Amplify your data storage prowess through our state-of-the-art solution, showcasing dual EEPROM memory with an impressive 4Mb capacity
A
A
Hardware Overview
How does it work?
Dual EE Click is based on two AT24CM02, an I2C serial EEPROM from Microchip. This means the ICs can have a different I2C address so that users can choose which one they would like to use at a particular time. This is achieved by wiring the I2C address selection lines from one of the ICs to the VCC while the other IC is wired to the GND. Given this feature, it is important to note that this click board has 4MB of memory. This Click board™ uses the I2C communication protocol. Therefore, the host MCU initiates every data transaction event, transmitting the I2C START condition, followed by the AT24CM02 device ID byte. Upon receiving the device ID byte, the AT24CM02 IC expects two more address bytes, completing the 18-bit address word. The EEPROM density is usually expressed in bits, so exactly 2.097.152 bits are organized in units or words of 8 bits, which gives 262.144 bytes of data memory. Furthermore, the EEPROM is
organized into so-called pages. One page holds 256 bytes, and there are 1024 pages (1024 pages x 256 bytes = 262.144 bytes total). Given that this click contains two EEPROM Ics, this Click board™ has twice as much memory, equaling 4 MB. Having insight into how the memory cells are organized is important for Write and Erase operations. The I2C pins are routed to the mikroBUS™, making communication easy and straightforward. Both 100KHz and 400KHz transfer speeds are supported by the AT24CM02 IC and the 1MHz Fast Mode Plus (FM+) I2C communication for the MCUs with I2C modules that can support that speed. One of the key features of the AT24CM02 IC is the Error Detection and Correction scheme (EDC), which allows error correction by utilizing six additional bits internally assigned to a group of four bytes. This protection scheme can correct some bit errors, staying transparent to the end
user. The bit comparison and error correction are done internally. The Dual EE Click board™ offers a selection between 3.3V and 5V operation, with the onboard SMD jumper labeled PWR SEL. This allows both 3.3V and 5V MCUs to be interfaced with this Click board™. The attached device datasheet contains an in-depth explanation of all the mentioned functions. However, Mikroe provides a library with functions that make the final code clean and readable, simplifying working with this device. These functions internally employ the aforementioned communication mechanism and expose only a simple and clean interface to the user. The provided example code demonstrates the functionality of these functions. It can be used as a reference point for custom development.
Features overview
Development board
Arduino UNO is a versatile microcontroller board built around the ATmega328P chip. It offers extensive connectivity options for various projects, featuring 14 digital input/output pins, six of which are PWM-capable, along with six analog inputs. Its core components include a 16MHz ceramic resonator, a USB connection, a power jack, an
ICSP header, and a reset button, providing everything necessary to power and program the board. The Uno is ready to go, whether connected to a computer via USB or powered by an AC-to-DC adapter or battery. As the first USB Arduino board, it serves as the benchmark for the Arduino platform, with "Uno" symbolizing its status as the
first in a series. This name choice, meaning "one" in Italian, commemorates the launch of Arduino Software (IDE) 1.0. Initially introduced alongside version 1.0 of the Arduino Software (IDE), the Uno has since become the foundational model for subsequent Arduino releases, embodying the platform's evolution.
Microcontroller Overview
MCU Card / MCU
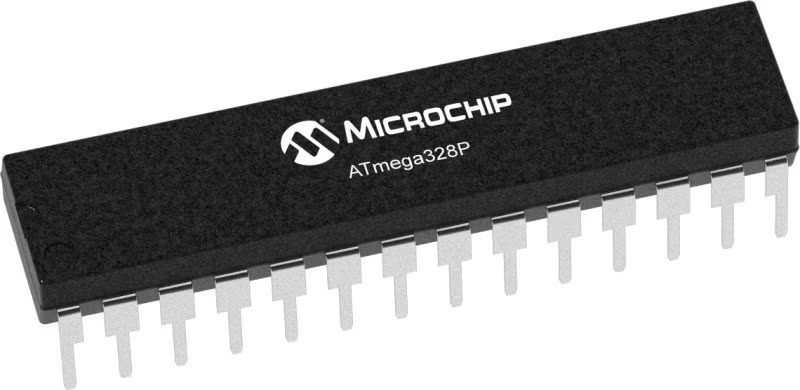
Architecture
AVR
MCU Memory (KB)
32
Silicon Vendor
Microchip
Pin count
28
RAM (Bytes)
2048
You complete me!
Accessories
Click Shield for Arduino UNO has two proprietary mikroBUS™ sockets, allowing all the Click board™ devices to be interfaced with the Arduino UNO board without effort. The Arduino Uno, a microcontroller board based on the ATmega328P, provides an affordable and flexible way for users to try out new concepts and build prototypes with the ATmega328P microcontroller from various combinations of performance, power consumption, and features. The Arduino Uno has 14 digital input/output pins (of which six can be used as PWM outputs), six analog inputs, a 16 MHz ceramic resonator (CSTCE16M0V53-R0), a USB connection, a power jack, an ICSP header, and reset button. Most of the ATmega328P microcontroller pins are brought to the IO pins on the left and right edge of the board, which are then connected to two existing mikroBUS™ sockets. This Click Shield also has several switches that perform functions such as selecting the logic levels of analog signals on mikroBUS™ sockets and selecting logic voltage levels of the mikroBUS™ sockets themselves. Besides, the user is offered the possibility of using any Click board™ with the help of existing bidirectional level-shifting voltage translators, regardless of whether the Click board™ operates at a 3.3V or 5V logic voltage level. Once you connect the Arduino UNO board with our Click Shield for Arduino UNO, you can access hundreds of Click boards™, working with 3.3V or 5V logic voltage levels.
Used MCU Pins
mikroBUS™ mapper
Take a closer look
Click board™ Schematic
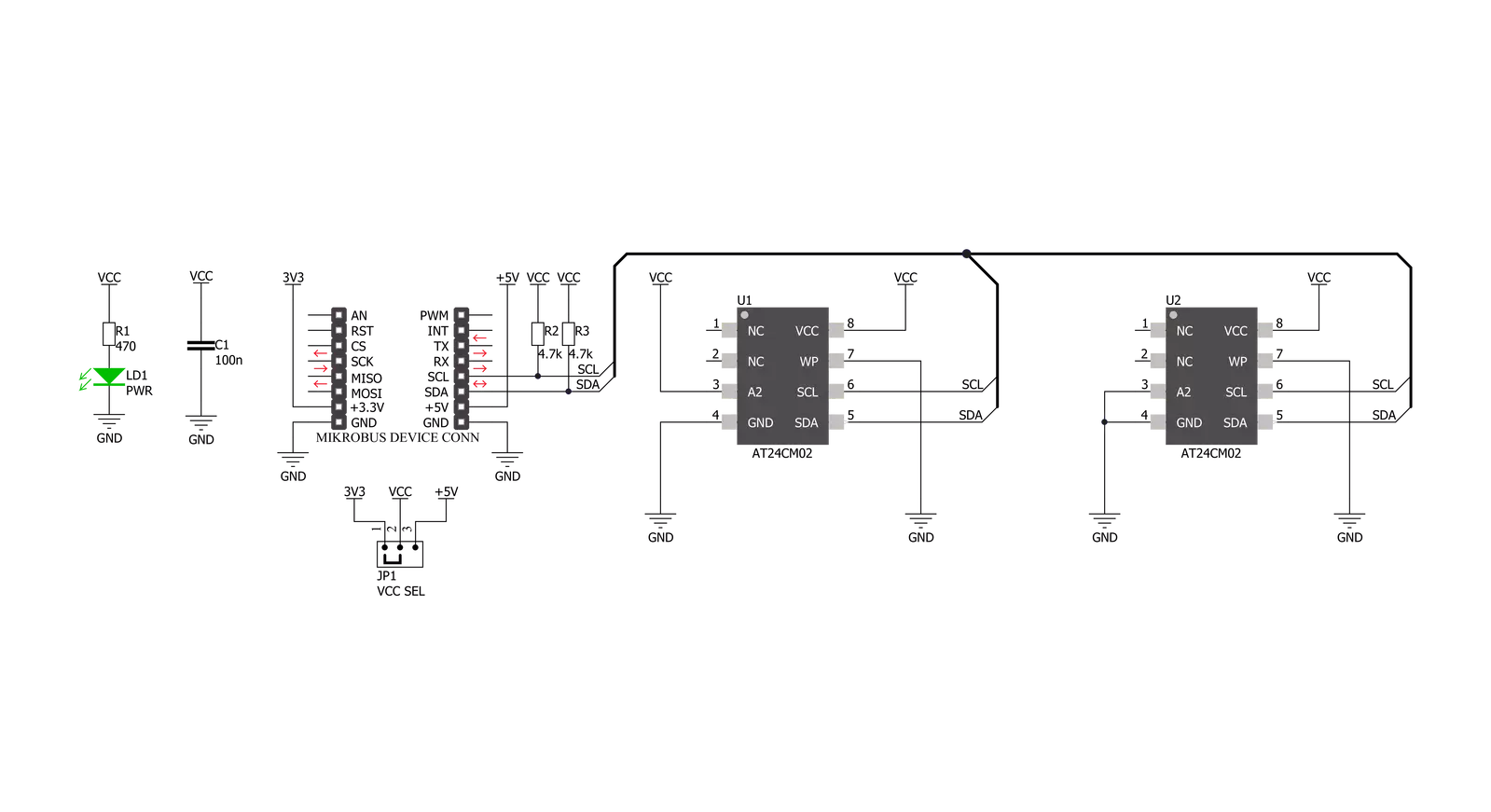
Step by step
Project assembly
Track your results in real time
Application Output
1. Application Output - In Debug mode, the 'Application Output' window enables real-time data monitoring, offering direct insight into execution results. Ensure proper data display by configuring the environment correctly using the provided tutorial.
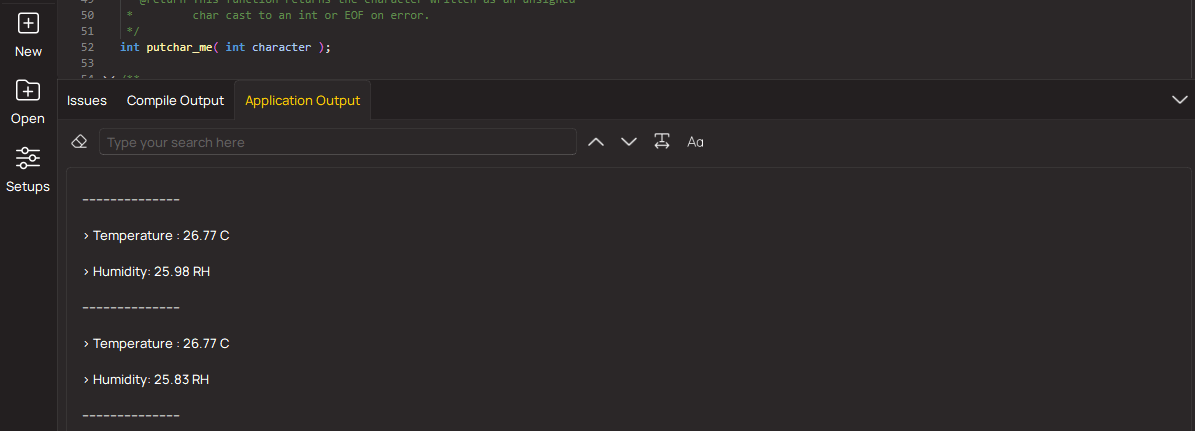
2. UART Terminal - Use the UART Terminal to monitor data transmission via a USB to UART converter, allowing direct communication between the Click board™ and your development system. Configure the baud rate and other serial settings according to your project's requirements to ensure proper functionality. For step-by-step setup instructions, refer to the provided tutorial.
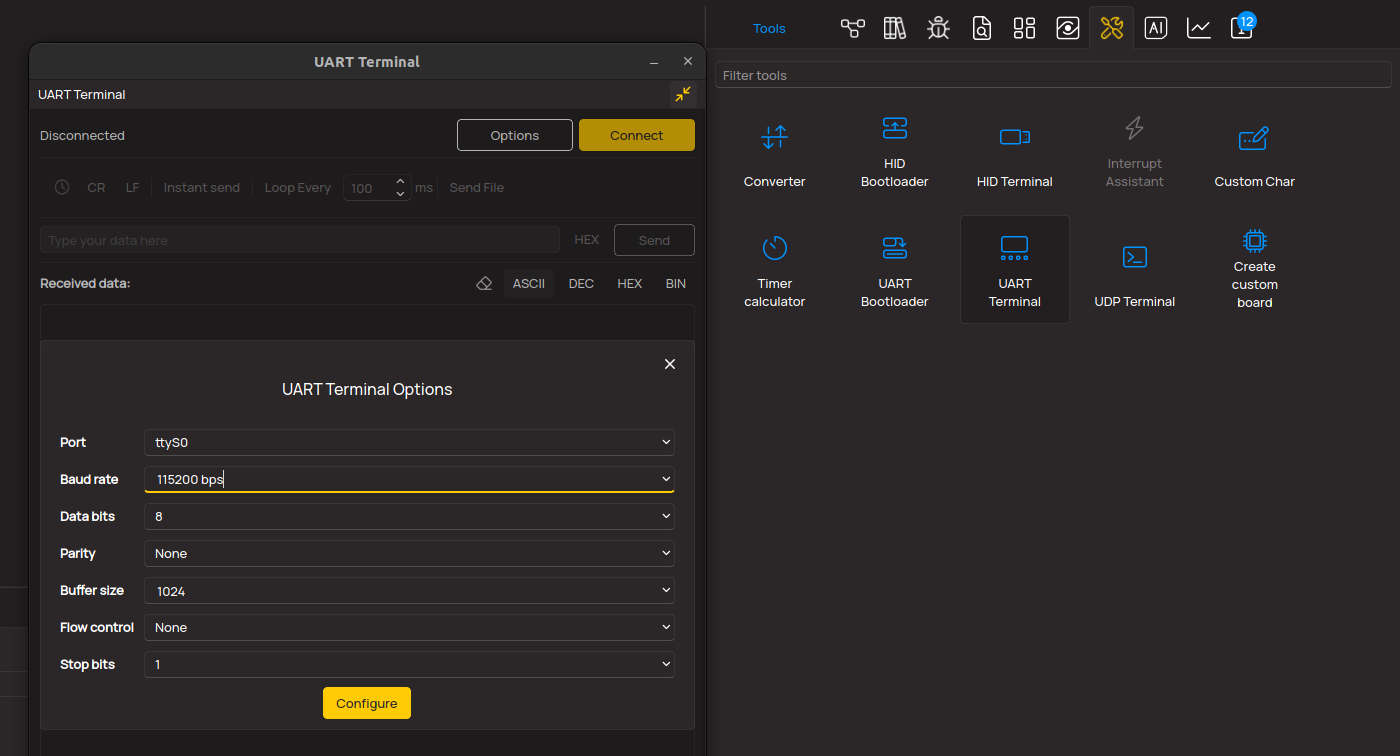
3. Plot Output - The Plot feature offers a powerful way to visualize real-time sensor data, enabling trend analysis, debugging, and comparison of multiple data points. To set it up correctly, follow the provided tutorial, which includes a step-by-step example of using the Plot feature to display Click board™ readings. To use the Plot feature in your code, use the function: plot(*insert_graph_name*, variable_name);. This is a general format, and it is up to the user to replace 'insert_graph_name' with the actual graph name and 'variable_name' with the parameter to be displayed.
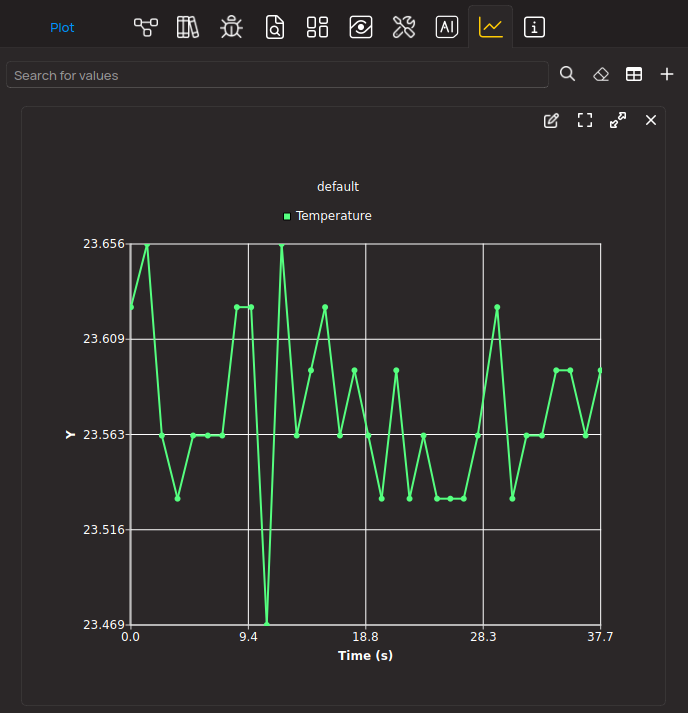
Software Support
Library Description
This library contains API for Dual EE Click driver.
Key functions:
dualee_read
- Generic write data functiondualee_write
- Generic write data function
Open Source
Code example
The complete application code and a ready-to-use project are available through the NECTO Studio Package Manager for direct installation in the NECTO Studio. The application code can also be found on the MIKROE GitHub account.
/*!
* \file
* \brief DualEE Click example
*
* # Description
* This application writes data in memory and reads data from memory
*
* The demo application is composed of two sections :
*
* ## Application Init
* Initializes device init
*
* ## Application Task
* Reads your command and then execute it
*
* \author MikroE Team
*
*/
// ------------------------------------------------------------------- INCLUDES
#include "board.h"
#include "log.h"
#include "dualee.h"
// ------------------------------------------------------------------ VARIABLES
static dualee_t dualee;
static log_t logger;
static uint32_t page_address = 0x00000000;
static uint8_t write_data[ 7 ] = { 'M', 'i', 'k', 'r', 'o', 'E', 0 };
// ------------------------------------------------------ APPLICATION FUNCTIONS
void application_init ( void )
{
log_cfg_t log_cfg;
dualee_cfg_t cfg;
/**
* Logger initialization.
* Default baud rate: 115200
* Default log level: LOG_LEVEL_DEBUG
* @note If USB_UART_RX and USB_UART_TX
* are defined as HAL_PIN_NC, you will
* need to define them manually for log to work.
* See @b LOG_MAP_USB_UART macro definition for detailed explanation.
*/
LOG_MAP_USB_UART( log_cfg );
log_init( &logger, &log_cfg );
log_info( &logger, "---- Application Init ----" );
// Click initialization.
dualee_cfg_setup( &cfg );
DUALEE_MAP_MIKROBUS( cfg, MIKROBUS_1 );
dualee_init( &dualee, &cfg );
log_printf( &logger, "*********** APPLICATION INIT ***********\r\n" );
Delay_ms ( 100 );
}
void application_task ( )
{
uint8_t write_dual;
uint8_t read_dual;
char demo_text[ 255 ];
log_printf( &logger, "Writing data [MikroE]....\r\n" );
write_dual = dualee_write( &dualee, page_address, write_data, 7 );
if ( write_dual == DUALEE_ERROR_RW )
{
log_printf( &logger, "Error writing data!!!\r\n" );
Delay_ms ( 1000 );
return;
}
Delay_ms ( 100 );
log_printf( &logger, "Reading data...\r\n" );
read_dual = dualee_read( &dualee, page_address, demo_text, 7 );
if ( read_dual == 0 )
{
log_printf( &logger, "Error reading data!!!\r\n" );
Delay_ms ( 1000 );
return;
}
Delay_ms ( 100 );
log_printf( &logger, "Data from read page is: %s \r\n", demo_text );
log_printf( &logger, "__________________________________\r\n" );
Delay_ms ( 1000 );
}
int main ( void )
{
/* Do not remove this line or clock might not be set correctly. */
#ifdef PREINIT_SUPPORTED
preinit();
#endif
application_init( );
for ( ; ; )
{
application_task( );
}
return 0;
}
// ------------------------------------------------------------------------ END
Additional Support
Resources
Category:EEPROM