Our solution is designed to accurately measure voltage and current through your connected load, providing critical insights into electrical performance
A
A
Hardware Overview
How does it work?
PWR Meter 3 Click is based on the ACS37800, a simple solution for voltage, current, and power monitoring from Allegro MicroSystems, which simplifies the addition of power monitoring in 60Hz to many AC/DC applications. The ACS37800 includes a copper conduction path that generates a magnetic field proportional to the applied current, sensed differentially to reject errors introduced by common mode fields. It is particularly well suited for high isolation, achieving reinforced isolation ratings of 4800 VRMS and a reliable ±90A bidirectional current sensing range. With high configurability and integrated features, this Click board™ can fit most power monitoring applications. The ACS37800 measures the voltage applied to the REF terminal, in the range from 9.5 to 27V, by resistor dividing it down to fit the input range of the onboard voltage sense amplifier and
add isolation. On the other hand, the current applied to the current sensing terminals is measured using the integrated current loop and galvanically isolated Hall sensor. Both analog signals are then sampled using integrated high-accuracy ADCs before entering the digital system. The metrology engine later determines the frequency, calculates RMS values of current, voltage, and power, and provides a range of averaging and configuration options. PWR Meter 3 Click communicates with an MCU using the standard I2C 2-Wire interface to read data and configure settings, supporting Standard Mode operation with a clock frequency of 100kHz and Fast Mode up to 400kHz. The ACS37800 can be turned on, or off through the EN pin routed to the RST pin of the mikroBUS™ socket, hence offering a switch operation to turn ON/OFF power delivery
to the ACS37800 via TPS2041B. Along with the ability to measure current and voltage, it also has two LED indicators, DIO0 and DIO1, for the realization of visual detection of some anomalies in operation, such as undervoltage and overvoltage reporting, and fast overcurrent fault detection. The DIO0 LED default state application is for zero crossing, while DIO1 stands for overcurrent detection. In addition to the LEDs, this information can be detected through the INT and AN pins of the mikroBUS™ socket, marked as D0 and D1. This Click board™ can be operated only with a 3.3V logic voltage level. The board must perform appropriate logic voltage level conversion before using MCUs with different logic levels. Also, it comes equipped with a library containing functions and an example code that can be used as a reference for further development.
Features overview
Development board
Nucleo 32 with STM32F031K6 MCU board provides an affordable and flexible platform for experimenting with STM32 microcontrollers in 32-pin packages. Featuring Arduino™ Nano connectivity, it allows easy expansion with specialized shields, while being mbed-enabled for seamless integration with online resources. The
board includes an on-board ST-LINK/V2-1 debugger/programmer, supporting USB reenumeration with three interfaces: Virtual Com port, mass storage, and debug port. It offers a flexible power supply through either USB VBUS or an external source. Additionally, it includes three LEDs (LD1 for USB communication, LD2 for power,
and LD3 as a user LED) and a reset push button. The STM32 Nucleo-32 board is supported by various Integrated Development Environments (IDEs) such as IAR™, Keil®, and GCC-based IDEs like AC6 SW4STM32, making it a versatile tool for developers.
Microcontroller Overview
MCU Card / MCU
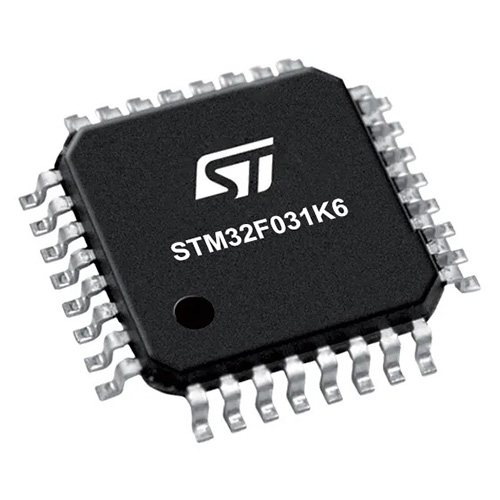
Architecture
ARM Cortex-M0
MCU Memory (KB)
32
Silicon Vendor
STMicroelectronics
Pin count
32
RAM (Bytes)
4096
You complete me!
Accessories
Click Shield for Nucleo-32 is the perfect way to expand your development board's functionalities with STM32 Nucleo-32 pinout. The Click Shield for Nucleo-32 provides two mikroBUS™ sockets to add any functionality from our ever-growing range of Click boards™. We are fully stocked with everything, from sensors and WiFi transceivers to motor control and audio amplifiers. The Click Shield for Nucleo-32 is compatible with the STM32 Nucleo-32 board, providing an affordable and flexible way for users to try out new ideas and quickly create prototypes with any STM32 microcontrollers, choosing from the various combinations of performance, power consumption, and features. The STM32 Nucleo-32 boards do not require any separate probe as they integrate the ST-LINK/V2-1 debugger/programmer and come with the STM32 comprehensive software HAL library and various packaged software examples. This development platform provides users with an effortless and common way to combine the STM32 Nucleo-32 footprint compatible board with their favorite Click boards™ in their upcoming projects.
Used MCU Pins
mikroBUS™ mapper
Take a closer look
Click board™ Schematic
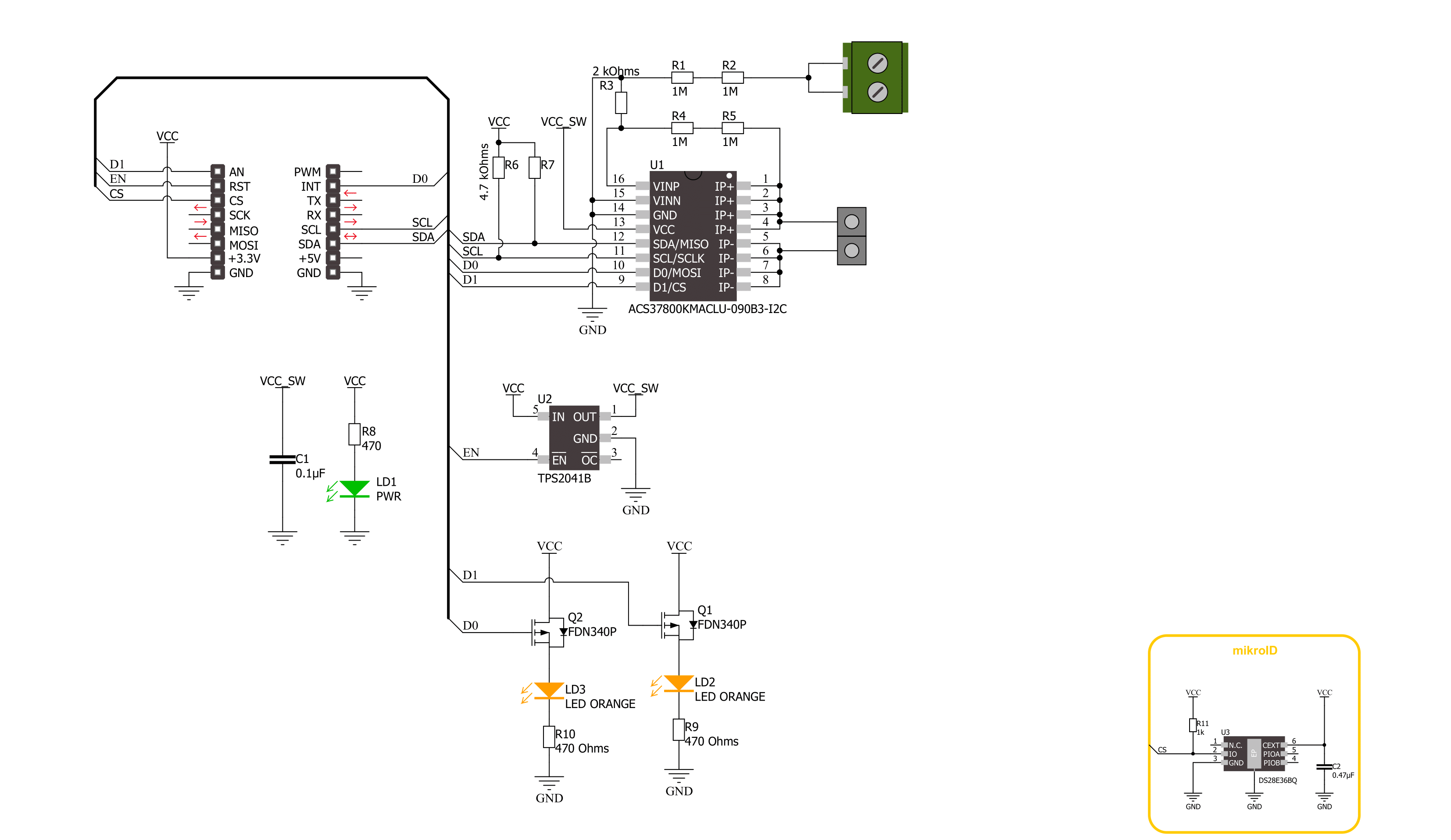
Step by step
Project assembly
Track your results in real time
Application Output
1. Application Output - In Debug mode, the 'Application Output' window enables real-time data monitoring, offering direct insight into execution results. Ensure proper data display by configuring the environment correctly using the provided tutorial.
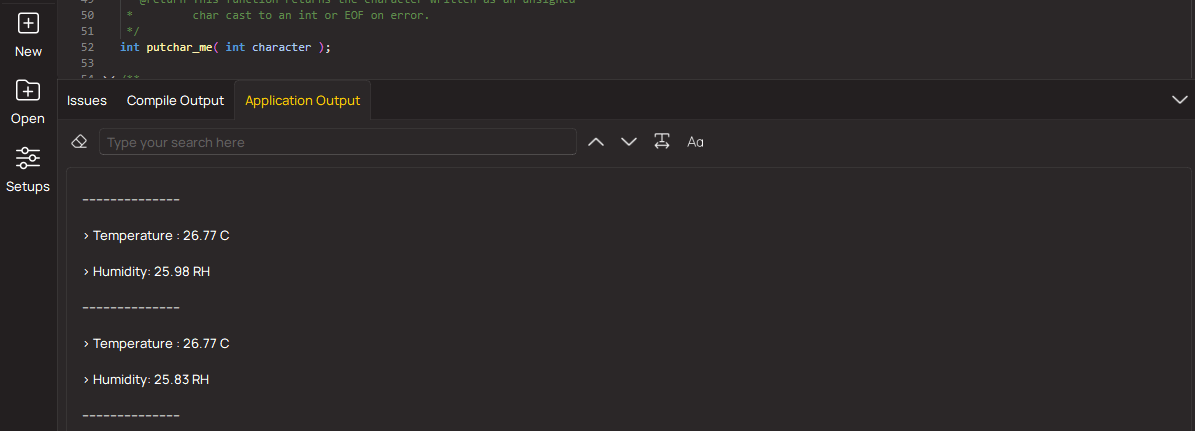
2. UART Terminal - Use the UART Terminal to monitor data transmission via a USB to UART converter, allowing direct communication between the Click board™ and your development system. Configure the baud rate and other serial settings according to your project's requirements to ensure proper functionality. For step-by-step setup instructions, refer to the provided tutorial.
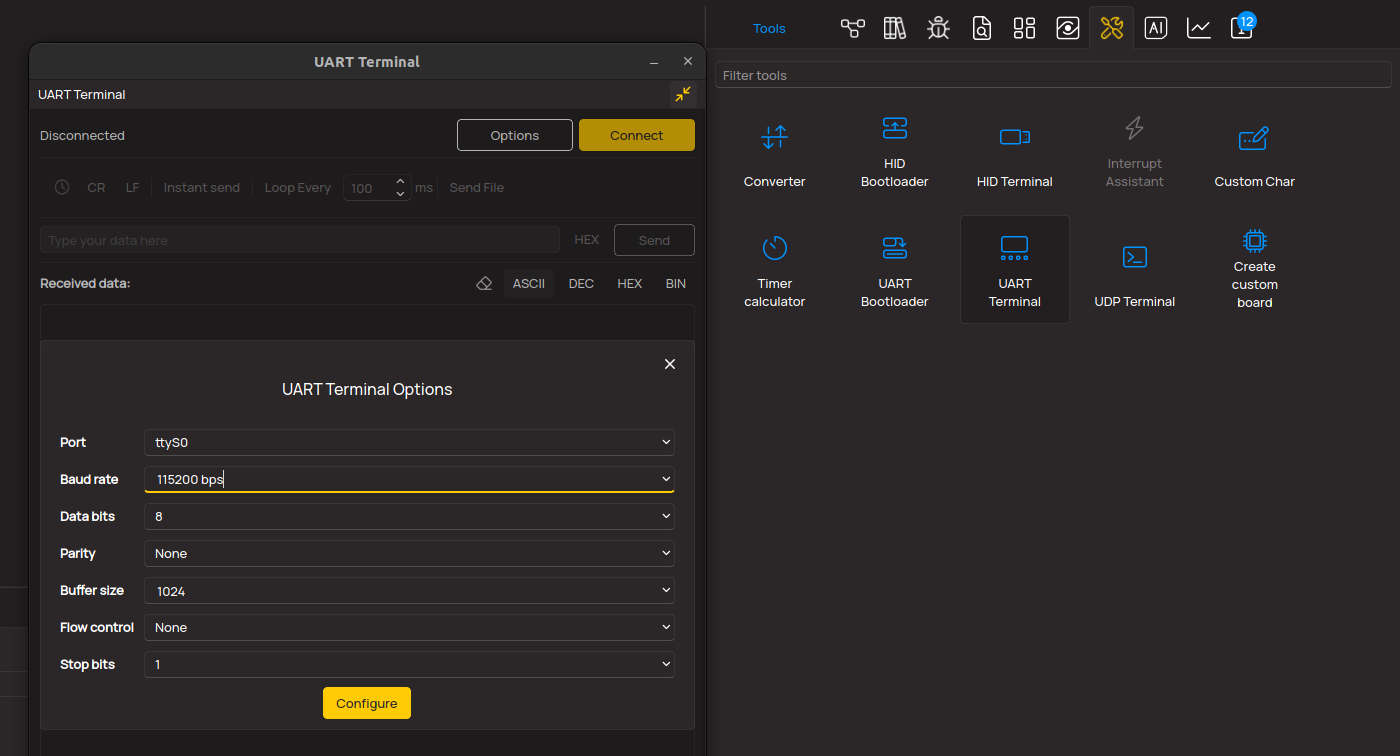
3. Plot Output - The Plot feature offers a powerful way to visualize real-time sensor data, enabling trend analysis, debugging, and comparison of multiple data points. To set it up correctly, follow the provided tutorial, which includes a step-by-step example of using the Plot feature to display Click board™ readings. To use the Plot feature in your code, use the function: plot(*insert_graph_name*, variable_name);. This is a general format, and it is up to the user to replace 'insert_graph_name' with the actual graph name and 'variable_name' with the parameter to be displayed.
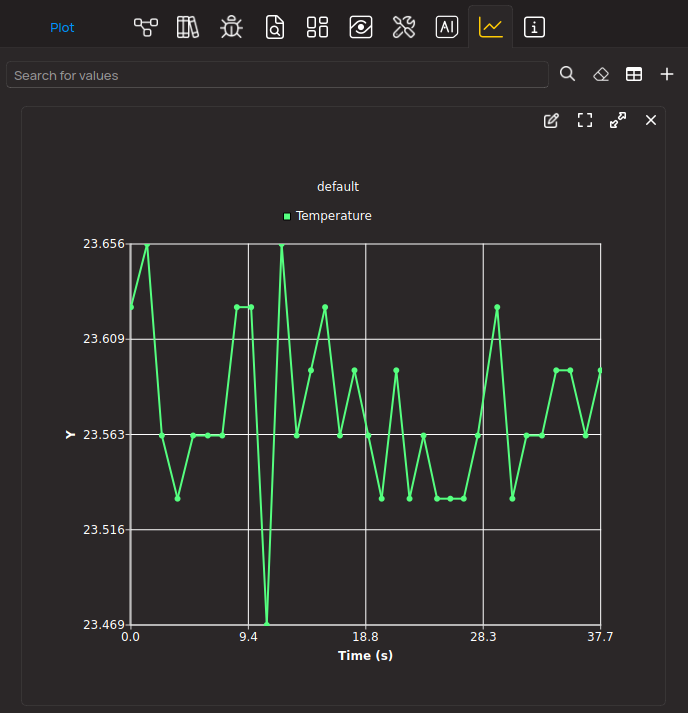
Software Support
Library Description
This library contains API for PWR Meter 3 Click driver.
Key functions:
pwrmeter3_get_dio0_pin
- This function returns the DIO0 pin logic statepwrmeter3_get_dio1_pin
- This function returns the DIO1 pin logic statepwrmeter3_read_average_rms
- This function reads the voltage and current RMS measurements averaged from a specified number of samples
Open Source
Code example
The complete application code and a ready-to-use project are available through the NECTO Studio Package Manager for direct installation in the NECTO Studio. The application code can also be found on the MIKROE GitHub account.
/*!
* @file main.c
* @brief PWR Meter 3 90A Click example
*
* # Description
* This example demonstrates the use of PWR Meter 3 90A Click board by reading and displaying
* the voltage, current, and power RMS measurements.
*
* The demo application is composed of two sections :
*
* ## Application Init
* Initializes the driver and performs the Click default configuration which sets the DC measurement
* and VRMS thresholds to about 28V for overvoltage and about 9.3V for undervoltage flag.
*
* ## Application Task
* Reads the voltage and current RMS values averaged from 500 samples, then calculates the power from it
* and displays the results on the USB UART. Also if an UV or OV flag is detected it will be logged accordingly.
*
* @author Stefan Filipovic
*
*/
#include "board.h"
#include "log.h"
#include "pwrmeter390a.h"
static pwrmeter390a_t pwrmeter390a;
static log_t logger;
void application_init ( void )
{
log_cfg_t log_cfg; /**< Logger config object. */
pwrmeter390a_cfg_t pwrmeter390a_cfg; /**< Click config object. */
/**
* Logger initialization.
* Default baud rate: 115200
* Default log level: LOG_LEVEL_DEBUG
* @note If USB_UART_RX and USB_UART_TX
* are defined as HAL_PIN_NC, you will
* need to define them manually for log to work.
* See @b LOG_MAP_USB_UART macro definition for detailed explanation.
*/
LOG_MAP_USB_UART( log_cfg );
log_init( &logger, &log_cfg );
log_info( &logger, " Application Init " );
// Click initialization.
pwrmeter390a_cfg_setup( &pwrmeter390a_cfg );
PWRMETER390A_MAP_MIKROBUS( pwrmeter390a_cfg, MIKROBUS_1 );
if ( I2C_MASTER_ERROR == pwrmeter390a_init( &pwrmeter390a, &pwrmeter390a_cfg ) )
{
log_error( &logger, " Communication init." );
for ( ; ; );
}
if ( PWRMETER390A_ERROR == pwrmeter390a_default_cfg ( &pwrmeter390a ) )
{
log_error( &logger, " Default configuration." );
for ( ; ; );
}
log_info( &logger, " Application Task " );
}
void application_task ( void )
{
float v_rms, i_rms;
if ( PWRMETER390A_OK == pwrmeter390a_read_average_rms ( &pwrmeter390a, &v_rms, &i_rms, PWRMETER390A_DEF_AVG_SAMPLES ) )
{
if ( !pwrmeter390a_get_dio0_pin ( &pwrmeter390a ) )
{
log_printf ( &logger, " Over-voltage detected!\r\n" );
}
if ( !pwrmeter390a_get_dio1_pin ( &pwrmeter390a ) )
{
log_printf ( &logger, " Under-voltage detected!\r\n" );
}
log_printf ( &logger, " Voltage: %.2f V\r\n", v_rms );
log_printf ( &logger, " Current: %.2f A\r\n", i_rms );
log_printf ( &logger, " Power: %.2f W\r\n\n", i_rms * v_rms );
}
}
int main ( void )
{
/* Do not remove this line or clock might not be set correctly. */
#ifdef PREINIT_SUPPORTED
preinit();
#endif
application_init( );
for ( ; ; )
{
application_task( );
}
return 0;
}
// ------------------------------------------------------------------------ END