This solution offers protection against ground potential differences, electrical noise, and voltage spikes, ensuring consistent and robust communication on the CAN bus.
A
A
Hardware Overview
How does it work?
CAN Isolator 2 Click is based on the ISO1042, an isolated CAN transceiver from Texas Instruments. It has several features, such as undervoltage protection, driver Dominant Time Out (TXD DTO), HBM ESD tolerance on bus pins, and more. The transceiver has ideal passive high-impedance bus terminals when unpowered. If used in conjunction with the isolated power supplies, the CAN Isolator 2 Click can be the ideal choice for protection against high voltages and noise currents from the bus. There are two states of operation on this Click board™: dominant and recessive. In a dominant state, the bus is driven differentially by a driver. In a recessive state, the host MCU of the CAN node
uses the TXD pin to drive the bus and receives the data from the bus on the RXD pin. To connect ISO1042 on a CAN bus, this Click board™ features a standard DB 9-pin male connector. According to the ISO 11898-2 standard, a maximum bus length is 40m, and a maximum stub length is 0.3m, while with careful design, the cables could be longer. This transceiver has a high input impedance, thus allowing a large number of nodes on the CAN bus. CAN Isolator 2 Click uses a standard UART interface to communicate with the host MCU, with commonly used UART RX and TX. In addition, there are few headers to interface lines directly with jumper wires. The left side of the CAN Isolator
2 Click has a VEXT 2-pin header to connect the external power supply. Along with the VEXT, on the opposite side, there are CANH and CANL pins to interface the CAN bus in the same manner. Under the CAN header, there is also one TX and RX header, which allows this Click board™ to be used independently of the host MCU. This Click board™ can operate with either 3.3V or 5V logic voltage levels selected via the VCC SEL jumper. This way, both 3.3V and 5V capable MCUs can use the communication lines properly. Also, this Click board™ comes equipped with a library containing easy-to-use functions and an example code that can be used for further development.
Features overview
Development board
EasyPIC v7a is the seventh generation of PIC development boards specially designed for the needs of rapid development of embedded applications. It supports a wide range of 8-bit PIC microcontrollers from Microchip and has a broad set of unique functions, such as the first-ever embedded debugger/programmer over USB-C. The development board is well organized and designed so that the end-user has all the necessary elements in one place, such as switches, buttons, indicators, connectors, and others. With four different connectors for each port, EasyPIC v7a allows you to connect accessory boards, sensors, and custom electronics more efficiently than ever. Each part of the EasyPIC v7a development board
contains the components necessary for the most efficient operation of the same board. In addition to the advanced integrated CODEGRIP programmer/debugger module, which offers many valuable programming/debugging options and seamless integration with the Mikroe software environment, the board also includes a clean and regulated power supply module for the development board. It can use various external power sources, including an external 12V power supply, 7-23V AC or 9-32V DC via DC connector/screw terminals, and a power source via the USB Type-C (USB-C) connector. Communication options such as USB-UART and RS-232 are also included, alongside the well-
established mikroBUS™ standard, three display options (7-segment, graphical, and character-based LCD), and several different DIP sockets. These sockets cover a wide range of 8-bit PIC MCUs, from PIC10F, PIC12F, PIC16F, PIC16Enh, PIC18F, PIC18FJ, and PIC18FK families. EasyPIC v7a is an integral part of the Mikroe ecosystem for rapid development. Natively supported by Mikroe software tools, it covers many aspects of prototyping and development thanks to a considerable number of different Click boards™ (over a thousand boards), the number of which is growing every day.
Microcontroller Overview
MCU Card / MCU
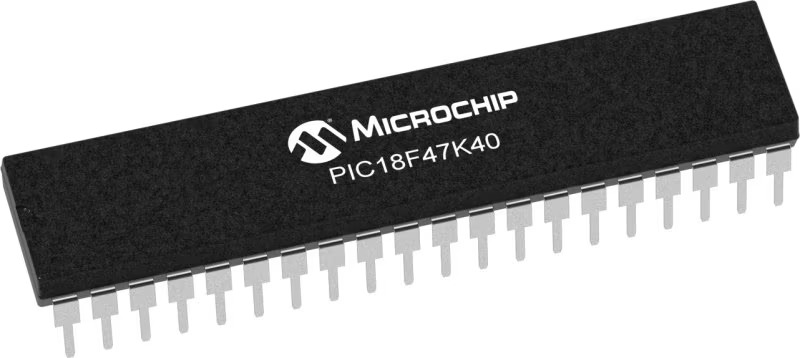
Architecture
PIC
MCU Memory (KB)
128
Silicon Vendor
Microchip
Pin count
40
RAM (Bytes)
3728
You complete me!
Accessories
DB9 Cable Female-to-Female (2m) cable is essential for establishing dependable serial data connections between devices. With its DB9 female connectors on both ends, this cable enables a seamless link between various equipment, such as computers, routers, switches, and other serial devices. Measuring 2 meters in length, it offers flexibility in arranging your setup without compromising data transmission quality. Crafted with precision, this cable ensures consistent and reliable data exchange, making it suitable for industrial applications, office environments, and home setups. Whether configuring networking equipment, accessing console ports, or utilizing serial peripherals, this cable's durable construction and robust connectors guarantee a stable connection. Simplify your data communication needs with the 2m DB9 female-to-female cable, an efficient solution designed to meet your serial connectivity requirements easily and efficiently.
Used MCU Pins
mikroBUS™ mapper
Take a closer look
Click board™ Schematic
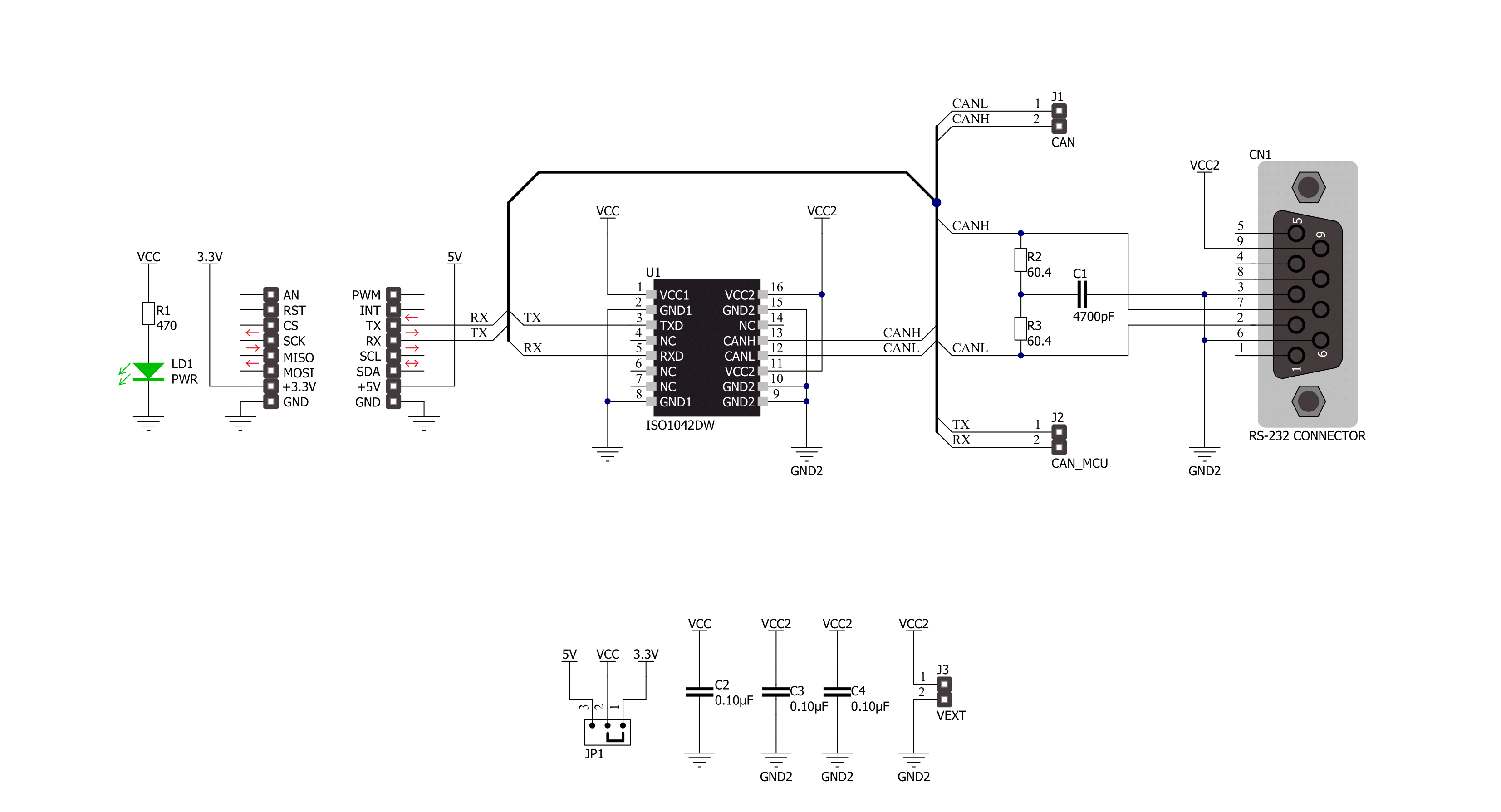
Step by step
Project assembly
Track your results in real time
Application Output
1. Application Output - In Debug mode, the 'Application Output' window enables real-time data monitoring, offering direct insight into execution results. Ensure proper data display by configuring the environment correctly using the provided tutorial.
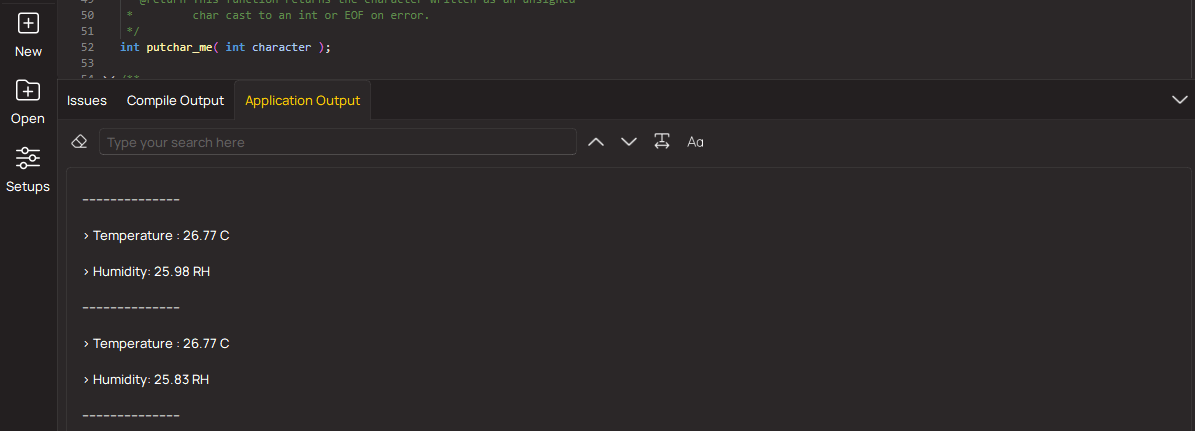
2. UART Terminal - Use the UART Terminal to monitor data transmission via a USB to UART converter, allowing direct communication between the Click board™ and your development system. Configure the baud rate and other serial settings according to your project's requirements to ensure proper functionality. For step-by-step setup instructions, refer to the provided tutorial.
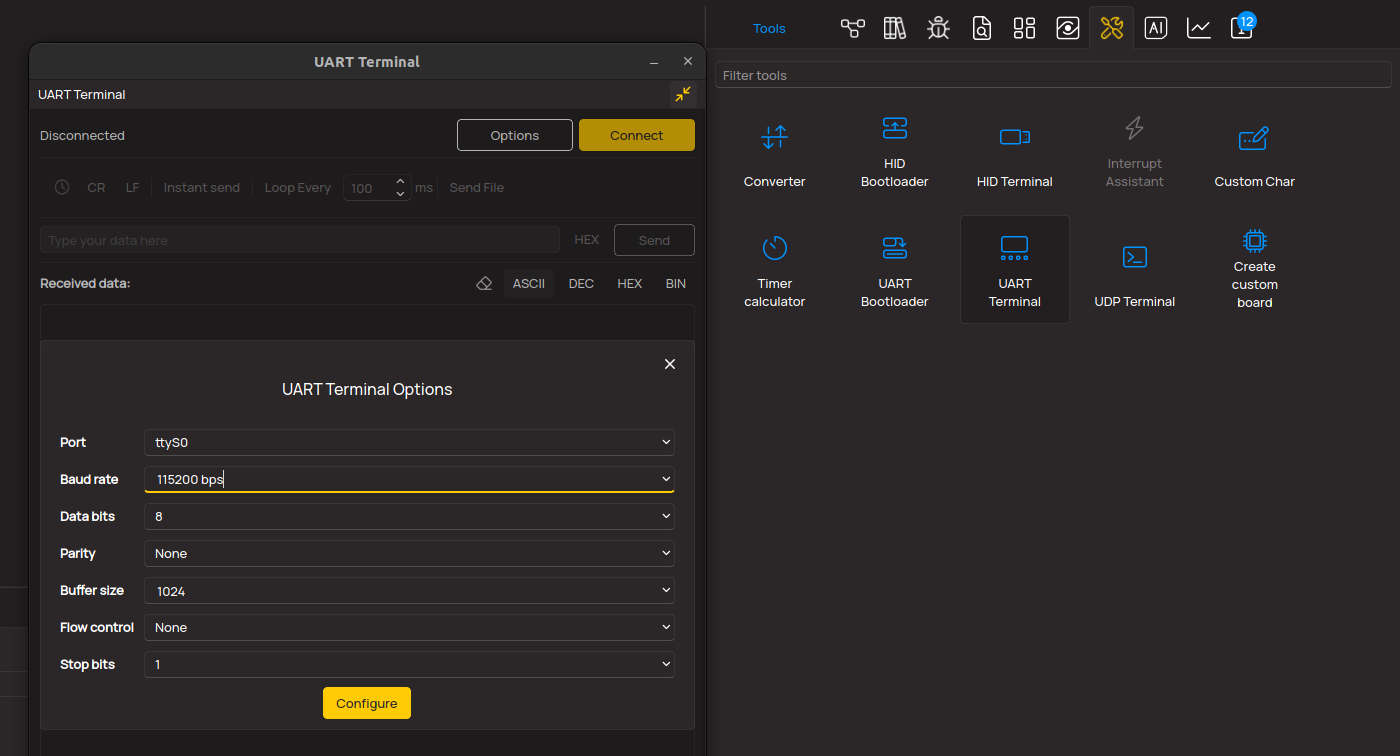
3. Plot Output - The Plot feature offers a powerful way to visualize real-time sensor data, enabling trend analysis, debugging, and comparison of multiple data points. To set it up correctly, follow the provided tutorial, which includes a step-by-step example of using the Plot feature to display Click board™ readings. To use the Plot feature in your code, use the function: plot(*insert_graph_name*, variable_name);. This is a general format, and it is up to the user to replace 'insert_graph_name' with the actual graph name and 'variable_name' with the parameter to be displayed.
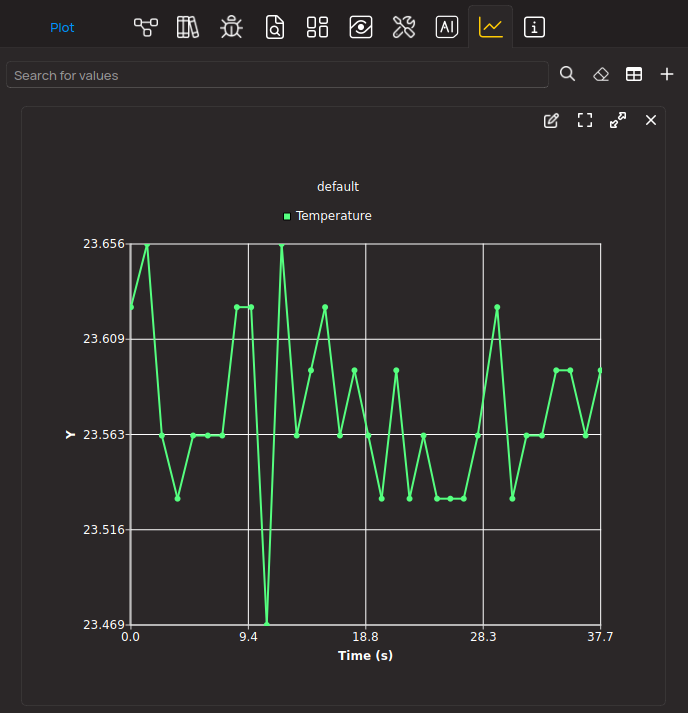
Software Support
Library Description
This library contains API for CAN Isolator 2 Click driver.
Key functions:
canisolator2_generic_write
- CAN Isolator 2 data writing function.canisolator2_generic_read
-CAN Isolator 2 data reading function.canisolator2_send_data
- CAN Isolator 2 send data function.
Open Source
Code example
The complete application code and a ready-to-use project are available through the NECTO Studio Package Manager for direct installation in the NECTO Studio. The application code can also be found on the MIKROE GitHub account.
/*!
* @file main.c
* @brief CAN Isolator 2 Click Example.
*
* # Description
* This example reads and processes data from CAN Isolator 2 Clicks.
*
* The demo application is composed of two sections :
*
* ## Application Init
* Initializes driver and wake-up module.
*
* ## Application Task
* Transmitter/Receiver task depends on uncommented code.
* Receiver logging each received byte to the UART for data logging,
* while transmitted send messages every 2 seconds.
*
* ## Additional Function
* - static void canisolator2_clear_app_buf ( void )
* - static err_t canisolator2_process ( void )
*
* @author Nenad Filipovic
*
*/
#include "board.h"
#include "log.h"
#include "canisolator2.h"
#define PROCESS_BUFFER_SIZE 200
// #define TRANSMIT
#define RECIEVER
static canisolator2_t canisolator2;
static log_t logger;
static char app_buf[ PROCESS_BUFFER_SIZE ] = { 0 };
static int32_t app_buf_len = 0;
static int32_t app_buf_cnt = 0;
unsigned char demo_message[ 9 ] = { 'M', 'i', 'k', 'r', 'o', 'E', 13, 10, 0 };
/**
* @brief CAN Isolator 2 clearing application buffer.
* @details This function clears memory of application buffer and reset it's length and counter.
* @note None.
*/
static void canisolator2_clear_app_buf ( void );
/**
* @brief CAN Isolator 2 data reading function.
* @details This function reads data from device and concatenates data to application buffer.
*
* @return @li @c 0 - Read some data.
* @li @c -1 - Nothing is read.
* @li @c -2 - Application buffer overflow.
*
* See #err_t definition for detailed explanation.
* @note None.
*/
static err_t canisolator2_process ( void );
void application_init ( void ) {
log_cfg_t log_cfg; /**< Logger config object. */
canisolator2_cfg_t canisolator2_cfg; /**< Click config object. */
/**
* Logger initialization.
* Default baud rate: 115200
* Default log level: LOG_LEVEL_DEBUG
* @note If USB_UART_RX and USB_UART_TX
* are defined as HAL_PIN_NC, you will
* need to define them manually for log to work.
* See @b LOG_MAP_USB_UART macro definition for detailed explanation.
*/
LOG_MAP_USB_UART( log_cfg );
log_init( &logger, &log_cfg );
log_info( &logger, " Application Init " );
// Click initialization.
canisolator2_cfg_setup( &canisolator2_cfg );
CANISOLATOR2_MAP_MIKROBUS( canisolator2_cfg, MIKROBUS_1 );
err_t init_flag = canisolator2_init( &canisolator2, &canisolator2_cfg );
if ( init_flag == UART_ERROR ) {
log_error( &logger, " Application Init Error. " );
log_info( &logger, " Please, run program again... " );
for ( ; ; );
}
app_buf_len = 0;
app_buf_cnt = 0;
log_info( &logger, " Application Task " );
Delay_ms ( 100 );
#ifdef TRANSMIT
log_printf( &logger, " Send data: \r\n" );
log_printf( &logger, " MikroE \r\n" );
log_printf( &logger, "------------------\r\n" );
log_printf( &logger, " Transmit data \r\n" );
Delay_ms ( 1000 );
#endif
#ifdef RECIEVER
log_printf( &logger, " Receive data \r\n" );
Delay_ms ( 1000 );
Delay_ms ( 1000 );
#endif
log_printf( &logger, "------------------\r\n" );
}
void application_task ( void ) {
#ifdef TRANSMIT
canisolator2_send_data( &canisolator2, demo_message );
log_printf( &logger, "\t%s", demo_message );
Delay_ms ( 1000 );
Delay_ms ( 1000 );
log_printf( &logger, "------------------\r\n" );
#endif
#ifdef RECIEVER
canisolator2_process( );
if ( app_buf_len > 0 ) {
log_printf( &logger, "%s", app_buf );
canisolator2_clear_app_buf( );
}
#endif
}
int main ( void )
{
/* Do not remove this line or clock might not be set correctly. */
#ifdef PREINIT_SUPPORTED
preinit();
#endif
application_init( );
for ( ; ; )
{
application_task( );
}
return 0;
}
static void canisolator2_clear_app_buf ( void ) {
memset( app_buf, 0, app_buf_len );
app_buf_len = 0;
app_buf_cnt = 0;
}
static err_t canisolator2_process ( void ) {
int32_t rx_size;
char rx_buff[ PROCESS_BUFFER_SIZE ] = { 0 };
rx_size = canisolator2_generic_read( &canisolator2, rx_buff, PROCESS_BUFFER_SIZE );
if ( rx_size > 0 ) {
int32_t buf_cnt = 0;
if ( app_buf_len + rx_size >= PROCESS_BUFFER_SIZE ) {
canisolator2_clear_app_buf( );
return CANISOLATOR2_ERROR;
} else {
buf_cnt = app_buf_len;
app_buf_len += rx_size;
}
for ( int32_t rx_cnt = 0; rx_cnt < rx_size; rx_cnt++ ) {
if ( rx_buff[ rx_cnt ] != 0 ) {
app_buf[ ( buf_cnt + rx_cnt ) ] = rx_buff[ rx_cnt ];
} else {
app_buf_len--;
buf_cnt--;
}
}
return CANISOLATOR2_OK;
}
return CANISOLATOR2_ERROR;
}
// ------------------------------------------------------------------------ END