Trust in our digital barometric sensor to keep you informed, whether you're an outdoor enthusiast, researcher, or IoT developer, enabling data-driven decisions and insights
A
A
Hardware Overview
How does it work?
Pressure 4 Click is based on the BMP280, a digital pressure sensor from Bosch Sensortec. This sensor is produced using the Bosch proprietary APSM manufacturing technology. APSM is an abbreviation for the Advanced Porous Silicon Membrane, which is CMOS compatible technology, used to hermetically seal the sensor cavity, in an all-silicon process. This advanced MEMS technology offers a high measurement precision of only 0.12 hPa, as well as low TOC (thermal coefficient) of only 1.5 Pa/K. The sensor is enclosed in a small metal lid housing and is very resilient: it can operate in a range of 300 hPa to 1100 hPa but can withstand up to 20,000 hPa before the membrane breaks down. The BMP280 offers a set of pressure and temperature measurement options. It can be programmed to skip either thermal or pressure measurement, allowing faster measurement of the required property. The low TOC of only 1.5K/Pa allows reading of the pressure with very small drift over temperature. Resolution of 0.12 hPa allows calculating of the altitude with the accuracy of 1m, which is ideal for indoor navigation applications (drones, flying toy models, and similar). Since this device is aimed at low power applications, it is
powered by the mikroBUS™ 3.3V rail and does not allow voltages up to 5V. Therefore the Click board™ supports only 3.3V MCUs and it is not intended to be connected or controlled via the 5V MCU without a proper level shifting circuitry. This sensor is comprised of a mixed signal front end (ASIC) and the piezo-sensitive pressure sensing element. The ASIC section provides analog to digital conversion of the measurement as well as the signal processing, in the form of the IIR filtering. The measurement readings and the compensation parameters are available at I2C or SPI bus pins of the BMP280 routed to the mikroBUS™ standard SPI and I2C pins. Pressure 4 click offers a selection between the two, by switching SMD jumpers labeled as I2C SPI to an appropriate position. Note that all the jumpers have to be placed to the same side, as mixed SPI and I2C positions will render the Click board™ unresponsive. Additionally, selection of the I2C communication protocol allows the least significant bit (LSB) of the I2C slave address of the device to be set. This can be done with the SMD jumper, labeled as I2C ADDR. The overall power consumption depends on several factors, such as the oversampling value, measurement rate, power
mode, standby duration, and so on. Bosch Sensortec recommends a set of operational parameters for different applications, in a form of a table, in the BMP280 datasheet. In general, this sensor allows several power modes, regardless of the selected measurement parameters, such as Sleep, Forced, and Normal mode. When the measurement is completed, the raw ADC values will be available in the output registers. However, to obtain actual pressure and temperature readings, a compensation algorithm needs to be applied to these raw values. A set of compensation parameters is available in the non-volatile memory of each sensor device. These compensation parameters take into account slight differences between the produced sensors and each BMP280 sensor device has its own set of compensation parameters. The BMP280 datasheet offers detailed instructions on how to apply these compensating algorithms properly. However, MikroElektronika provides a library that contains functions, which can be used for the simplified operation of the Pressure 4 click. The library also contains an example application, which demonstrates their use. This example application can be used as a reference for custom designs.
Features overview
Development board
Arduino UNO is a versatile microcontroller board built around the ATmega328P chip. It offers extensive connectivity options for various projects, featuring 14 digital input/output pins, six of which are PWM-capable, along with six analog inputs. Its core components include a 16MHz ceramic resonator, a USB connection, a power jack, an
ICSP header, and a reset button, providing everything necessary to power and program the board. The Uno is ready to go, whether connected to a computer via USB or powered by an AC-to-DC adapter or battery. As the first USB Arduino board, it serves as the benchmark for the Arduino platform, with "Uno" symbolizing its status as the
first in a series. This name choice, meaning "one" in Italian, commemorates the launch of Arduino Software (IDE) 1.0. Initially introduced alongside version 1.0 of the Arduino Software (IDE), the Uno has since become the foundational model for subsequent Arduino releases, embodying the platform's evolution.
Microcontroller Overview
MCU Card / MCU
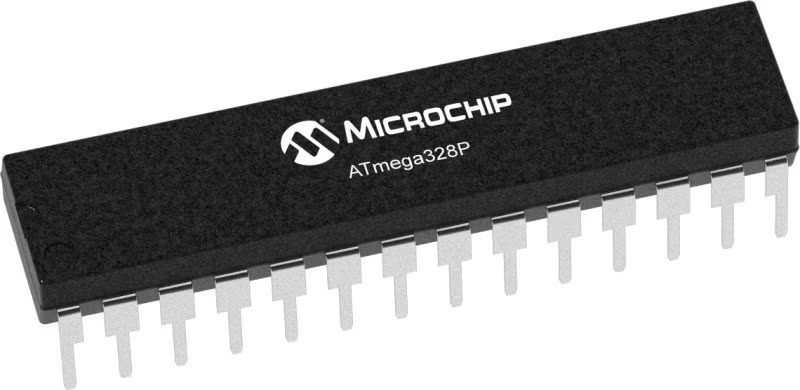
Architecture
AVR
MCU Memory (KB)
32
Silicon Vendor
Microchip
Pin count
28
RAM (Bytes)
2048
You complete me!
Accessories
Click Shield for Arduino UNO has two proprietary mikroBUS™ sockets, allowing all the Click board™ devices to be interfaced with the Arduino UNO board without effort. The Arduino Uno, a microcontroller board based on the ATmega328P, provides an affordable and flexible way for users to try out new concepts and build prototypes with the ATmega328P microcontroller from various combinations of performance, power consumption, and features. The Arduino Uno has 14 digital input/output pins (of which six can be used as PWM outputs), six analog inputs, a 16 MHz ceramic resonator (CSTCE16M0V53-R0), a USB connection, a power jack, an ICSP header, and reset button. Most of the ATmega328P microcontroller pins are brought to the IO pins on the left and right edge of the board, which are then connected to two existing mikroBUS™ sockets. This Click Shield also has several switches that perform functions such as selecting the logic levels of analog signals on mikroBUS™ sockets and selecting logic voltage levels of the mikroBUS™ sockets themselves. Besides, the user is offered the possibility of using any Click board™ with the help of existing bidirectional level-shifting voltage translators, regardless of whether the Click board™ operates at a 3.3V or 5V logic voltage level. Once you connect the Arduino UNO board with our Click Shield for Arduino UNO, you can access hundreds of Click boards™, working with 3.3V or 5V logic voltage levels.
Used MCU Pins
mikroBUS™ mapper
Take a closer look
Click board™ Schematic
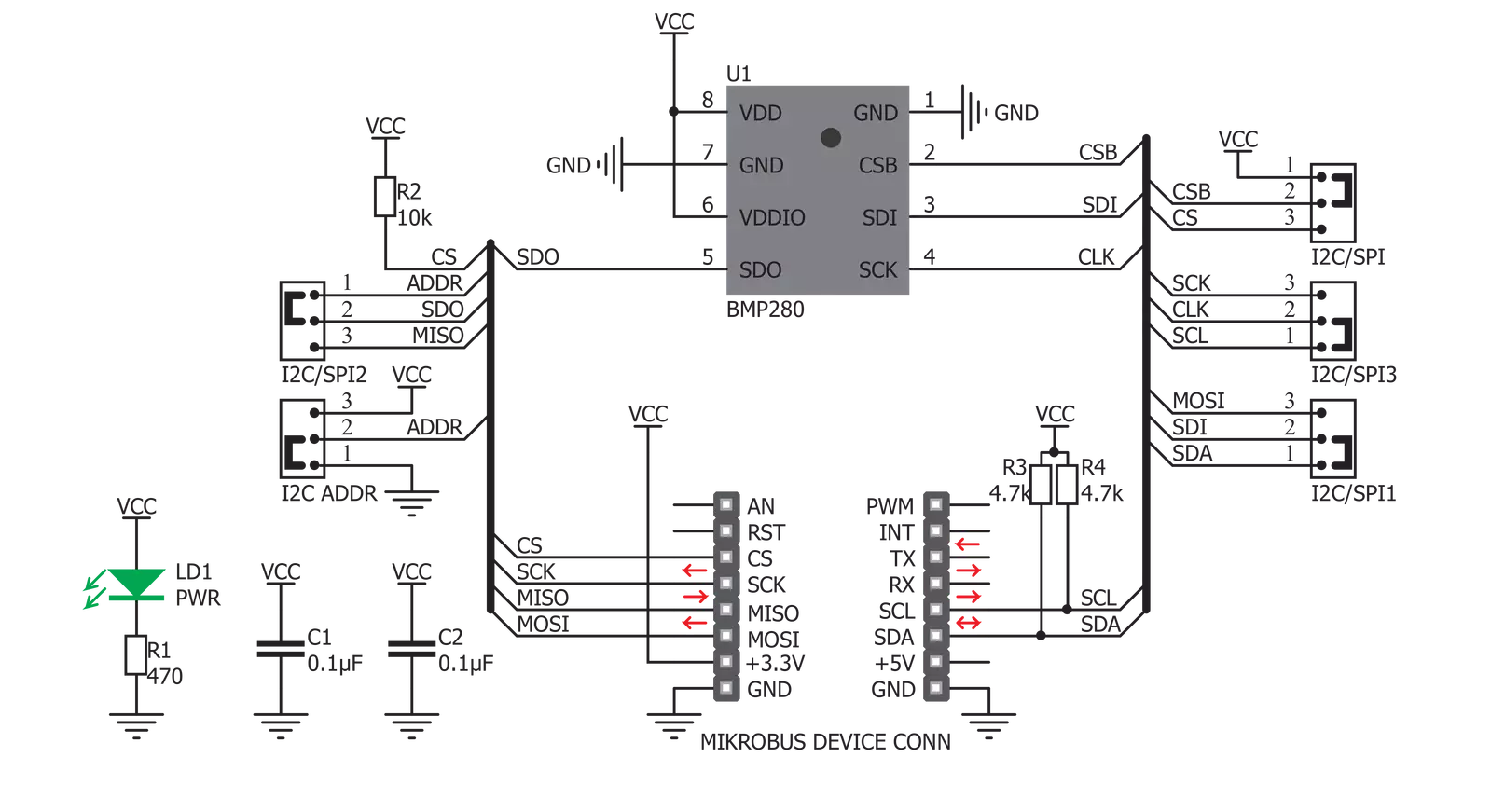
Step by step
Project assembly
Track your results in real time
Application Output
1. Application Output - In Debug mode, the 'Application Output' window enables real-time data monitoring, offering direct insight into execution results. Ensure proper data display by configuring the environment correctly using the provided tutorial.
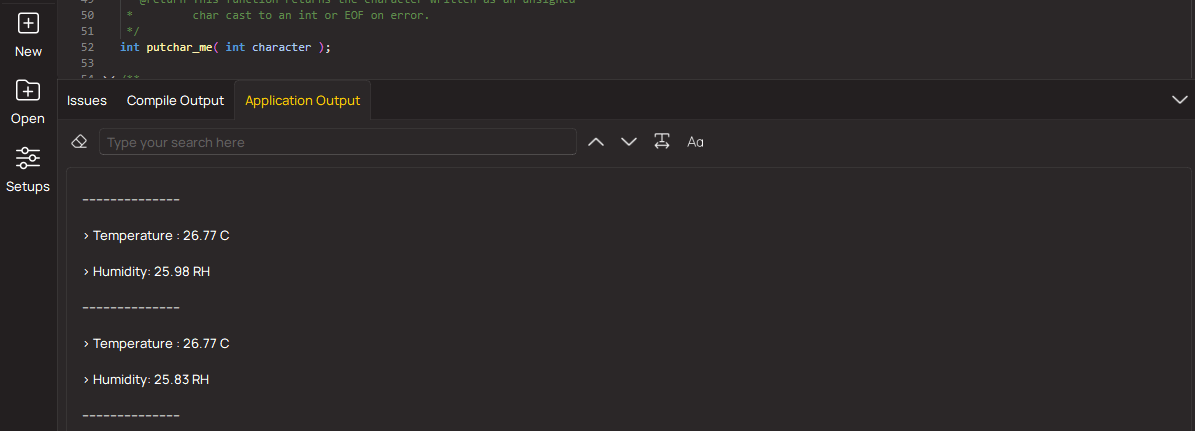
2. UART Terminal - Use the UART Terminal to monitor data transmission via a USB to UART converter, allowing direct communication between the Click board™ and your development system. Configure the baud rate and other serial settings according to your project's requirements to ensure proper functionality. For step-by-step setup instructions, refer to the provided tutorial.
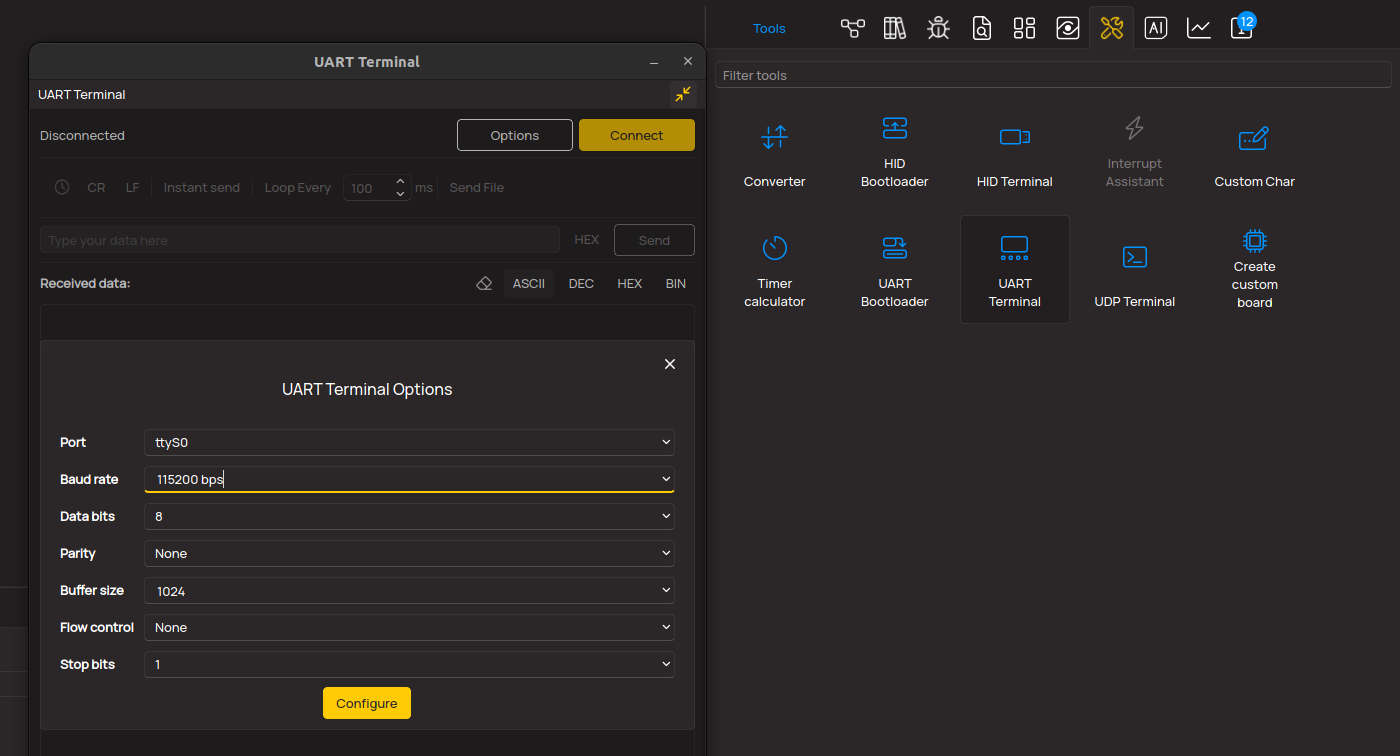
3. Plot Output - The Plot feature offers a powerful way to visualize real-time sensor data, enabling trend analysis, debugging, and comparison of multiple data points. To set it up correctly, follow the provided tutorial, which includes a step-by-step example of using the Plot feature to display Click board™ readings. To use the Plot feature in your code, use the function: plot(*insert_graph_name*, variable_name);. This is a general format, and it is up to the user to replace 'insert_graph_name' with the actual graph name and 'variable_name' with the parameter to be displayed.
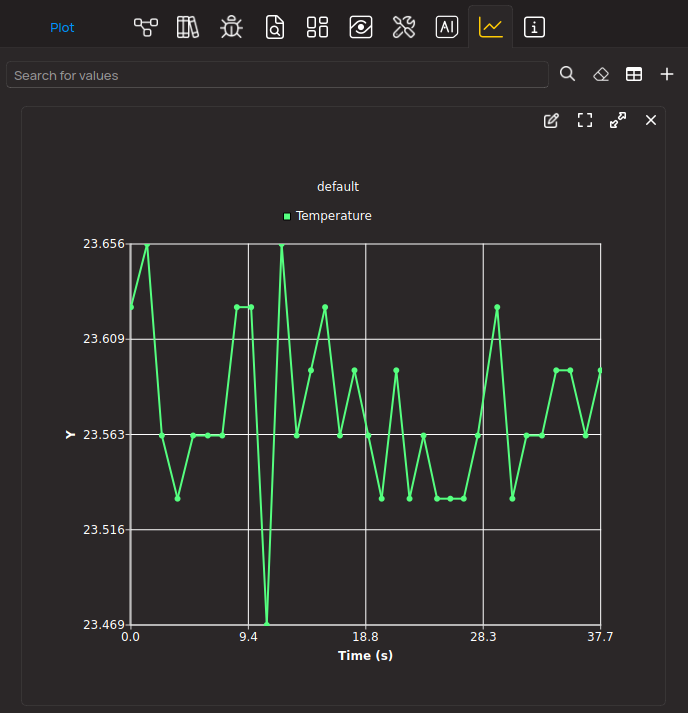
Software Support
Library Description
This library contains API for Pressure 4 Click driver.
Key functions:
pressure4_read_id
- This function returns the contents of the chipid registerpressure4_get_temperature
- This function returning the calculated temperature valuepressure4_get_pressure
- This function returning the calculated value of the pressure
Open Source
Code example
The complete application code and a ready-to-use project are available through the NECTO Studio Package Manager for direct installation in the NECTO Studio. The application code can also be found on the MIKROE GitHub account.
/*!
* \file
* \brief Pressure4 Click example
*
* # Description
* This app measure barometric pressure.
*
* The demo application is composed of two sections :
*
* ## Application Init
* Initializes the Click board.
*
* ## Application Task
* The pressure and temperature data is read from the sensor
* and it is printed to the UART.
*
* \author MikroE Team
*
*/
// ------------------------------------------------------------------- INCLUDES
#include "board.h"
#include "log.h"
#include "pressure4.h"
// ------------------------------------------------------------------ VARIABLES
static pressure4_t pressure4;
static log_t logger;
// ------------------------------------------------------ APPLICATION FUNCTIONS
void application_init ( void )
{
log_cfg_t log_cfg;
pressure4_cfg_t cfg;
/**
* Logger initialization.
* Default baud rate: 115200
* Default log level: LOG_LEVEL_DEBUG
* @note If USB_UART_RX and USB_UART_TX
* are defined as HAL_PIN_NC, you will
* need to define them manually for log to work.
* See @b LOG_MAP_USB_UART macro definition for detailed explanation.
*/
LOG_MAP_USB_UART( log_cfg );
log_init( &logger, &log_cfg );
log_info( &logger, " Application Init " );
// Click initialization.
pressure4_cfg_setup( &cfg );
PRESSURE4_MAP_MIKROBUS( cfg, MIKROBUS_1 );
pressure4_init( &pressure4, &cfg );
pressure4_default_cfg( &pressure4 );
log_info( &logger, " Application Task " );
}
void application_task ( void )
{
float pressure = 0;
float temperature = 0;
temperature = pressure4_get_temperature( &pressure4 );
log_printf( &logger, "Temperature : %.2f degC\r\n", temperature );
Delay_ms ( 100 );
pressure = pressure4_get_pressure( &pressure4 );
log_printf( &logger, "Pressure : %.2f mBar\r\n", pressure );
log_printf( &logger, "========================\r\n" );
Delay_ms ( 500 );
}
int main ( void )
{
/* Do not remove this line or clock might not be set correctly. */
#ifdef PREINIT_SUPPORTED
preinit();
#endif
application_init( );
for ( ; ; )
{
application_task( );
}
return 0;
}
// ------------------------------------------------------------------------ END
Additional Support
Resources
Category:Pressure