Brushless DC motor control ideal for precise speed and direction adjustments in cooling systems, automation, and precision machinery
A
A
Hardware Overview
How does it work?
Brushless 10 Click is based on the TC78B016FTG, a 3-phase sine-wave PWM driver for brushless DC motors from Toshiba Semiconductor. This driver is equipped with Toshiba's Intelligent Phase Control (InPAC), an advanced feature designed to automate the motor's phase adjustment. Doing so negates manual calibration, streamlines the setup process, and boosts the motor's efficiency. Primarily utilized in fan motors, this driver leverages its phase adjustment capability to enhance operational efficiency significantly. The TC78B016FTG has several control and diagnostic features to effectively manage and monitor brushless DC motors. The FGO (Rotational Speed Output) function produces a rotation pulse derived from hall sensors, offering a choice between one or three pulses per electrical angle, configurable via an FG switch or an onboard DAC if R26 is populated. This allows for a HIGH logic level (logic 1) to emit three pulses per electrical angle and a LOW logic level (logic 0) for one pulse, visually indicating the operational mode by a blue FG LED. The motor operation can be stopped using the BRK pin, where a HIGH logic state activates the Brake function, and a LOW state resumes Normal operation. Motor speed control is managed through the TSP (Rotational Speed Command) feature, which allows startup, stop, and speed adjustments based on the PWM duty output. This feature is selectable through either analog voltage or pulse duty control, achieved via the SP switch or an onboard DAC if R25 is populated. The LD pin enhances safety by detecting abnormalities such as overcurrent, thermal shutdown, motor lockout, or under/overvoltage conditions, with visual alerts provided by a red ALR LED. Additionally, the board facilitates directional control of the motor, enabling
forward or reverse rotation through the CW/CCW switch or an onboard DAC if R22 is populated, with a LOW level for forward and HIGH for setting reverse direction. The TC78B016FTG's additional functionalities are tunable via the onboard DAC43608, which interfaces with the host MCU through an I2C connection. This DAC enables the selection of its I2C address through the ADDR SEL jumper by setting it to position 0 or 1, thereby offering a layer of customization for the communication protocol. Various motor control enhancements can be implemented through this DAC, like Lead Angle Control. This feature dynamically improves motor efficiency in response to rotation speed and current variations. This control can be activated using the LA switch for Intelligent Phase Control (InPAC) or Proportion to Frequency adjustments or through an external lead angle control, adjustable via input voltage for a range of 0° to 58° when R27 is populated. Additionally, it allows for setting a minimum output duty cycle and the configuration of Motor Lockout, determining whether the lockout function is active and its duration of operation versus pause. Furthermore, the DAC enables the selection of the motor's PWM frequency, offering options of 25kHz, 50kHz, 100kHz, or 200kHz, tailoring the motor's performance to the application's needs. Another key feature of this Click board™ is the TSTEP SEL jumper, which performs the acceleration and deceleration control of the motor. This function allows the motor to gradually increase or decrease its speed at startup, with the timing of these transitions adjustable to either 0.01 or 10 seconds based on the jumper's position. Brushless 10 Click supports an external power supply from 6V to 30V through the VM terminal and allows for current
output adjustments up to 3A, thanks to the R19 and R23 current sense resistors. Based on these populated current sense resistors, which form a value of 150mΩ, the current is rated on 1.5A. This feature ensures that the board can manage various brushless DC (BLDC) motors, including those equipped with Hall sensors, like the BLDC Motor with Hall Sensor offered by MIKROE. In addition to the motor connection terminals, the board is equipped with dedicated pins to connect these additional Hall signals, enhancing the motor's precision and efficiency. Moreover, the board can fine-tune these Hall signal inputs by using optional 4k7 pull-up resistors, which can be added via jumpers on the back of the board. Depending on the user's requirements, these jumpers can be set to an ON or OFF position, offering a layer of customization for signal integrity. Furthermore, this Click board™ is pre-configured for the operational mode of Hall IC usage, with provided additional configuration of Hall U/V/W signals based on a reference voltage provided by the TC78B016FTG. This configuration is set through front-side jumpers to Vreg/2 (2.5V) or Vreg (5V) positions. De-soldering some elements on the board is mandatory in the case of Hall element use. An orange VREG LED visually indicates this reference voltage, ensuring that users can easily verify the board's status at a glance. This Click board™ can operate with either 3.3V or 5V logic voltage levels selected via the VCC SEL jumper. This way, both 3.3V and 5V capable MCUs can use the communication lines properly. Also, this Click board™ comes equipped with a library containing easy-to-use functions and an example code that can be used as a reference for further development.
Features overview
Development board
Nucleo 32 with STM32F031K6 MCU board provides an affordable and flexible platform for experimenting with STM32 microcontrollers in 32-pin packages. Featuring Arduino™ Nano connectivity, it allows easy expansion with specialized shields, while being mbed-enabled for seamless integration with online resources. The
board includes an on-board ST-LINK/V2-1 debugger/programmer, supporting USB reenumeration with three interfaces: Virtual Com port, mass storage, and debug port. It offers a flexible power supply through either USB VBUS or an external source. Additionally, it includes three LEDs (LD1 for USB communication, LD2 for power,
and LD3 as a user LED) and a reset push button. The STM32 Nucleo-32 board is supported by various Integrated Development Environments (IDEs) such as IAR™, Keil®, and GCC-based IDEs like AC6 SW4STM32, making it a versatile tool for developers.
Microcontroller Overview
MCU Card / MCU
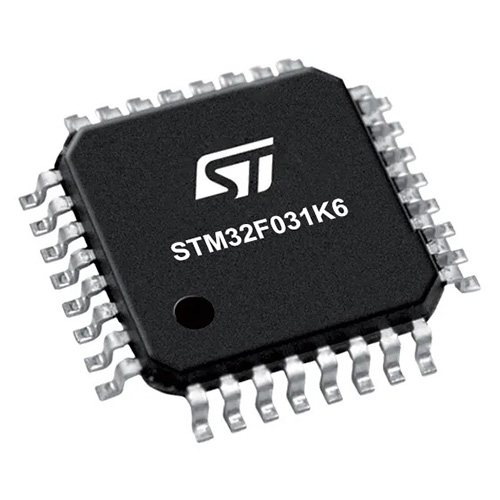
Architecture
ARM Cortex-M0
MCU Memory (KB)
32
Silicon Vendor
STMicroelectronics
Pin count
32
RAM (Bytes)
4096
You complete me!
Accessories
Click Shield for Nucleo-32 is the perfect way to expand your development board's functionalities with STM32 Nucleo-32 pinout. The Click Shield for Nucleo-32 provides two mikroBUS™ sockets to add any functionality from our ever-growing range of Click boards™. We are fully stocked with everything, from sensors and WiFi transceivers to motor control and audio amplifiers. The Click Shield for Nucleo-32 is compatible with the STM32 Nucleo-32 board, providing an affordable and flexible way for users to try out new ideas and quickly create prototypes with any STM32 microcontrollers, choosing from the various combinations of performance, power consumption, and features. The STM32 Nucleo-32 boards do not require any separate probe as they integrate the ST-LINK/V2-1 debugger/programmer and come with the STM32 comprehensive software HAL library and various packaged software examples. This development platform provides users with an effortless and common way to combine the STM32 Nucleo-32 footprint compatible board with their favorite Click boards™ in their upcoming projects.
Brushless DC (BLDC) Motor with a Hall sensor represents a high-performance motor from the 42BLF motor series. This motor, wired in a star configuration, boasts a Hall Effect angle of 120°, ensuring precise and reliable performance. With a compact motor length of 47mm and a lightweight design tipping the scales at just 0.29kg, this BLDC motor is engineered to meet your needs. Operating flawlessly at a voltage rating of 24VDC and a speed range of 4000 ± 10% RPM, this motor offers consistent and dependable power. It excels in a normal operational temperature range from -20 to +50°C, maintaining efficiency with a rated current of 1.9A. Also, this product seamlessly integrates with all Brushless Click boards™ and those that require BLDC motors with Hall sensors.
Used MCU Pins
mikroBUS™ mapper
Take a closer look
Click board™ Schematic
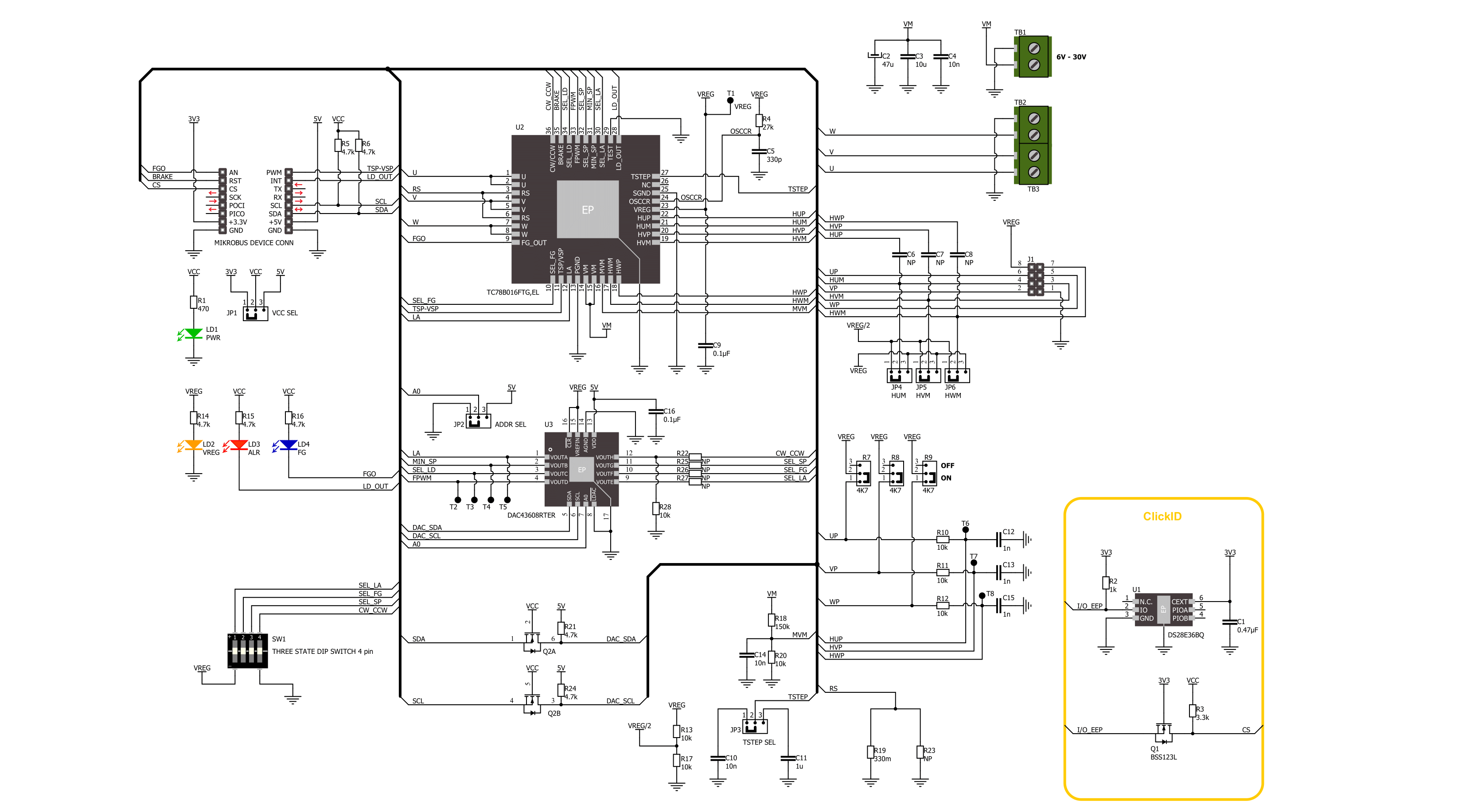
Step by step
Project assembly
Track your results in real time
Application Output
1. Application Output - In Debug mode, the 'Application Output' window enables real-time data monitoring, offering direct insight into execution results. Ensure proper data display by configuring the environment correctly using the provided tutorial.
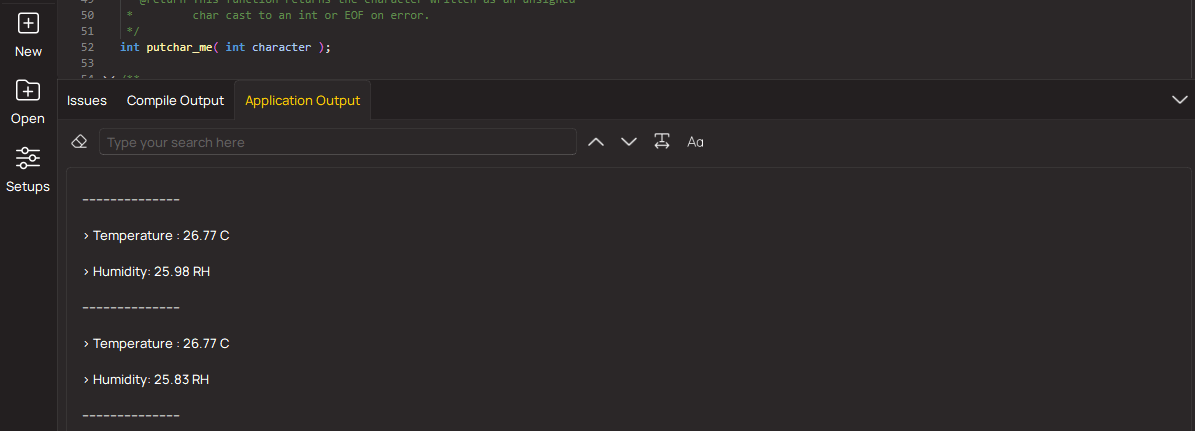
2. UART Terminal - Use the UART Terminal to monitor data transmission via a USB to UART converter, allowing direct communication between the Click board™ and your development system. Configure the baud rate and other serial settings according to your project's requirements to ensure proper functionality. For step-by-step setup instructions, refer to the provided tutorial.
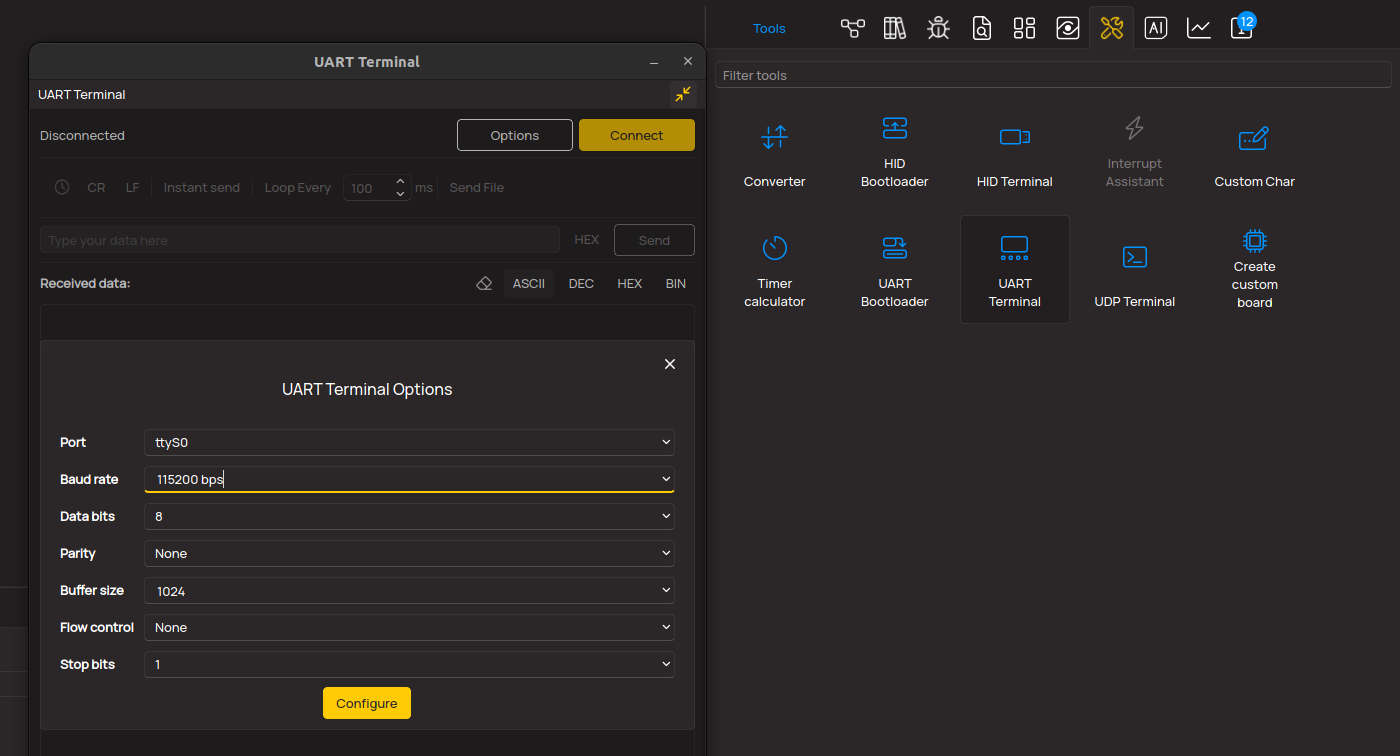
3. Plot Output - The Plot feature offers a powerful way to visualize real-time sensor data, enabling trend analysis, debugging, and comparison of multiple data points. To set it up correctly, follow the provided tutorial, which includes a step-by-step example of using the Plot feature to display Click board™ readings. To use the Plot feature in your code, use the function: plot(*insert_graph_name*, variable_name);. This is a general format, and it is up to the user to replace 'insert_graph_name' with the actual graph name and 'variable_name' with the parameter to be displayed.
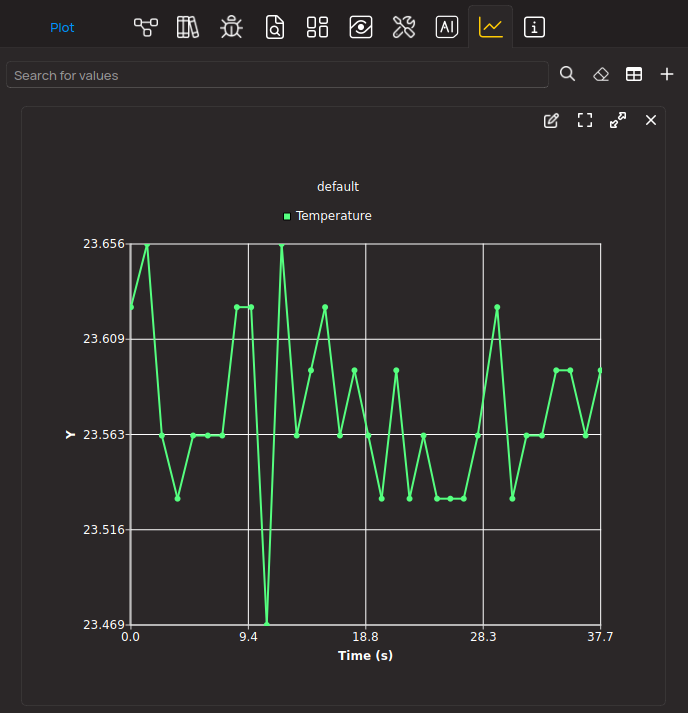
Software Support
Library Description
This library contains API for Brushless 10 Click driver.
Key functions:
brushless10_set_duty_cycle
- This function sets the PWM duty cycle in percentages ( Range[ 0..1 ] )brushless10_pull_brake
- This function pulls brake by setting the BRAKE pin to high logic statebrushless10_release_brake
- This function releases brake by setting the BRAKE pin to low logic state
Open Source
Code example
The complete application code and a ready-to-use project are available through the NECTO Studio Package Manager for direct installation in the NECTO Studio. The application code can also be found on the MIKROE GitHub account.
/*!
* @file main.c
* @brief Brushless 10 Click example
*
* # Description
* This example demonstrates the use of the Brushless 10 Click board by driving the
* motor at different speeds.
*
* The demo application is composed of two sections :
*
* ## Application Init
* Initializes the driver and performs the Click default configuration.
*
* ## Application Task
* Controls the motor speed by changing the PWM duty cycle every 2 seconds.
* The duty cycle ranges from 20% to 100%. Each step will be logged on the USB UART
* where you can track the program flow.
*
* @author Stefan Filipovic
*
*/
#include "board.h"
#include "log.h"
#include "brushless10.h"
static brushless10_t brushless10;
static log_t logger;
void application_init ( void )
{
log_cfg_t log_cfg; /**< Logger config object. */
brushless10_cfg_t brushless10_cfg; /**< Click config object. */
/**
* Logger initialization.
* Default baud rate: 115200
* Default log level: LOG_LEVEL_DEBUG
* @note If USB_UART_RX and USB_UART_TX
* are defined as HAL_PIN_NC, you will
* need to define them manually for log to work.
* See @b LOG_MAP_USB_UART macro definition for detailed explanation.
*/
LOG_MAP_USB_UART( log_cfg );
log_init( &logger, &log_cfg );
log_info( &logger, " Application Init " );
// Click initialization.
brushless10_cfg_setup( &brushless10_cfg );
BRUSHLESS10_MAP_MIKROBUS( brushless10_cfg, MIKROBUS_1 );
if ( BRUSHLESS10_OK != brushless10_init( &brushless10, &brushless10_cfg ) )
{
log_error( &logger, " Communication init." );
for ( ; ; );
}
if ( BRUSHLESS10_OK != brushless10_default_cfg ( &brushless10 ) )
{
log_error( &logger, " Default configuration." );
for ( ; ; );
}
log_info( &logger, " Application Task " );
}
void application_task ( void )
{
static int8_t duty_cnt = 2;
static int8_t duty_inc = 1;
float duty = duty_cnt / 10.0;
brushless10_set_duty_cycle ( &brushless10, duty );
log_printf( &logger, "> Duty: %d%%\r\n", ( uint16_t )( duty_cnt * 10 ) );
Delay_ms ( 1000 );
Delay_ms ( 1000 );
duty_cnt += duty_inc;
if ( duty_cnt > 10 )
{
duty_cnt = 9;
duty_inc = -1;
}
else if ( duty_cnt < 2 )
{
duty_cnt = 2;
duty_inc = 1;
log_printf( &logger, " Pull brake\r\n" );
brushless10_pull_brake ( &brushless10 );
Delay_ms ( 1000 );
Delay_ms ( 1000 );
Delay_ms ( 1000 );
log_printf( &logger, " Release brake\r\n" );
brushless10_release_brake ( &brushless10 );
Delay_ms ( 1000 );
}
}
int main ( void )
{
/* Do not remove this line or clock might not be set correctly. */
#ifdef PREINIT_SUPPORTED
preinit();
#endif
application_init( );
for ( ; ; )
{
application_task( );
}
return 0;
}
// ------------------------------------------------------------------------ END