Enhance safety and reliability with our brushless motor control, offering fault detection and protection features to safeguard both motor and equipment
A
A
Hardware Overview
How does it work?
Brushless 14 Click is based on the TB67B001FTG, a three-phase PWM chopper driver for sensorless brushless motors from Toshiba Semiconductor. It controls motor rotation speed by changing the PWM duty cycle based on the speed control input. This Click board™ offers an energy-saving solution and quiet motor operation in brushless DC (BLDC) motors for various applications. The TSP signal, routed to the PWM signal of the mikroBUS™ socket, starts up and stops the motor operation and controls the output PWM duty to control the rotation speed of the motor. The procedure moves as follows: DC resolution mode - Forced commutation mode - Sensorless mode. Start-Up may fail when the initial rotor position is irregular because they do not synchronize in the forced commutation mode. In this case, adjustment to synchronize the forced commutation frequency to the motor rotation is necessary by adjusting the FST signal of the TB67B001FTG and the input voltage of the VST pin through the VR1 potentiometer to move the operation to the Sensorless mode. In forced commutation mode in Start-Up, the motor operates under the following condition: lead angle = 0°, 120° commutation, and without soft switching. When the process switches to the Sensorless mode, the operation changes automatically to the configured mode by setting the LA pin, LAP, and SLOP switches. SLOP and LAP
switches can select six types of drives (120°, 135°, and 150° commutation with and without soft switching). The TSP pin can select pulse duty control or analog voltage control by the SP pin of the SW3 switch. Besides, the TSP signal can adjust the output PWM duty by the configuration of ADJ0-3 channels done by DAC43608, a low-power, eight-channel, digital-to-analog converter. The desired value on the lead angle LA pin the TC78B042FTG and FPWM (output PWM frequency selection) is also obtained by the DAC3608, which establishes communication with MCU via I2C serial communication. The rotation speed of lead angle switching is selectable through the onboard ROT switch. When the most appropriate lead angle is set, the efficiency is improved, and the noise is reduced. In addition to I2C communication, several GPIO pins connected to the mikroBUS™ socket pins are also used. A DIR pin can switch the rotation direction of the motor, routed to the RST signal of the mikroBUS™ socket. While switching the rotation direction, first stop the motor, turn off the output by the TSP pin, and then switch the rotation direction by changing the configuration of the DIR pin. Besides, it is possible to detect motor lock events where the indication of such a condition is performed using the LED indicator labeled as LOCK and rotation speed, where the information is forwarded to the
MCU via the PCA9538 expander port. The user is left with the option of adding pull-up (R13-R16) or pull-down (R23-R26) resistors as desired for their applications and activating and deactivating the selected ADJ channels using jumper JP2-JP5. Also, when the motor is vibrating by an external factor, it may not start operating normally. In such a case, the motor can start operating normally by adding the external resistances of R17-R19 to provide the offset voltage in the position detection comparator inside the TB67B001FTG. Brushless 14 Click supports an external power supply for the motor, which can be connected to the input terminal labeled as VM and should be within the range of 5.5V to 22V. The next ones marked with U, V, W, and COM are terminals on which the BLDC motor needs to be connected. The absolute maximum rating of the power supply voltage is 25V (3A maximum current), which must not be exceeded, even for a moment. Do not exceed any of these ratings! This Click board™ can operate with either 3.3V or 5V logic voltage levels selected via the VCC SEL jumper. This way, both 3.3V and 5V capable MCUs can use the communication lines properly. This Click board™ comes equipped with a library containing easy-to-use functions and an example code that can be used, as a reference, for further development.
Features overview
Development board
Arduino UNO is a versatile microcontroller board built around the ATmega328P chip. It offers extensive connectivity options for various projects, featuring 14 digital input/output pins, six of which are PWM-capable, along with six analog inputs. Its core components include a 16MHz ceramic resonator, a USB connection, a power jack, an
ICSP header, and a reset button, providing everything necessary to power and program the board. The Uno is ready to go, whether connected to a computer via USB or powered by an AC-to-DC adapter or battery. As the first USB Arduino board, it serves as the benchmark for the Arduino platform, with "Uno" symbolizing its status as the
first in a series. This name choice, meaning "one" in Italian, commemorates the launch of Arduino Software (IDE) 1.0. Initially introduced alongside version 1.0 of the Arduino Software (IDE), the Uno has since become the foundational model for subsequent Arduino releases, embodying the platform's evolution.
Microcontroller Overview
MCU Card / MCU
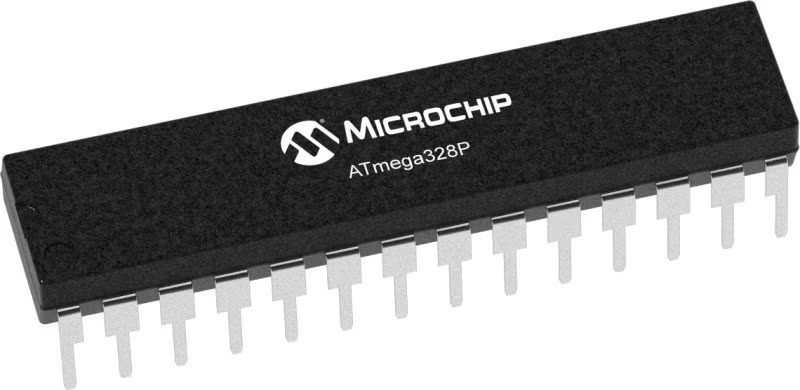
Architecture
AVR
MCU Memory (KB)
32
Silicon Vendor
Microchip
Pin count
28
RAM (Bytes)
2048
You complete me!
Accessories
Click Shield for Arduino UNO has two proprietary mikroBUS™ sockets, allowing all the Click board™ devices to be interfaced with the Arduino UNO board without effort. The Arduino Uno, a microcontroller board based on the ATmega328P, provides an affordable and flexible way for users to try out new concepts and build prototypes with the ATmega328P microcontroller from various combinations of performance, power consumption, and features. The Arduino Uno has 14 digital input/output pins (of which six can be used as PWM outputs), six analog inputs, a 16 MHz ceramic resonator (CSTCE16M0V53-R0), a USB connection, a power jack, an ICSP header, and reset button. Most of the ATmega328P microcontroller pins are brought to the IO pins on the left and right edge of the board, which are then connected to two existing mikroBUS™ sockets. This Click Shield also has several switches that perform functions such as selecting the logic levels of analog signals on mikroBUS™ sockets and selecting logic voltage levels of the mikroBUS™ sockets themselves. Besides, the user is offered the possibility of using any Click board™ with the help of existing bidirectional level-shifting voltage translators, regardless of whether the Click board™ operates at a 3.3V or 5V logic voltage level. Once you connect the Arduino UNO board with our Click Shield for Arduino UNO, you can access hundreds of Click boards™, working with 3.3V or 5V logic voltage levels.
Brushless DC (BLDC) Motor with a Hall sensor represents a high-performance motor from the 42BLF motor series. This motor, wired in a star configuration, boasts a Hall Effect angle of 120°, ensuring precise and reliable performance. With a compact motor length of 47mm and a lightweight design tipping the scales at just 0.29kg, this BLDC motor is engineered to meet your needs. Operating flawlessly at a voltage rating of 24VDC and a speed range of 4000 ± 10% RPM, this motor offers consistent and dependable power. It excels in a normal operational temperature range from -20 to +50°C, maintaining efficiency with a rated current of 1.9A. Also, this product seamlessly integrates with all Brushless Click boards™ and those that require BLDC motors with Hall sensors.
Used MCU Pins
mikroBUS™ mapper
Take a closer look
Click board™ Schematic
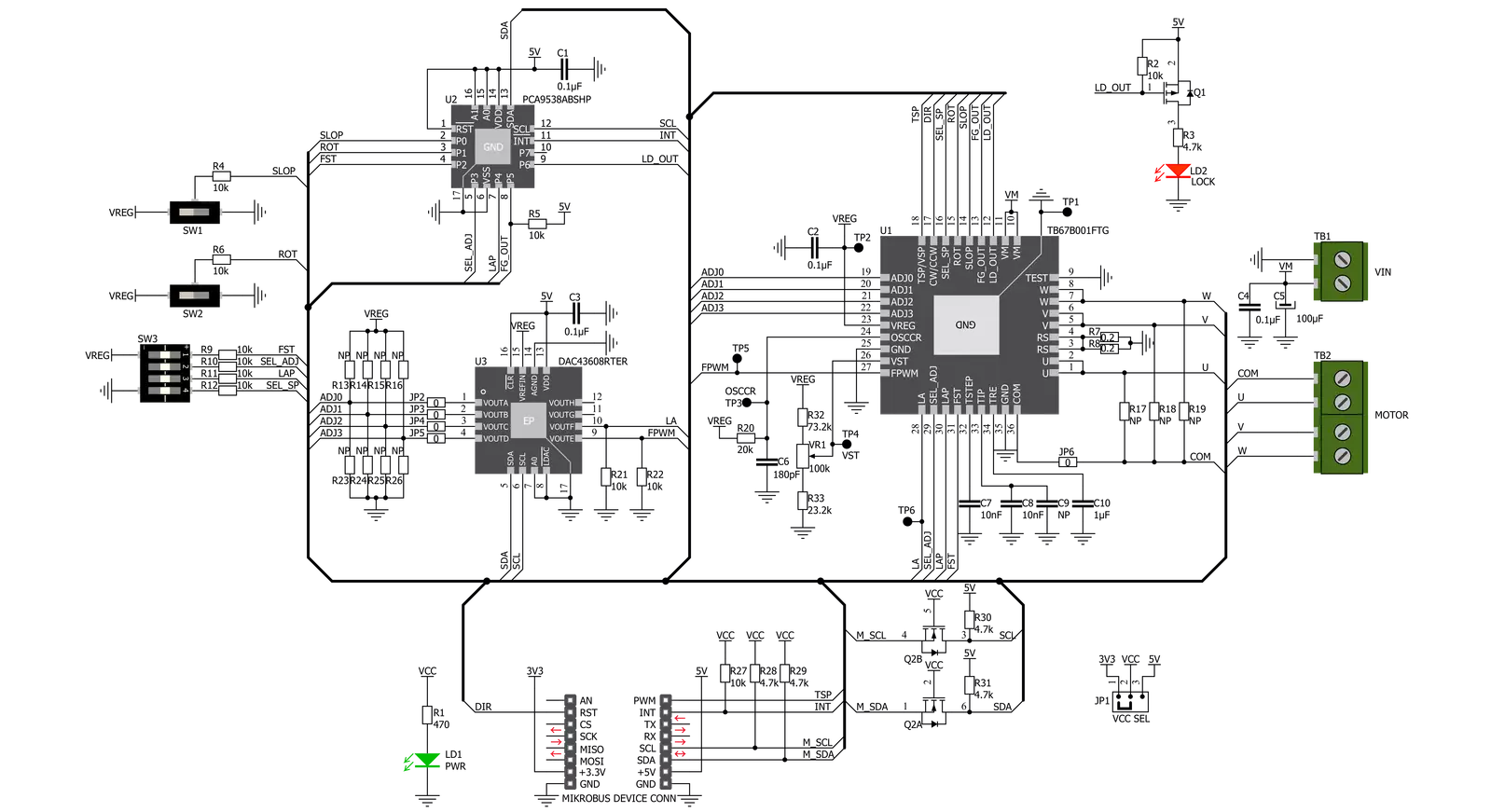
Step by step
Project assembly
Track your results in real time
Application Output
1. Application Output - In Debug mode, the 'Application Output' window enables real-time data monitoring, offering direct insight into execution results. Ensure proper data display by configuring the environment correctly using the provided tutorial.
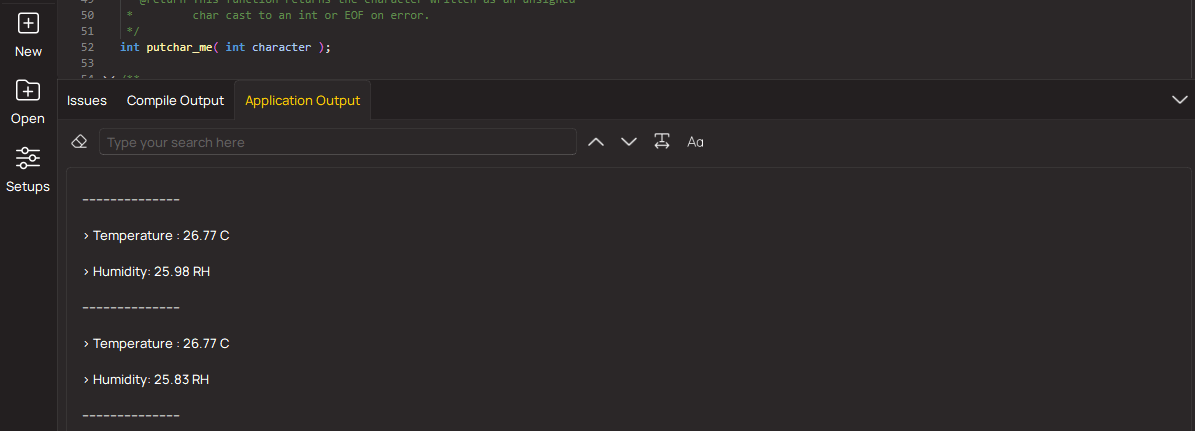
2. UART Terminal - Use the UART Terminal to monitor data transmission via a USB to UART converter, allowing direct communication between the Click board™ and your development system. Configure the baud rate and other serial settings according to your project's requirements to ensure proper functionality. For step-by-step setup instructions, refer to the provided tutorial.
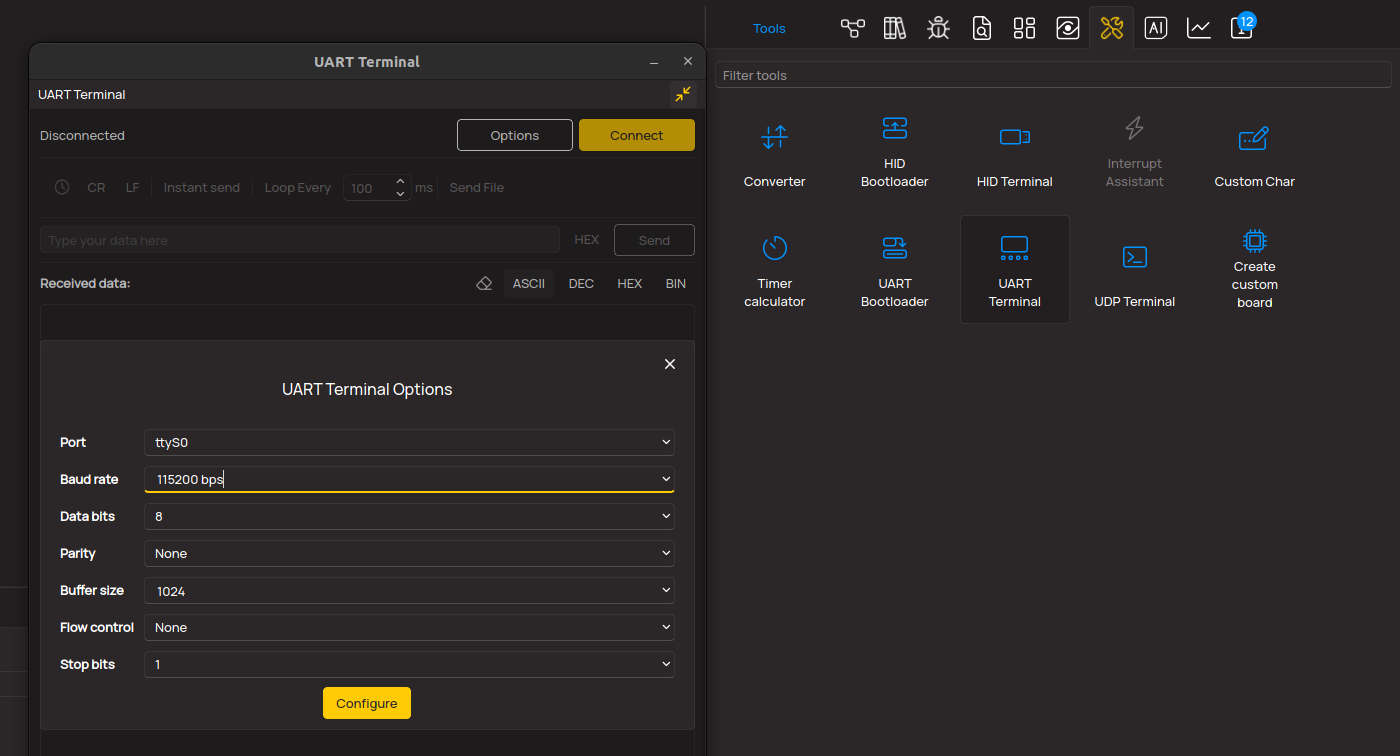
3. Plot Output - The Plot feature offers a powerful way to visualize real-time sensor data, enabling trend analysis, debugging, and comparison of multiple data points. To set it up correctly, follow the provided tutorial, which includes a step-by-step example of using the Plot feature to display Click board™ readings. To use the Plot feature in your code, use the function: plot(*insert_graph_name*, variable_name);. This is a general format, and it is up to the user to replace 'insert_graph_name' with the actual graph name and 'variable_name' with the parameter to be displayed.
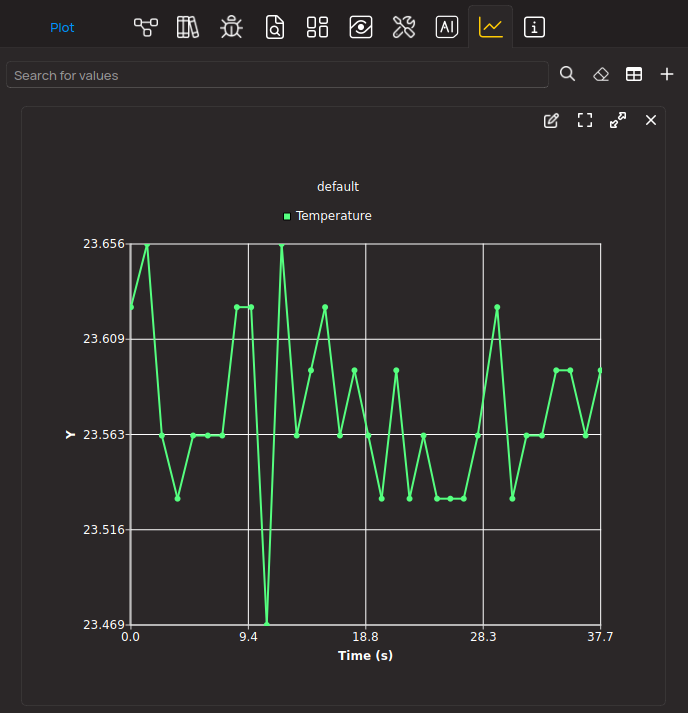
Software Support
Library Description
This library contains API for Brushless 14 Click driver.
Key functions:
brushless14_set_duty_cycle
- This function sets PWM duty cyclebrushless14_set_la
- This function set lead angle setting inputbrushless14_set_dir
- This function set dirrection pin state
Open Source
Code example
The complete application code and a ready-to-use project are available through the NECTO Studio Package Manager for direct installation in the NECTO Studio. The application code can also be found on the MIKROE GitHub account.
/*!
* @file main.c
* @brief Brushless14 Click example
*
* # Description
* This application example showcases ability of the device to control motor,
* It's speed and rotation direction. Also it gives user ability to change other
* configuration parameters.
*
* The demo application is composed of two sections :
*
* ## Application Init
* Initialization of communication modules (I2C, PWM, UART) and additional
* pins (INT, DIR). It reads ID from DAC ic to confirm communcation. Then
* configures device for control.
*
* ## Application Task
* Drives motor using PWM from 10% duty cycle to 100% and back to 0%.
* Increment is done by 10% in span of 2 seconds. Whenever application gets
* to 0% duty cycle it chages direction of rotation.
*
* @author Luka Filipovic
*
*/
#include "board.h"
#include "log.h"
#include "brushless14.h"
static brushless14_t brushless14;
static log_t logger;
void application_init ( void )
{
log_cfg_t log_cfg; /**< Logger config object. */
brushless14_cfg_t brushless14_cfg; /**< Click config object. */
/**
* Logger initialization.
* Default baud rate: 115200
* Default log level: LOG_LEVEL_DEBUG
* @note If USB_UART_RX and USB_UART_TX
* are defined as HAL_PIN_NC, you will
* need to define them manually for log to work.
* See @b LOG_MAP_USB_UART macro definition for detailed explanation.
*/
LOG_MAP_USB_UART( log_cfg );
log_init( &logger, &log_cfg );
log_info( &logger, " Application Init " );
// Click initialization.
brushless14_cfg_setup( &brushless14_cfg );
BRUSHLESS14_MAP_MIKROBUS( brushless14_cfg, MIKROBUS_1 );
err_t init_flag = brushless14_init( &brushless14, &brushless14_cfg );
if ( I2C_MASTER_ERROR == init_flag )
{
log_error( &logger, " Application Init Error. " );
log_info( &logger, " Please, run program again... " );
for ( ; ; );
}
uint16_t data_read = 0;
brushless14_dac_read( &brushless14, 0x02, &data_read);
if ( BRUSHLESS14_DAC_ID != data_read )
{
log_error( &logger, " Communication. " );
}
brushless14_default_cfg ( &brushless14 );
Delay_ms ( 1000 );
log_info( &logger, " Application Task " );
}
void application_task ( void )
{
static int8_t duty_cnt = 1;
static int8_t duty_inc = 1;
static uint8_t direction = 0;
float duty = duty_cnt / 10.0;
brushless14_set_duty_cycle ( &brushless14, duty );
log_printf( &logger, "> Duty: %d%%\r\n", ( uint16_t )( duty_cnt * 10 ) );
Delay_ms ( 1000 );
Delay_ms ( 1000 );
if ( 10 == duty_cnt )
{
duty_inc = -1;
}
else if ( 0 == duty_cnt )
{
duty_inc = 1;
direction = !direction;
brushless14_set_dir( &brushless14, direction );
}
duty_cnt += duty_inc;
}
int main ( void )
{
/* Do not remove this line or clock might not be set correctly. */
#ifdef PREINIT_SUPPORTED
preinit();
#endif
application_init( );
for ( ; ; )
{
application_task( );
}
return 0;
}
// ------------------------------------------------------------------------ END
Additional Support
Resources
Category:Brushless