The ultimate DC motor driving solution
A
A
Hardware Overview
How does it work?
DC Motor 12 Click is based on the TB9054FTG, a dual-channel, H-bridge, brushed DC motor driver from Toshiba Semiconductor. The TB9054FTG allows a dual configuration with two motors with 5A current ratings per channel or one 10A channel drive in a Parallel mode of operation. It is also rated for an operating voltage range from 4.5V to 28V, with the motor controlled directly through an SPI serial interface or PWM signal from an unpopulated header. The PWM control with low on-resistance enables highly efficient motor drive output, ensuring reliable operation for highly competitive automotive applications. Besides the SPI communication, several GPIO pins connected to the mikroBUS™ socket pins are also used to control the TB9054FTG associated with the PCA9538A I2C-configurable port expander, such as Sleep Mode pin and DC motor channels current monitor routed to the RST and AN pins (SLP and CM) of the mikroBUS™ socket. The PCA9538A also allows choosing the least significant bit (LSB) of its I2C slave address by positioning SMD jumpers labeled as ADDR SEL
to an appropriate position marked as 0 and 1, alongside its interrupt feature routed to the INT pin of the mikroBUS™ socket. As mentioned, this Click board™ supports double or single DC motor configuration. The corresponding switches on the board marked with SW1-SW4 are used to select the motor control and operational modes. The first two represent the switches for motor control selection - more precisely, the choice of control directly by the PWM signal or through the SPI interface - while the second two represent the selection of the motor operational mode. There are four possible modes, i.e., Small mode (two independent channels), Large Mode (two channels are connected and support one DC motor), Half Mode, and Prohibited Mode, where the channels are completely disabled. The control and PWM signals can also be brought externally via the onboard header J1. In that case, the PWM1 and PWM2 pins specify forward, reverse, or brake modes for motor 1, and the PWM3 and PWM4 pins specify these modes for motor 2. The enable EN pins select the drive or stop mode for the motor.
A broad range of configuration options for control and mode selections can be found in the attached datasheet. This Click board™ also has additional LEDs for anomaly indication. Suppose a state such as an overtemperature or overcurrent/under voltage is detected. In that case, a such anomaly is indicated by red LEDs marked as DIAG1 and DIAG2 associated with the interrupt pin. The DC Motor 12 supports an external power supply for the TB9054FTG, which can be connected to the input terminal labeled as VM and should be within the range of 4.5V to 28V, while the DC motor coils can be connected to the terminals labeled from OUT1 up to OUT4. This Click board™ can operate with either 3.3V or 5V logic voltage levels selected via the VCC SEL jumper. This way, both 3.3V and 5V capable MCUs can use the communication lines properly. However, the Click board™ comes equipped with a library containing easy-to-use functions and an example code that can be used, as a reference, for further development.
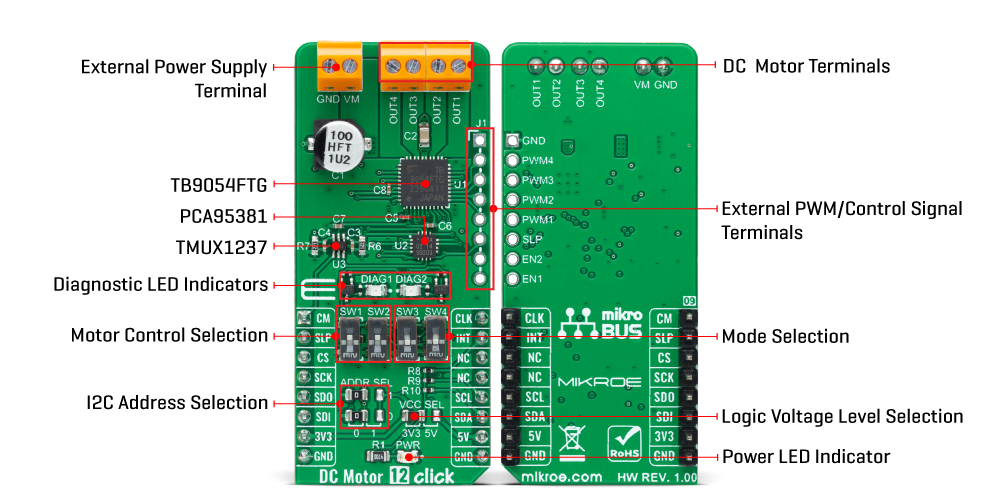
Features overview
Development board
Arduino Mega 2560 is a robust microcontroller platform built around the ATmega 2560 chip. It has extensive capabilities and boasts 54 digital input/output pins, including 15 PWM outputs, 16 analog inputs, and 4 UARTs. With a 16MHz crystal
oscillator ensuring precise timing, it offers seamless connectivity via USB, a convenient power jack, an ICSP header, and a reset button. This all-inclusive board simplifies microcontroller projects; connect it to your computer via USB or power it up
using an AC-to-DC adapter or battery. Notably, the Mega 2560 maintains compatibility with a wide range of shields crafted for the Uno, Duemilanove, or Diecimila boards, ensuring versatility and ease of integration.
Microcontroller Overview
MCU Card / MCU
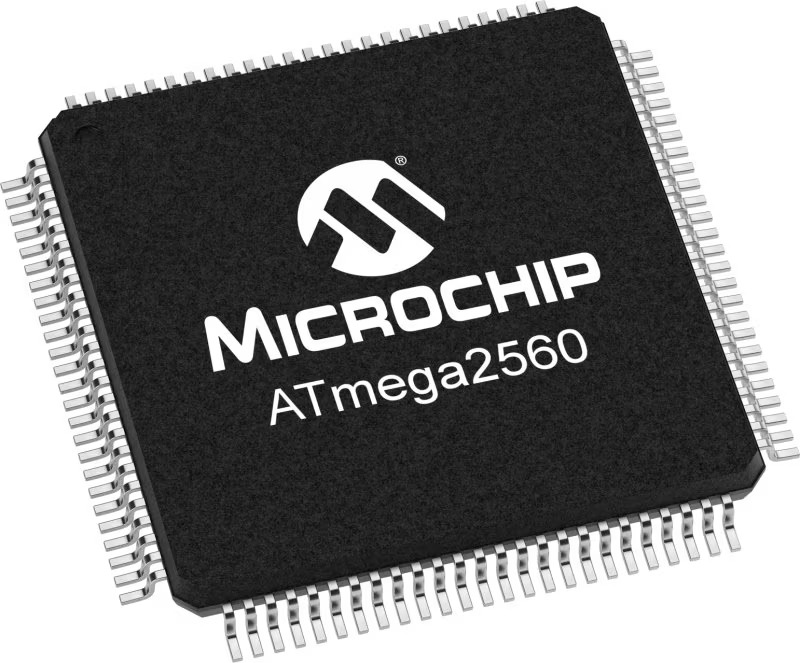
Architecture
AVR
MCU Memory (KB)
256
Silicon Vendor
Microchip
Pin count
100
RAM (Bytes)
8192
You complete me!
Accessories
Click Shield for Arduino Mega comes equipped with four mikroBUS™ sockets, with two in the form of a Shuttle connector, allowing all the Click board™ devices to be interfaced with the Arduino Mega board with no effort. Featuring an AVR 8-bit microcontroller with advanced RISC architecture, 54 digital I/O pins, and Arduino™ compatibility, the Arduino Mega board offers limitless possibilities for prototyping and creating diverse applications. This board is controlled and powered conveniently through a USB connection to program and debug the Arduino Mega board efficiently out of the box, with an additional USB cable connected to the USB B port on the board. Simplify your project development with the integrated ATmega16U2 programmer and unleash creativity using the extensive I/O options and expansion capabilities. There are eight switches, which you can use as inputs, and eight LEDs, which can be used as outputs of the MEGA2560. In addition, the shield features the MCP1501, a high-precision buffered voltage reference from Microchip. This reference is selected by default over the EXT REF jumper at the bottom of the board. You can choose an external one, as you would usually do with an Arduino Mega board. There is also a GND hook for testing purposes. Four additional LEDs are PWR, LED (standard pin D13), RX, and TX LEDs connected to UART1 (mikroBUS™ 1 socket). This Click Shield also has several switches that perform functions such as selecting the logic levels of analog signals on mikroBUS™ sockets and selecting logic voltage levels of the mikroBUS™ sockets themselves. Besides, the user is offered the possibility of using any Click board™ with the help of existing bidirectional level-shifting voltage translators, regardless of whether the Click board™ operates at a 3.3V or 5V logic voltage level. Once you connect the Arduino Mega board with Click Shield for Arduino Mega, you can access hundreds of Click boards™, working with 3.3V or 5V logic voltage levels.
DC Gear Motor - 430RPM (3-6V) represents an all-in-one combination of a motor and gearbox, where the addition of gear leads to a reduction of motor speed while increasing the torque output. This gear motor has a spur gearbox, making it a highly reliable solution for applications with lower torque and speed requirements. The most critical parameters for gear motors are speed, torque, and efficiency, which are, in this case, 520RPM with no load and 430RPM at maximum efficiency, alongside a current of 60mA and a torque of 50g.cm. Rated for a 3-6V operational voltage range and clockwise/counterclockwise rotation direction, this motor represents an excellent solution for many functions initially performed by brushed DC motors in robotics, medical equipment, electric door locks, and much more.
Used MCU Pins
mikroBUS™ mapper
Take a closer look
Click board™ Schematic
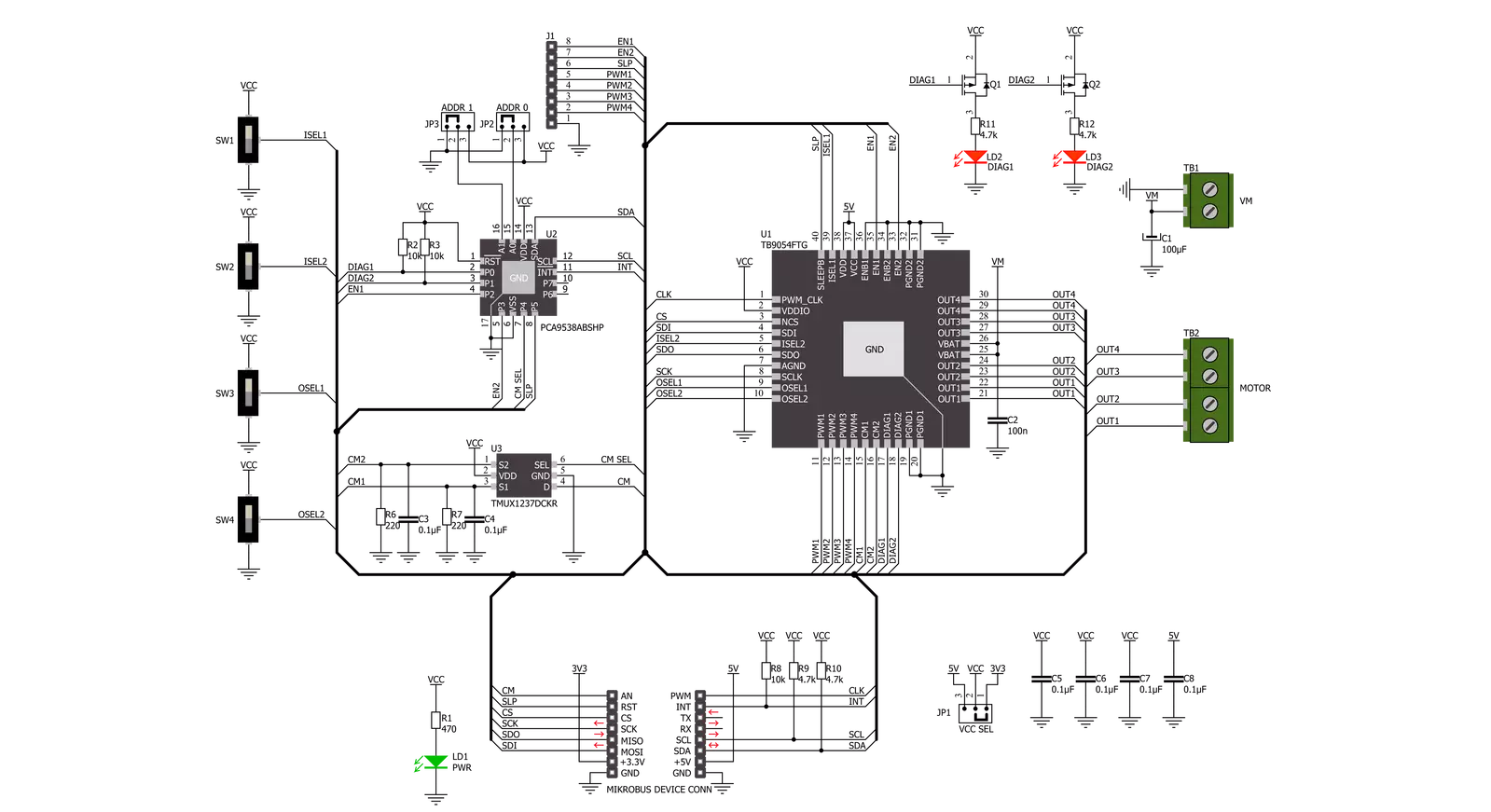
Step by step
Project assembly
Track your results in real time
Application Output
1. Application Output - In Debug mode, the 'Application Output' window enables real-time data monitoring, offering direct insight into execution results. Ensure proper data display by configuring the environment correctly using the provided tutorial.
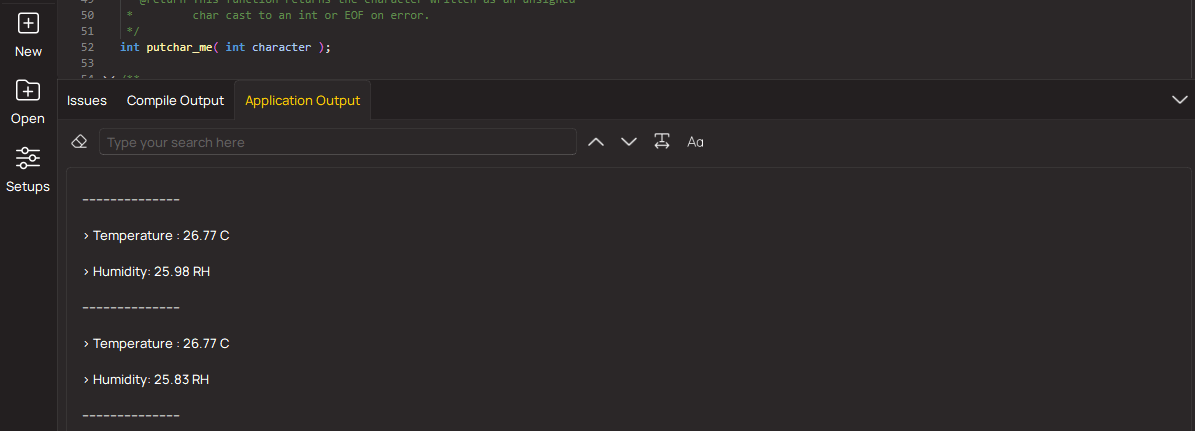
2. UART Terminal - Use the UART Terminal to monitor data transmission via a USB to UART converter, allowing direct communication between the Click board™ and your development system. Configure the baud rate and other serial settings according to your project's requirements to ensure proper functionality. For step-by-step setup instructions, refer to the provided tutorial.
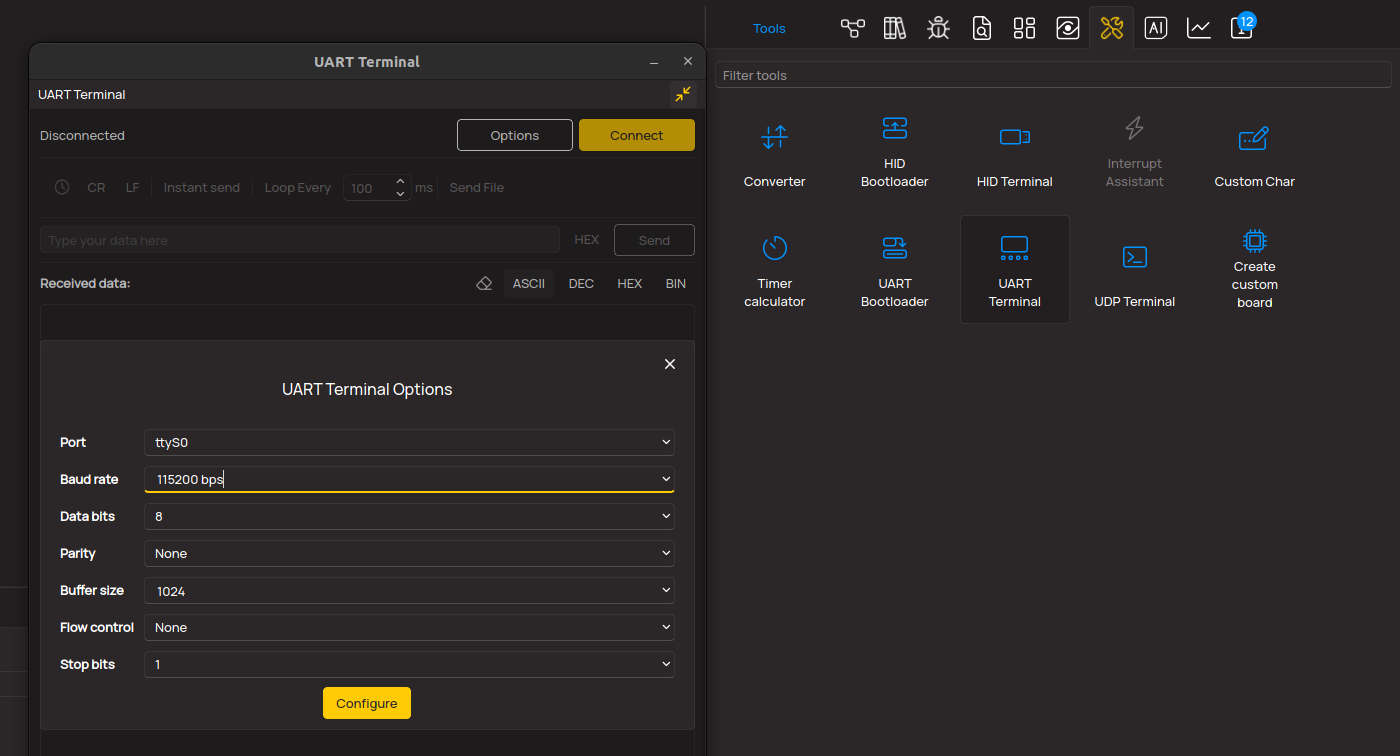
3. Plot Output - The Plot feature offers a powerful way to visualize real-time sensor data, enabling trend analysis, debugging, and comparison of multiple data points. To set it up correctly, follow the provided tutorial, which includes a step-by-step example of using the Plot feature to display Click board™ readings. To use the Plot feature in your code, use the function: plot(*insert_graph_name*, variable_name);. This is a general format, and it is up to the user to replace 'insert_graph_name' with the actual graph name and 'variable_name' with the parameter to be displayed.
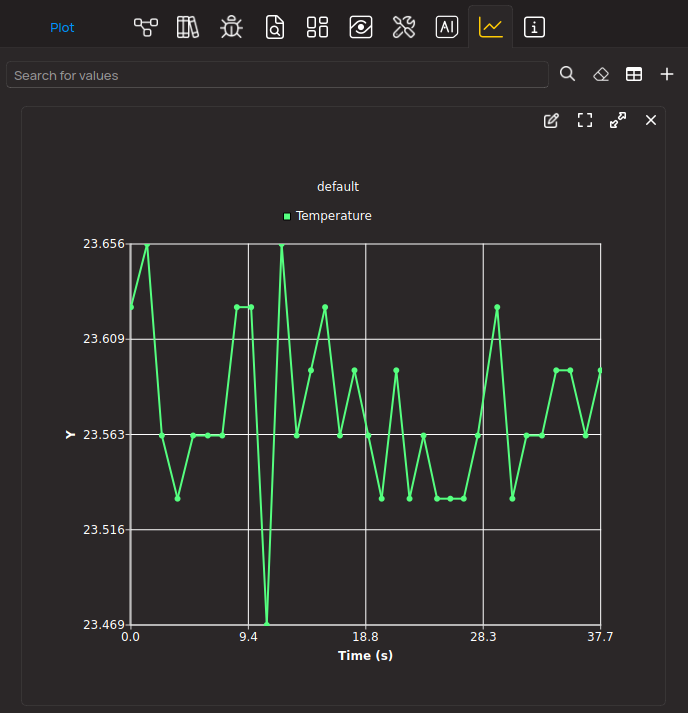
Software Support
Library Description
This library contains API for DC Motor 12 Click driver.
Key functions:
dcmotor12_get_motor_current
DC Motor 12 get motor current function.dcmotor12_set_ch1_operation_mode
DC Motor 12 set ch1 operation mode function.dcmotor12_set_cm_sel_pin
DC Motor 12 set cm sel pin function.
Open Source
Code example
The complete application code and a ready-to-use project are available through the NECTO Studio Package Manager for direct installation in the NECTO Studio. The application code can also be found on the MIKROE GitHub account.
/*!
* @file main.c
* @brief DC Motor 12 Click example
*
* # Description
* This example demonstrates the use of DC Motor 12 click board by controlling the speed
* of DC motor over PWM duty cycle as well as displaying the motor current consumption.
*
* The demo application is composed of two sections :
*
* ## Application Init
* Initializes the driver and performs the click default configuration.
*
* ## Application Task
* Changes the operation mode and motor speed by setting the PWM duty cycle and then calculates
* the motor current consumption for that speed. All data is being logged on the USB UART
* where you can track changes.
*
* @note
* The click board swiches should be set as follows: SW 1-2-3-4 : H-H-L-L
* This sets the click board as a SPI controlled single-channel device so
* the motor should be connected to OUT1/2 and OUT3/4.
*
* @author Stefan Filipovic
*
*/
#include "board.h"
#include "log.h"
#include "dcmotor12.h"
static dcmotor12_t dcmotor12;
static log_t logger;
void application_init ( void )
{
log_cfg_t log_cfg; /**< Logger config object. */
dcmotor12_cfg_t dcmotor12_cfg; /**< Click config object. */
/**
* Logger initialization.
* Default baud rate: 115200
* Default log level: LOG_LEVEL_DEBUG
* @note If USB_UART_RX and USB_UART_TX
* are defined as HAL_PIN_NC, you will
* need to define them manually for log to work.
* See @b LOG_MAP_USB_UART macro definition for detailed explanation.
*/
LOG_MAP_USB_UART( log_cfg );
log_init( &logger, &log_cfg );
log_info( &logger, " Application Init " );
// Click initialization.
dcmotor12_cfg_setup( &dcmotor12_cfg );
DCMOTOR12_MAP_MIKROBUS( dcmotor12_cfg, MIKROBUS_1 );
if ( DCMOTOR12_OK != dcmotor12_init( &dcmotor12, &dcmotor12_cfg ) )
{
log_error( &logger, " Communication init." );
for ( ; ; );
}
if ( DCMOTOR12_OK != dcmotor12_default_cfg ( &dcmotor12 ) )
{
log_error( &logger, " Default configuration." );
for ( ; ; );
}
log_info( &logger, " Application Task " );
}
void application_task ( void )
{
if ( DCMOTOR12_OK == dcmotor12_set_ch1_operation_mode ( &dcmotor12, DCMOTOR12_MODE_OUTPUT_OFF ) )
{
log_printf ( &logger, " MODE: OFF\r\n" );
Delay_ms ( 3000 );
}
if ( DCMOTOR12_OK == dcmotor12_set_ch1_operation_mode ( &dcmotor12, DCMOTOR12_MODE_FORWARD ) )
{
dcmotor12_set_cm_sel_pin ( &dcmotor12, DCMOTOR12_PIN_LOW_LEVEL );
for ( uint16_t duty = 0; duty <= DCMOTOR12_CONFIG56_DUTY_PERIOD_MAX; duty += 100 )
{
float current;
log_printf ( &logger, " MODE: FORWARD\r\n" );
if ( DCMOTOR12_OK == dcmotor12_set_ch1_duty_period ( &dcmotor12, duty ) )
{
log_printf ( &logger, " Duty: %u\r\n", duty );
}
if ( DCMOTOR12_OK == dcmotor12_get_motor_current ( &dcmotor12, ¤t ) )
{
log_printf ( &logger, " Current: %.3f A\r\n\n", current );
}
Delay_ms ( 500 );
}
}
if ( DCMOTOR12_OK == dcmotor12_set_ch1_operation_mode ( &dcmotor12, DCMOTOR12_MODE_BRAKE ) )
{
log_printf ( &logger, " MODE: BRAKE\r\n" );
Delay_ms ( 3000 );
}
if ( DCMOTOR12_OK == dcmotor12_set_ch1_operation_mode ( &dcmotor12, DCMOTOR12_MODE_REVERSE ) )
{
dcmotor12_set_cm_sel_pin ( &dcmotor12, DCMOTOR12_PIN_HIGH_LEVEL );
for ( uint16_t duty = 0; duty <= DCMOTOR12_CONFIG56_DUTY_PERIOD_MAX; duty += 100 )
{
float current;
log_printf ( &logger, " MODE: REVERSE\r\n" );
if ( DCMOTOR12_OK == dcmotor12_set_ch1_duty_period ( &dcmotor12, duty ) )
{
log_printf ( &logger, " Duty: %u\r\n", duty );
}
if ( DCMOTOR12_OK == dcmotor12_get_motor_current ( &dcmotor12, ¤t ) )
{
log_printf ( &logger, " Current: %.3f A\r\n\n", current );
}
Delay_ms ( 500 );
}
}
}
void main ( void )
{
application_init( );
for ( ; ; )
{
application_task( );
}
}
// ------------------------------------------------------------------------ END
Additional Support
Resources
Category:Brushed