Experience absolutely noiseless motor operation, coupled with maximum efficiency and optimal motor torque, thanks to the industry's most advanced stepper motor driver
A
A
Hardware Overview
How does it work?
Silent Step 4 Click is based on the TMC2240, a smart integrated stepper driver from Analog Devices. It is highly integrated and highly efficient with a best-in-class performance stepper driver. The maximum output current per H-Bridge is 3A, which an onboard resistor sets. You can, however, set it to a lower level over the software. The step driver also features abundant diagnostics and protections such as short protection/OCP, thermal shutdown, and under-voltage lockout. It can measure the driver temperature, estimate the motor temperature, and more. One cool feature is the rotary encoder interface integration directly into the step driver. The external incremental encoder can be connected over the ENC connector. The
encoder can be used for consistency checks on the fly between the encoder position and the external ramp generator position. A 32-bit encoder counter is provided. StallGuard2 is a great functionality for detecting a motor stall and is part of the diagnostic system of the stepper driver. Silent Step 4 Click uses a 4-wire SPI serial interface to communicate with the host MCU, supporting a max frequency of up to 10MHz. The motor is controlled using step and direction inputs over the STP and DIR pins. Each step can be a full-step or a micro-step. The additional functionalities are provided over the PCA9538, an 8-bit I/O port from NXP. The PCA9538 uses an I2C interface to communicate with the host MCU. The I2C address can be set
over the ADDR SEL jumpers. It provides monitoring of both DIAG outputs and over-voltage indicators. It also controls the enable and sleep inputs of the stepper driver. The host MCU can reset the PCA9538 over the RST pin and receive interrupts over the INT pin. This Click board™ can operate with either 3.3V or 5V logic voltage levels selected via the VCC SEL jumper. This way, both 3.3V and 5V capable MCUs can use the communication lines properly. Also, this Click board™ comes equipped with a library containing easy-to-use functions and an example code that can be used as a reference for further development.
Features overview
Development board
Curiosity PIC32 MZ EF development board is a fully integrated 32-bit development platform featuring the high-performance PIC32MZ EF Series (PIC32MZ2048EFM) that has a 2MB Flash, 512KB RAM, integrated FPU, Crypto accelerator, and excellent connectivity options. It includes an integrated programmer and debugger, requiring no additional hardware. Users can expand
functionality through MIKROE mikroBUS™ Click™ adapter boards, add Ethernet connectivity with the Microchip PHY daughter board, add WiFi connectivity capability using the Microchip expansions boards, and add audio input and output capability with Microchip audio daughter boards. These boards are fully integrated into PIC32’s powerful software framework, MPLAB Harmony,
which provides a flexible and modular interface to application development a rich set of inter-operable software stacks (TCP-IP, USB), and easy-to-use features. The Curiosity PIC32 MZ EF development board offers expansion capabilities making it an excellent choice for a rapid prototyping board in Connectivity, IOT, and general-purpose applications.
Microcontroller Overview
MCU Card / MCU
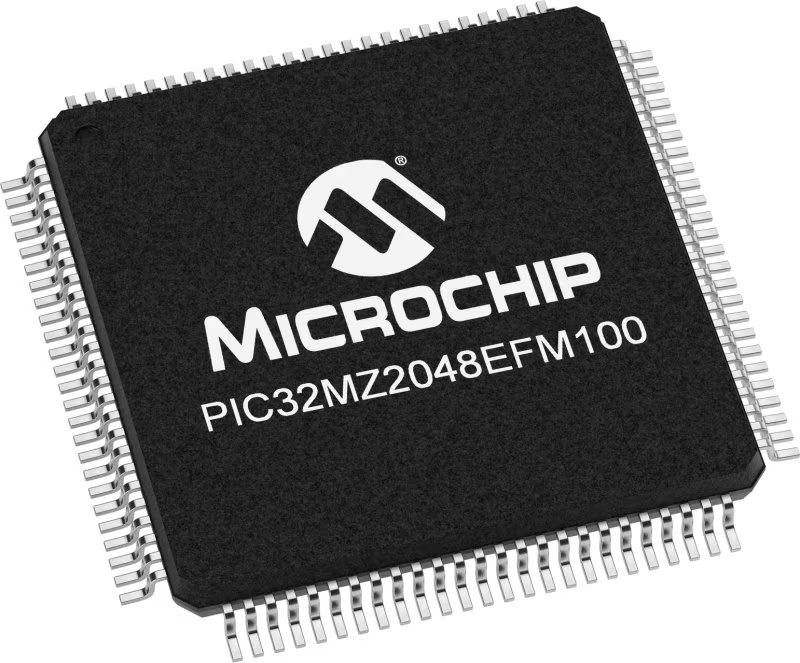
Architecture
PIC32
MCU Memory (KB)
2048
Silicon Vendor
Microchip
Pin count
100
RAM (Bytes)
524288
You complete me!
Accessories
The 17HD40005-22B stepper motor is a two-phase hybrid motor for high torque, high speed, and low noise performance. It features a 1m wire with optional ports on the connection end and heat shrink tubing to prevent tangling. The motor's D-shaped axle is 22mm in length. This motor operates with a chopping wave constant current drive and has a two-phase 4-wire exciting mode, allowing for both forward and reverse rotation. The power order follows AB-BC-CD-DA, viewed as clockwise from the shaft end. It has a rated current of 1.3A DC, a rated voltage of 2.4V, and a stepping angle of 1.8°, with an insulation grade of B. This stepper motor is ideal for applications requiring precise movement control and reliability.
Used MCU Pins
mikroBUS™ mapper
Take a closer look
Click board™ Schematic
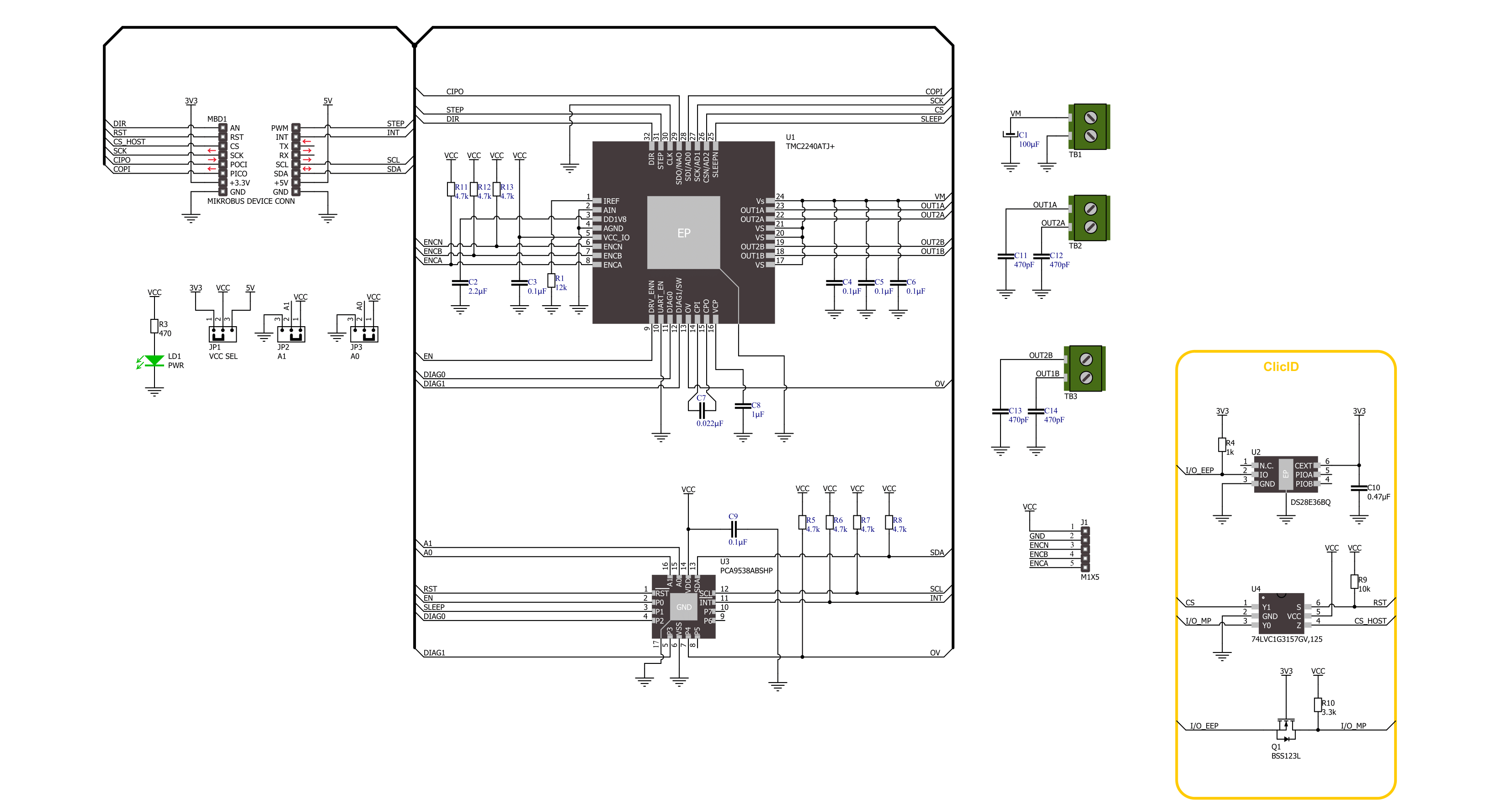
Step by step
Project assembly
Track your results in real time
Application Output
1. Application Output - In Debug mode, the 'Application Output' window enables real-time data monitoring, offering direct insight into execution results. Ensure proper data display by configuring the environment correctly using the provided tutorial.
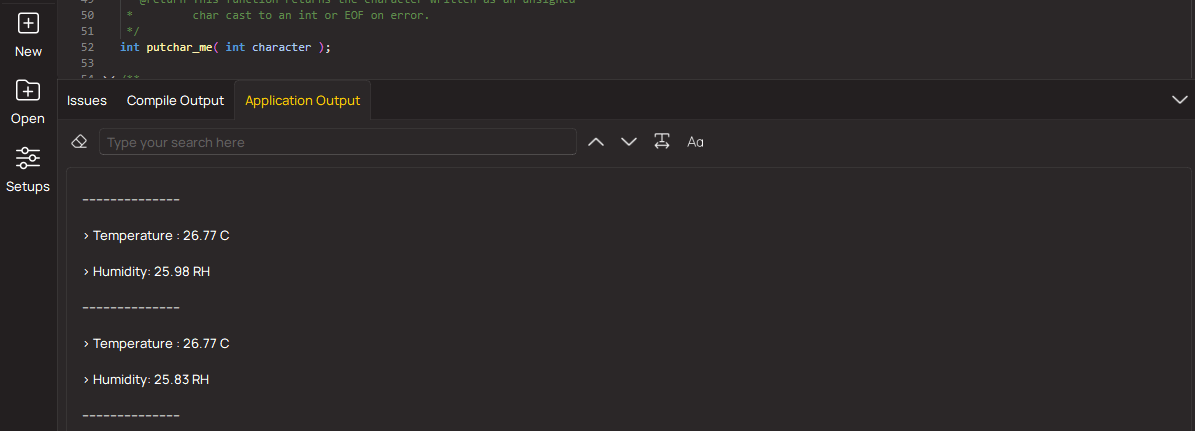
2. UART Terminal - Use the UART Terminal to monitor data transmission via a USB to UART converter, allowing direct communication between the Click board™ and your development system. Configure the baud rate and other serial settings according to your project's requirements to ensure proper functionality. For step-by-step setup instructions, refer to the provided tutorial.
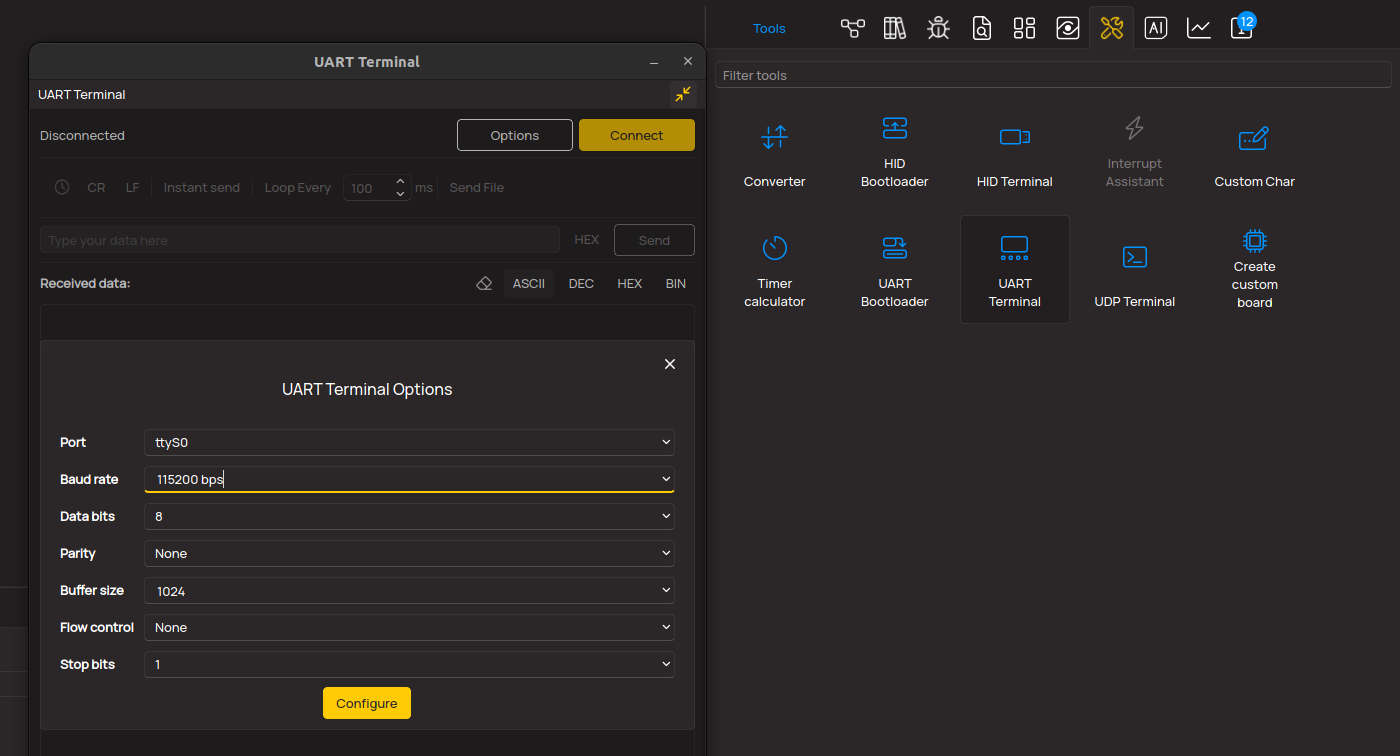
3. Plot Output - The Plot feature offers a powerful way to visualize real-time sensor data, enabling trend analysis, debugging, and comparison of multiple data points. To set it up correctly, follow the provided tutorial, which includes a step-by-step example of using the Plot feature to display Click board™ readings. To use the Plot feature in your code, use the function: plot(*insert_graph_name*, variable_name);. This is a general format, and it is up to the user to replace 'insert_graph_name' with the actual graph name and 'variable_name' with the parameter to be displayed.
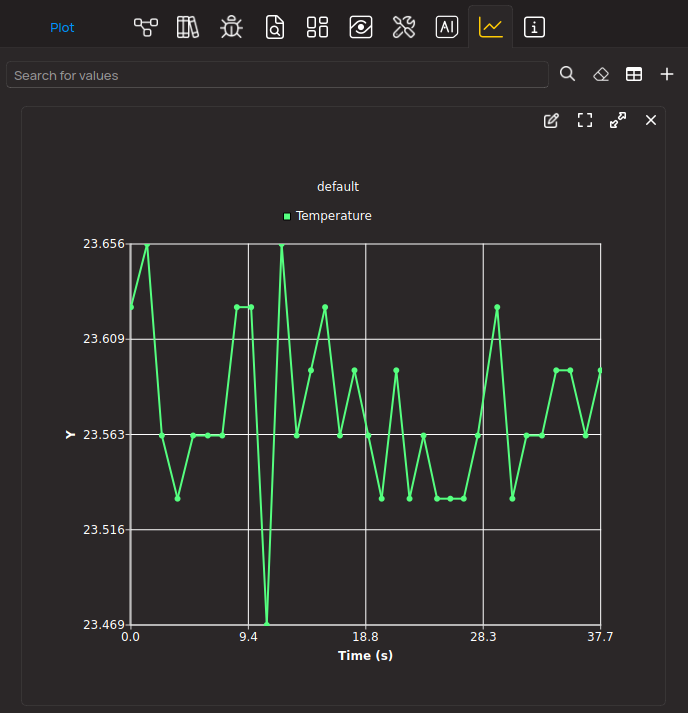
Software Support
Library Description
This library contains API for Silent Step 4 Click driver.
Key functions:
silentstep4_set_direction
- This function sets the motor direction by setting the DIR pin logic statesilentstep4_set_step_res
- This function sets the microstep resolution bits in CHOPCONF registersilentstep4_drive_motor
- This function drives the motor for the specific number of steps at the selected speed
Open Source
Code example
The complete application code and a ready-to-use project are available through the NECTO Studio Package Manager for direct installation in the NECTO Studio. The application code can also be found on the MIKROE GitHub account.
/*!
* @file main.c
* @brief Silent Step 4 Click example
*
* # Description
* This example demonstrates the use of the Silent Step 4 Click board by driving the
* motor in both directions for a desired number of steps.
*
* The demo application is composed of two sections :
*
* ## Application Init
* Initializes the driver and performs the Click default configuration.
*
* ## Application Task
* Drives the motor clockwise for 200 full steps and then counter-clockiwse for 200 half
* steps and 400 quarter steps with 2 seconds delay on driving mode change. All data is
* being logged on the USB UART where you can track the program flow.
*
* @author Stefan Filipovic
*
*/
#include "board.h"
#include "log.h"
#include "silentstep4.h"
static silentstep4_t silentstep4;
static log_t logger;
void application_init ( void )
{
log_cfg_t log_cfg; /**< Logger config object. */
silentstep4_cfg_t silentstep4_cfg; /**< Click config object. */
/**
* Logger initialization.
* Default baud rate: 115200
* Default log level: LOG_LEVEL_DEBUG
* @note If USB_UART_RX and USB_UART_TX
* are defined as HAL_PIN_NC, you will
* need to define them manually for log to work.
* See @b LOG_MAP_USB_UART macro definition for detailed explanation.
*/
LOG_MAP_USB_UART( log_cfg );
log_init( &logger, &log_cfg );
log_info( &logger, " Application Init " );
// Click initialization.
silentstep4_cfg_setup( &silentstep4_cfg );
SILENTSTEP4_MAP_MIKROBUS( silentstep4_cfg, MIKROBUS_1 );
err_t init_flag = silentstep4_init( &silentstep4, &silentstep4_cfg );
if ( ( I2C_MASTER_ERROR == init_flag ) || ( SPI_MASTER_ERROR == init_flag ) )
{
log_error( &logger, " Communication init." );
for ( ; ; );
}
if ( SILENTSTEP4_ERROR == silentstep4_default_cfg ( &silentstep4 ) )
{
log_error( &logger, " Default configuration." );
for ( ; ; );
}
log_info( &logger, " Application Task " );
}
void application_task ( void )
{
log_printf ( &logger, " Move 200 full steps clockwise, speed: slow\r\n\n" );
silentstep4_set_direction ( &silentstep4, SILENTSTEP4_DIR_CW );
silentstep4_set_step_res ( &silentstep4, SILENTSTEP4_MRES_FULLSTEP );
silentstep4_drive_motor ( &silentstep4, 200, SILENTSTEP4_SPEED_SLOW );
Delay_ms ( 1000 );
Delay_ms ( 1000 );
log_printf ( &logger, " Move 200 half steps counter-clockwise, speed: medium\r\n\n" );
silentstep4_set_direction ( &silentstep4, SILENTSTEP4_DIR_CCW );
silentstep4_set_step_res ( &silentstep4, SILENTSTEP4_MRES_2 );
silentstep4_drive_motor ( &silentstep4, 200, SILENTSTEP4_SPEED_MEDIUM );
Delay_ms ( 1000 );
Delay_ms ( 1000 );
log_printf ( &logger, " Move 400 quarter steps counter-clockwise, speed: fast\r\n\n" );
silentstep4_set_direction ( &silentstep4, SILENTSTEP4_DIR_CCW );
silentstep4_set_step_res ( &silentstep4, SILENTSTEP4_MRES_4 );
silentstep4_drive_motor ( &silentstep4, 400, SILENTSTEP4_SPEED_FAST );
Delay_ms ( 1000 );
Delay_ms ( 1000 );
}
int main ( void )
{
/* Do not remove this line or clock might not be set correctly. */
#ifdef PREINIT_SUPPORTED
preinit();
#endif
application_init( );
for ( ; ; )
{
application_task( );
}
return 0;
}
// ------------------------------------------------------------------------ END