Multi-channel data acquisition with robust 5000-VRMS isolation and advanced filtering for electricity meters and battery management
A
A
Hardware Overview
How does it work?
ISO ADC 7 Click is based on the AMC131M03, a three-channel, 24-bit delta-sigma (ΔΣ) ADC with simultaneous sampling capabilities from Texas Instruments, designed for applications requiring precise multi-channel data acquisition, such as electricity meters, battery management systems, EV charging stations, and circuit breakers. The AMC131M03 includes a silicon-dioxide (SiO2)-based capacitive isolation barrier that provides 5000-VRMS isolation (certified by UL1577) for 1 minute, offering excellent immunity to magnetic fields and enhanced safety for use in industrial and high-voltage applications. Additionally, the AMC131M03 meets low EMI standards (CISPR-11 and CISPR-25), ensuring reliable performance in environments with stringent electromagnetic compatibility requirements. Each of the three channels (AIN0-AIN2) of the AMC131M03 includes a built-in digital decimation filter that demodulates the output of the ΔΣ modulator, enabling data rates up to 64kSPS per channel in high-resolution mode. This filter significantly reduces quantization noise, providing a wide dynamic range. The relative phase of the samples between channels can also be adjusted, compensating for any phase delay in sensor responses. Additionally, the modulator's
frequency is derived from a user-selectable clock source, which can be configured via the CLK SEL switch, allowing the choice between 4.096 MHz and 8.192 MHz. The main clock is activated using the XEN pin. A programmable clock divider provides flexibility in setting the modulator's frequency to match specific application needs, further optimizing the device's performance. Thus, as mentioned, the digital decimation filter enhances the signal-to-noise ratio by filtering out-of-band noise, resulting in improved accuracy and efficiency. The AMC131M03 also integrates a low-drift internal voltage reference and a high-precision programmable gain amplifier (PGA), offering gains up to 128. Its integrated precharge buffer ensures high input impedance when the PGA gain exceeds 4, enabling accurate measurements of signals with small amplitudes. The ADC also incorporates a negative charge pump, allowing absolute input voltages as low as 1.3V, making it ideal for single-ended power supply systems measuring signals close to ground. This Click board™ communicates with the host MCU via a standard SPI interface. Additional control pins include the RST pin, which can be used both as a reset and for synchronization across multiple AMC131M03-
based devices, and the RDY pin, which serves as a data-ready interrupt signal. These features allow for flexible and synchronized multi-channel data acquisition, ensuring precise timing and data integrity. A key feature of the AMC131M03 is its integrated temperature sensor, which supports both internal and external temperature measurements. The AIN2 input channel is multiplexed with the temperature sensor, and users can select between internal and external sensing modes through register settings. The AIN2 SEL jumper on the Click board™ allows for selecting the type of external temperature coefficient (TC) element. In the "EXT" position, the jumper enables the use of an external positive (PTC) or negative temperature coefficient (NTC) element, while the "NTC" position activates the onboard NTC sensor for direct temperature measurement. This Click board™ can operate with either 3.3V or 5V logic voltage levels selected via the VCC SEL jumper. This way, both 3.3V and 5V capable MCUs can use the communication lines properly. Also, this Click board™ comes equipped with a library containing easy-to-use functions and an example code that can be used as a reference for further development.
Features overview
Development board
Curiosity PIC32 MZ EF development board is a fully integrated 32-bit development platform featuring the high-performance PIC32MZ EF Series (PIC32MZ2048EFM) that has a 2MB Flash, 512KB RAM, integrated FPU, Crypto accelerator, and excellent connectivity options. It includes an integrated programmer and debugger, requiring no additional hardware. Users can expand
functionality through MIKROE mikroBUS™ Click™ adapter boards, add Ethernet connectivity with the Microchip PHY daughter board, add WiFi connectivity capability using the Microchip expansions boards, and add audio input and output capability with Microchip audio daughter boards. These boards are fully integrated into PIC32’s powerful software framework, MPLAB Harmony,
which provides a flexible and modular interface to application development a rich set of inter-operable software stacks (TCP-IP, USB), and easy-to-use features. The Curiosity PIC32 MZ EF development board offers expansion capabilities making it an excellent choice for a rapid prototyping board in Connectivity, IOT, and general-purpose applications.
Microcontroller Overview
MCU Card / MCU
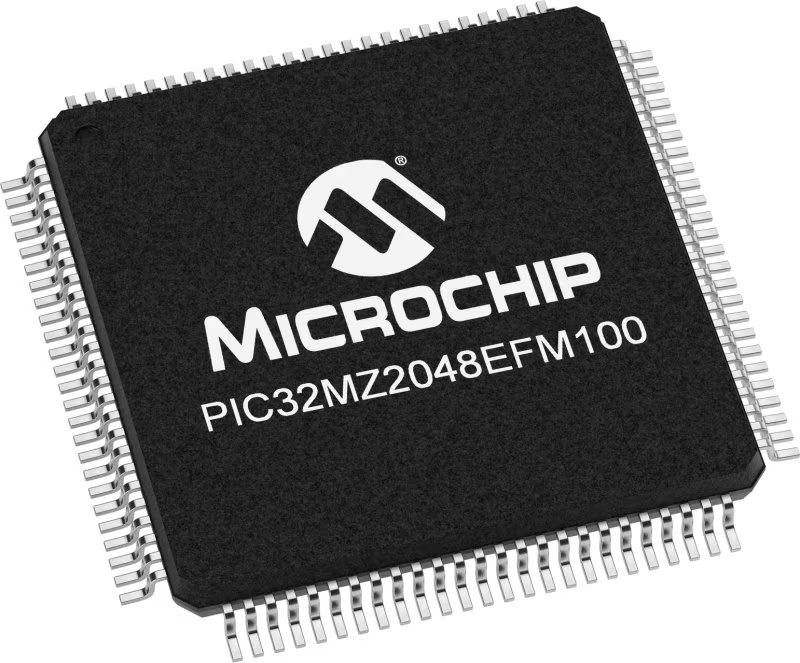
Architecture
PIC32
MCU Memory (KB)
2048
Silicon Vendor
Microchip
Pin count
100
RAM (Bytes)
524288
Used MCU Pins
mikroBUS™ mapper
Take a closer look
Click board™ Schematic
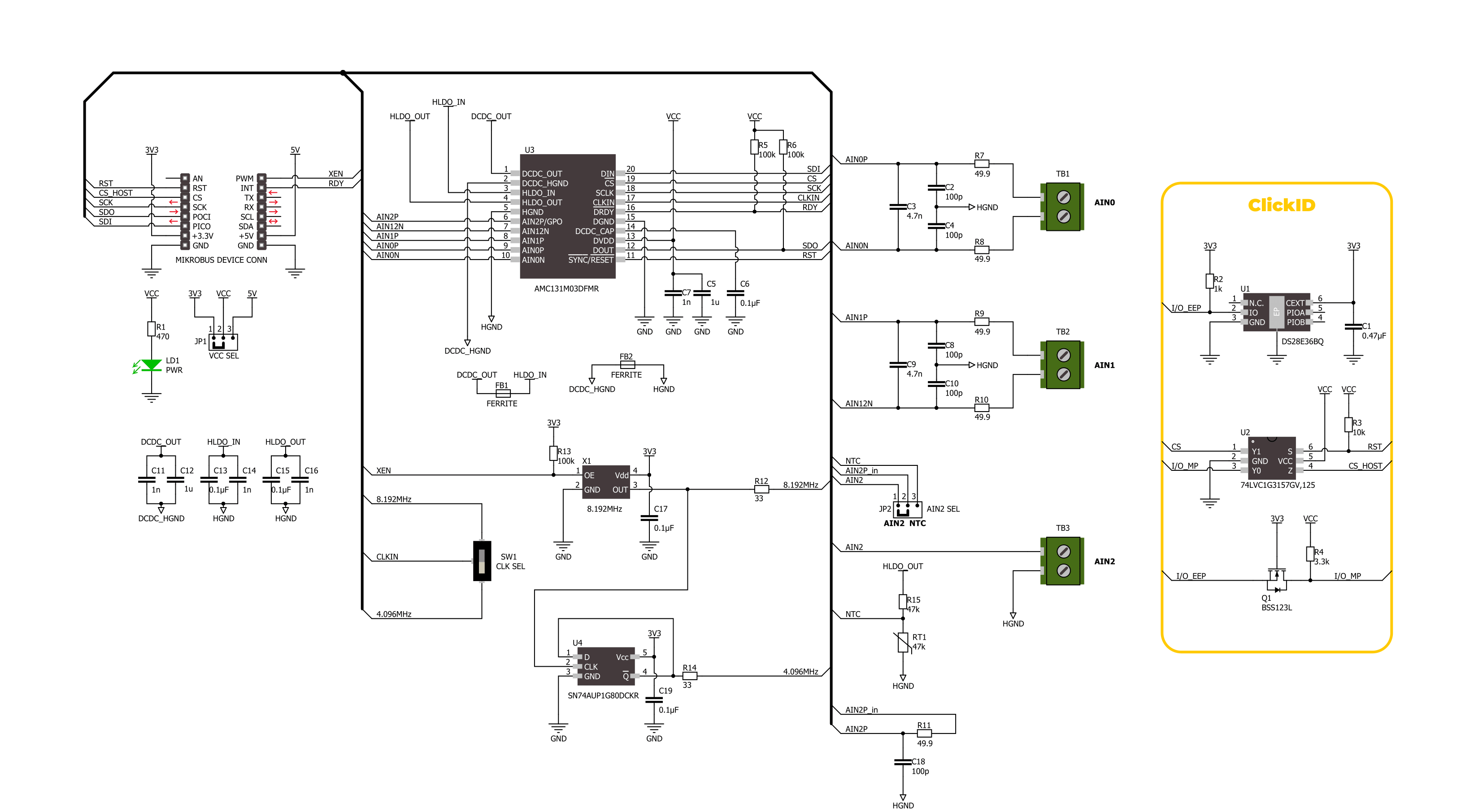
Step by step
Project assembly
Track your results in real time
Application Output
1. Application Output - In Debug mode, the 'Application Output' window enables real-time data monitoring, offering direct insight into execution results. Ensure proper data display by configuring the environment correctly using the provided tutorial.
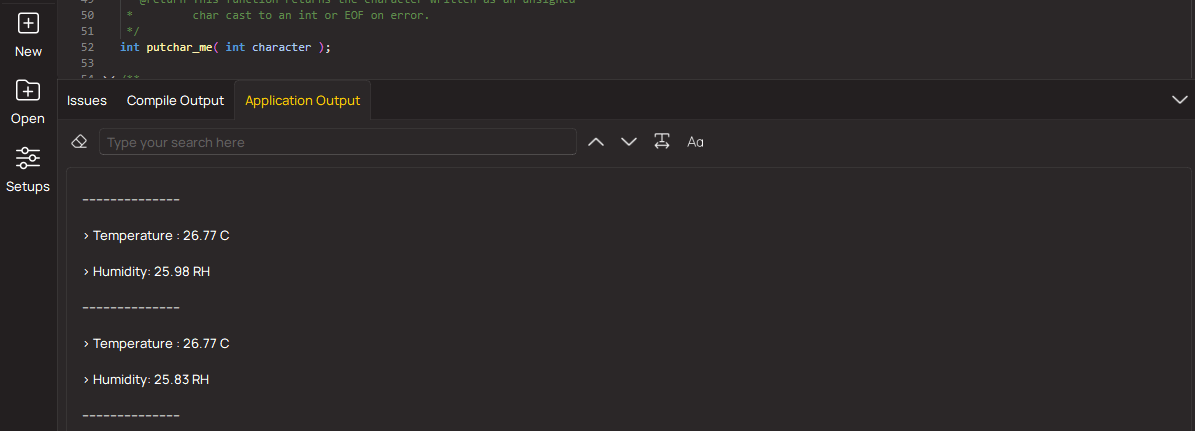
2. UART Terminal - Use the UART Terminal to monitor data transmission via a USB to UART converter, allowing direct communication between the Click board™ and your development system. Configure the baud rate and other serial settings according to your project's requirements to ensure proper functionality. For step-by-step setup instructions, refer to the provided tutorial.
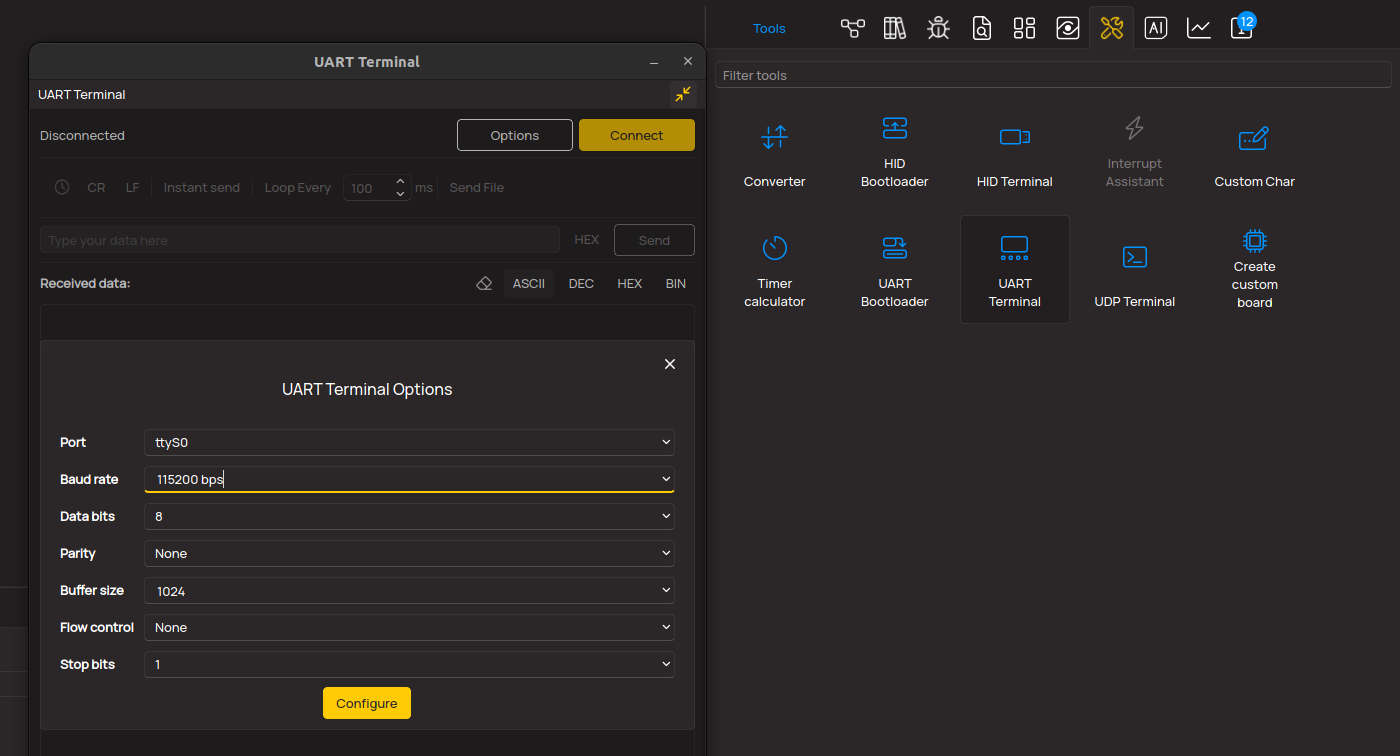
3. Plot Output - The Plot feature offers a powerful way to visualize real-time sensor data, enabling trend analysis, debugging, and comparison of multiple data points. To set it up correctly, follow the provided tutorial, which includes a step-by-step example of using the Plot feature to display Click board™ readings. To use the Plot feature in your code, use the function: plot(*insert_graph_name*, variable_name);. This is a general format, and it is up to the user to replace 'insert_graph_name' with the actual graph name and 'variable_name' with the parameter to be displayed.
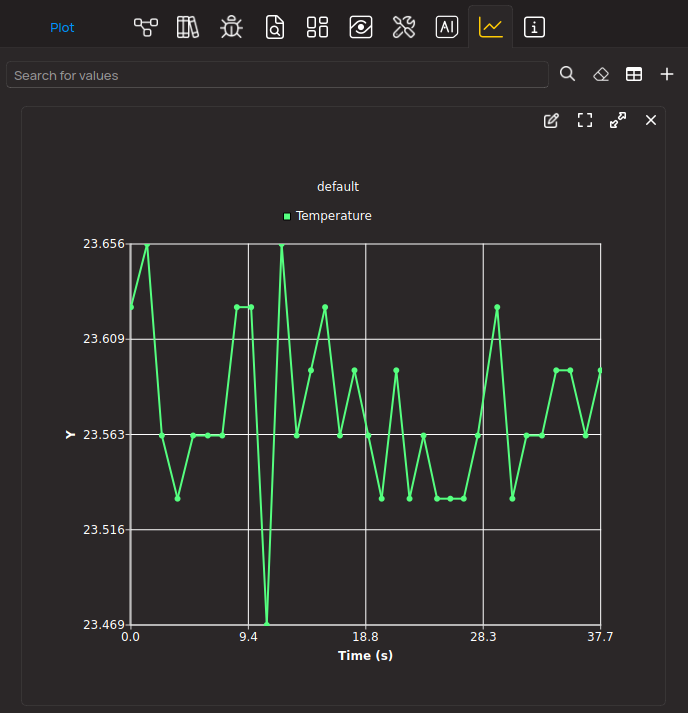
Software Support
Library Description
This library contains API for ISO ADC 7 Click driver.
Key functions:
isoadc7_read_voltage
- This function reads the voltage measurements of all three channels.isoadc7_read_data
- This function reads the status register and raw data of all three channels.isoadc7_set_gain
- This function sets the gain level for all channels.
Open Source
Code example
The complete application code and a ready-to-use project are available through the NECTO Studio Package Manager for direct installation in the NECTO Studio. The application code can also be found on the MIKROE GitHub account.
/*!
* @file main.c
* @brief ISO ADC 7 Click example
*
* # Description
* This example demonstrates the use of ISO ADC 7 Click board by reading and displaying
* the voltage levels from 3 isolated analog input channels.
*
* The demo application is composed of two sections :
*
* ## Application Init
* Initializes the driver and performs the Click default configuration.
* The full-scale voltage input range is set to +-1.2V for all channels.
*
* ## Application Task
* Reads the voltage levels from all 3 isolated analog input channels and displays
* the results on the USB UART once per second approximately.
*
* @author Stefan Filipovic
*
*/
#include "board.h"
#include "log.h"
#include "isoadc7.h"
static isoadc7_t isoadc7;
static log_t logger;
void application_init ( void )
{
log_cfg_t log_cfg; /**< Logger config object. */
isoadc7_cfg_t isoadc7_cfg; /**< Click config object. */
/**
* Logger initialization.
* Default baud rate: 115200
* Default log level: LOG_LEVEL_DEBUG
* @note If USB_UART_RX and USB_UART_TX
* are defined as HAL_PIN_NC, you will
* need to define them manually for log to work.
* See @b LOG_MAP_USB_UART macro definition for detailed explanation.
*/
LOG_MAP_USB_UART( log_cfg );
log_init( &logger, &log_cfg );
log_info( &logger, " Application Init " );
// Click initialization.
isoadc7_cfg_setup( &isoadc7_cfg );
ISOADC7_MAP_MIKROBUS( isoadc7_cfg, MIKROBUS_1 );
if ( SPI_MASTER_ERROR == isoadc7_init( &isoadc7, &isoadc7_cfg ) )
{
log_error( &logger, " Communication init." );
for ( ; ; );
}
if ( ISOADC7_ERROR == isoadc7_default_cfg ( &isoadc7 ) )
{
log_error( &logger, " Default configuration." );
for ( ; ; );
}
log_info( &logger, " Application Task " );
}
void application_task ( void )
{
float ch0 = 0;
float ch1 = 0;
float ch2 = 0;
if ( ISOADC7_OK == isoadc7_read_voltage ( &isoadc7, &ch0, &ch1, &ch2 ) )
{
log_printf ( &logger, " CH0: %.1f mV\r\n", ch0 );
log_printf ( &logger, " CH1: %.1f mV\r\n", ch1 );
log_printf ( &logger, " CH2: %.1f mV\r\n\n", ch2 );
Delay_ms ( 1000 );
}
}
int main ( void )
{
/* Do not remove this line or clock might not be set correctly. */
#ifdef PREINIT_SUPPORTED
preinit();
#endif
application_init( );
for ( ; ; )
{
application_task( );
}
return 0;
}
// ------------------------------------------------------------------------ END