMM150 geomagnetic sensor from Bosch is a standalone sensor for consumer market applications. It allows measurements of the magnetic field in three perpendicular axes. The sensor is carefully tuned and a perfect match for the demanding requirements of all 3-axis mobile apps such as electronic compass, navigation or augmented reality.An application specific circuit (ASIC) converts the output of the geomagnetic sensor to digital results which can be read out over the industry standard digital I2C interface. Package and interfaces of the BMM150 have been designed to match a multitude of hardware
requirements. As the sensor features an ultra-small footprint and a flat package, it is ingeniously suited for mobile applications, such as cell phones, handhelds, computer peripherals, man-machine interfaces, virtual reality features, game controllers, and other. The BMI088 is an inertial measurement unit (IMU) for the detection of movements and rotations in 6 degrees of freedom (6DoF). It reflects the full functionality of a triaxial, low-g acceleration sensor and at the same time it is capable to measure angular rates. Both – acceleration and angular rate – in three perpendicular room dimensions, the x-, y- and z-axis. The BMI088 is designed to meet all requirements for consumer applications such as gaming and pointing devices, HMI and image stabilization (DSC and camera-phone). It also senses tilt, motion, inactivity and shock vibration in cell phones, handhelds, computer peripherals, HMI interfaces, virtual reality features and game controllers. An ASIC converts the output of the MEMS, developed, produced and tested in BOSCH facilities. To provide maximum performance and reliability each device is tested and ready-to-use calibrated. On the other side, the BME680 - a small, high performance, low power, 4-in-1 sensor is in charge for the gas, humidity, pressure and temperature measurements. It also features very low power
consumption, for example, 3.7µA is typical at 1 Hz humidity, pressure and temperature measurement mode. It also features a very high accuracy humidity sensor (tolerance ±3% r.H. and hysteresis ±1.5% r.H.), pressure sensor with only 0.12 Pa RMS Noise (equivalent to to 1.7 cm of altitude) and a very low temperature offset drift, and a gas sensor with direct indoor air quality (IAQ) index output system. In principle, the IAQ index output is in an index that can have values between 0 and 500 with a resolution of 1 to indicate or quantify the quality of the air available in the surrounding. It greatly simplifies the categorization of the air quality measurements. 13DOF click supports I2C communication interface, allowing it to be used with a wide range of different MCUs. The I2C slave address for the communication can be selected by moving SMD jumpers grouped under the COMM SEL to an appropriate position. This Click board™ can be operated only with a 3.3V logic voltage level. The board must perform appropriate logic voltage level conversion before using MCUs with different logic levels. Also, it comes equipped with a library containing functions and an example code that can be used as a reference for further development.
Features overview
Development board
Clicker 2 for Kinetis is a compact starter development board that brings the flexibility of add-on Click boards™ to your favorite microcontroller, making it a perfect starter kit for implementing your ideas. It comes with an onboard 32-bit ARM Cortex-M4F microcontroller, the MK64FN1M0VDC12 from NXP Semiconductors, two mikroBUS™ sockets for Click board™ connectivity, a USB connector, LED indicators, buttons, a JTAG programmer connector, and two 26-pin headers for interfacing with external electronics. Its compact design with clear and easily recognizable silkscreen markings allows you to build gadgets with unique functionalities and
features quickly. Each part of the Clicker 2 for Kinetis development kit contains the components necessary for the most efficient operation of the same board. In addition to the possibility of choosing the Clicker 2 for Kinetis programming method, using a USB HID mikroBootloader or an external mikroProg connector for Kinetis programmer, the Clicker 2 board also includes a clean and regulated power supply module for the development kit. It provides two ways of board-powering; through the USB Micro-B cable, where onboard voltage regulators provide the appropriate voltage levels to each component on the board, or
using a Li-Polymer battery via an onboard battery connector. All communication methods that mikroBUS™ itself supports are on this board, including the well-established mikroBUS™ socket, reset button, and several user-configurable buttons and LED indicators. Clicker 2 for Kinetis is an integral part of the Mikroe ecosystem, allowing you to create a new application in minutes. Natively supported by Mikroe software tools, it covers many aspects of prototyping thanks to a considerable number of different Click boards™ (over a thousand boards), the number of which is growing every day.
Microcontroller Overview
MCU Card / MCU
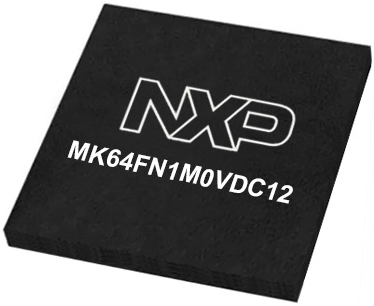
Architecture
ARM Cortex-M4
MCU Memory (KB)
1024
Silicon Vendor
NXP
Pin count
121
RAM (Bytes)
262144
Used MCU Pins
mikroBUS™ mapper
Take a closer look
Click board™ Schematic
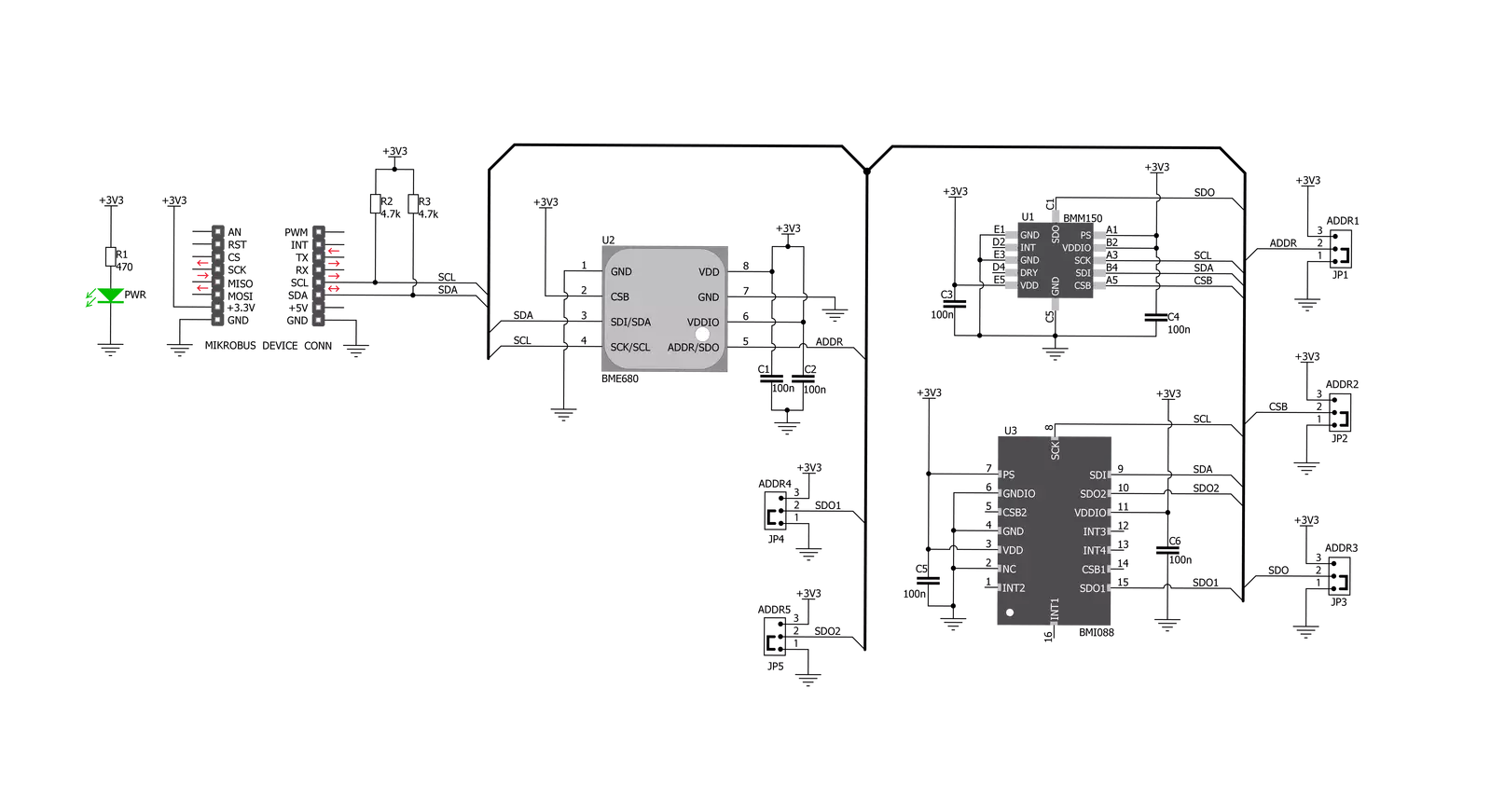
Step by step
Project assembly
Track your results in real time
Application Output
1. Application Output - In Debug mode, the 'Application Output' window enables real-time data monitoring, offering direct insight into execution results. Ensure proper data display by configuring the environment correctly using the provided tutorial.
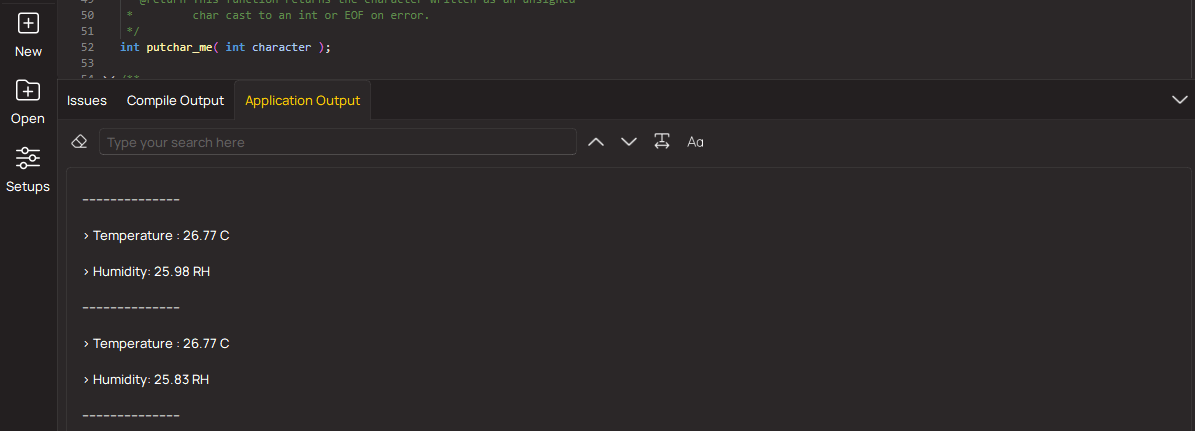
2. UART Terminal - Use the UART Terminal to monitor data transmission via a USB to UART converter, allowing direct communication between the Click board™ and your development system. Configure the baud rate and other serial settings according to your project's requirements to ensure proper functionality. For step-by-step setup instructions, refer to the provided tutorial.
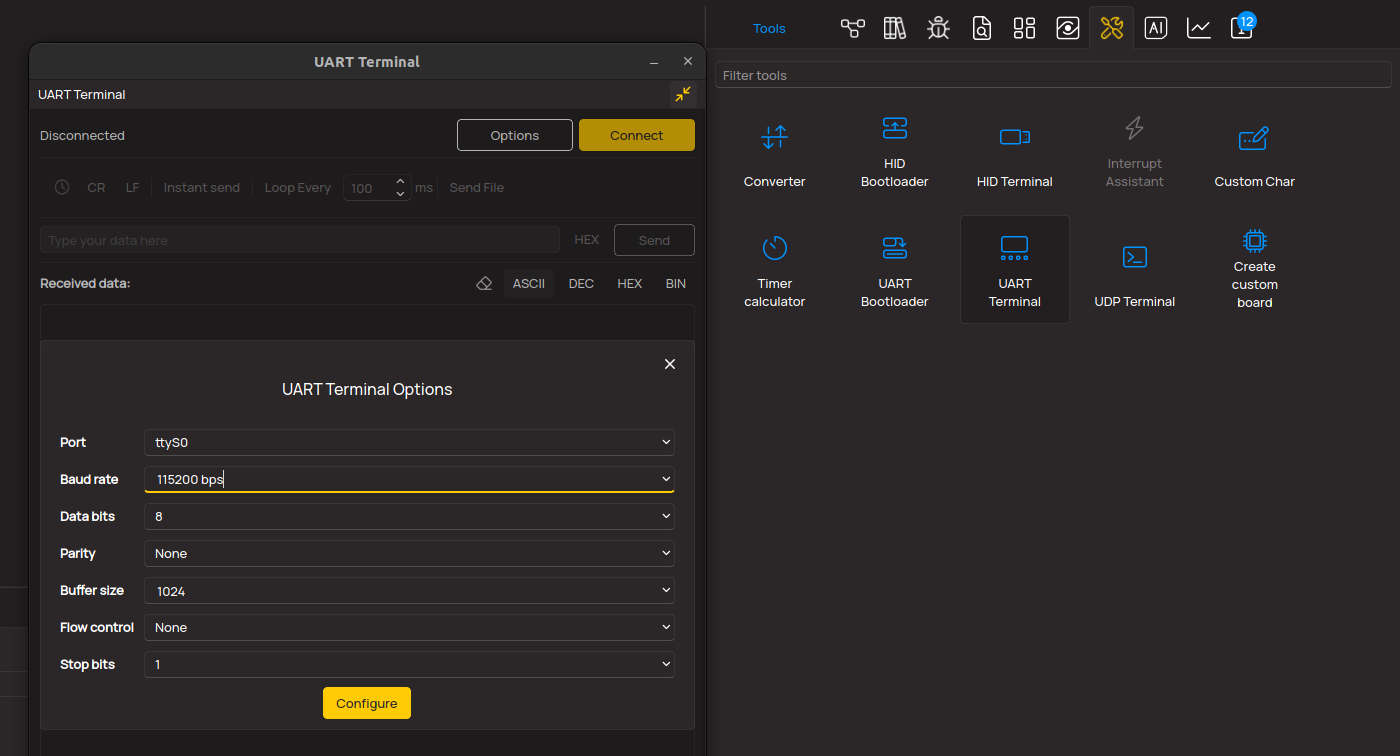
3. Plot Output - The Plot feature offers a powerful way to visualize real-time sensor data, enabling trend analysis, debugging, and comparison of multiple data points. To set it up correctly, follow the provided tutorial, which includes a step-by-step example of using the Plot feature to display Click board™ readings. To use the Plot feature in your code, use the function: plot(*insert_graph_name*, variable_name);. This is a general format, and it is up to the user to replace 'insert_graph_name' with the actual graph name and 'variable_name' with the parameter to be displayed.
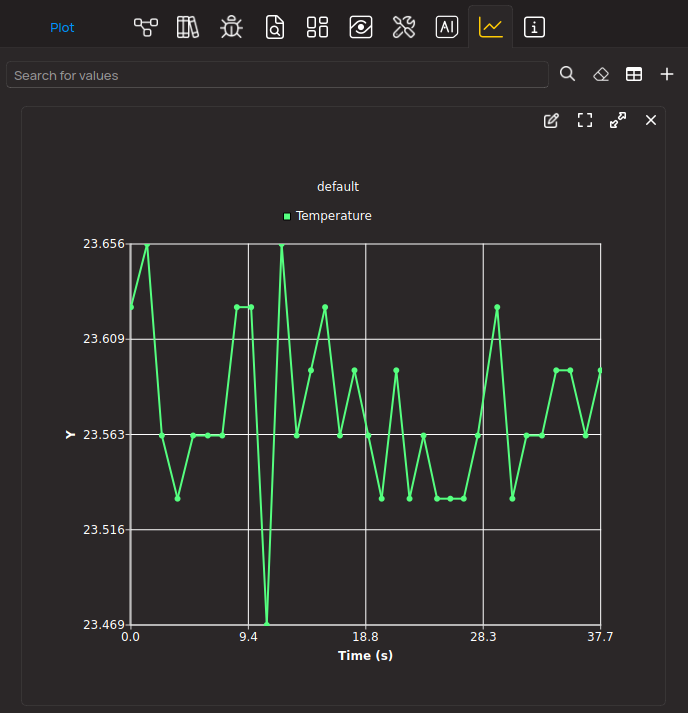
Software Support
Library Description
This library contains API for 13DOF Click driver.
Key functions:
c13dof_bmi088_read_accel
- Function reads 16-bit X-axis, Y-axis data and Z-axis datac13dof_bmi088_accel_read_bytes
- Function read a sequential data starting from the targeted 8-bit register addressc13dof_bmi088_read_gyro
- Function reads 16-bit X-axis, Y-axis data and Z-axis data of BMM150 sensor on 13DOF Click
Open Source
Code example
The complete application code and a ready-to-use project are available through the NECTO Studio Package Manager for direct installation in the NECTO Studio. The application code can also be found on the MIKROE GitHub account.
/*!
* \file
* \brief c13DOF Click example
*
* # Description
* This example displays values registered by sensors on Click board.
*
* The demo application is composed of two sections :
*
* ## Application Init
* Initialization driver enables -
* BME680 Low power gas, pressure, temperature & humidity sensor,
* BMI088 6-axis Motion Tracking Sensor and
* BMM150 Geomagnetic Sensor, also write log.
*
* ## Application Task
* This is a example which demonstrates the use of 13DOF Click board.
* Measures and display temperature in degrees Celsius [ C ], humidity data [ % ],
* pressure [ mbar ] and gas resistance data from the BME680 sensor.
* Measures and display Accel and Gyro data coordinates values
* for X-axis, Y-axis and Z-axis from the BMI088 sensor.
* Measures and display Geomagnetic data coordinates values for
* X-axis, Y-axis and Z-axis from the BMM150 sensor.
* Results are being sent to the Usart Terminal where you can track their changes.
* All data logs write on usb uart changes for each second.
*
*
* \author MikroE Team
*
*/
// ------------------------------------------------------------------- INCLUDES
#include "board.h"
#include "log.h"
#include "c13dof.h"
// ------------------------------------------------------------------ VARIABLES
static c13dof_t c13dof;
static log_t logger;
float temperature;
float pressure;
float humidity;
int32_t gas_res;
int16_t accel_x;
int16_t accel_y;
int16_t accel_z;
int16_t gyro_x;
int16_t gyro_y;
int16_t gyro_z;
int16_t mag_x;
int16_t mag_y;
int16_t mag_z;
uint16_t r_hall;
uint8_t ready_check;
// ------------------------------------------------------ APPLICATION FUNCTIONS
void application_init ( void )
{
log_cfg_t log_cfg;
c13dof_cfg_t cfg;
/**
* Logger initialization.
* Default baud rate: 115200
* Default log level: LOG_LEVEL_DEBUG
* @note If USB_UART_RX and USB_UART_TX
* are defined as HAL_PIN_NC, you will
* need to define them manually for log to work.
* See @b LOG_MAP_USB_UART macro definition for detailed explanation.
*/
LOG_MAP_USB_UART( log_cfg );
log_init( &logger, &log_cfg );
log_info( &logger, "---- Application Init ----" );
// Click initialization.
c13dof_cfg_setup( &cfg );
C13DOF_MAP_MIKROBUS( cfg, MIKROBUS_1 );
c13dof_init( &c13dof, &cfg );
c13dof_default_cfg( &c13dof );
}
void application_task ( void )
{
temperature = c13dof_bme680_get_temperature( &c13dof );
log_printf( &logger, "----------------------------------------------------------\n");
log_printf( &logger, "Temperature : %.2f C \r\n", temperature );
humidity = c13dof_bme680_get_humidity( &c13dof );
log_printf( &logger, "Humidity : %.2f %% \r\n", humidity );
pressure = c13dof_bme680_get_pressure( &c13dof );
log_printf( &logger, "Pressure : %.2f mbar \r\n", pressure );
gas_res = c13dof_bme680_get_gas_resistance( &c13dof );
log_printf( &logger, "Gas Resistance : %ld \r\n", gas_res );
ready_check = c13dof_bmm150_check_ready( &c13dof );
while ( ready_check != C13DOF_BMM150_DATA_READY )
{
ready_check = c13dof_bmm150_check_ready( &c13dof );
}
c13dof_bmi088_read_accel( &c13dof, &accel_x, &accel_y, &accel_z );
c13dof_bmi088_read_gyro( &c13dof, &gyro_x, &gyro_y, &gyro_z );
c13dof_bmm150_read_geo_mag_data( &c13dof, &mag_x, &mag_y, &mag_z, &r_hall );
log_printf( &logger, "Accel X : %d ", accel_x );
log_printf( &logger, " Y : %d ", accel_y );
log_printf( &logger, " Z : %d \r\n", accel_z );
log_printf( &logger, "Gyro X : %d ", gyro_x );
log_printf( &logger, " Y : %d ", gyro_y );
log_printf( &logger, " Z : %d \r\n", gyro_z );
log_printf( &logger, "Mag X : %d ", mag_x );
log_printf( &logger, " Y : %d ", mag_y );
log_printf( &logger, " Z : %d \r\n", mag_z );
Delay_ms ( 1000 );
}
int main ( void )
{
/* Do not remove this line or clock might not be set correctly. */
#ifdef PREINIT_SUPPORTED
preinit();
#endif
application_init( );
for ( ; ; )
{
application_task( );
}
return 0;
}
// ------------------------------------------------------------------------ END