Enhance your design, unlock the full potential of your DC motors, and attain versatile control across multiple operational modes
A
A
Hardware Overview
How does it work?
DC MOTOR 10 Click is based on the TLE 6208-6 G, a fully protected Hex-Half-Bridge-Driver explicitly designed for automotive and industrial motion control applications from Infineon Technologies. It integrates an efficient H-Bridge with a low ON resistance of approximately 0.8Ω through each branch. Furthermore, the built-in features like Over- and Undervoltage-Lockout, Over-Temperature-Protection, and the low quiescent current in standby mode open a wide range of automotive- and industrial applications. DC MOTOR 10 Click is ideally suited for the rapid development of various DC motor driving applications, including home appliances, printers, industrial equipment, mechatronic applications, and more. The part is based on Infineon Smart Power Technology SPT®, which
allows bipolar and CMOS control circuitry in accordance with DMOS power devices existing on the same monolithic circuitry. The six low and high-side drivers are freely configurable and can be controlled separately. Therefore all kinds of loads can be combined. In motion control, up to 5 actuators (DCMotors) can be connected to the six half-bridge outputs (cascade configuration). Operation modes forward (CW), reverse (CCW), brake, and high impedance are controlled from a standard SPI-Interface. Controlling the outputs via software from a central logic allows for limiting power dissipation. The internal logic of TLE 6208-6 G is supplied by the VCC voltage, typical with 5V. The VCC voltage uses an internally generated Power-On Reset (POR) to initialize
the module at Power-on. The advantage of this system is that information stored in the logic remains intact in the event of short-term failures in the supply voltage VS. The system can therefore continue to operate following VS undervoltage without having to be reprogrammed. The undervoltage information is stored and can be read out via the interface. This Click board™ can only be operated with a 5V logic voltage level. The board must perform appropriate logic voltage level conversion before using MCUs with different logic levels. However, the Click board™ comes equipped with a library containing functions and an example code that can be used as a reference for further development.
Features overview
Development board
PIC18F57Q43 Curiosity Nano evaluation kit is a cutting-edge hardware platform designed to evaluate microcontrollers within the PIC18-Q43 family. Central to its design is the inclusion of the powerful PIC18F57Q43 microcontroller (MCU), offering advanced functionalities and robust performance. Key features of this evaluation kit include a yellow user LED and a responsive
mechanical user switch, providing seamless interaction and testing. The provision for a 32.768kHz crystal footprint ensures precision timing capabilities. With an onboard debugger boasting a green power and status LED, programming and debugging become intuitive and efficient. Further enhancing its utility is the Virtual serial port (CDC) and a debug GPIO channel (DGI
GPIO), offering extensive connectivity options. Powered via USB, this kit boasts an adjustable target voltage feature facilitated by the MIC5353 LDO regulator, ensuring stable operation with an output voltage ranging from 1.8V to 5.1V, with a maximum output current of 500mA, subject to ambient temperature and voltage constraints.
Microcontroller Overview
MCU Card / MCU
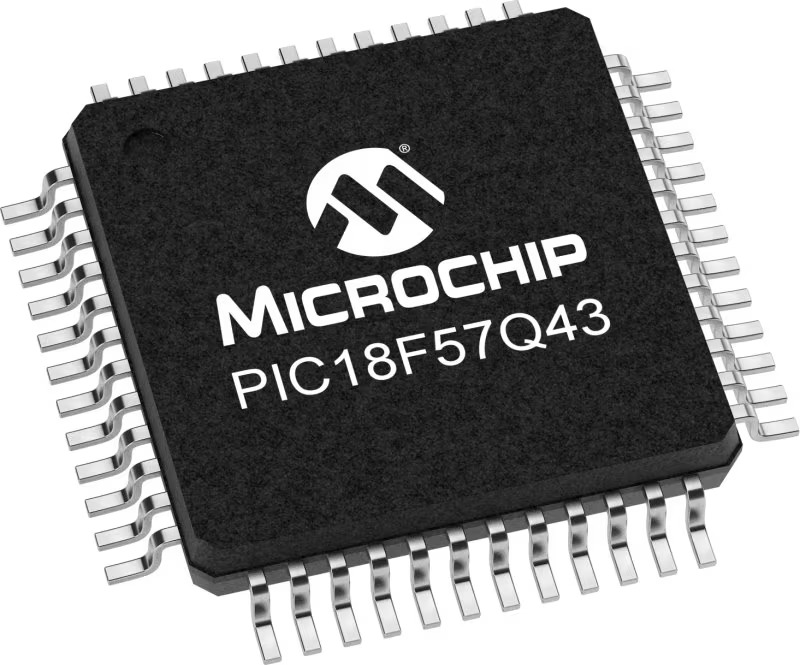
Architecture
PIC
MCU Memory (KB)
128
Silicon Vendor
Microchip
Pin count
48
RAM (Bytes)
8196
You complete me!
Accessories
Curiosity Nano Base for Click boards is a versatile hardware extension platform created to streamline the integration between Curiosity Nano kits and extension boards, tailored explicitly for the mikroBUS™-standardized Click boards and Xplained Pro extension boards. This innovative base board (shield) offers seamless connectivity and expansion possibilities, simplifying experimentation and development. Key features include USB power compatibility from the Curiosity Nano kit, alongside an alternative external power input option for enhanced flexibility. The onboard Li-Ion/LiPo charger and management circuit ensure smooth operation for battery-powered applications, simplifying usage and management. Moreover, the base incorporates a fixed 3.3V PSU dedicated to target and mikroBUS™ power rails, alongside a fixed 5.0V boost converter catering to 5V power rails of mikroBUS™ sockets, providing stable power delivery for various connected devices.
DC Gear Motor - 430RPM (3-6V) represents an all-in-one combination of a motor and gearbox, where the addition of gear leads to a reduction of motor speed while increasing the torque output. This gear motor has a spur gearbox, making it a highly reliable solution for applications with lower torque and speed requirements. The most critical parameters for gear motors are speed, torque, and efficiency, which are, in this case, 520RPM with no load and 430RPM at maximum efficiency, alongside a current of 60mA and a torque of 50g.cm. Rated for a 3-6V operational voltage range and clockwise/counterclockwise rotation direction, this motor represents an excellent solution for many functions initially performed by brushed DC motors in robotics, medical equipment, electric door locks, and much more.
Used MCU Pins
mikroBUS™ mapper
Take a closer look
Click board™ Schematic
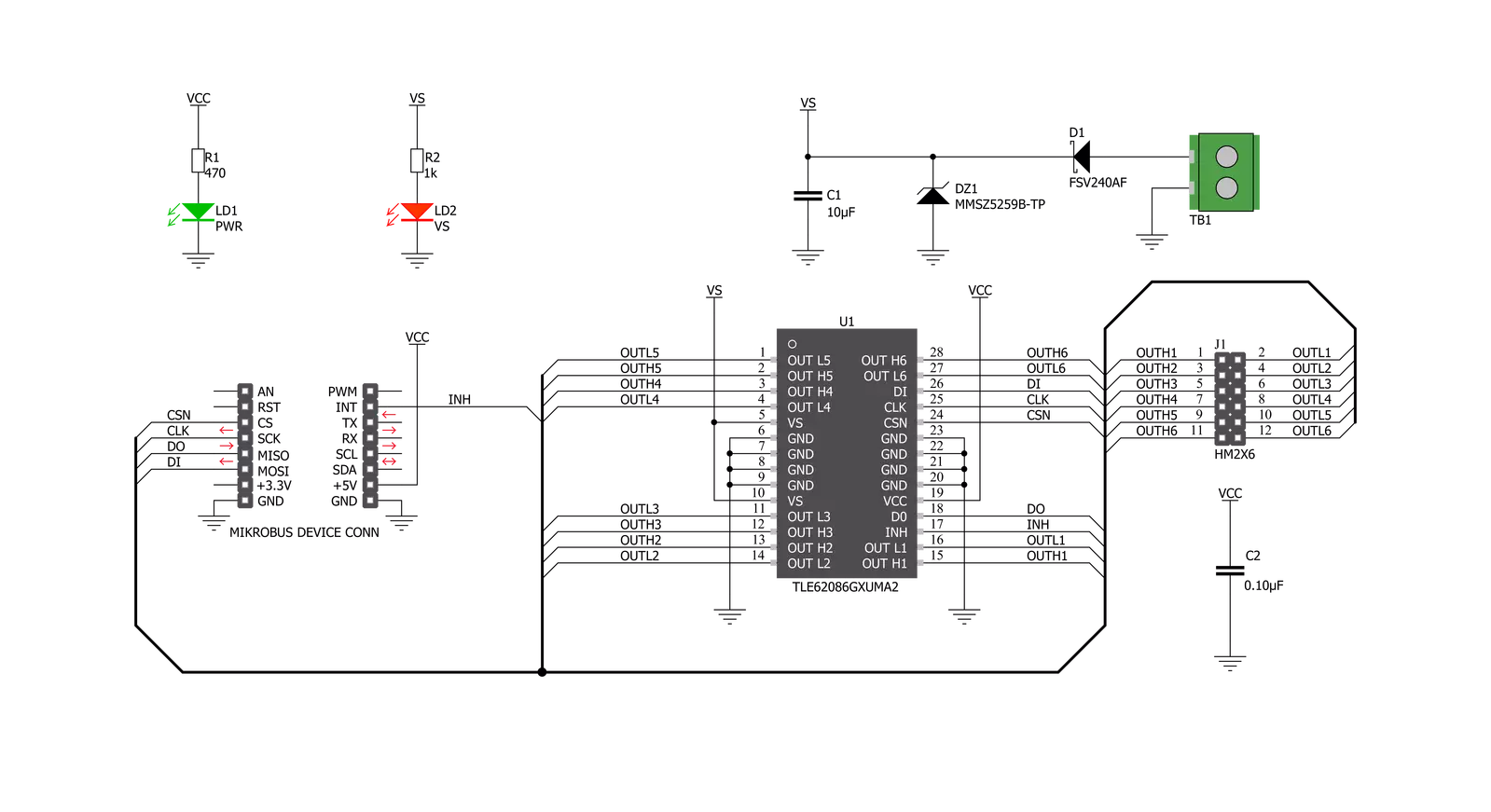
Step by step
Project assembly
Track your results in real time
Application Output
1. Application Output - In Debug mode, the 'Application Output' window enables real-time data monitoring, offering direct insight into execution results. Ensure proper data display by configuring the environment correctly using the provided tutorial.
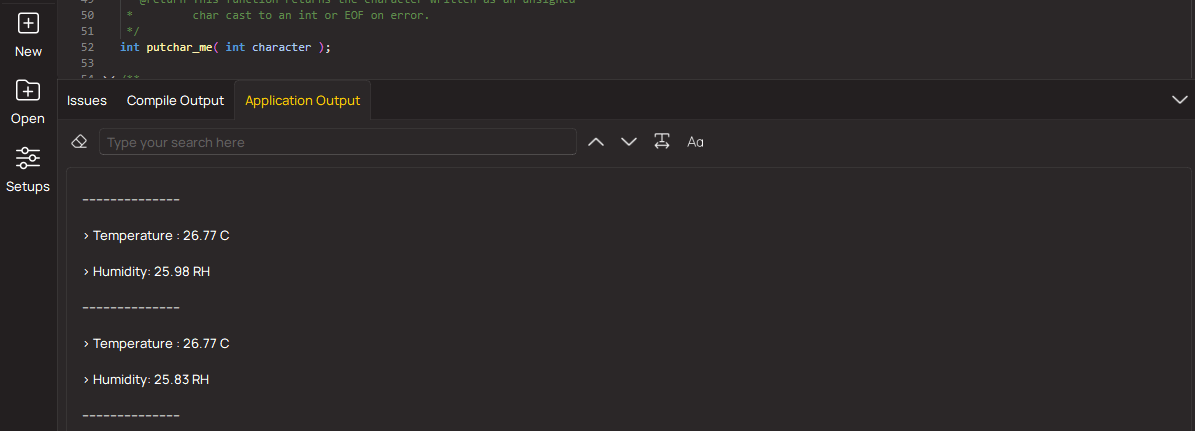
2. UART Terminal - Use the UART Terminal to monitor data transmission via a USB to UART converter, allowing direct communication between the Click board™ and your development system. Configure the baud rate and other serial settings according to your project's requirements to ensure proper functionality. For step-by-step setup instructions, refer to the provided tutorial.
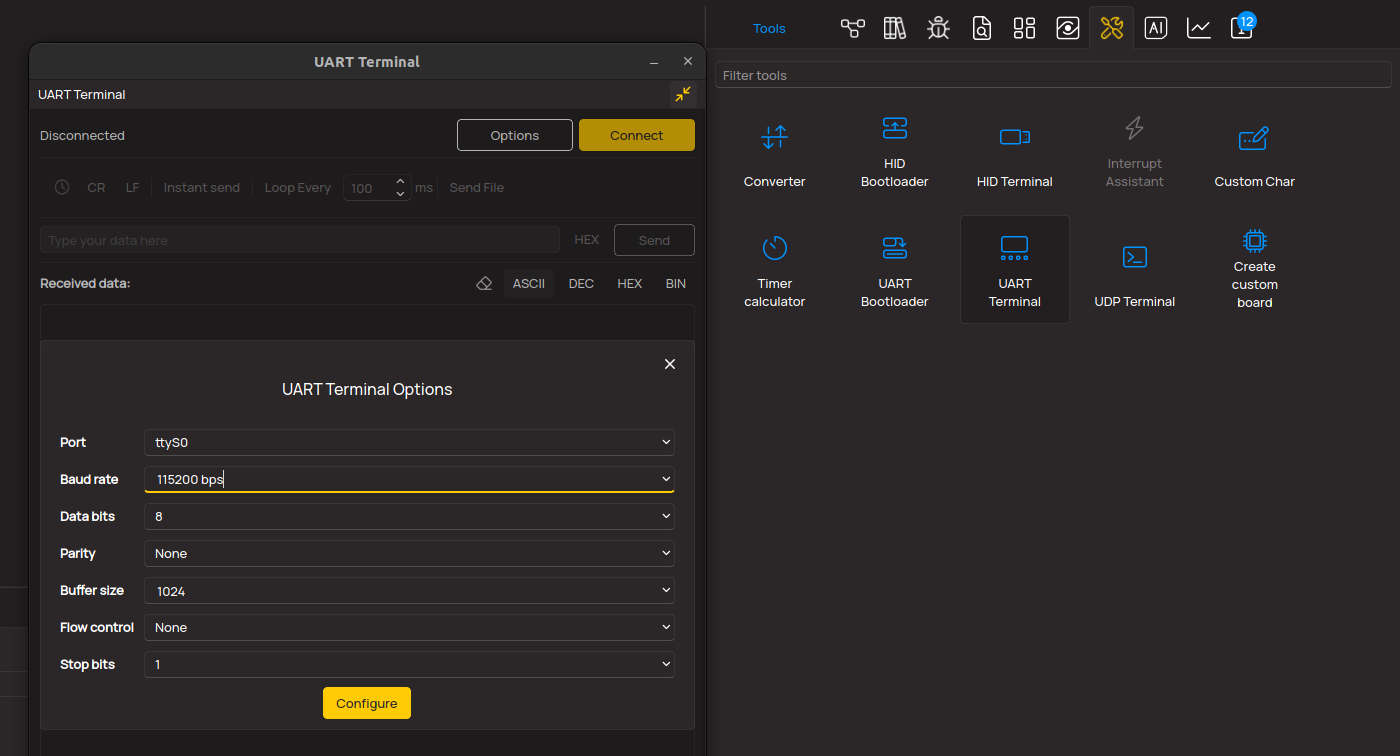
3. Plot Output - The Plot feature offers a powerful way to visualize real-time sensor data, enabling trend analysis, debugging, and comparison of multiple data points. To set it up correctly, follow the provided tutorial, which includes a step-by-step example of using the Plot feature to display Click board™ readings. To use the Plot feature in your code, use the function: plot(*insert_graph_name*, variable_name);. This is a general format, and it is up to the user to replace 'insert_graph_name' with the actual graph name and 'variable_name' with the parameter to be displayed.
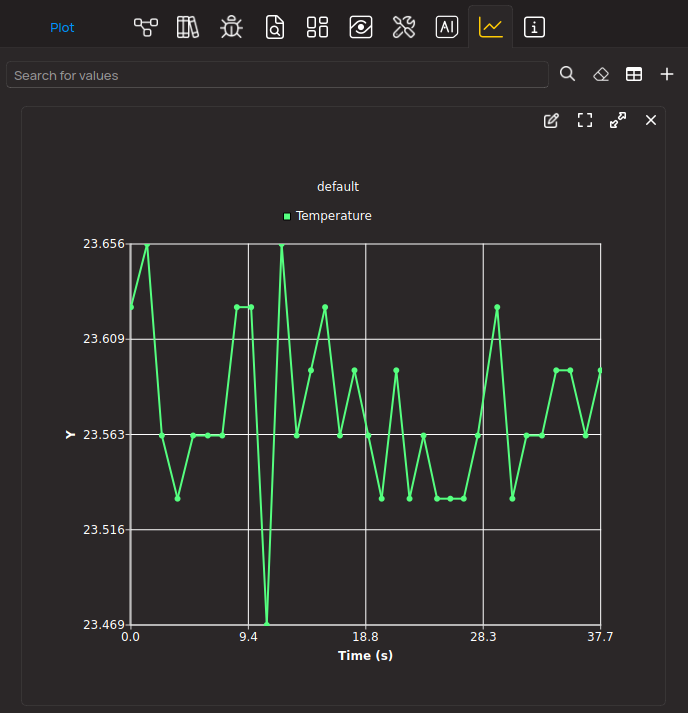
Software Support
Library Description
This library contains API for DC Motor 10 Click driver.
Key functions:
void dcmotor10_resetStatusReg();
- Function is used to reset status register.void dcmotor10_enableChann1();
- Function is used to enable channel 1.void dcmotor10_sendCommand( uint16_t wrData );
- Function is used to send command.
Open Source
Code example
The complete application code and a ready-to-use project are available through the NECTO Studio Package Manager for direct installation in the NECTO Studio. The application code can also be found on the MIKROE GitHub account.
/*!
* \file
* \brief DcMotor10 Click example
*
* # Description
* This example is running dc motors on channels 1 through 3.
*
* The demo application is composed of two sections :
*
* ## Application Init
* Initalizes SPI, Click drivers and uninhibites the device.
*
* ## Application Task
* This example demonstrates the use of DC MOTOR 10 Click by running dc motors
* on channels 1 through 3, first all 3 together and then separately.
*
* \author Jovan Stajkovic
*
*/
// ------------------------------------------------------------------- INCLUDES
#include "board.h"
#include "log.h"
#include "dcmotor10.h"
// ------------------------------------------------------------------ VARIABLES
static dcmotor10_t dcmotor10;
static log_t logger;
// ------------------------------------------------------ APPLICATION FUNCTIONS
void application_init ( void )
{
log_cfg_t log_cfg;
dcmotor10_cfg_t cfg;
/**
* Logger initialization.
* Default baud rate: 115200
* Default log level: LOG_LEVEL_DEBUG
* @note If USB_UART_RX and USB_UART_TX
* are defined as HAL_PIN_NC, you will
* need to define them manually for log to work.
* See @b LOG_MAP_USB_UART macro definition for detailed explanation.
*/
LOG_MAP_USB_UART( log_cfg );
log_init( &logger, &log_cfg );
log_info( &logger, "---- Application Init ----" );
// Click initialization.
dcmotor10_cfg_setup( &cfg );
DCMOTOR10_MAP_MIKROBUS( cfg, MIKROBUS_1 );
dcmotor10_init( &dcmotor10, &cfg );
Delay_ms ( 100 );
dcmotor10_inhibit(&dcmotor10, DCMOTOR10_UNINHIBIT );
dcmotor10_send_cmd( &dcmotor10, DCMOTOR10_RESET_STATUS_REG );
Delay_ms ( 100 );
}
void application_task ( void )
{
dcmotor10_send_cmd( &dcmotor10, DCMOTOR10_ENABLE_1 | DCMOTOR10_ENABLE_2
| DCMOTOR10_ENABLE_3 );
Delay_ms ( 1000 );
Delay_ms ( 1000 );
Delay_ms ( 1000 );
Delay_ms ( 1000 );
Delay_ms ( 1000 );
dcmotor10_send_cmd( &dcmotor10, DCMOTOR10_ENABLE_1 );
Delay_ms ( 1000 );
Delay_ms ( 1000 );
Delay_ms ( 1000 );
Delay_ms ( 1000 );
Delay_ms ( 1000 );
dcmotor10_send_cmd( &dcmotor10, DCMOTOR10_ENABLE_2 );
Delay_ms ( 1000 );
Delay_ms ( 1000 );
Delay_ms ( 1000 );
Delay_ms ( 1000 );
Delay_ms ( 1000 );
dcmotor10_send_cmd( &dcmotor10, DCMOTOR10_ENABLE_3 );
Delay_ms ( 1000 );
Delay_ms ( 1000 );
Delay_ms ( 1000 );
Delay_ms ( 1000 );
Delay_ms ( 1000 );
dcmotor10_send_cmd( &dcmotor10, DCMOTOR10_RESET_STATUS_REG );
Delay_ms ( 1000 );
}
int main ( void )
{
/* Do not remove this line or clock might not be set correctly. */
#ifdef PREINIT_SUPPORTED
preinit();
#endif
application_init( );
for ( ; ; )
{
application_task( );
}
return 0;
}
// ------------------------------------------------------------------------ END