Upgrade your solution's heart rate monitoring capabilities with our advanced sensor technology - designed to deliver accurate and consistent readings
A
A
Hardware Overview
How does it work?
Heart Rate 9 Click is based on the SFH 7060, a heart rate and pulse oximetry monitoring sensor from ams OSRAM. It utilizes a Phase Division Multiplexing technique to simultaneously measure multiple signals with zero cross-talk. This technique uses the PIC16F1779 MCU's integrated Core Independent Peripherals (CIPs) from Microchip. CIPs allow you to achieve a low-noise reflective heart rate monitor design with significantly lower BOM costs than conventional designs. This Heart Rate 9 Click board™ introduces Microchip's proprietary method (hereafter "proprietary method") of measuring multiple signals in a body using pseudorandom binary sequence generation and phase division multiplexing. This proprietary method uses a special encoding/decoding scheme to allow multiple light-emitting diodes (LED) to transmit light simultaneously with a single photodiode to condition each light from the combined lights at the receiving side. While the blood passes through the capillary blood vessels, they expand and dilate. Their light reflectance index changes accordingly. This is the basis of the photo-plethysmogram (PPM), a method used for the volumetric measurement of an organ, or in this case - blood vessels. The heart rate signal is calculated
according to the changes in the reflected green light sensed by the PD element. The Heart Rate 6 click can provide the HRM readings by placing the index finger over the optical sensor. Oxygen saturation in the blood can be determined by measuring the light absorption in the red/IR part of the spectrum. The oxygen-saturated blood absorbs more red light and less infrared than the unsaturated blood. This fact can be used to determine the oxygen saturation of the blood. The peripheral capillary oxygen saturation (SpO2) percentage ranges from 95% to 100% for a healthy adult. The challenge in a multiple signal sources system (for example, the LEDs in the case of a pulse oximeter) is that each LED must share the same photodiode. A classic solution is to turn on each light source in sequence and then take each measurement in turn. Each light source gets its slice of time in which the photodiode can get its measurement. This method is called Time-Division Multiplexing (TDM). The same principle is also applied to the TDMA-based cellular system. The drawback of the TDM approach is that adding more light sources while keeping the data processing routine the same results in more time to get a measurement from every source. Microchip's proprietary method uses a known
concept called Maximal Length (ML) sequence, a type of pseudorandom binary sequence, to generate a gold code or a reference sequence. This reference sequence is then phase-shifted using PhaseDivision Multiplexing (PDM) to drive multiple LEDs. After passing through a part of a body, the light amplitudes from these LEDs are detected by a phototransistor or photodiode and digitized with an Analog-to-Digital Converter (ADC). The digitized ADC light amplitude values are re-correlated with each LED's driving sequence. Spread spectrum techniques are known for their noise mitigation properties and ability to pass multiple signals through the same medium without interference. Thus, these measurements of each light absorption of the body can be performed substantially simultaneously with minimal interference from each other. The SFH7060, made by ams OSRAM, integrates three green, one red, one infrared emitter, and one photodiode in a reflective package. The reflective photo sensing method has become increasingly popular in developing small, wearable biometric sensors, such as those green light sensors seen in the back of smartwatches or activity tracker wristbands.
Features overview
Development board
EasyPIC v7 is the seventh generation of PIC development boards specially designed to develop embedded applications rapidly. It supports a wide range of 8-bit PIC microcontrollers from Microchip and has a broad set of unique functions, such as a powerful onboard mikroProg programmer and In-Circuit debugger over USB-B. The development board is well organized and designed so that the end-user has all the necessary elements in one place, such as switches, buttons, indicators, connectors, and others. With four different connectors for each port, EasyPIC v7 allows you to connect accessory boards, sensors, and custom electronics more efficiently than ever. Each part of
the EasyPIC v7 development board contains the components necessary for the most efficient operation of the same board. An integrated mikroProg, a fast USB 2.0 programmer with mikroICD hardware In-Circuit Debugger, offers many valuable programming/debugging options and seamless integration with the Mikroe software environment. Besides it also includes a clean and regulated power supply block for the development board. It can use various external power sources, including an external 12V power supply, 7-23V AC or 9-32V DC via DC connector/screw terminals, and a power source via the USB Type-B (USB-B) connector. Communication options such as
USB-UART and RS-232 are also included, alongside the well-established mikroBUS™ standard, three display options (7-segment, graphical, and character-based LCD), and several different DIP sockets. These sockets cover a wide range of 8-bit PIC MCUs, from PIC10F, PIC12F, PIC16F, PIC16Enh, PIC18F, PIC18FJ, and PIC18FK families. EasyPIC v7 is an integral part of the Mikroe ecosystem for rapid development. Natively supported by Mikroe software tools, it covers many aspects of prototyping and development thanks to a considerable number of different Click boards™ (over a thousand boards), the number of which is growing every day.
Microcontroller Overview
MCU Card / MCU
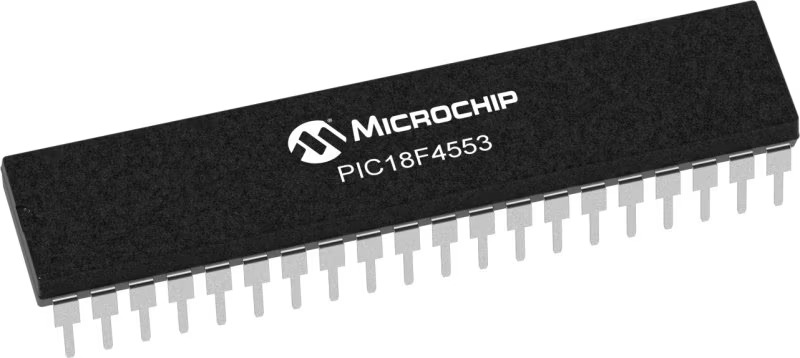
Architecture
PIC
MCU Memory (KB)
32
Silicon Vendor
Microchip
Pin count
40
RAM (Bytes)
2048
Used MCU Pins
mikroBUS™ mapper
Take a closer look
Click board™ Schematic
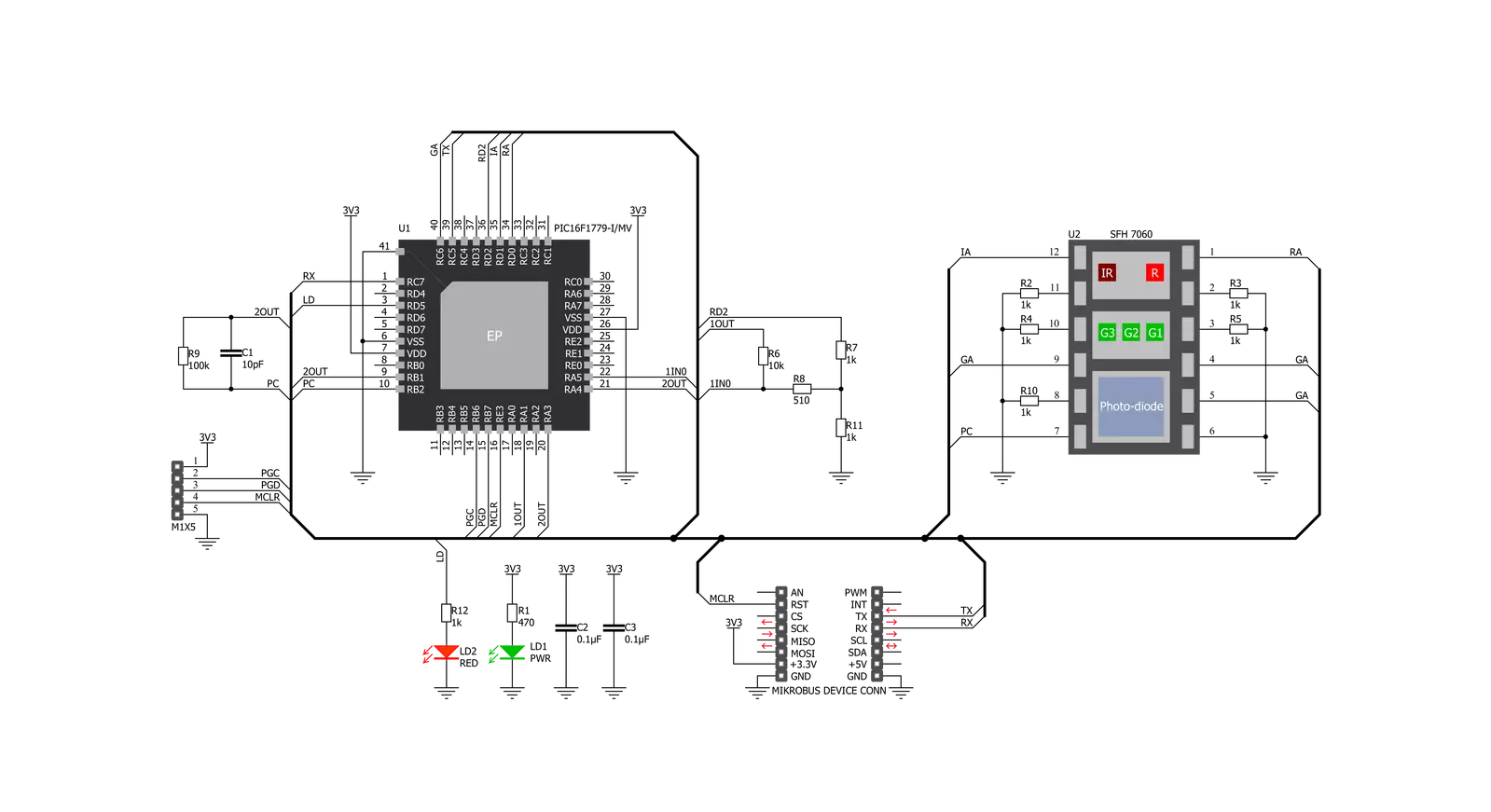
Step by step
Project assembly
Track your results in real time
Application Output
1. Application Output - In Debug mode, the 'Application Output' window enables real-time data monitoring, offering direct insight into execution results. Ensure proper data display by configuring the environment correctly using the provided tutorial.
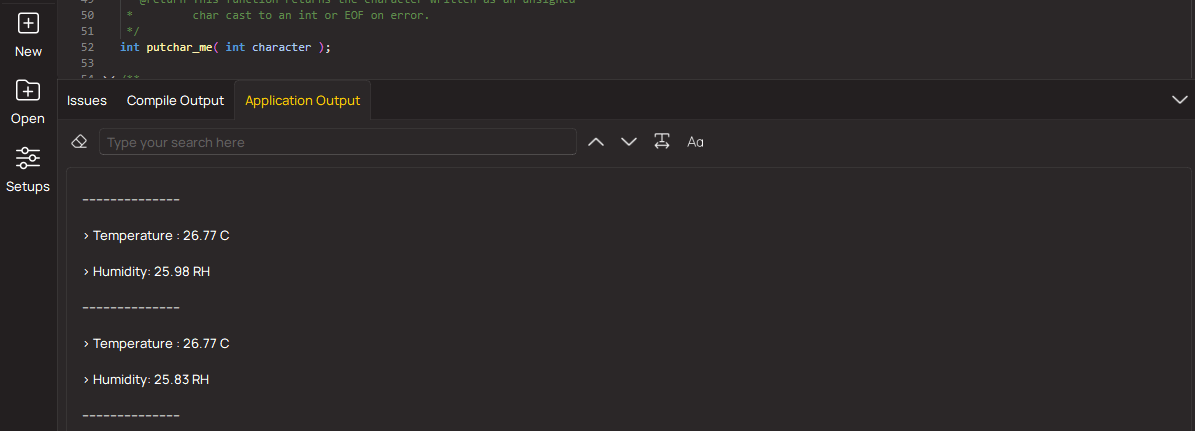
2. UART Terminal - Use the UART Terminal to monitor data transmission via a USB to UART converter, allowing direct communication between the Click board™ and your development system. Configure the baud rate and other serial settings according to your project's requirements to ensure proper functionality. For step-by-step setup instructions, refer to the provided tutorial.
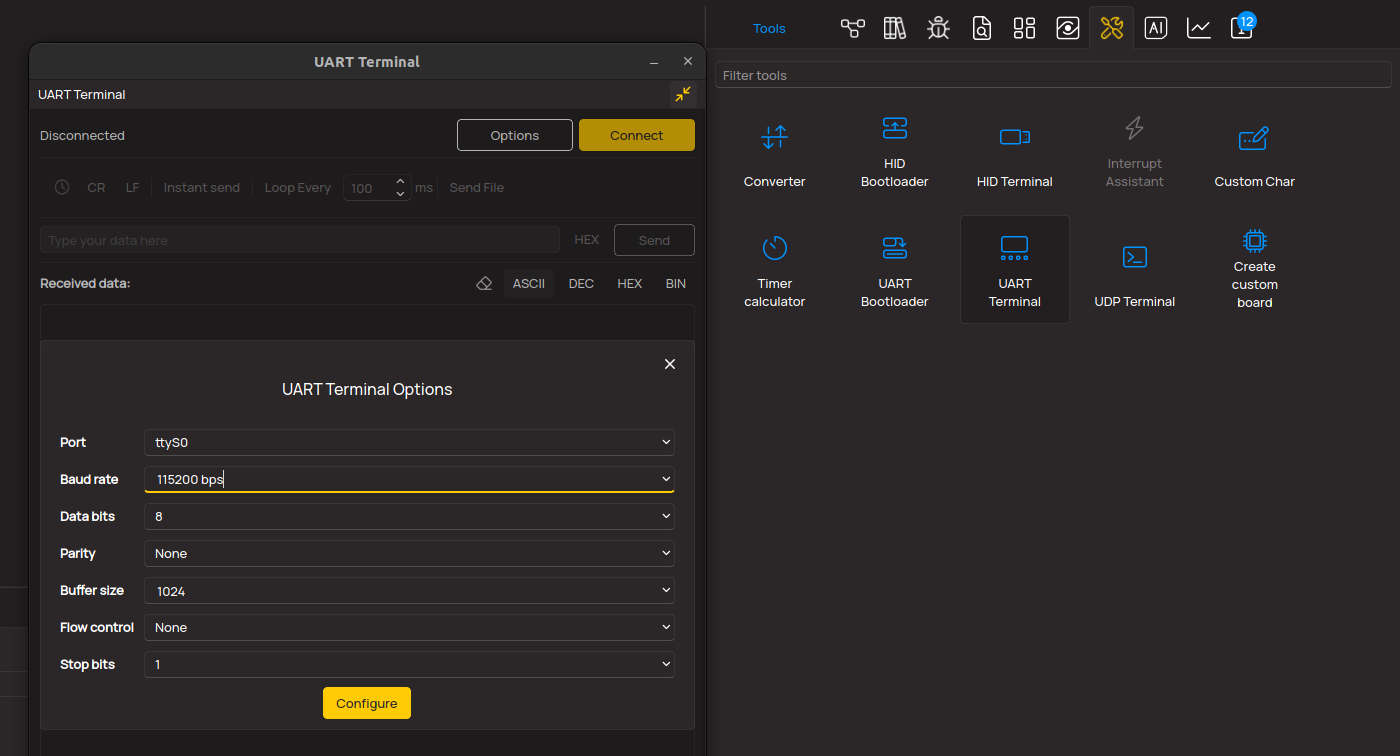
3. Plot Output - The Plot feature offers a powerful way to visualize real-time sensor data, enabling trend analysis, debugging, and comparison of multiple data points. To set it up correctly, follow the provided tutorial, which includes a step-by-step example of using the Plot feature to display Click board™ readings. To use the Plot feature in your code, use the function: plot(*insert_graph_name*, variable_name);. This is a general format, and it is up to the user to replace 'insert_graph_name' with the actual graph name and 'variable_name' with the parameter to be displayed.
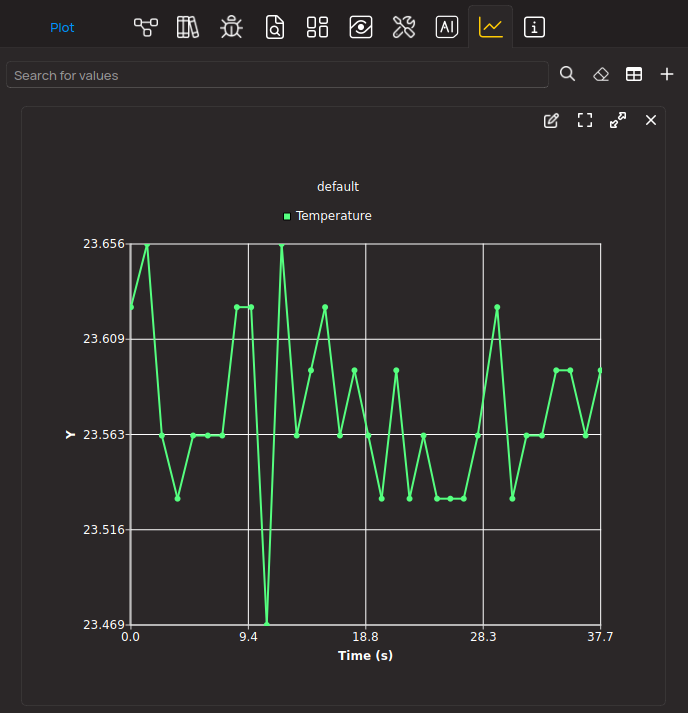
Software Support
Library Description
This library contains API for Heart Rate 9 Click driver.
Key functions:
heartrate9_generic_write
- Heart Rate 9 data writing functionheartrate9_generic_read
- Heart Rate 9 data reading functionheartrate9_set_rst
- Sets state of the rst pin setting
Open Source
Code example
The complete application code and a ready-to-use project are available through the NECTO Studio Package Manager for direct installation in the NECTO Studio. The application code can also be found on the MIKROE GitHub account.
/*!
* @file main.c
* @brief Heart Rate 9 Click Example.
*
* # Description
* This example reads and processes data from Heart Rate 9 Clicks.
*
* The demo application is composed of two sections :
*
* ## Application Init
* Initializes driver and wake-up module.
*
* ## Application Task
* Reads the received data and logs it.
*
* ## Additional Function
* - static void heartrate9_clear_app_buf ( void ) - Function clears memory of app_buf.
* - static err_t heartrate9_process ( void ) - The general process of collecting data the module sends.
*
* @note
* Data structure is:
* > AA;BB;CC;DD;EE; <
*
* > AA -> Data header.
* > BB -> Red diode.
* > CC -> IR diode.
* > DD -> Green diode.
* > EE -> BPM.
*
* @author Luka Filipovic
*
*/
#include "board.h"
#include "log.h"
#include "heartrate9.h"
#define PROCESS_BUFFER_SIZE 200
static heartrate9_t heartrate9;
static log_t logger;
static char app_buf[ PROCESS_BUFFER_SIZE ] = { 0 };
static int32_t app_buf_len = 0;
static int32_t app_buf_cnt = 0;
/**
* @brief Heart Rate 9 clearing application buffer.
* @details This function clears memory of application buffer and reset it's length and counter.
* @note None.
*/
static void heartrate9_clear_app_buf ( void );
/**
* @brief Heart Rate 9 data reading function.
* @details This function reads data from device and concatenates data to application buffer.
*
* @return @li @c 0 - Read some data.
* @li @c -1 - Nothing is read.
* @li @c -2 - Application buffer overflow.
*
* See #err_t definition for detailed explanation.
* @note None.
*/
static err_t heartrate9_process ( void );
void application_init ( void )
{
log_cfg_t log_cfg; /**< Logger config object. */
heartrate9_cfg_t heartrate9_cfg; /**< Click config object. */
/**
* Logger initialization.
* Default baud rate: 115200
* Default log level: LOG_LEVEL_DEBUG
* @note If USB_UART_RX and USB_UART_TX
* are defined as HAL_PIN_NC, you will
* need to define them manually for log to work.
* See @b LOG_MAP_USB_UART macro definition for detailed explanation.
*/
LOG_MAP_USB_UART( log_cfg );
log_init( &logger, &log_cfg );
// Click initialization.
heartrate9_cfg_setup( &heartrate9_cfg );
HEARTRATE9_MAP_MIKROBUS( heartrate9_cfg, MIKROBUS_1 );
err_t init_flag = heartrate9_init( &heartrate9, &heartrate9_cfg );
if ( init_flag == UART_ERROR )
{
log_error( &logger, " Application Init Error. " );
log_info( &logger, " Please, run program again... " );
for ( ; ; );
}
app_buf_len = 0;
app_buf_cnt = 0;
}
void application_task ( void )
{
heartrate9_process();
if ( app_buf_len > 0 )
{
log_printf( &logger, "%s", app_buf );
heartrate9_clear_app_buf( );
}
}
int main ( void )
{
/* Do not remove this line or clock might not be set correctly. */
#ifdef PREINIT_SUPPORTED
preinit();
#endif
application_init( );
for ( ; ; )
{
application_task( );
}
return 0;
}
static void heartrate9_clear_app_buf ( void )
{
memset( app_buf, 0, app_buf_len );
app_buf_len = 0;
app_buf_cnt = 0;
}
static err_t heartrate9_process ( void )
{
int32_t rx_size;
char rx_buff[ PROCESS_BUFFER_SIZE ] = { 0 };
rx_size = heartrate9_generic_read( &heartrate9, rx_buff, PROCESS_BUFFER_SIZE );
if ( rx_size > 0 )
{
int32_t buf_cnt = 0;
if ( app_buf_len + rx_size >= PROCESS_BUFFER_SIZE )
{
heartrate9_clear_app_buf( );
return -2;
}
else
{
buf_cnt = app_buf_len;
app_buf_len += rx_size;
}
for ( int32_t rx_cnt = 0; rx_cnt < rx_size; rx_cnt++ )
{
if ( rx_buff[ rx_cnt ] != 0 )
{
app_buf[ ( buf_cnt + rx_cnt ) ] = rx_buff[ rx_cnt ];
}
else
{
app_buf_len--;
}
}
return 0;
}
return -1;
}
// ------------------------------------------------------------------------ END