Capable of delivering up to 2.5A of full-scale output current, ideal for driving various stepper motors in robotics, precision systems, and automation
A
A
Hardware Overview
How does it work?
Stepper 19 Click is based on the DRV8424, a stepper motor driver from Texas Instruments, made for both industrial and consumer applications. This integrated circuit stands out with its comprehensive integration, including dual N-channel power MOSFET H-bridge drivers, a microstepping indexer, and integrated current sensing. The DRV8424 operates on an external power supply ranging from 5V to 30V and can drive up to 2.5A of full-scale output current. Its design eliminates the need for external power sense resistors by utilizing an internal current sense architecture, conserving PCB space and reducing overall system cost. The DRV8424 optimizes performance through an internal PWM current regulation scheme, offering smart tune, slow, and mixed decay options selections. The smart tune feature dynamically adjusts to ensure optimal current regulation,
compensates for motor variations and aging, and minimizes audible noise produced by the motor. Control over the stepper motor is achieved via a straightforward STEP/DIR interface, which permits an external controller to dictate the motor's stepping direction and rate. Microstepping resolution ranges from full-step to 1/256, selectable through the STP pin of the mikroBUS™ socket, with the direction controlled by the DIR pin. The device also includes a low-power sleep mode accessible via the RST pin. It has several protection features for conditions like supply undervoltage, charge pump faults, overcurrent, short circuits, and overtemperature, with fault indications through the FLT pin. The DRV8424's enable/disable function is managed by the EN pin. Additional functionalities on this Click board™ are achieved over the PCA9538A, an 8-bit I/O port from NXP, which
interfaces with the main MCU via I2C, offering selectable addresses through the ADDR SEL jumpers. Besides DIR and STP pins on the mikroBUS™ socket, the PCA9538A can also control these functions if the R12 and R16 resistors are populated on the board. This configuration flexibility, combined with the DRV8424's efficiency and the PCA9538A's extensive control capabilities, makes Stepper 19 Click a powerful solution for driving stepper motors in various application scenarios. This Click board™ can operate with either 3.3V or 5V logic voltage levels selected via the VCC SEL jumper. This way, both 3.3V and 5V capable MCUs can use the communication lines properly. Also, this Click board™ comes equipped with a library containing easy-to-use functions and an example code that can be used as a reference for further development.
Features overview
Development board
Arduino UNO is a versatile microcontroller board built around the ATmega328P chip. It offers extensive connectivity options for various projects, featuring 14 digital input/output pins, six of which are PWM-capable, along with six analog inputs. Its core components include a 16MHz ceramic resonator, a USB connection, a power jack, an
ICSP header, and a reset button, providing everything necessary to power and program the board. The Uno is ready to go, whether connected to a computer via USB or powered by an AC-to-DC adapter or battery. As the first USB Arduino board, it serves as the benchmark for the Arduino platform, with "Uno" symbolizing its status as the
first in a series. This name choice, meaning "one" in Italian, commemorates the launch of Arduino Software (IDE) 1.0. Initially introduced alongside version 1.0 of the Arduino Software (IDE), the Uno has since become the foundational model for subsequent Arduino releases, embodying the platform's evolution.
Microcontroller Overview
MCU Card / MCU
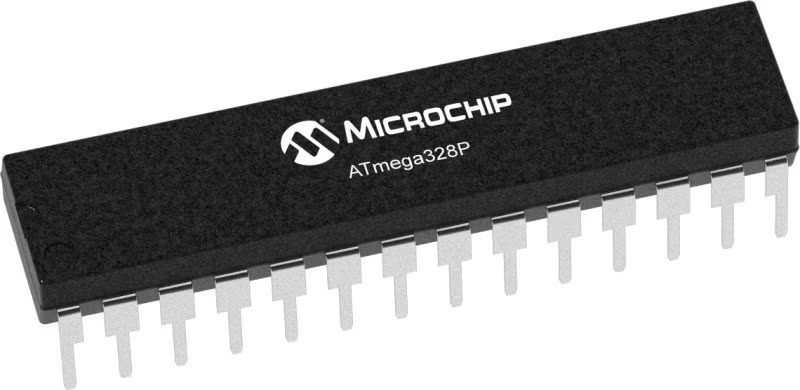
Architecture
AVR
MCU Memory (KB)
32
Silicon Vendor
Microchip
Pin count
28
RAM (Bytes)
2048
You complete me!
Accessories
Click Shield for Arduino UNO has two proprietary mikroBUS™ sockets, allowing all the Click board™ devices to be interfaced with the Arduino UNO board without effort. The Arduino Uno, a microcontroller board based on the ATmega328P, provides an affordable and flexible way for users to try out new concepts and build prototypes with the ATmega328P microcontroller from various combinations of performance, power consumption, and features. The Arduino Uno has 14 digital input/output pins (of which six can be used as PWM outputs), six analog inputs, a 16 MHz ceramic resonator (CSTCE16M0V53-R0), a USB connection, a power jack, an ICSP header, and reset button. Most of the ATmega328P microcontroller pins are brought to the IO pins on the left and right edge of the board, which are then connected to two existing mikroBUS™ sockets. This Click Shield also has several switches that perform functions such as selecting the logic levels of analog signals on mikroBUS™ sockets and selecting logic voltage levels of the mikroBUS™ sockets themselves. Besides, the user is offered the possibility of using any Click board™ with the help of existing bidirectional level-shifting voltage translators, regardless of whether the Click board™ operates at a 3.3V or 5V logic voltage level. Once you connect the Arduino UNO board with our Click Shield for Arduino UNO, you can access hundreds of Click boards™, working with 3.3V or 5V logic voltage levels.
The 28BYJ-48 is an adaptable 5VDC stepper motor with a compact design, ideal for various applications. It features four phases, a speed variation ratio of 1/64, and a stride angle of 5.625°/64 steps, allowing precise control. The motor operates at a frequency of 100Hz and has a DC resistance of 50Ω ±7% at 25°C. It boasts an idle in-traction frequency greater than 600Hz and an idle out-traction frequency exceeding 1000Hz, ensuring reliability in different scenarios. With a self-positioning torque and in-traction torque both exceeding 34.3mN.m at 120Hz, the 28BYJ-48 offers robust performance. Its friction torque ranges from 600 to 1200 gf.cm, while the pull-in torque is 300 gf.cm. This motor makes a reliable and efficient choice for your stepper motor needs.
Used MCU Pins
mikroBUS™ mapper
Take a closer look
Click board™ Schematic
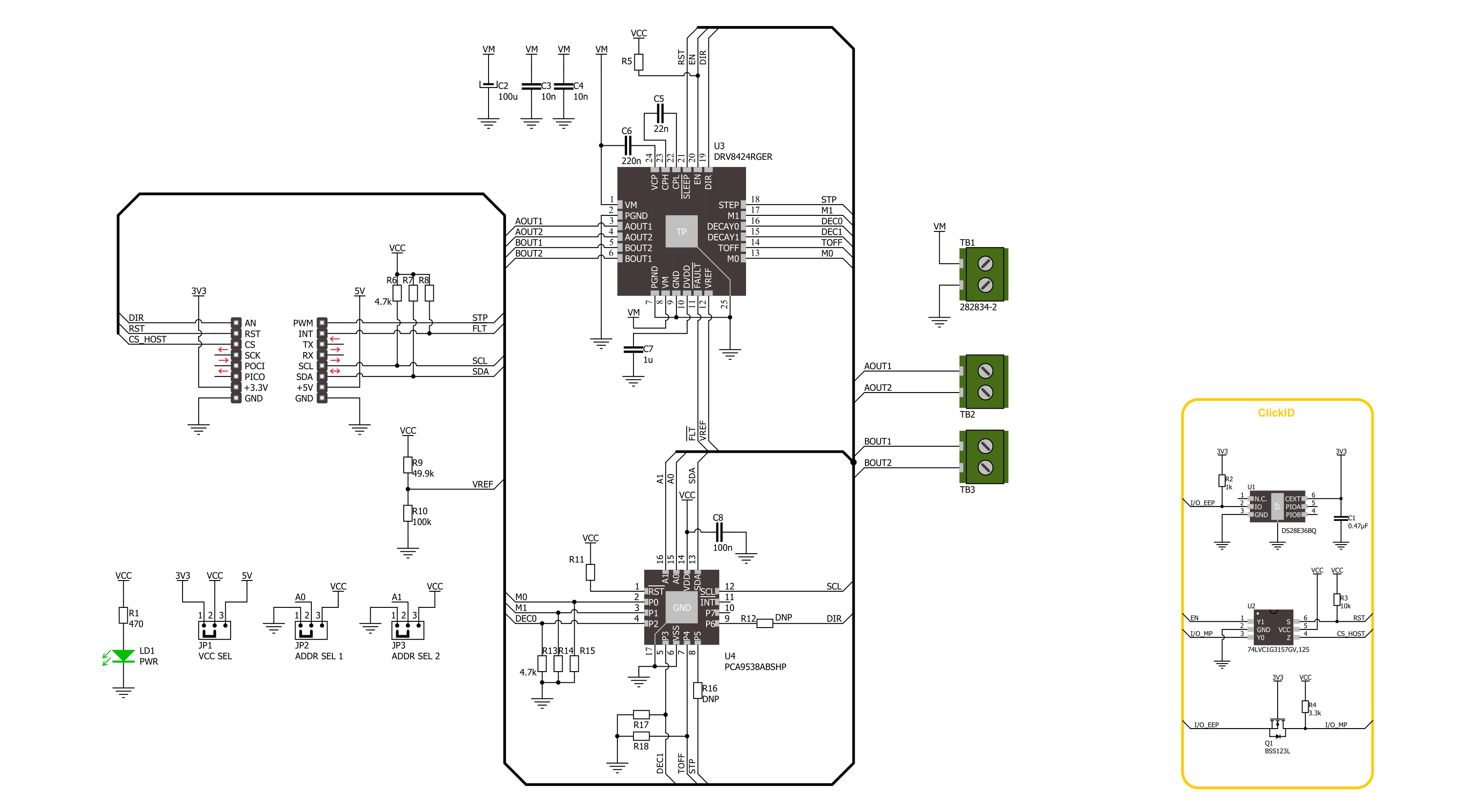
Step by step
Project assembly
Track your results in real time
Application Output
1. Application Output - In Debug mode, the 'Application Output' window enables real-time data monitoring, offering direct insight into execution results. Ensure proper data display by configuring the environment correctly using the provided tutorial.
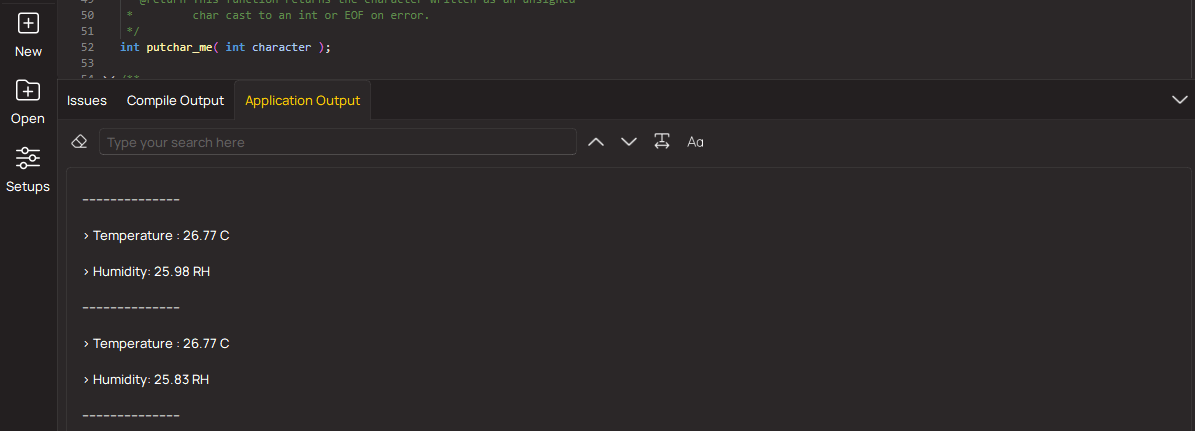
2. UART Terminal - Use the UART Terminal to monitor data transmission via a USB to UART converter, allowing direct communication between the Click board™ and your development system. Configure the baud rate and other serial settings according to your project's requirements to ensure proper functionality. For step-by-step setup instructions, refer to the provided tutorial.
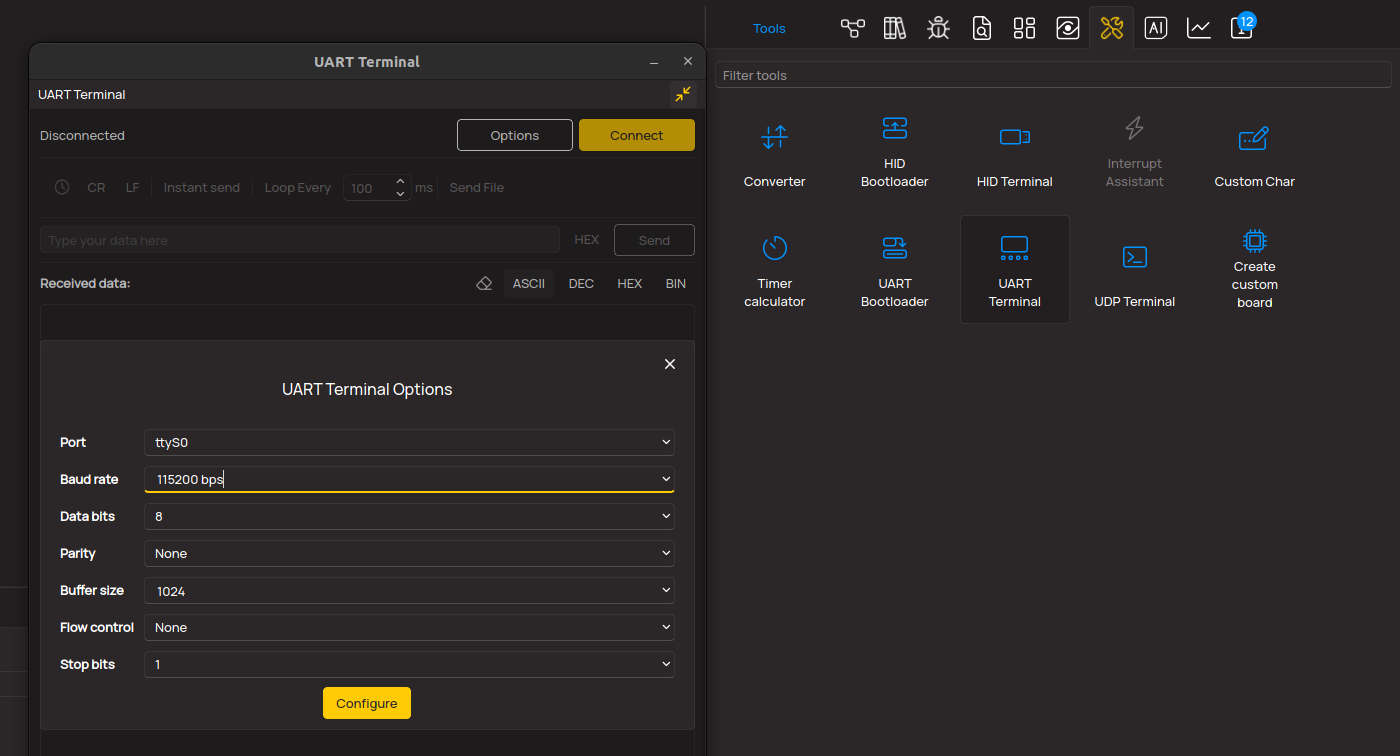
3. Plot Output - The Plot feature offers a powerful way to visualize real-time sensor data, enabling trend analysis, debugging, and comparison of multiple data points. To set it up correctly, follow the provided tutorial, which includes a step-by-step example of using the Plot feature to display Click board™ readings. To use the Plot feature in your code, use the function: plot(*insert_graph_name*, variable_name);. This is a general format, and it is up to the user to replace 'insert_graph_name' with the actual graph name and 'variable_name' with the parameter to be displayed.
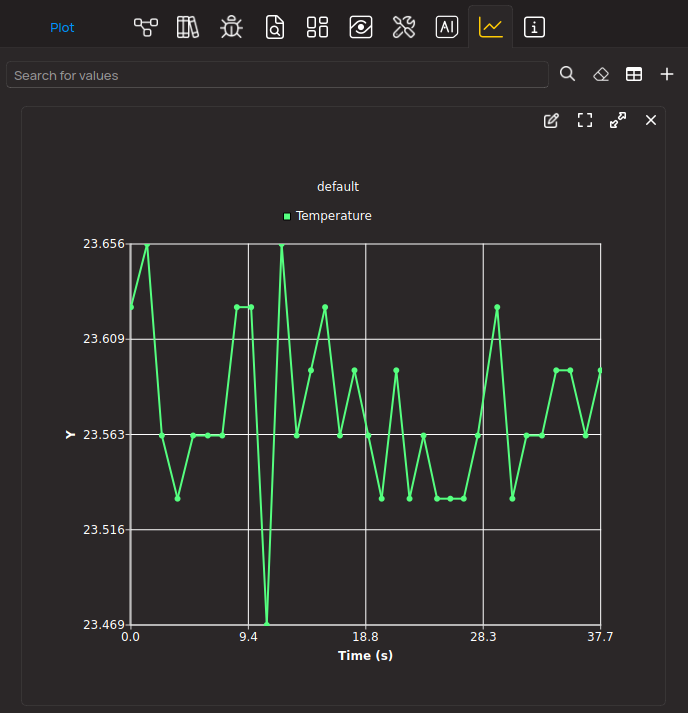
Software Support
Library Description
This library contains API for Stepper 19 Click driver.
Key functions:
stepper19_rotate_by_angle
- This function rotates the shaft through a desired step speed and anglestepper19_rotate_by_step
- This function rotates the shaft through for the specific number of steps at the selected speedstepper19_set_direction
- This function sets the desired direction of motor movement: clockwise or counterclockwise
Open Source
Code example
The complete application code and a ready-to-use project are available through the NECTO Studio Package Manager for direct installation in the NECTO Studio. The application code can also be found on the MIKROE GitHub account.
/*!
* @file main.c
* @brief Stepper 19 Click example
*
* # Description
* This example demonstrates the use of Stepper 19 Click board
* by driving the motor in both directions for a desired rotation angle.
*
* The demo application is composed of two sections :
*
* ## Application Init
* The initialization of I2C module and log UART.
* After driver initialization, the app sets the default configuration.
*
* ## Application Task
* The application task represents an example that demonstrates
* the use of the Stepper 19 Click board with which the user can sequentially move the motor.
* The first part of the sequence executes the clockwise/counterclockwise motor movement
* for an angle of 90 degrees with a step speed of 50%,
* all the way to the last sequence of the same movement routine
* of 360 degree angle with a step speed of 90%.
* Results are being sent to the UART Terminal, where you can track their changes.
*
* @author Nenad Filipovic
*
*/
#include "board.h"
#include "log.h"
#include "stepper19.h"
// Bipolar stepper motor, resolution of 200 steps per revolution (1.8 degrees)
#define STEPPER19_STEP_RES_200 200
static stepper19_t stepper19;
static log_t logger;
void application_init ( void )
{
log_cfg_t log_cfg; /**< Logger config object. */
stepper19_cfg_t stepper19_cfg; /**< Click config object. */
/**
* Logger initialization.
* Default baud rate: 115200
* Default log level: LOG_LEVEL_DEBUG
* @note If USB_UART_RX and USB_UART_TX
* are defined as HAL_PIN_NC, you will
* need to define them manually for log to work.
* See @b LOG_MAP_USB_UART macro definition for detailed explanation.
*/
LOG_MAP_USB_UART( log_cfg );
log_init( &logger, &log_cfg );
log_info( &logger, " Application Init " );
// Click initialization.
stepper19_cfg_setup( &stepper19_cfg );
STEPPER19_MAP_MIKROBUS( stepper19_cfg, MIKROBUS_1 );
if ( I2C_MASTER_ERROR == stepper19_init( &stepper19, &stepper19_cfg ) )
{
log_error( &logger, " Communication init." );
for ( ; ; );
}
if ( STEPPER19_ERROR == stepper19_default_cfg ( &stepper19 ) )
{
log_error( &logger, " Default configuration." );
for ( ; ; );
}
log_info( &logger, " Application Task " );
log_printf( &logger, "-----------------------------\r\n" );
}
void application_task ( void )
{
log_printf( &logger, " Clockwise motion\r\n" );
log_printf( &logger, " Angle of rotation : 90 degrees\r\n" );
log_printf( &logger, " Step speed : 50 %%\r\n" );
stepper19_set_direction( &stepper19, STEPPER19_DIR_CLOCKWISE );
if ( STEPPER19_OK == stepper19_rotate_by_angle( &stepper19, 50, 90, STEPPER19_STEP_RES_200 ) )
{
log_printf( &logger, "-----------------------------\r\n" );
Delay_ms( 2000 );
}
log_printf( &logger, " Counterclockwise motion\r\n" );
log_printf( &logger, " Angle of rotation : 180 deg\r\n" );
log_printf( &logger, " Step speed : 50 %%\r\n" );
stepper19_set_direction( &stepper19, STEPPER19_DIR_COUNTERCLOCKWISE );
if ( STEPPER19_OK == stepper19_rotate_by_angle( &stepper19, 50, 180, STEPPER19_STEP_RES_200 ) )
{
log_printf( &logger, "-----------------------------\r\n" );
Delay_ms( 2000 );
}
log_printf( &logger, " Clockwise motion\r\n" );
log_printf( &logger, " Angle of rotation : 270 deg\r\n" );
log_printf( &logger, " Step speed : 90 %% \r\n" );
stepper19_set_direction( &stepper19, STEPPER19_DIR_CLOCKWISE );
if ( STEPPER19_OK == stepper19_rotate_by_angle( &stepper19, 90, 270, STEPPER19_STEP_RES_200 ) )
{
log_printf( &logger, "-----------------------------\r\n" );
Delay_ms( 2000 );
}
log_printf( &logger, " Counterclockwise motion\r\n" );
log_printf( &logger, " Angle of rotation : 360 deg\r\n" );
log_printf( &logger, " Step speed : 90 %%\r\n" );
stepper19_set_direction( &stepper19, STEPPER19_DIR_COUNTERCLOCKWISE );
if ( STEPPER19_OK == stepper19_rotate_by_angle( &stepper19, 90, 360, STEPPER19_STEP_RES_200 ) )
{
log_printf( &logger, "-----------------------------\r\n" );
Delay_ms( 2000 );
}
log_printf( &logger, " Clockwise motion\r\n" );
log_printf( &logger, " Angle of rotation : 360 deg\r\n" );
log_printf( &logger, " Step speed : 90 %% \r\n" );
stepper19_set_direction( &stepper19, STEPPER19_DIR_CLOCKWISE );
if ( STEPPER19_OK == stepper19_rotate_by_angle( &stepper19, 90, 360, STEPPER19_STEP_RES_200 ) )
{
log_printf( &logger, "-----------------------------\r\n" );
Delay_ms( 2000 );
}
}
void main ( void )
{
application_init( );
for ( ; ; )
{
application_task( );
}
}
// ------------------------------------------------------------------------ END
Additional Support
Resources
Category:Stepper