Enhance automation in industrial environments and applications that need managing resistive and inductive loads up to 50mH, featuring a current capability of 0.5A for each channel
A
A
Hardware Overview
How does it work?
IPD Click - 2017 is based on the TPD2017FN, an 8-channel low-side switch featuring MOSFET outputs from Toshiba Semiconductor, designed to be directly driven by CMOS and TTL logic circuitry. It's ideally suited for driving inductive and resistive loads, such as industrial programmable logic controllers for industrial use, motors, relays, lamps in factory automation equipment, and more. A key advantage of the TPD2017FN is its built-in overcurrent and overtemperature protection, enhancing system stability by safeguarding against excessive heat and current. Equipped with the capability to handle back electromotive force from inductive loads without surpassing the component's voltage tolerance, the TPD2017FN is optimized for loads up to 50mH with a current capacity of 0.5A per channel, supported by an external power supply ranging from 8-24V. The channels can be
operated in parallel to increase the current capability of the outputs. As mentioned, this Click board™ incorporates comprehensive protection mechanisms, including overtemperature protection that deactivates all outputs (OUT1-OUT8) if the temperature exceeds 175°C and overcurrent protection that limits voltage and current during load shorts, ensuring the device and its connected peripheral safety. Designed for straightforward integration with CMOS and TTL systems, the IPD Click features input control terminals for each output channel, allowing independent channel control. Inputs IN1 to IN4 interface directly via the mikroBUS™ socket, with additional inputs IN5 to IN8 accessible through an unpopulated header. Each input control pin of the TPD2017FN is equipped with a built-in 300kΩ pull-down resistor to maintain a LOW logic state in an open state. This
Click board™ comes with optional inductive load decoupling diodes unpopulated by default, the CRS20140A from Toshiba Semiconductor, allowing users to add them in the case of higher inductive loads. Also, it is equipped with jumpers for the diode configuration of the used load switch and its power management. These jumpers are pre-configured, enabling immediate use without the need for any adjustments. This Click board™ can operate with either 3.3V or 5V logic voltage levels selected via the VCC SEL jumper. This way, both 3.3V and 5V capable MCUs can use the communication lines properly. Also, this Click board™ comes equipped with a library containing easy-to-use functions and an example code that can be used as a reference for further development.
Features overview
Development board
Clicker 4 for STM32F4 is a compact development board designed as a complete solution that you can use to quickly build your own gadgets with unique functionalities. Featuring an STM32F407VGT6 MCU, four mikroBUS™ sockets for Click boards™ connectivity, power management, and more, it represents a perfect solution for the rapid development of many different types of applications. At its core is an STM32F407VGT6 MCU, a powerful microcontroller by STMicroelectronics based on the high-performance
Arm® Cortex®-M4 32-bit processor core operating at up to 168 MHz frequency. It provides sufficient processing power for the most demanding tasks, allowing Clicker 4 to adapt to any specific application requirements. Besides two 1x20 pin headers, four improved mikroBUS™ sockets represent the most distinctive connectivity feature, allowing access to a huge base of Click boards™, growing on a daily basis. Each section of Clicker 4 is clearly marked, offering an intuitive and clean interface. This makes working with the
development board much simpler and, thus, faster. The usability of Clicker 4 doesn’t end with its ability to accelerate the prototyping and application development stages: it is designed as a complete solution that can be implemented directly into any project, with no additional hardware modifications required. Four mounting holes [4.2mm/0.165”] at all four corners allow simple installation by using mounting screws.
Microcontroller Overview
MCU Card / MCU
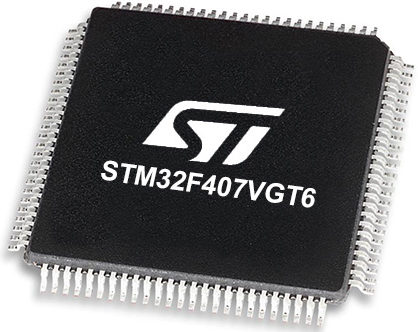
Architecture
ARM Cortex-M4
MCU Memory (KB)
10
Silicon Vendor
STMicroelectronics
Pin count
100
RAM (Bytes)
100
Used MCU Pins
mikroBUS™ mapper
Take a closer look
Click board™ Schematic
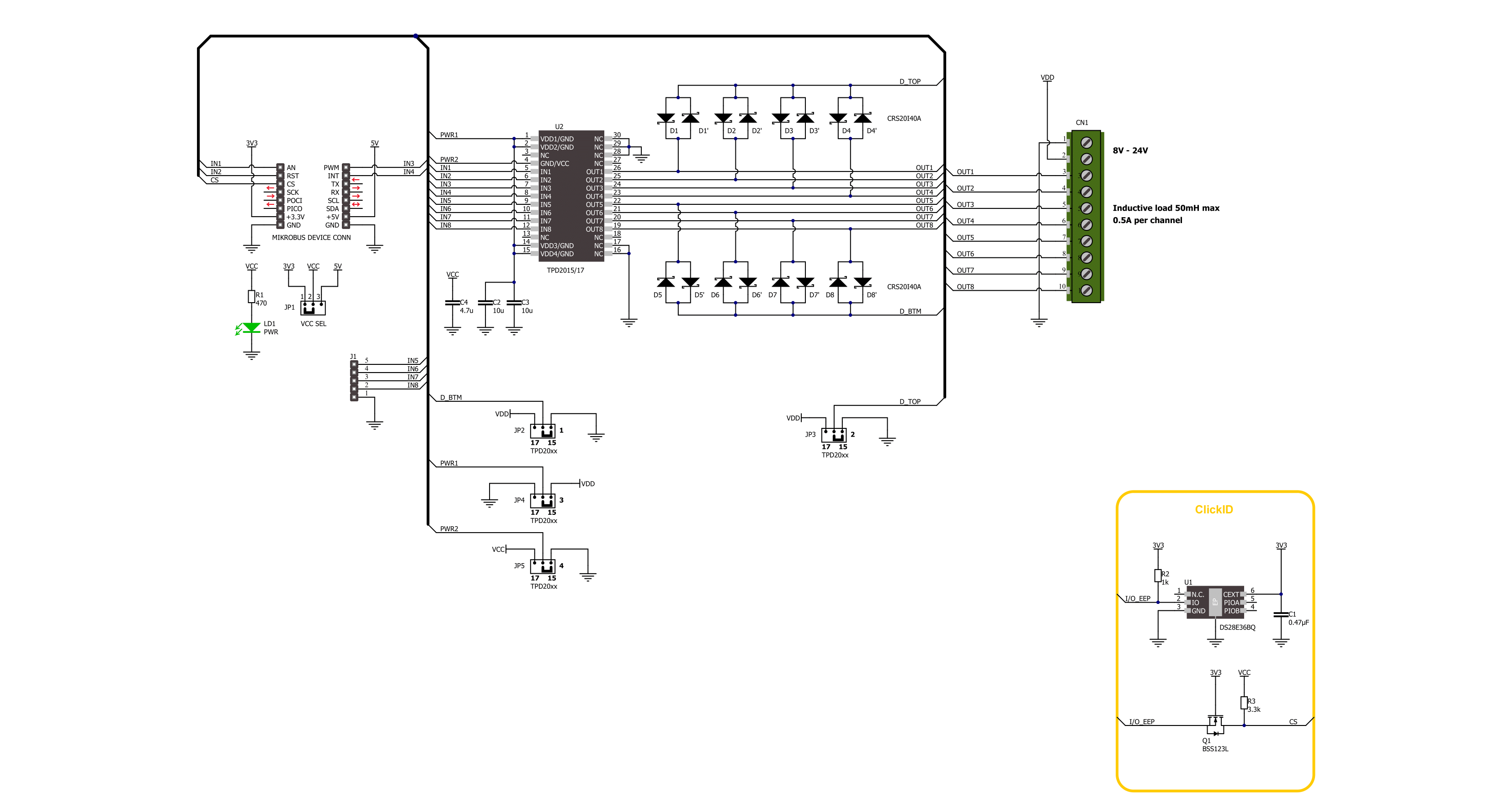
Step by step
Project assembly
Track your results in real time
Application Output
1. Application Output - In Debug mode, the 'Application Output' window enables real-time data monitoring, offering direct insight into execution results. Ensure proper data display by configuring the environment correctly using the provided tutorial.
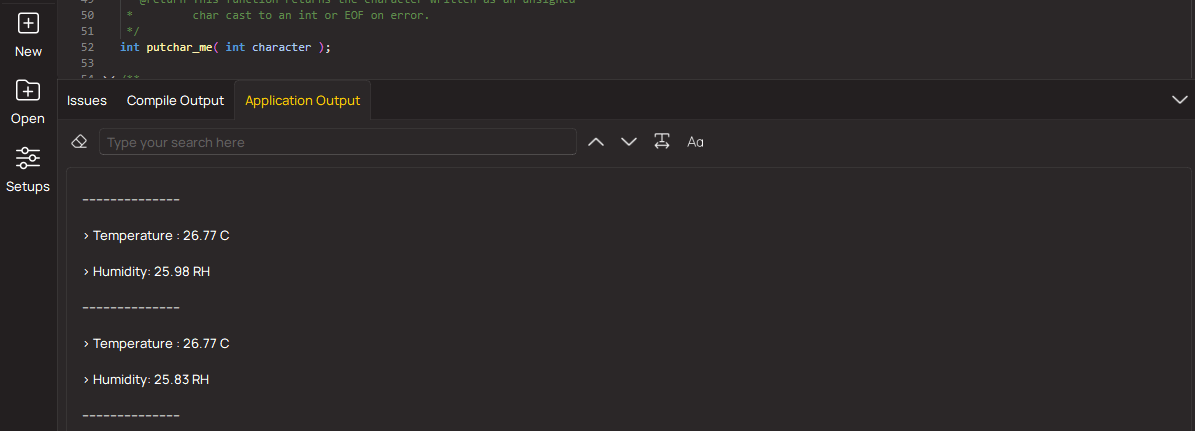
2. UART Terminal - Use the UART Terminal to monitor data transmission via a USB to UART converter, allowing direct communication between the Click board™ and your development system. Configure the baud rate and other serial settings according to your project's requirements to ensure proper functionality. For step-by-step setup instructions, refer to the provided tutorial.
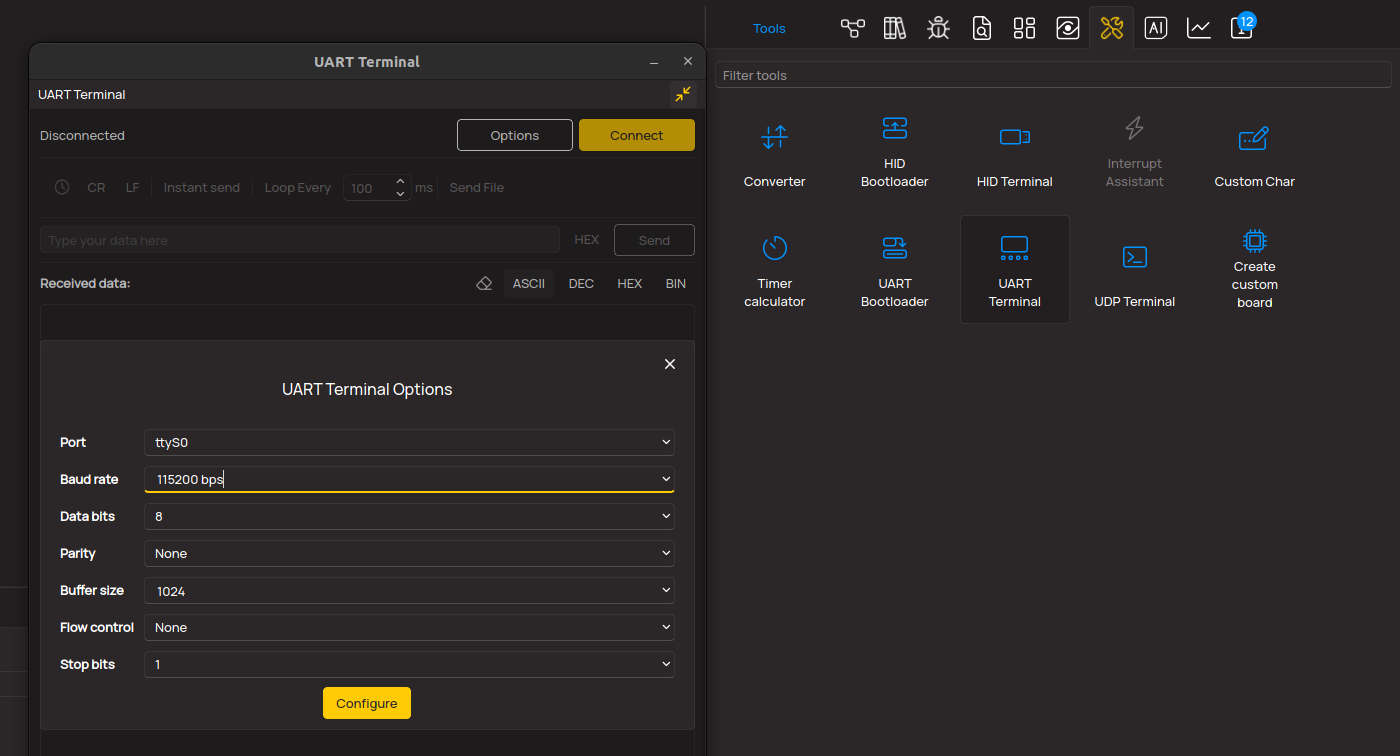
3. Plot Output - The Plot feature offers a powerful way to visualize real-time sensor data, enabling trend analysis, debugging, and comparison of multiple data points. To set it up correctly, follow the provided tutorial, which includes a step-by-step example of using the Plot feature to display Click board™ readings. To use the Plot feature in your code, use the function: plot(*insert_graph_name*, variable_name);. This is a general format, and it is up to the user to replace 'insert_graph_name' with the actual graph name and 'variable_name' with the parameter to be displayed.
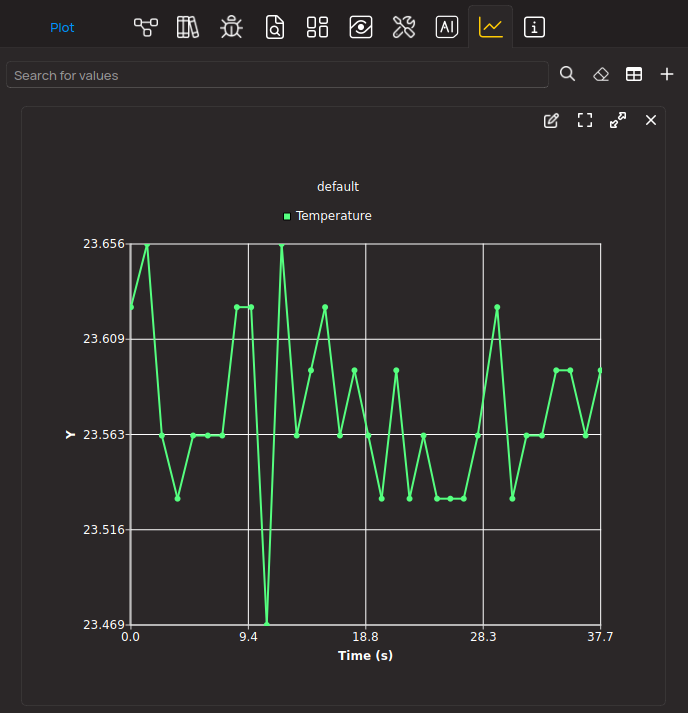
Software Support
Library Description
This library contains API for IPD Click -2017 driver.
Key functions:
ipd2017_all_pins_set
- IPD 2017 pin setting functionipd2017_set_out_level
- IPD 2017 set output level functionipd2017_get_out_state
- IPD 2017 get output level function
Open Source
Code example
The complete application code and a ready-to-use project are available through the NECTO Studio Package Manager for direct installation in the NECTO Studio. The application code can also be found on the MIKROE GitHub account.
/*!
* @file main.c
* @brief IPD 2017 Click Example.
*
* # Description
* This example demonstrates the use of IPD 2017 Click board by toggling the output state.
*
* The demo application is composed of two sections :
*
* ## Application Init
* Initializes the driver and logger.
*
* ## Application Task
* Switches on all output pins state for 2 seconds, then switches them off, and turns them on one by one.
*
* @author Stefan Ilic
*
*/
#include "board.h"
#include "log.h"
#include "ipd2017.h"
static ipd2017_t ipd2017; /**< IPD 2017 Click driver object. */
static log_t logger; /**< Logger object. */
void application_init ( void )
{
log_cfg_t log_cfg; /**< Logger config object. */
ipd2017_cfg_t ipd2017_cfg; /**< Click config object. */
/**
* Logger initialization.
* Default baud rate: 115200
* Default log level: LOG_LEVEL_DEBUG
* @note If USB_UART_RX and USB_UART_TX
* are defined as HAL_PIN_NC, you will
* need to define them manually for log to work.
* See @b LOG_MAP_USB_UART macro definition for detailed explanation.
*/
LOG_MAP_USB_UART( log_cfg );
log_init( &logger, &log_cfg );
log_info( &logger, " Application Init " );
// Click initialization.
ipd2017_cfg_setup( &ipd2017_cfg );
IPD2017_MAP_MIKROBUS( ipd2017_cfg, MIKROBUS_1 );
if ( DIGITAL_OUT_UNSUPPORTED_PIN == ipd2017_init( &ipd2017, &ipd2017_cfg ) )
{
log_error( &logger, " Communication init." );
for ( ; ; );
}
log_info( &logger, " Application Task " );
}
void application_task ( void )
{
log_printf( &logger, " Turning OUT 1 to OUT 4 HIGH \r\n" );
ipd2017_all_pins_set( &ipd2017 );
Delay_ms ( 1000 );
Delay_ms ( 1000 );
log_printf( &logger, " Turning OUT 1 to OUT 4 LOW \r\n" );
ipd2017_all_pins_clear( &ipd2017 );
Delay_ms ( 1000 );
Delay_ms ( 1000 );
log_printf( &logger, " Turning OUT 1 to OUT 4 one by one \r\n" );
uint8_t out_sel = IPD2017_OUT1_PIN_MASK;
do
{
ipd2017_set_out_level( &ipd2017, out_sel, IPD2017_PIN_STATE_HIGH );
Delay_ms ( 1000 );
Delay_ms ( 1000 );
ipd2017_set_out_level( &ipd2017, out_sel, IPD2017_PIN_STATE_LOW );
out_sel <<= 1;
}
while ( out_sel <= IPD2017_OUT4_PIN_MASK );
}
int main ( void )
{
/* Do not remove this line or clock might not be set correctly. */
#ifdef PREINIT_SUPPORTED
preinit();
#endif
application_init( );
for ( ; ; )
{
application_task( );
}
return 0;
}
// ------------------------------------------------------------------------ END