Experience the power of our ADC and discover what you've been missing
A
A
Hardware Overview
How does it work?
ADC 9 Click is based on MCP3564, a 24-bit Delta-Sigma Analog-to-Digital Converter with a programmable data rate of up to 153.6ksps from Microchip. The MCP3564 is fully configurable with Oversampling Ratio (OSR) from 32 to 98304 and gain from 1/3x to 64x. It includes an internal sequencer (SCAN mode) with multiple monitor channels and a 24-bit timer to automatically create conversion loop sequences without needing MCU communications. Advanced security features, such as CRC and register map lock, can ensure configuration locking and integrity and communication data integrity for secure environments. ADC 9 Click comes with a 20 MHz SPI-compatible serial interface. Communication is simplified with 8-bit commands, including various Continuous Read/Write modes and 24/32-bit multiple data formats that can be accessed by the Direct Memory Access (DMA) of an 8-bit, 16-bit, or 32-bit MCU.
The noise value generally increases when the temperature increases, as thermal noise is dominant for all OSRs larger than 32. For high OSR settings (>512), the thermal noise is dominant and increases proportionally to the square root of the absolute temperature. The noise performance is also a function of the measurement duration. The peak-to-peak noise is usually reduced for short-duration measurements (low number of consecutive samples) because the crest factor (ratio between the RMS noise and peak-to-peak noise) is reduced. This feature is only a consequence of the noise distribution being Gaussian by nature. ADC 9 Click use MCP3564 IC with a fully configurable analog input dual multiplexer that can select which input is connected to each of the two differential input pins (VIN+/VIN-) of the Delta-Sigma ADC. Each of these multiplexers includes the same possibilities for the input selection so that the ADC can convert any
required combination of input voltages. The analog multiplexer comprises parallel low-resistance input switches turned on or off depending on the input channel selection. Their resistance is negligible compared to the input impedance of the ADC (caused by the charge and discharge of the input sampling capacitors on the VIN+/VIN- ADC inputs). ADC 9 Click also features MCP1501, a low drift bandgap-based voltage reference from Microchip for precision data acquisition systems. The bandgap uses chopper-based amplifiers, effectively reducing the drift to zero. This Click board™ can only be operated with a 3.3V logic voltage level. The board must perform appropriate logic voltage level conversion before using MCUs with different logic levels. However, the Click board™ comes equipped with a library containing functions and an example code that can be used as a reference for further development.
Features overview
Development board
PIC32MZ Clicker is a compact starter development board that brings the flexibility of add-on Click boards™ to your favorite microcontroller, making it a perfect starter kit for implementing your ideas. It comes with an onboard 32-bit PIC32MZ microcontroller with FPU from Microchip, a USB connector, LED indicators, buttons, a mikroProg connector, and a header for interfacing with external electronics. Thanks to its compact design with clear and easy-recognizable silkscreen markings, it provides a fluid and immersive working experience, allowing access anywhere and under
any circumstances. Each part of the PIC32MZ Clicker development kit contains the components necessary for the most efficient operation of the same board. In addition to the possibility of choosing the PIC32MZ Clicker programming method, using USB HID mikroBootloader, or through an external mikroProg connector for PIC, dsPIC, or PIC32 programmer, the Clicker board also includes a clean and regulated power supply module for the development kit. The USB Micro-B connection can provide up to 500mA of current, which is more than enough to operate all onboard
and additional modules. All communication methods that mikroBUS™ itself supports are on this board, including the well-established mikroBUS™ socket, reset button, and several buttons and LED indicators. PIC32MZ Clicker is an integral part of the Mikroe ecosystem, allowing you to create a new application in minutes. Natively supported by Mikroe software tools, it covers many aspects of prototyping thanks to a considerable number of different Click boards™ (over a thousand boards), the number of which is growing every day.
Microcontroller Overview
MCU Card / MCU
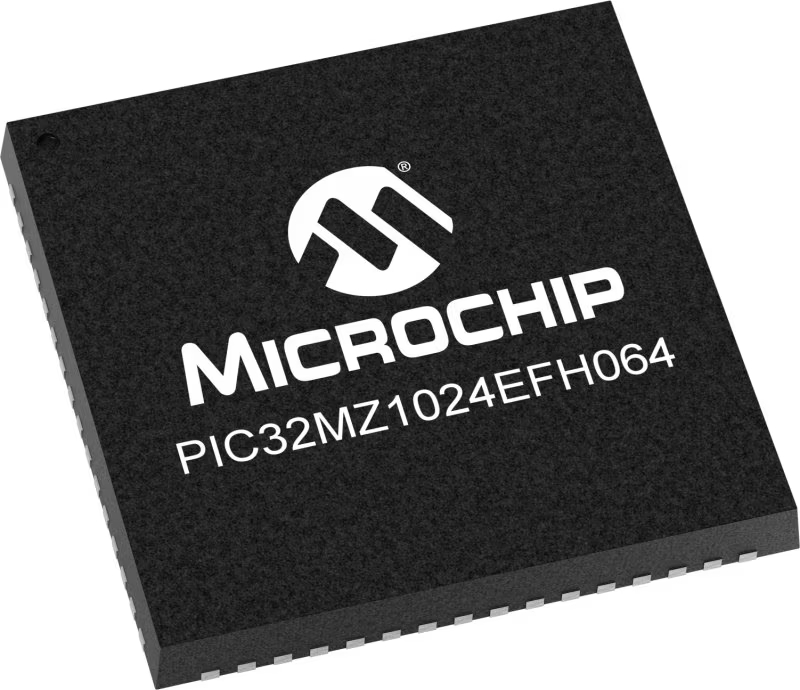
Architecture
PIC32
MCU Memory (KB)
1024
Silicon Vendor
Microchip
Pin count
64
RAM (Bytes)
524288
Used MCU Pins
mikroBUS™ mapper
Take a closer look
Click board™ Schematic
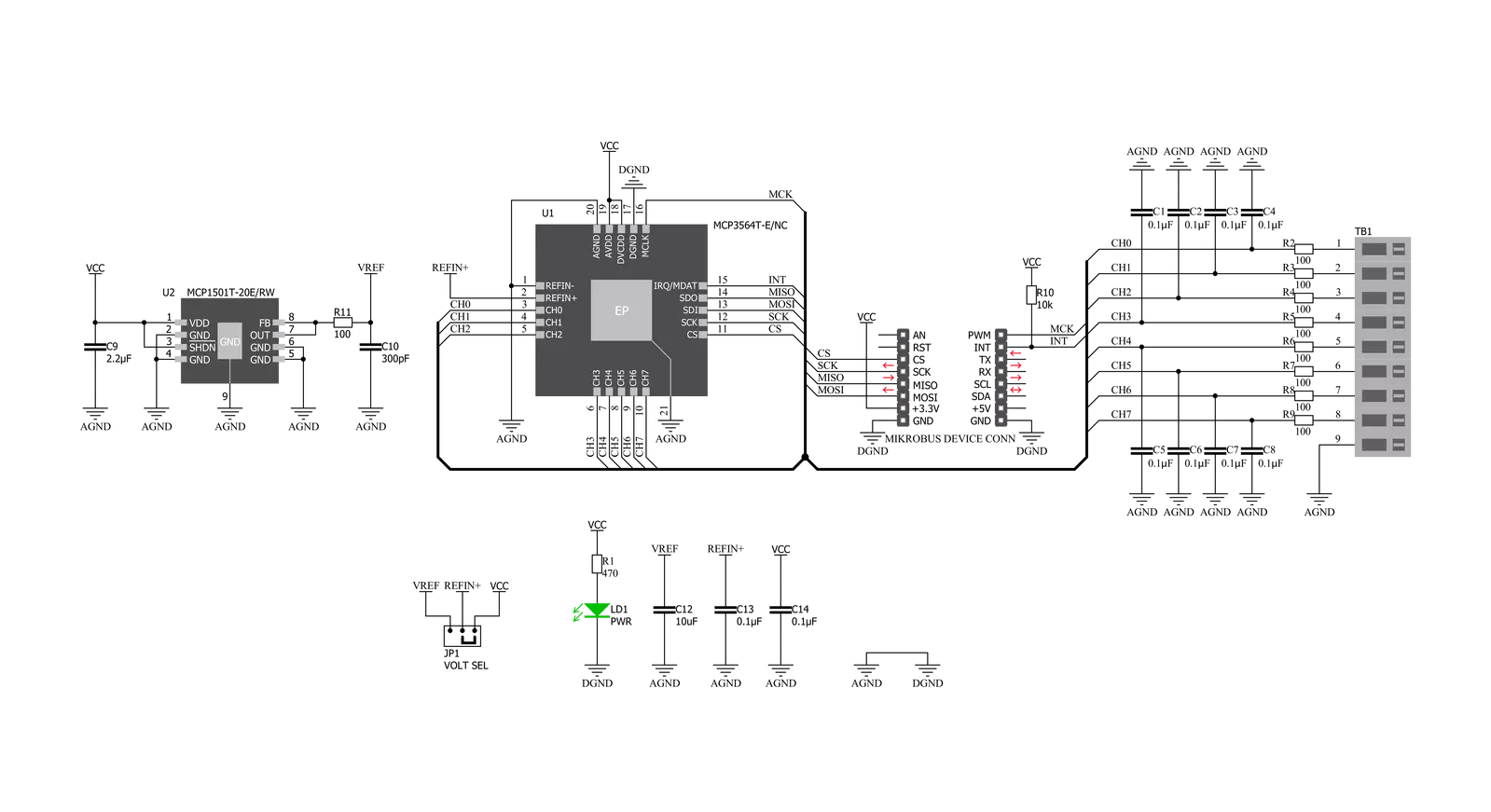
Step by step
Project assembly
Track your results in real time
Application Output
1. Application Output - In Debug mode, the 'Application Output' window enables real-time data monitoring, offering direct insight into execution results. Ensure proper data display by configuring the environment correctly using the provided tutorial.
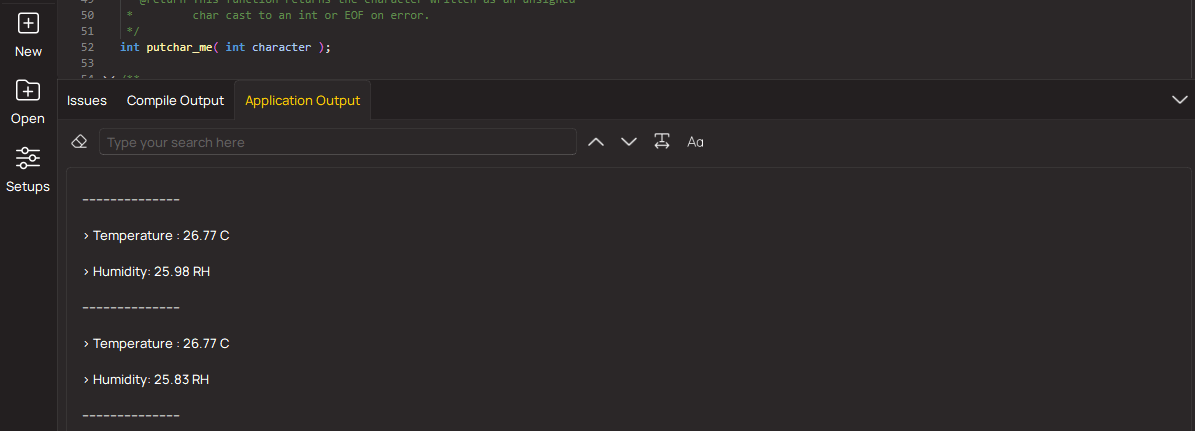
2. UART Terminal - Use the UART Terminal to monitor data transmission via a USB to UART converter, allowing direct communication between the Click board™ and your development system. Configure the baud rate and other serial settings according to your project's requirements to ensure proper functionality. For step-by-step setup instructions, refer to the provided tutorial.
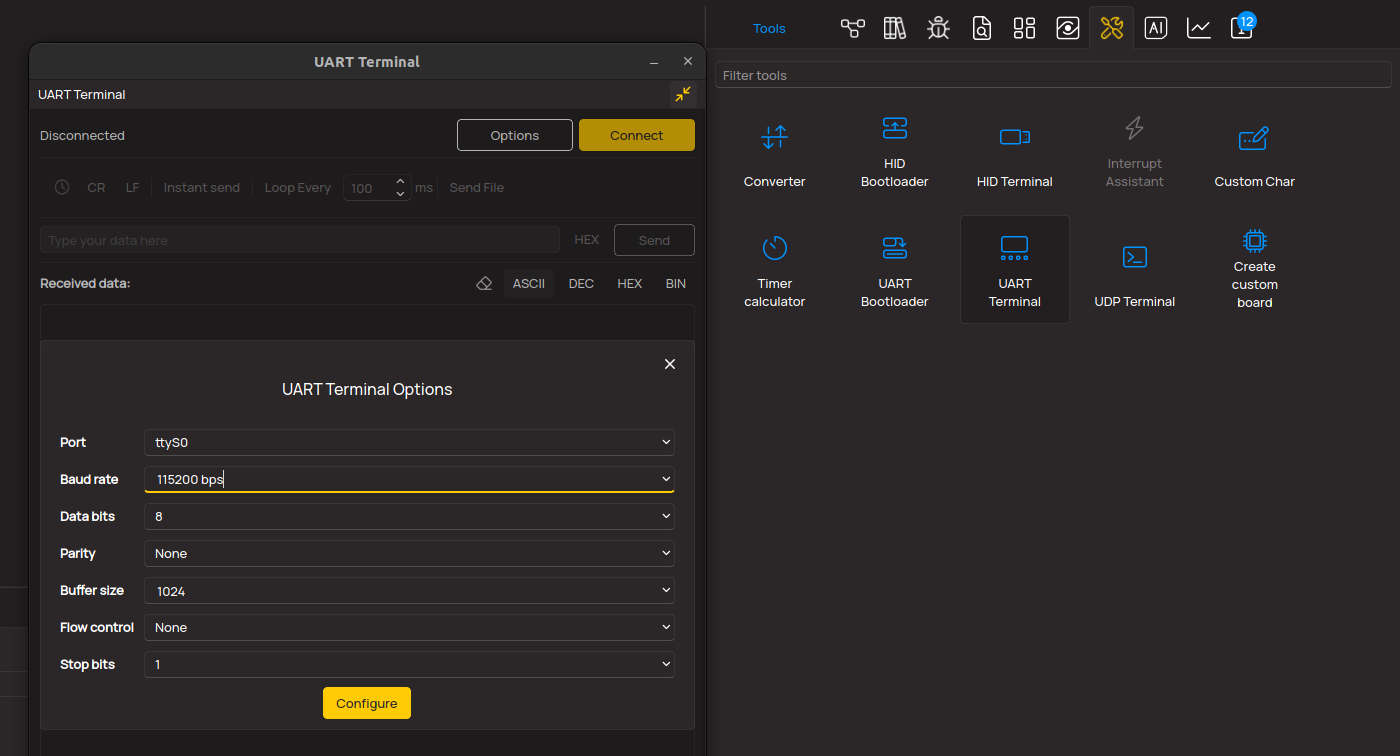
3. Plot Output - The Plot feature offers a powerful way to visualize real-time sensor data, enabling trend analysis, debugging, and comparison of multiple data points. To set it up correctly, follow the provided tutorial, which includes a step-by-step example of using the Plot feature to display Click board™ readings. To use the Plot feature in your code, use the function: plot(*insert_graph_name*, variable_name);. This is a general format, and it is up to the user to replace 'insert_graph_name' with the actual graph name and 'variable_name' with the parameter to be displayed.
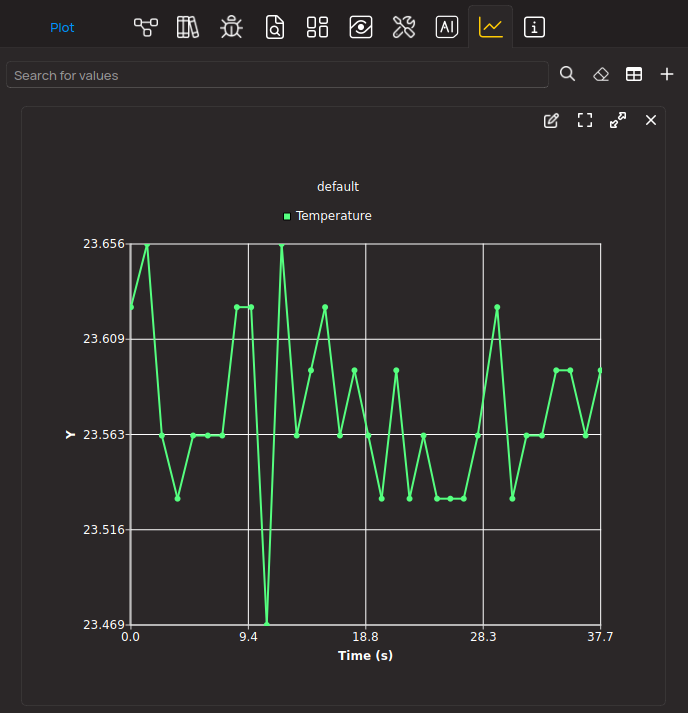
Software Support
Library Description
This library contains API for ADC 9 Click driver.
Key functions:
uint8_t adc9_write_fast_cmd ( uint8_t dev_adr, uint8_t cmd );
- Function is used to execute fast command.uint8_t adc9_read_def_adc ( uint8_t dev_adr, int32_t *rd_data );
- Function is used to read ADC value when the default fata format is applied.float adc9_volt_calc ( int32_t adc_val, uint16_t v_ref, uint8_t gain );
- Function is used to calculate voltage based on ADC values.
Open Source
Code example
The complete application code and a ready-to-use project are available through the NECTO Studio Package Manager for direct installation in the NECTO Studio. The application code can also be found on the MIKROE GitHub account.
/*!
* \file
* \brief Adc9 Click example
*
* # Description
* This Click is 8th channel analog to digital converter expansion board, usefull for projects
* where we have demand for multi channel ADC conversion such as microcontrollers with small
* number or none analog inputs. It offers integrated features, such as internal oscillator,
* temperature sensor and burnout sensor detection, in order to reduce system component count
* and total solution cost.
*
* The demo application is composed of two sections :
*
* ## Application Init
* Initalizes SPI driver, resets and starts the device, and makes an initial log.
*
* ## Application Task
* This is an example that shows the capabilities of the ADC 9 Click by calculating voltage level
* based on ADC from channels 0(positive) and 1(negative), and logs the result.
*
* ## Additional Function
* - void measurement_init ( adc9_t *ctx, adc9_rw_t *rw ) - Measurement Initialization function
* is used to easily apply desired settings, in this case device is set to read ADC value
* from channels 0 (positive) and 1 (negative) with default data format, gain, boost and internal clock.
*
* ## NOTE
* Depending on the VOLT SEL jumper position on the Click board the user needs to set VREF
* macro value (mV) in the code.
*
* \author MikroE Team
*
*/
// ------------------------------------------------------------------- INCLUDES
#include "board.h"
#include "log.h"
#include "adc9.h"
#define VREF 2048
// ------------------------------------------------------------------ VARIABLES
static adc9_t adc9;
static adc9_rw_t adc9_rw;
static log_t logger;
int32_t adc_value;
float m_volts;
// ------------------------------------------------------- ADDITIONAL FUNCTIONS
// Measurement Initialization function
void measurement_init ( adc9_t *ctx, adc9_rw_t *rw )
{
uint8_t cfg_data;
uint32_t cfg_data_l;
uint32_t dummy_data;
rw->dev_adr = ADC9_DEVICE_ADR;
rw->reg = ADC9_REG_ADC_DATA;
rw->cmd = ADC9_CMD_INC_READ;
adc9_read_u32( ctx, rw, &dummy_data );
Delay_ms ( 1 );
rw->reg = ADC9_REG_CFG_0;
cfg_data = ADC9_CFG_0_VREF_SEL_0 | ADC9_CFG_0_CLK_SEL_2 |
ADC9_CFG_0_CS_SEL_0 | ADC9_CFG_0_MODE_CONV;
adc9_write_u8( ctx, rw, cfg_data );
Delay_ms ( 1 );
rw->reg = ADC9_REG_CFG_1;
cfg_data = ADC9_CFG_1_PRE_1 | ADC9_CFG_1_OSR_32 | ADC9_CFG_1_DITHER_DEF;
adc9_write_u8( ctx, rw, cfg_data );
Delay_ms ( 1 );
rw->reg = ADC9_REG_CFG_2;
cfg_data = ADC9_CFG_2_BOOST_X_1 | ADC9_CFG_2_GAIN_X_1 | ADC9_CFG_2_AZ_MUX_DIS |
ADC9_CFG_2_AZ_VREF_EN | ADC9_CFG_2_AZ_FREQ_HIGH;
adc9_write_u8( ctx, rw, cfg_data );
Delay_ms ( 1 );
rw->reg = ADC9_REG_CFG_3;
cfg_data = ADC9_CFG_3_CONV_MODE_CONT | ADC9_CFG_3_DATA_FORMAT_DEF |
ADC9_CFG_3_CRC_FORMAT_16 | ADC9_CFG_3_CRC_COM_DIS | ADC9_CFG_3_CRC_OFF_CAL_EN |
ADC9_CFG_3_CRC_GAIN_CAL_EN;
adc9_write_u8( ctx, rw, cfg_data );
Delay_ms ( 1 );
rw->reg = ADC9_REG_MUX;
cfg_data = ADC9_MUX_VIN_POS_CH0 | ADC9_MUX_VIN_NEG_CH1;
adc9_write_u8( ctx, rw, cfg_data );
Delay_ms ( 1 );
cfg_data_l = 0;
rw->reg = ADC9_REG_SCAN;
adc9_write_u24( ctx, rw, cfg_data_l );
Delay_ms ( 1 );
cfg_data_l = 0;
rw->reg = ADC9_REG_OFFSET_CAL;
adc9_write_u24( ctx, rw, cfg_data_l );
Delay_ms ( 1 );
cfg_data_l = 0x00800000;
rw->reg = ADC9_REG_GAIN_CAL;
adc9_write_u24( ctx, rw, cfg_data_l );
Delay_ms ( 1 );
cfg_data_l = 0x00900F00;
rw->reg = ADC9_RSV_REG_W_A;
adc9_write_u24( ctx, rw, cfg_data_l );
Delay_ms ( 1 );
}
// ------------------------------------------------------ APPLICATION FUNCTIONS
void application_init ( void )
{
log_cfg_t log_cfg;
adc9_cfg_t cfg;
/**
* Logger initialization.
* Default baud rate: 115200
* Default log level: LOG_LEVEL_DEBUG
* @note If USB_UART_RX and USB_UART_TX
* are defined as HAL_PIN_NC, you will
* need to define them manually for log to work.
* See @b LOG_MAP_USB_UART macro definition for detailed explanation.
*/
LOG_MAP_USB_UART( log_cfg );
log_init( &logger, &log_cfg );
log_info( &logger, "---- Application Init ----" );
// Click initialization.
adc9_cfg_setup( &cfg );
ADC9_MAP_MIKROBUS( cfg, MIKROBUS_1 );
uint8_t err_flag = adc9_init( &adc9, &cfg );
if ( ADC9_INIT_ERROR == err_flag )
{
log_info( &logger, "---- Error Init ----" );
for ( ; ; );
}
adc9_default_cfg( &adc9, &adc9_rw );
Delay_ms ( 1000 );
}
void application_task ( void )
{
measurement_init( &adc9, &adc9_rw );
while ( adc9_irq_pin_state( &adc9 ) );
adc9_rw.reg = ADC9_DEVICE_ADR;
adc9_read_def_adc ( &adc9, &adc9_rw, &adc_value );
log_printf( &logger, "ADC Value : %ld\r\n" , adc_value );
m_volts = adc9_volt_calc ( &adc9, adc_value, VREF, 1 );
log_printf( &logger, "Voltage in milivolts : %.2f\r\n", m_volts );
log_printf( &logger, "------------------------\r\n" );
Delay_ms ( 1000 );
}
int main ( void )
{
/* Do not remove this line or clock might not be set correctly. */
#ifdef PREINIT_SUPPORTED
preinit();
#endif
application_init( );
for ( ; ; )
{
application_task( );
}
return 0;
}
// ------------------------------------------------------------------------ END