Monitor the current consumption of your motor at all times. Upgrade your engineering toolkit, and embrace the possibilities of brushed motor control.
A
A
Hardware Overview
How does it work?
DC Motor 9 Click is based on the DR8871, a brushed DC motor driver with internal current sensing, by Texas Instruments. This IC is an integrated H-Bridge driver with a current regulation circuit limiting the current through the connected load with a single resistor. Unlike many other solutions, no external sensing resistors are required. A low ON resistance through the H-Bridge reduces the overall power dissipation, while an advanced control circuit injects dead-time intervals whenever the outputs change their state, preventing current shoot-throughs. The DRV8871 integrates protection features, including undervoltage, overcurrent, and overtemperature protection. Each of these events will cause the H-Bridge MOSFETs to be disabled. After removing a fault condition, the device will continue its operation. Two methods can be used to control the motor: the first consists of applying a constant logic level to IN1 and IN2 inputs. While one of the inputs is held at a HIGH logic level, the other should be held at a LOW logic level. The direction of the motor rotation depends on which input is at the
HIGH logic level. The second method involves holding one pin to the LOW level while applying a PWM signal to the other. Changing the PWM frequency makes it possible to control the speed of the motor, while the direction of the motor rotation is determined by the pin the PWM signal is applied to. Both pins to HIGH will set all the MOSFETs in HIGH-Z mode (coast), allowing the backEMF-generated current to return to the source through the MOSFET body diodes. If both IN1 and IN2 pins are set to the LOW logic level, the connected motor is in a braking state. When the PWM signal is applied, the motor will be switched between the braking and rotating modes, causing it to slow down, depending on the pulse width of the applied PWM signal. The frequency of the PWM signal can range between 0 and 200 kHz, with the limitation that the PWM pulses must stay above 800ns for proper detection. Current through the connected load is internally limited to a maximum of 3.6A. A higher current will cause the overcurrent protection to be activated. The peak current through the motor is
limited to about 3.2A, ensuring reliable spin-up while preventing the overcurrent protection from being activated, even if a large load torque is applied. Although there is a low resistance across the H-Bridge, the current should be monitored to prevent excessive heating in situations where the load is reasonably high. Therefore, an additional IC is added, allowing the current to be monitored. The Click board™ uses the LT1999, a bidirectional current sense amplifier from Analog Devices (Linear Technology division). It is used to amplify voltage drop across the shunt resistor so that it can be accurately sampled. The output of the LT1999 IC is routed to the AN pin of the mikroBUS™, allowing the host MCU to sense the current using its integrated ADC module. This Click board™ can only be operated with a 5V logic voltage level. The board must perform appropriate logic voltage level conversion before using MCUs with different logic levels. However, the Click board™ comes equipped with a library containing functions and an example code that can be used as a reference for further development.
Features overview
Development board
Clicker 2 for Kinetis is a compact starter development board that brings the flexibility of add-on Click boards™ to your favorite microcontroller, making it a perfect starter kit for implementing your ideas. It comes with an onboard 32-bit ARM Cortex-M4F microcontroller, the MK64FN1M0VDC12 from NXP Semiconductors, two mikroBUS™ sockets for Click board™ connectivity, a USB connector, LED indicators, buttons, a JTAG programmer connector, and two 26-pin headers for interfacing with external electronics. Its compact design with clear and easily recognizable silkscreen markings allows you to build gadgets with unique functionalities and
features quickly. Each part of the Clicker 2 for Kinetis development kit contains the components necessary for the most efficient operation of the same board. In addition to the possibility of choosing the Clicker 2 for Kinetis programming method, using a USB HID mikroBootloader or an external mikroProg connector for Kinetis programmer, the Clicker 2 board also includes a clean and regulated power supply module for the development kit. It provides two ways of board-powering; through the USB Micro-B cable, where onboard voltage regulators provide the appropriate voltage levels to each component on the board, or
using a Li-Polymer battery via an onboard battery connector. All communication methods that mikroBUS™ itself supports are on this board, including the well-established mikroBUS™ socket, reset button, and several user-configurable buttons and LED indicators. Clicker 2 for Kinetis is an integral part of the Mikroe ecosystem, allowing you to create a new application in minutes. Natively supported by Mikroe software tools, it covers many aspects of prototyping thanks to a considerable number of different Click boards™ (over a thousand boards), the number of which is growing every day.
Microcontroller Overview
MCU Card / MCU
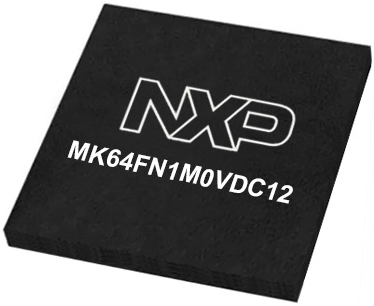
Architecture
ARM Cortex-M4
MCU Memory (KB)
1024
Silicon Vendor
NXP
Pin count
121
RAM (Bytes)
262144
You complete me!
Accessories
DC Gear Motor - 430RPM (3-6V) represents an all-in-one combination of a motor and gearbox, where the addition of gear leads to a reduction of motor speed while increasing the torque output. This gear motor has a spur gearbox, making it a highly reliable solution for applications with lower torque and speed requirements. The most critical parameters for gear motors are speed, torque, and efficiency, which are, in this case, 520RPM with no load and 430RPM at maximum efficiency, alongside a current of 60mA and a torque of 50g.cm. Rated for a 3-6V operational voltage range and clockwise/counterclockwise rotation direction, this motor represents an excellent solution for many functions initially performed by brushed DC motors in robotics, medical equipment, electric door locks, and much more.
Used MCU Pins
mikroBUS™ mapper
Take a closer look
Click board™ Schematic
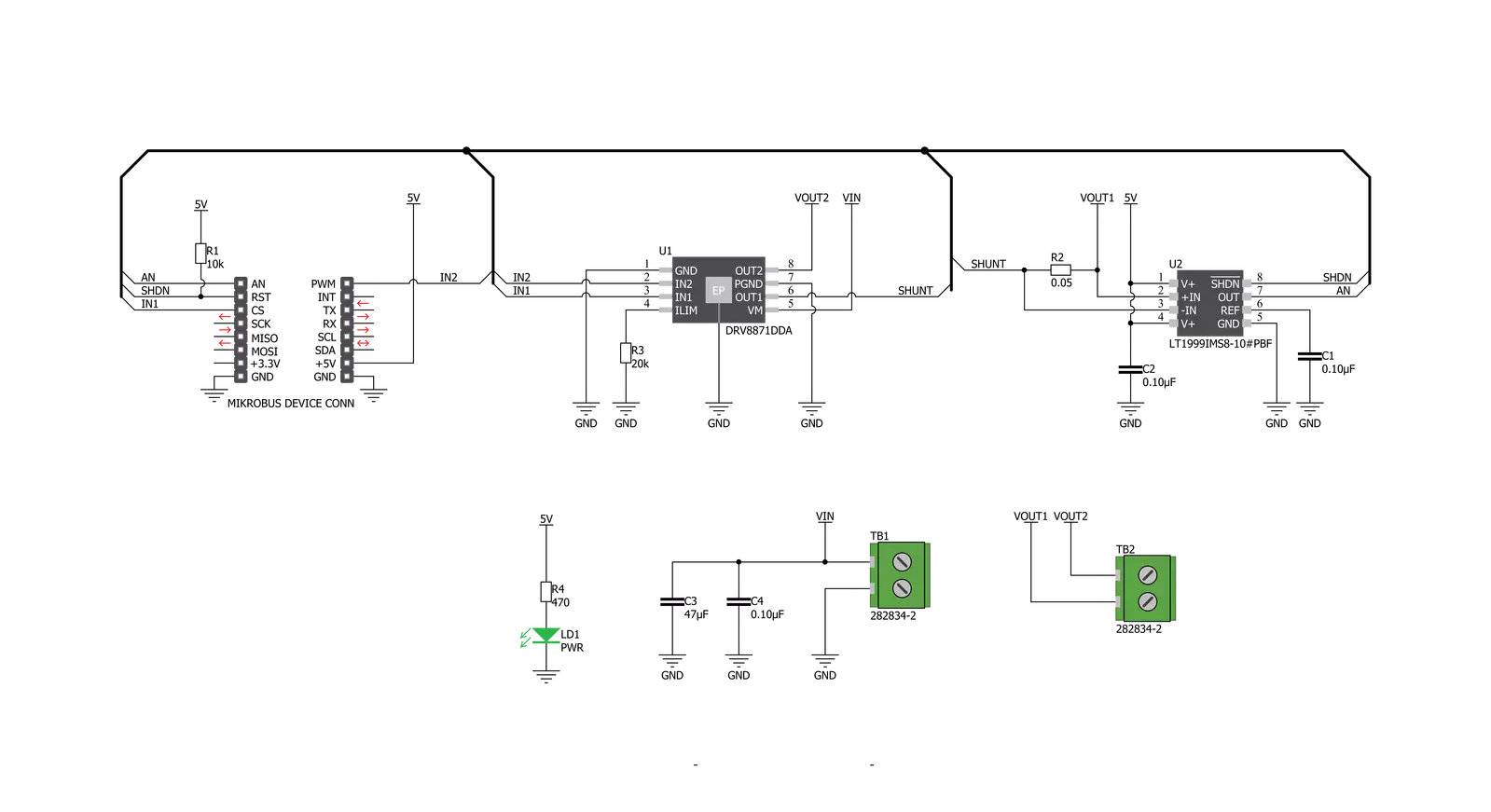
Step by step
Project assembly
Track your results in real time
Application Output
1. Application Output - In Debug mode, the 'Application Output' window enables real-time data monitoring, offering direct insight into execution results. Ensure proper data display by configuring the environment correctly using the provided tutorial.
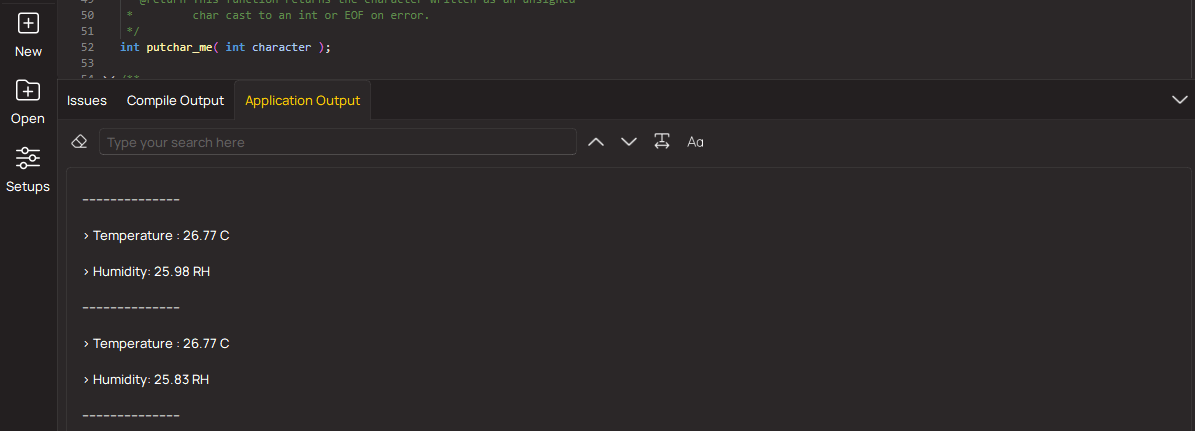
2. UART Terminal - Use the UART Terminal to monitor data transmission via a USB to UART converter, allowing direct communication between the Click board™ and your development system. Configure the baud rate and other serial settings according to your project's requirements to ensure proper functionality. For step-by-step setup instructions, refer to the provided tutorial.
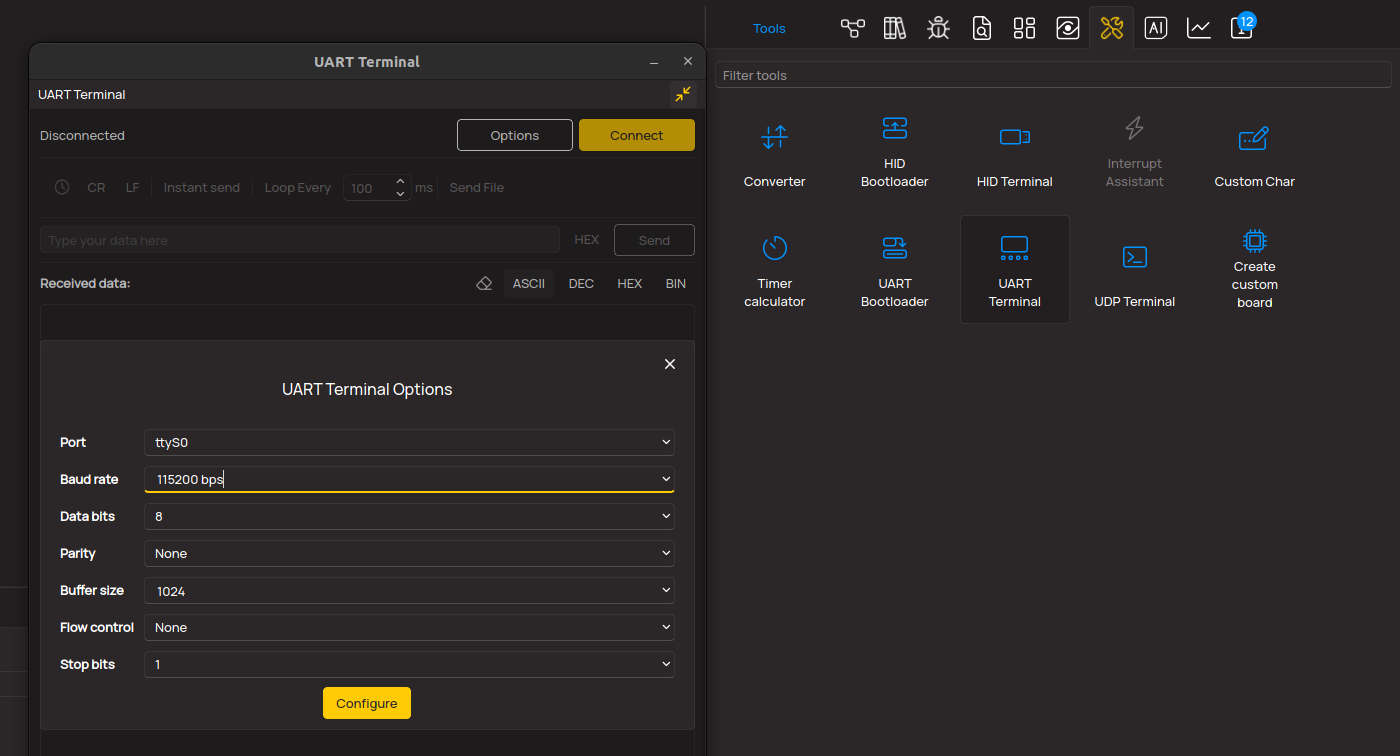
3. Plot Output - The Plot feature offers a powerful way to visualize real-time sensor data, enabling trend analysis, debugging, and comparison of multiple data points. To set it up correctly, follow the provided tutorial, which includes a step-by-step example of using the Plot feature to display Click board™ readings. To use the Plot feature in your code, use the function: plot(*insert_graph_name*, variable_name);. This is a general format, and it is up to the user to replace 'insert_graph_name' with the actual graph name and 'variable_name' with the parameter to be displayed.
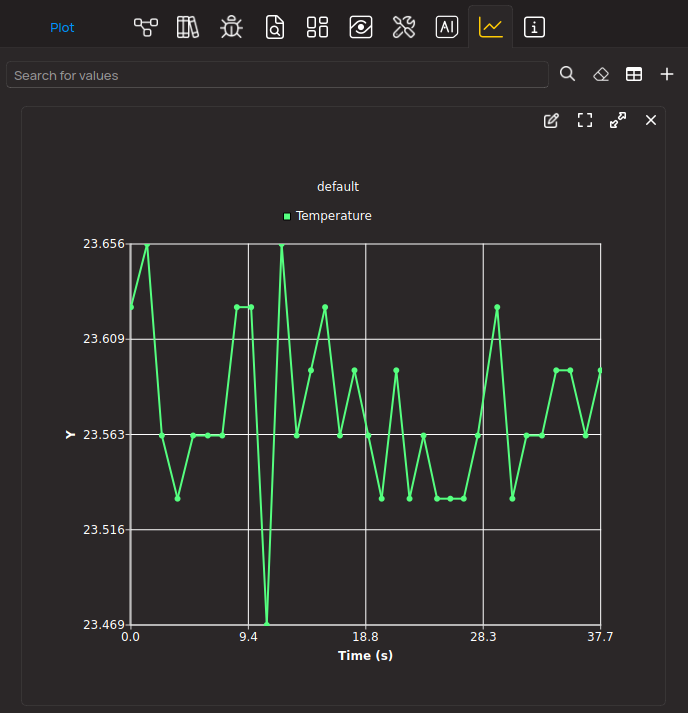
Software Support
Library Description
This library contains API for DC Motor 9 Click driver.
Key functions:
dcmotor9_generic_read
- This function read ADC data.dcmotor9_pwm_start
- This function starts PWM module.dcmotor9_set_duty_cycle
- This function sets the PWM duty cycle.
Open Source
Code example
The complete application code and a ready-to-use project are available through the NECTO Studio Package Manager for direct installation in the NECTO Studio. The application code can also be found on the MIKROE GitHub account.
/*!
* @file main.c
* @brief DC Motor 9 Click Example
*
* # Description
* DC Motor 9 Click is a brushed DC motor driver with the current limiting and
* current sensing. It can be operated by two logic signals, allowing to drive
* the connected motor in two different ways:
* it can use fixed logic levels for the direction control,
* or it can be controlled by a PWM signal, offering an additional speed control
* option.
*
* The demo application is composed of two sections :
*
* ## Application Init
* Initializes GPIO, PWM and logger and enables the Click board.
*
* ## Application Task
* This is a example which demonstrates the use of DC Motor 9 Click board.
* DC Motor 9 Click controls DC Motor speed via PWM interface.
* It shows moving in the both directions from slow to fast speed
* and from fast to slow speed.
* Results are being sent to the Usart Terminal where you can track their changes.
*
* @author Nikola Peric
*
*/
// ------------------------------------------------------------------- INCLUDES
#include "board.h"
#include "log.h"
#include "dcmotor9.h"
// ------------------------------------------------------------------ VARIABLES
static dcmotor9_t dcmotor9;
static log_t logger;
// ------------------------------------------------------ APPLICATION FUNCTIONS
void application_init ( void )
{
log_cfg_t log_cfg;
dcmotor9_cfg_t dcmotor9_cfg;
/**
* Logger initialization.
* Default baud rate: 115200
* Default log level: LOG_LEVEL_DEBUG
* @note If USB_UART_RX and USB_UART_TX
* are defined as HAL_PIN_NC, you will
* need to define them manually for log to work.
* See @b LOG_MAP_USB_UART macro definition for detailed explanation.
*/
LOG_MAP_USB_UART( log_cfg );
log_init( &logger, &log_cfg );
log_info( &logger, "---- Application Init ----" );
// Click initialization.
dcmotor9_cfg_setup( &dcmotor9_cfg );
DCMOTOR9_MAP_MIKROBUS( dcmotor9_cfg, MIKROBUS_1 );
if ( dcmotor9_init( &dcmotor9, &dcmotor9_cfg ) == PWM_ERROR )
{
log_info( &logger, "---- Application Init Error ----" );
log_info( &logger, "---- Please, run program again ----" );
for ( ; ; );
}
dcmotor9_set_duty_cycle ( &dcmotor9, DCMOTOR9_PWM_DUTY_PERCENT_0 );
dcmotor9_enable( &dcmotor9 );
dcmotor9_pwm_start( &dcmotor9 );
log_info( &logger, "---- Application Task ----" );
Delay_ms ( 1000 );
}
void application_task ( void )
{
static float duty;
static uint8_t n_cnt;
dcmotor9_clockwise ( &dcmotor9 );
log_printf( &logger, "> CLOCKWISE <\r\n" );
dcmotor9_enable ( &dcmotor9 );
for ( n_cnt = 10; n_cnt > 0; n_cnt-- )
{
duty = ( float ) n_cnt ;
duty /= 10;
dcmotor9_set_duty_cycle( &dcmotor9, duty );
Delay_ms ( 500 );
}
for ( n_cnt = 1; n_cnt <= 10; n_cnt++ )
{
duty = ( float ) n_cnt ;
duty /= 10;
dcmotor9_set_duty_cycle( &dcmotor9, duty );
Delay_ms ( 500 );
}
log_printf( &logger, "* Pull break *\r\n" );
dcmotor9_short_brake( &dcmotor9 );
Delay_ms ( 1000 );
dcmotor9_counter_clockwise ( &dcmotor9 );
log_printf( &logger, "> COUNTER CLOCKWISE <\r\n" );
for ( n_cnt = 1; n_cnt <= 10; n_cnt++ )
{
duty = ( float ) n_cnt ;
duty /= 10;
dcmotor9_set_duty_cycle( &dcmotor9, duty );
Delay_ms ( 500 );
}
for ( n_cnt = 10; n_cnt > 0; n_cnt-- )
{
duty = ( float ) n_cnt ;
duty /= 10;
dcmotor9_set_duty_cycle( &dcmotor9, duty );
Delay_ms ( 500 );
}
}
int main ( void )
{
/* Do not remove this line or clock might not be set correctly. */
#ifdef PREINIT_SUPPORTED
preinit();
#endif
application_init( );
for ( ; ; )
{
application_task( );
}
return 0;
}
// ------------------------------------------------------------------------ END