Explore the principles and technology behind differential pressure sensors, highlighting their critical role in modern measurement systems
A
A
Hardware Overview
How does it work?
Diff Press 2 Click is based on the SDP31-500PA, a highly versatile differential pressure sensor designed for high-volume applications from Sensirion. It builds on the next-generation CMOSens® sensor chip at the heart of Sensirion’s new differential pressure and flows sensing platform. It features fast measurement speed, excellent accuracy, and long-term stability, has no zero-point drift, and offers an ultra-low power consumption, making the SDP31-500PA the perfect choice for applications where accurate and reliable pressure monitoring is essential. The SDP31-500PA is very flexible regarding
measurement speed. This flexibility allows for optimizing the sensor’s performance for a specific application and for adapting the sensor to different use cases. For example, the sensor detects the smallest and quickest changes in one use case, whereas, in another mode, the sensor can measure in larger intervals while consuming only a little energy. Diff Press 2 Click communicates with MCU using the standard I2C 2-Wire interface to read data and configure settings, supporting Fast Mode up to 400kHz. Besides, the SDP31-500PA allows choosing the least significant bit (LSB) of its I2C slave address
using the SMD jumper labeled ADDR SEL. It also possesses an additional interrupt signal, routed on the INT pin of the mikroBUS™ socket labeled as INT, indicating when a specific interrupt event occurs, such as whether new measurement results are available. This Click board™ can operate with either 3.3V or 5V logic voltage levels selected via the VCC SEL jumper. This way, both 3.3V and 5V capable MCUs can use the communication lines properly. Also, this Click board™ comes equipped with a library containing easy-to-use functions and an example code that can be used as a reference for further development.
Features overview
Development board
SparkFun MicroMod mikroBUS Carrier board takes advantage of the MicroMod, Qwiic, and mikroBUS™ ecosystems making it easy to prototype with each combined rapidly. The MicroMod M.2 socket and mikroBUS™ 8-pin header allow users to experiment with any processor board in the MicroMod ecosystem and any Click board™ in the mikroBUS™ ecosystem,
respectively. This board also features two Qwiic connectors to seamlessly integrate hundreds of Qwiic sensors and accessories into your project. The mikroBUS™ socket comprises a pair of 8-pin female headers with a standardized pin configuration. The pins consist of three groups of communications pins (SPI, UART, and I2C), six additional pins (PWM, Interrupt, Analog input,
Reset, and Chip select), and two power groups (3.3V and 5V). While a modern USB-C connector makes programming easy, the Carrier Board is also equipped with an MCP73831 single-cell Lithium-Ion/Lithium-Polymer charge IC so you can charge an attached single-cell Li-Po battery. The charge IC receives power from the USB connection and can source up to 450mA to charge an attached battery.
Microcontroller Overview
MCU Card / MCU
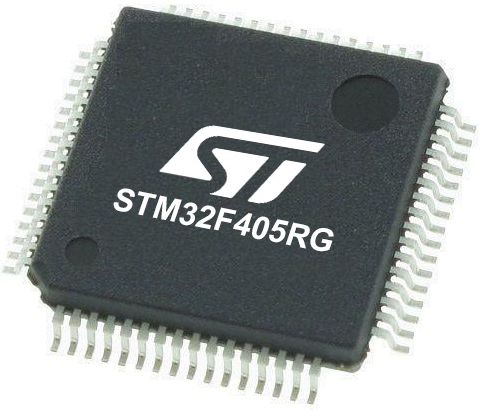
Architecture
ARM Cortex-M4
MCU Memory (KB)
1024
Silicon Vendor
STMicroelectronics
Pin count
64
RAM (Bytes)
196608
Used MCU Pins
mikroBUS™ mapper
Take a closer look
Click board™ Schematic
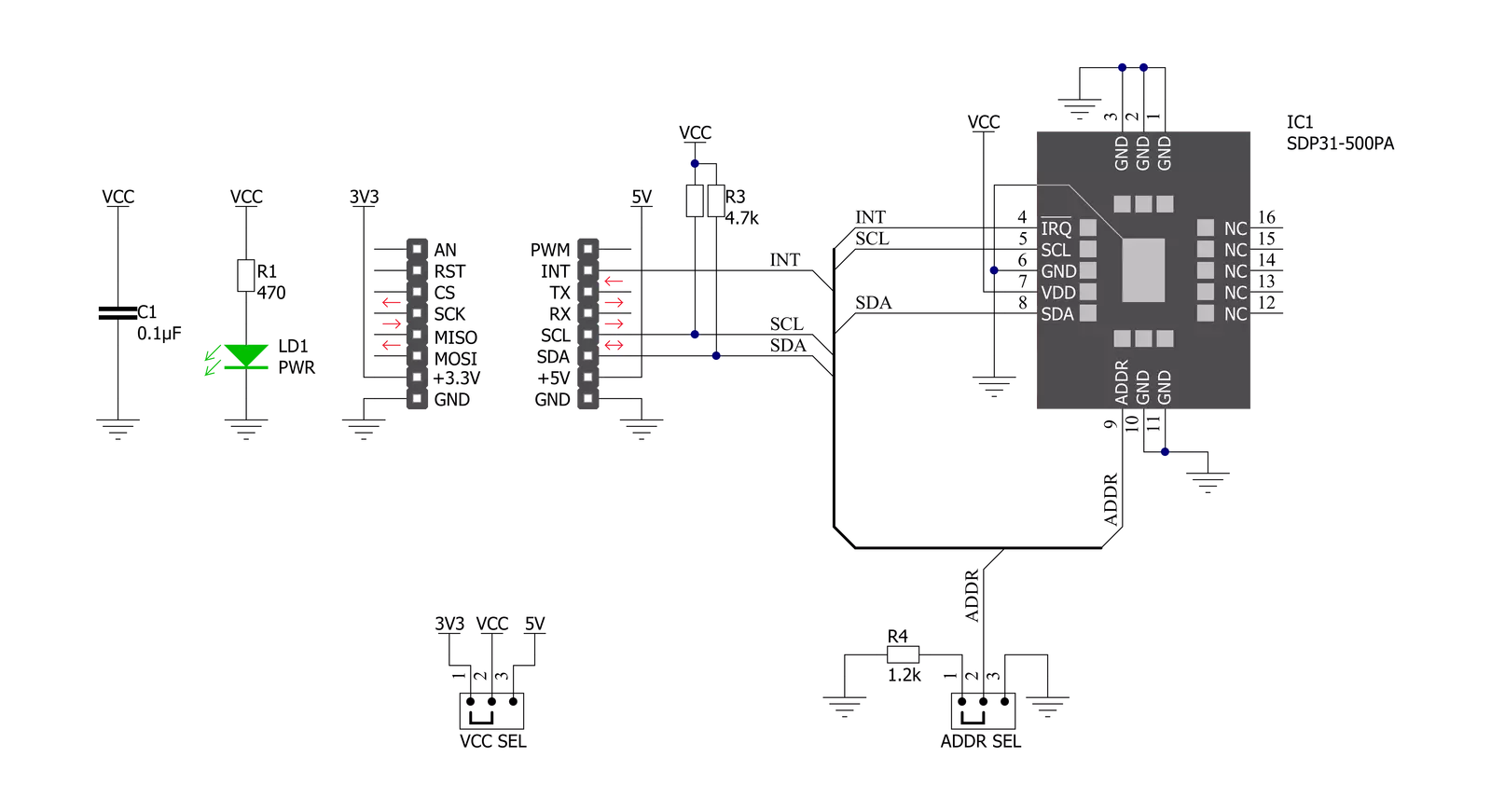
Step by step
Project assembly
Track your results in real time
Application Output
1. Application Output - In Debug mode, the 'Application Output' window enables real-time data monitoring, offering direct insight into execution results. Ensure proper data display by configuring the environment correctly using the provided tutorial.
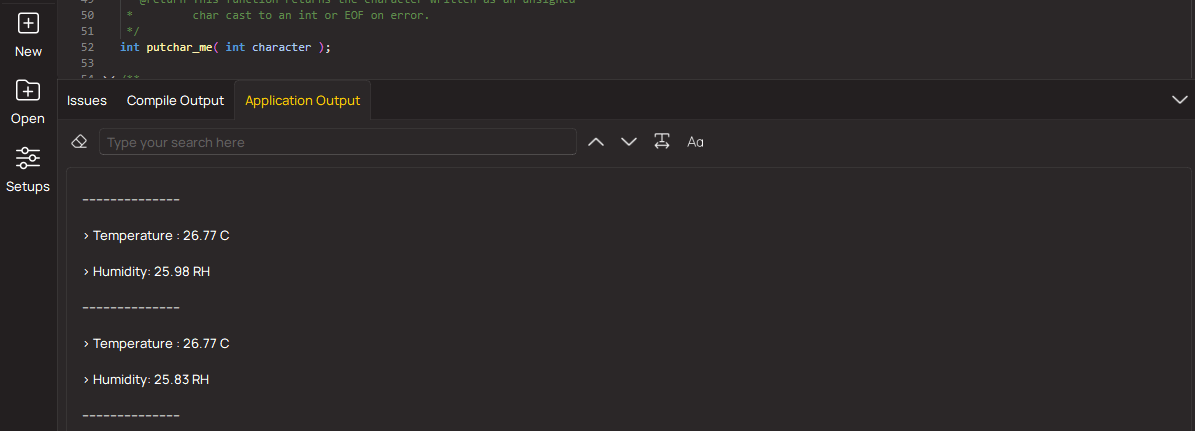
2. UART Terminal - Use the UART Terminal to monitor data transmission via a USB to UART converter, allowing direct communication between the Click board™ and your development system. Configure the baud rate and other serial settings according to your project's requirements to ensure proper functionality. For step-by-step setup instructions, refer to the provided tutorial.
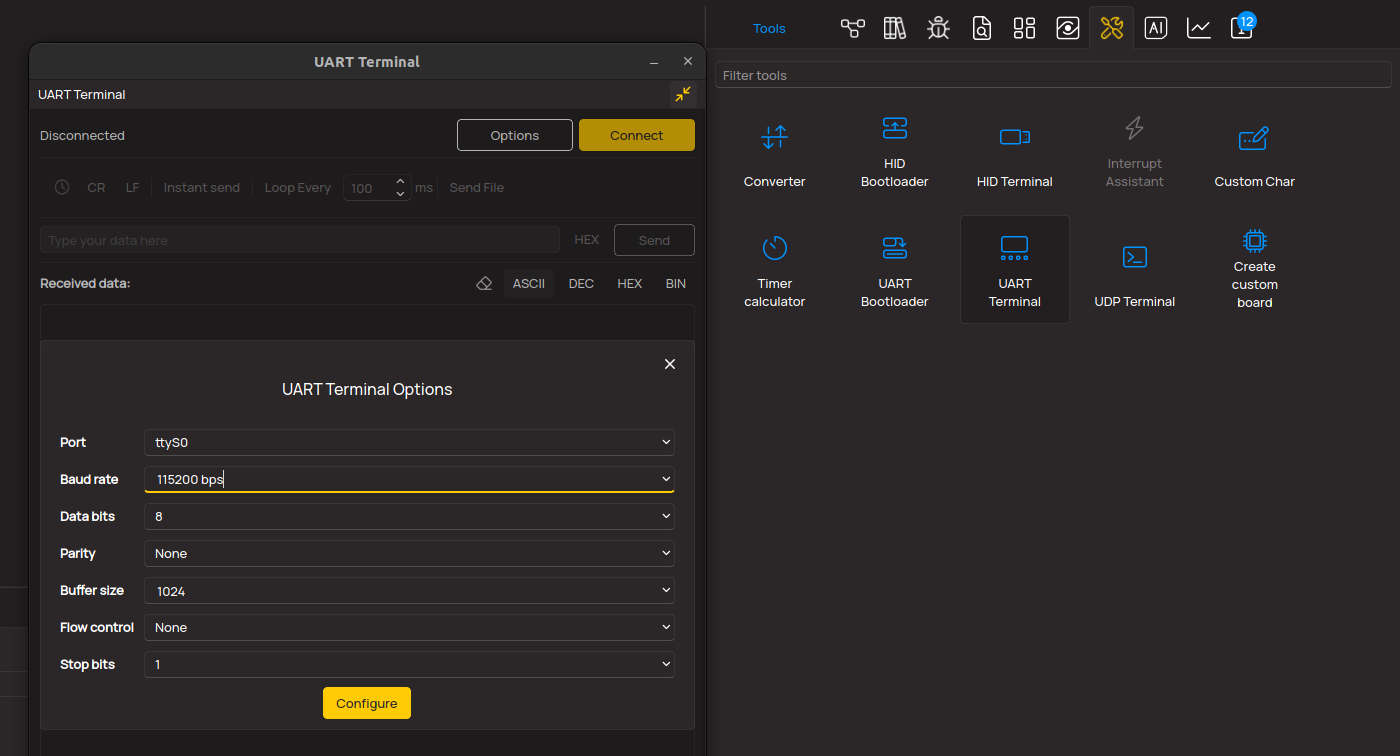
3. Plot Output - The Plot feature offers a powerful way to visualize real-time sensor data, enabling trend analysis, debugging, and comparison of multiple data points. To set it up correctly, follow the provided tutorial, which includes a step-by-step example of using the Plot feature to display Click board™ readings. To use the Plot feature in your code, use the function: plot(*insert_graph_name*, variable_name);. This is a general format, and it is up to the user to replace 'insert_graph_name' with the actual graph name and 'variable_name' with the parameter to be displayed.
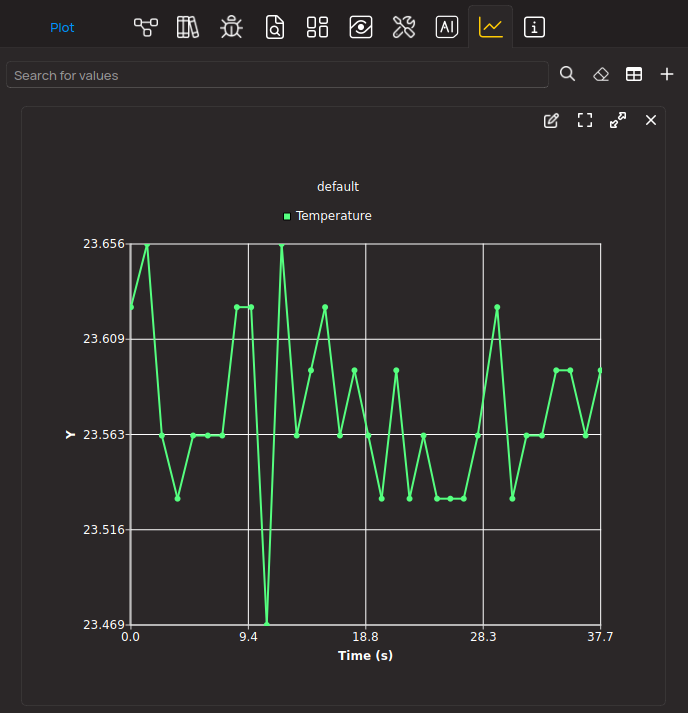
Software Support
Library Description
This library contains API for Diff Press 2 Click driver.
Key functions:
diffpress2_get_id
- Reads device ID'sdiffpress2_reset
- Reset devicediffpress2_trigger_measurement
- Pressure and temperature reading
Open Source
Code example
The complete application code and a ready-to-use project are available through the NECTO Studio Package Manager for direct installation in the NECTO Studio. The application code can also be found on the MIKROE GitHub account.
/*!
* @file main.c
* @brief DiffPress2 Click example
*
* # Description
* This example application showcases ability for device
* to read and calculate mass flow or diff press pressure
* in Pascals and temperature in degrees Celsius.
*
* The demo application is composed of two sections :
*
* ## Application Init
* Initialization of module communication(I2C, UART) and
* additional interrupt pin. Resets device and reads
* serial and product ID's and logs them.
*
* ## Application Task
* Read and calculate differential in Pascal and temperature
* in degrees Celsius every 300ms.
*
* @author Luka Filipovic
*
*/
#include "board.h"
#include "log.h"
#include "diffpress2.h"
static diffpress2_t diffpress2;
static log_t logger;
void application_init ( void )
{
log_cfg_t log_cfg; /**< Logger config object. */
diffpress2_cfg_t diffpress2_cfg; /**< Click config object. */
/**
* Logger initialization.
* Default baud rate: 115200
* Default log level: LOG_LEVEL_DEBUG
* @note If USB_UART_RX and USB_UART_TX
* are defined as HAL_PIN_NC, you will
* need to define them manually for log to work.
* See @b LOG_MAP_USB_UART macro definition for detailed explanation.
*/
LOG_MAP_USB_UART( log_cfg );
log_init( &logger, &log_cfg );
log_info( &logger, " Application Init " );
// Click initialization.
diffpress2_cfg_setup( &diffpress2_cfg );
DIFFPRESS2_MAP_MIKROBUS( diffpress2_cfg, MIKROBUS_1 );
err_t init_flag = diffpress2_init( &diffpress2, &diffpress2_cfg );
if ( I2C_MASTER_ERROR == init_flag )
{
log_error( &logger, " Application Init Error. " );
log_info( &logger, " Please, run program again... " );
for ( ; ; );
}
if ( diffpress2_default_cfg ( &diffpress2 ) )
{
log_error( &logger, " Default configuration." );
for ( ; ; );
}
log_printf( &logger, " > Product ID: 0x%.8LX\r\n", diffpress2.product_id );
log_printf( &logger, " > Serial ID: 0x%.8LX%.8LX\r\n",
diffpress2.serial_id[ 0 ], diffpress2.serial_id[ 1 ] );
log_info( &logger, " Application Task " );
}
void application_task ( void )
{
float pressure;
float temperature;
if ( diffpress2_trigger_measurement( &diffpress2, DIFFPRESS2_CMD_TRIGGER_MEAS_DIFF_PRESS,
&pressure, &temperature ) )
{
log_error( &logger, " Read data." );
}
else
{
log_printf( &logger, " > Pressure[Pa]: %.2f\r\n", pressure );
log_printf( &logger, " > Temperature[degC]: %.2f\r\n", temperature );
log_printf( &logger, "*************************************\r\n" );
}
Delay_ms ( 300 );
}
int main ( void )
{
/* Do not remove this line or clock might not be set correctly. */
#ifdef PREINIT_SUPPORTED
preinit();
#endif
application_init( );
for ( ; ; )
{
application_task( );
}
return 0;
}
// ------------------------------------------------------------------------ END
Additional Support
Resources
Category:Pressure