Measuring heat with ease has never been simpler, thanks to our innovative temperature monitoring solution.
A
A
Hardware Overview
How does it work?
Thermo 20 Click is based on the TSYS03, an ultra-compact digital temperature sensor with precise digital output and low power consumption from TE Connectivity. The TSYS03 is factory-calibrated and provides accurate temperature measurements through several I2C configurable addresses. Operating from a supply voltage between 2.4V and 5.5V and drawing just 5µA Thermo 20 Click board™ is well suited for battery-powered and automotive applications. With an extended operating range from -40°C to +125°C, the TSYS03 provides digital temperature measurements that offer an accuracy of ±0.5°C when operating at ambient temperatures between 0°C and 60°C. The TSYS03 consists of a semiconductor
diode as a measuring element, which was integrated into an ASIC. The temperature is obtained from the voltage that drops across the diode and through an A/D converter with a 16-bit resolution. The output is obtained as a digital value via a configurable I2C interface. The TSYS03 impresses with its high accuracy, current consumption lower than 5 µA, and low self-heating of max. 0.1 °C. Thermo 20 Click communicates with MCU using the standard I2C 2-Wire interface with a maximum clock frequency of 1MHz. The standard I2C address is 0x40, but the sensor can also react to a second, alternative I2C address. It is possible to do one-time subsequent writing of an alternative static I2C address.
This leads to a wrong memory CRC, but the sensor is still functional. It is also possible to write an alternative I2C address to the sensor during operation. This address is temporary and is overwritten during a software reset or a hardware restart function. This Click board™ can operate with either 3.3V or 5V logic voltage levels selected via the VCC SEL jumper. This way, both 3.3V and 5V capable MCUs can use the communication lines properly. Also, this Click board™ comes equipped with a library containing easy-to-use functions and an example code that can be used as a reference for further development.
Features overview
Development board
UNI-DS v8 is a development board specially designed for the needs of rapid development of embedded applications. It supports a wide range of microcontrollers, such as different STM32, Kinetis, TIVA, CEC, MSP, PIC, dsPIC, PIC32, and AVR MCUs regardless of their number of pins, and a broad set of unique functions, such as the first-ever embedded debugger/programmer over WiFi. The development board is well organized and designed so that the end-user has all the necessary elements, such as switches, buttons, indicators, connectors, and others, in one place. Thanks to innovative manufacturing technology, UNI-DS v8 provides a fluid and immersive working experience, allowing access anywhere and under any
circumstances at any time. Each part of the UNI-DS v8 development board contains the components necessary for the most efficient operation of the same board. An advanced integrated CODEGRIP programmer/debugger module offers many valuable programming/debugging options, including support for JTAG, SWD, and SWO Trace (Single Wire Output)), and seamless integration with the Mikroe software environment. Besides, it also includes a clean and regulated power supply module for the development board. It can use a wide range of external power sources, including a battery, an external 12V power supply, and a power source via the USB Type-C (USB-C) connector. Communication options such as USB-UART, USB
HOST/DEVICE, CAN (on the MCU card, if supported), and Ethernet is also included. In addition, it also has the well-established mikroBUS™ standard, a standardized socket for the MCU card (SiBRAIN standard), and two display options for the TFT board line of products and character-based LCD. UNI-DS v8 is an integral part of the Mikroe ecosystem for rapid development. Natively supported by Mikroe software tools, it covers many aspects of prototyping and development thanks to a considerable number of different Click boards™ (over a thousand boards), the number of which is growing every day.
Microcontroller Overview
MCU Card / MCU
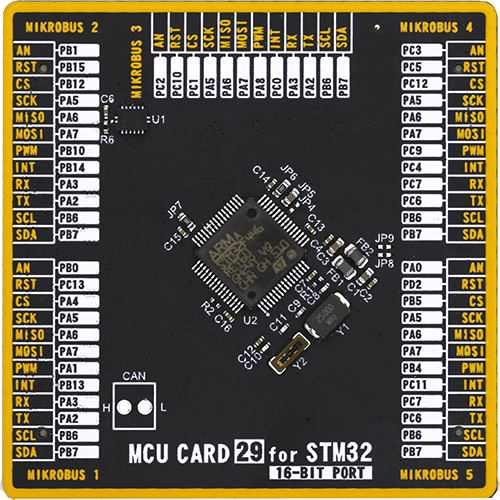
Type
8th Generation
Architecture
ARM Cortex-M4
MCU Memory (KB)
512
Silicon Vendor
STMicroelectronics
Pin count
64
RAM (Bytes)
131072
Used MCU Pins
mikroBUS™ mapper
Take a closer look
Click board™ Schematic
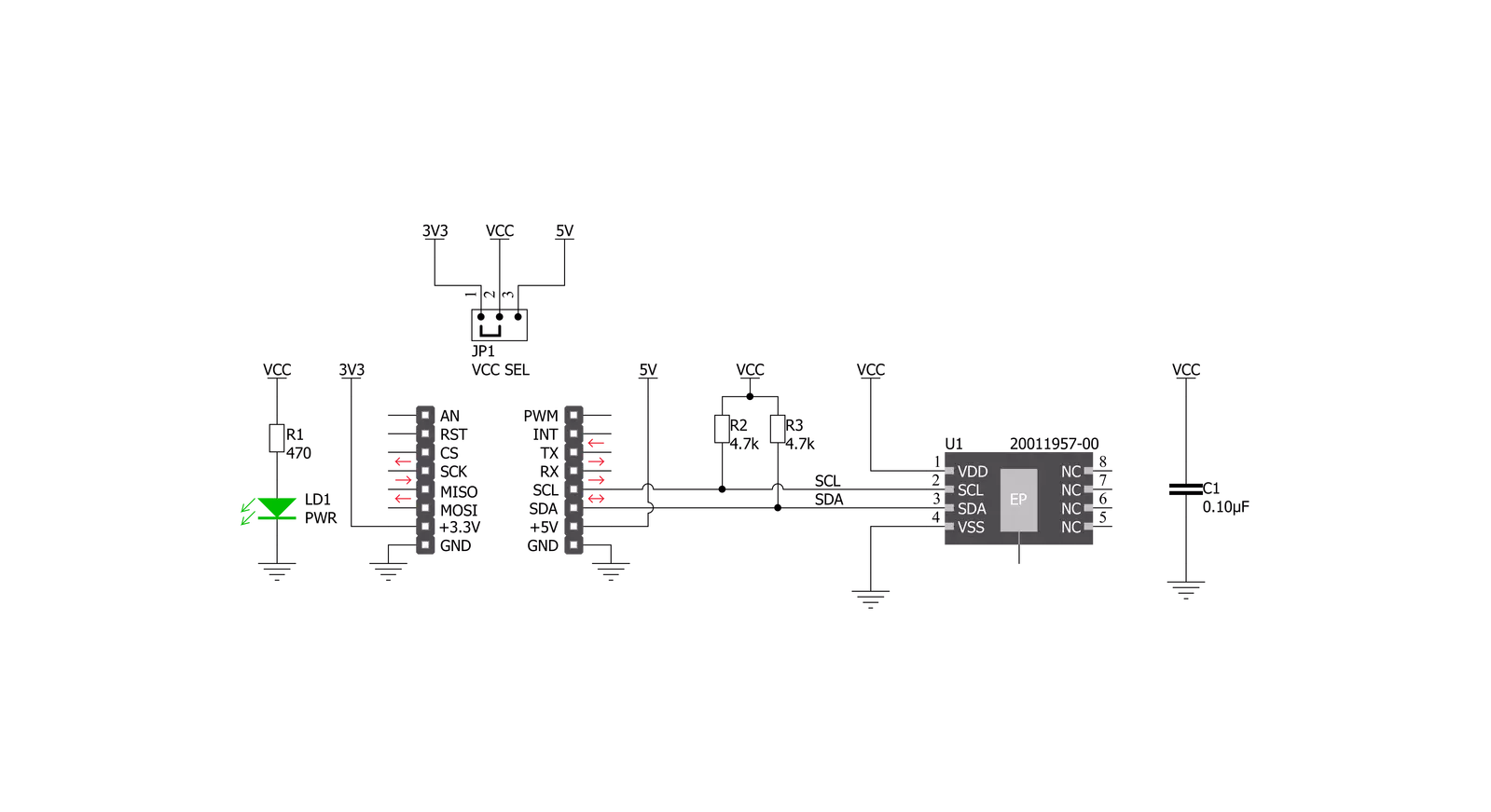
Step by step
Project assembly
Track your results in real time
Application Output
1. Application Output - In Debug mode, the 'Application Output' window enables real-time data monitoring, offering direct insight into execution results. Ensure proper data display by configuring the environment correctly using the provided tutorial.
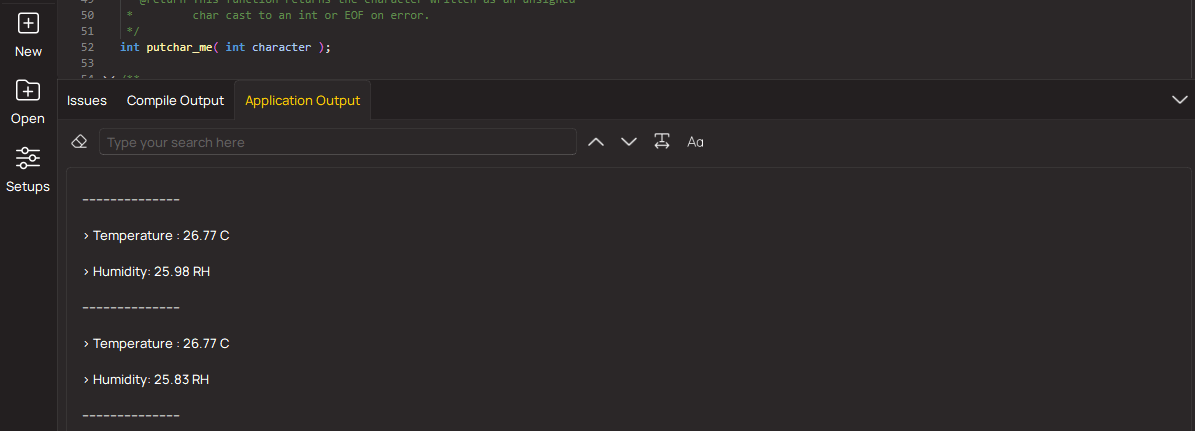
2. UART Terminal - Use the UART Terminal to monitor data transmission via a USB to UART converter, allowing direct communication between the Click board™ and your development system. Configure the baud rate and other serial settings according to your project's requirements to ensure proper functionality. For step-by-step setup instructions, refer to the provided tutorial.
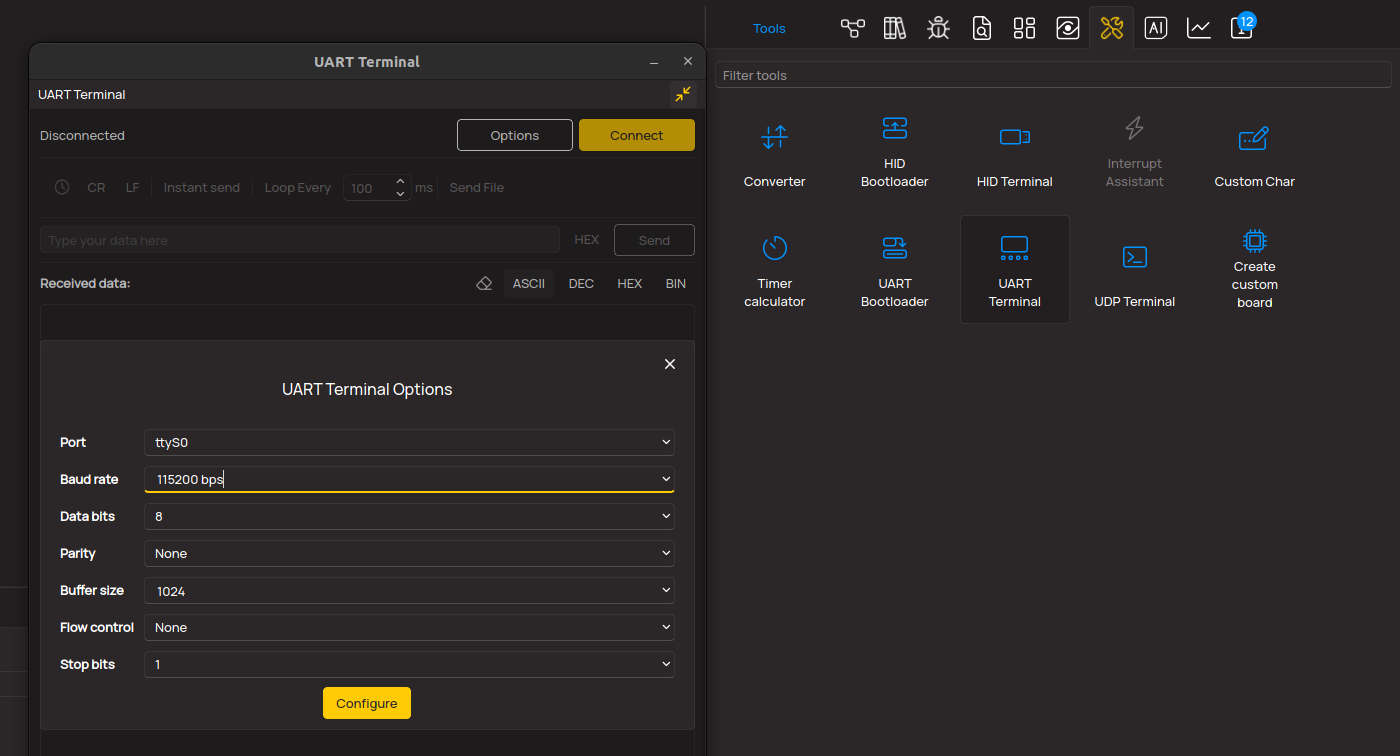
3. Plot Output - The Plot feature offers a powerful way to visualize real-time sensor data, enabling trend analysis, debugging, and comparison of multiple data points. To set it up correctly, follow the provided tutorial, which includes a step-by-step example of using the Plot feature to display Click board™ readings. To use the Plot feature in your code, use the function: plot(*insert_graph_name*, variable_name);. This is a general format, and it is up to the user to replace 'insert_graph_name' with the actual graph name and 'variable_name' with the parameter to be displayed.
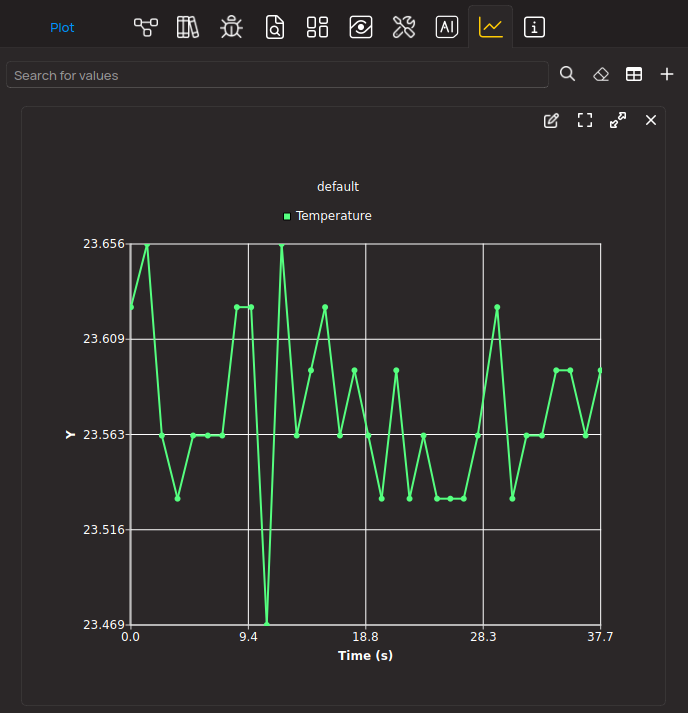
Software Support
Library Description
This library contains API for Thermo 20 Click driver.
Key functions:
thermo20_set_cmd
- Send command function.thermo20_start_conversion
- Start conversion function.thermo20_get_temperature
- Get temperature data function.
Open Source
Code example
The complete application code and a ready-to-use project are available through the NECTO Studio Package Manager for direct installation in the NECTO Studio. The application code can also be found on the MIKROE GitHub account.
/*!
* @file main.c
* @brief Thermo20 Click example
*
* # Description
* This example showcases the ability of Thermo 20 Click board to
* read it's serial number. It can read themperature and measure from -40degC to
* 120degC.
*
* The demo application is composed of two sections :
*
* ## Application Init
* Initialization communication modules(I2C, UART). Resets device and read Serial Number.
*
* ## Application Task
* In span of ~ 1000ms it sends command for adc conversion of temperature, reads ADC value,
* and calculates temperature in degrees C.
*
* @note For this driver to work on 18bit PIC MCU-s you need to additionally pull up communication lines.
*
* @author Mikroe Team
*
*/
#include "board.h"
#include "log.h"
#include "thermo20.h"
static thermo20_t thermo20;
static log_t logger;
void application_init ( void )
{
log_cfg_t log_cfg; /**< Logger config object. */
thermo20_cfg_t thermo20_cfg; /**< Click config object. */
/**
* Logger initialization.
* Default baud rate: 115200
* Default log level: LOG_LEVEL_DEBUG
* @note If USB_UART_RX and USB_UART_TX
* are defined as HAL_PIN_NC, you will
* need to define them manually for log to work.
* See @b LOG_MAP_USB_UART macro definition for detailed explanation.
*/
LOG_MAP_USB_UART( log_cfg );
log_init( &logger, &log_cfg );
log_info( &logger, " Application Init " );
// Click initialization.
thermo20_cfg_setup( &thermo20_cfg );
THERMO20_MAP_MIKROBUS( thermo20_cfg, MIKROBUS_1 );
err_t init_flag = thermo20_init( &thermo20, &thermo20_cfg );
if ( I2C_MASTER_ERROR == init_flag )
{
log_error( &logger, " Application Init Error. " );
log_info( &logger, " Please, run program again... " );
for ( ; ; );
}
thermo20_default_cfg ( &thermo20 );
uint32_t ser_numb = thermo20_get_serial_number( &thermo20 );
log_printf( &logger, " > Serial Number: %lu\r\n", ser_numb );
log_info( &logger, " Application Task " );
}
void application_task ( void )
{
thermo20_start_conversion( &thermo20 );
float temperature = thermo20_get_temperature( &thermo20 );
log_printf( &logger, " > Temperature[deg C]: %.2f\r\n", temperature );
Delay_ms ( 1000 );
}
int main ( void )
{
/* Do not remove this line or clock might not be set correctly. */
#ifdef PREINIT_SUPPORTED
preinit();
#endif
application_init( );
for ( ; ; )
{
application_task( );
}
return 0;
}
// ------------------------------------------------------------------------ END
Additional Support
Resources
Category:Temperature & humidity