Discover a solution that guarantees data retention for extended periods, offering peace of mind in critical scenarios and safeguarding valuable information against unforeseen events
A
A
Hardware Overview
How does it work?
EEPROM 4 Click is based on the AT25M02, an SPI serial EEPROM from Microchip, with a memory cell density of 2 Mbits. The EEPROM density is usually expressed in bits, so exactly 2,097,152 bits are organized in units or words of 8 bits, which gives 262,144 bytes of data memory. Furthermore, the EEPROM is organized into so-called pages. One page holds 256 bytes, and there are 1024 pages (1024 pages x 256 bytes = 262,144 bytes total). Having insight into how the memory cells are organized is important for write and erase operations. The SPI pins are routed to the mikroBUS™, making communication easy and straightforward. The SPI can be clocked as high as 5MHz, providing a fast throughput for the data transfer. A dedicated #HOLD pin is routed to the PWM pin of the mikroBUS™. When the communication with the click board™ is initiated by setting the CS pin to a LOW logic state, it is possible to pause the serial data transfer without
resetting the communication if the #HOLD pin (PWM pin on the mikroBUS™) is set to a LOW logic state. To resume the communication, setting this pin to a HIGH logic state while the SCK is still running is enough. Once the HOLD is initiated, the state of the SCK line is irrelevant, and any serial data input will be ignored. This pin is pulled HIGH by the onboard resistor. A dedicated #WP write protect pin puts the device into the hardware write protect mode. This pin is routed to the RST pin of the mikroBUS™. Hardware write-protect works with the Write Protect Enable (WPEN) bit of the Status Register. When this bit is set to 1, and the #WP pin is set to a LOW logic state, the device will ignore any attempt to write to the Status Register and the EEPROM memory regions selected by the Block Write Protect bits of the Status Register (BP0 and BP1). WRSR instruction is used to write to the Status Register (01h). Again, WREN instruction should be executed first before
attempting to write to Status Register. Once the WPEN bit is set to 1 and the RST has been pulled to a LOW logic state, setting the WPEN bit to 0 won’t turn off write protection as long as the #WP pin (RST) stays LOW. WPEN bit and the BP0 and BP1 bits are constructed as EEPROM cells, meaning that they are nonvolatile and will retain their states even after power is off. The #WP pin is pulled HIGH by the onboard resistor. As usual, the onboard SMD jumper labeled as VCCSEL is used to select the operating voltage between 3.3V and 5V. However, there’s the third position for this jumper, which sets the operating voltage to 1.8V. This is achieved thanks to the TC1015, a small 100 mA LDO from Microchip powered by the 5V rail. As always, MikroElektronika provides libraries that simplify and speed up working with this device. The provided application example demonstrates the functionality of the provided libraries and can be used as a reference point for own development.
Features overview
Development board
Flip&Click PIC32MZ is a compact development board designed as a complete solution that brings the flexibility of add-on Click boards™ to your favorite microcontroller, making it a perfect starter kit for implementing your ideas. It comes with an onboard 32-bit PIC32MZ microcontroller, the PIC32MZ2048EFH100 from Microchip, four mikroBUS™ sockets for Click board™ connectivity, two USB connectors, LED indicators, buttons, debugger/programmer connectors, and two headers compatible with Arduino-UNO pinout. Thanks to innovative manufacturing technology,
it allows you to build gadgets with unique functionalities and features quickly. Each part of the Flip&Click PIC32MZ development kit contains the components necessary for the most efficient operation of the same board. In addition, there is the possibility of choosing the Flip&Click PIC32MZ programming method, using the chipKIT bootloader (Arduino-style development environment) or our USB HID bootloader using mikroC, mikroBasic, and mikroPascal for PIC32. This kit includes a clean and regulated power supply block through the USB Type-C (USB-C) connector. All communication
methods that mikroBUS™ itself supports are on this board, including the well-established mikroBUS™ socket, user-configurable buttons, and LED indicators. Flip&Click PIC32MZ development kit allows you to create a new application in minutes. Natively supported by Mikroe software tools, it covers many aspects of prototyping thanks to a considerable number of different Click boards™ (over a thousand boards), the number of which is growing every day.
Microcontroller Overview
MCU Card / MCU

Architecture
PIC32
MCU Memory (KB)
2048
Silicon Vendor
Microchip
Pin count
100
RAM (Bytes)
524288
Used MCU Pins
mikroBUS™ mapper
Take a closer look
Click board™ Schematic
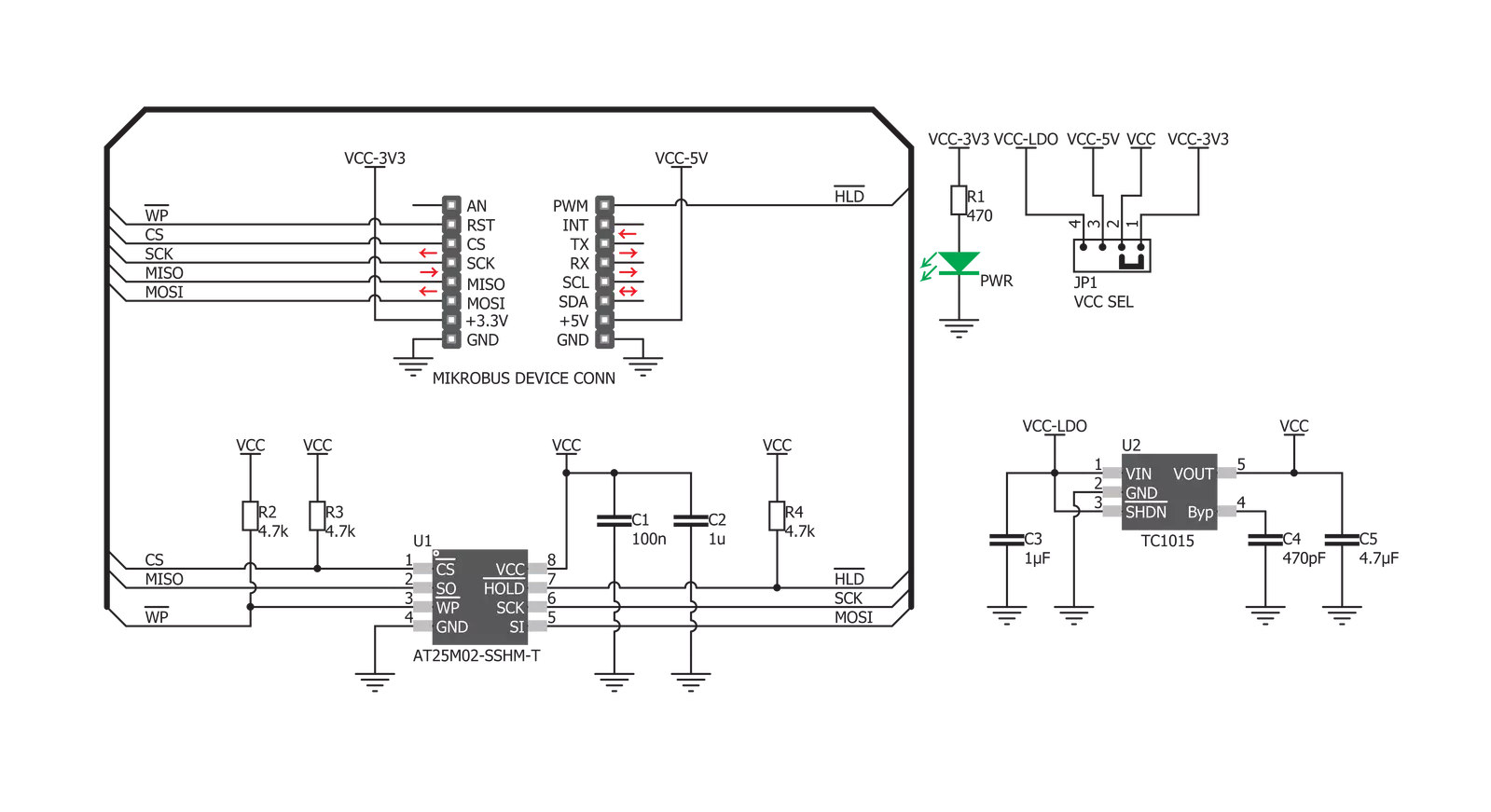
Step by step
Project assembly
Track your results in real time
Application Output
1. Application Output - In Debug mode, the 'Application Output' window enables real-time data monitoring, offering direct insight into execution results. Ensure proper data display by configuring the environment correctly using the provided tutorial.
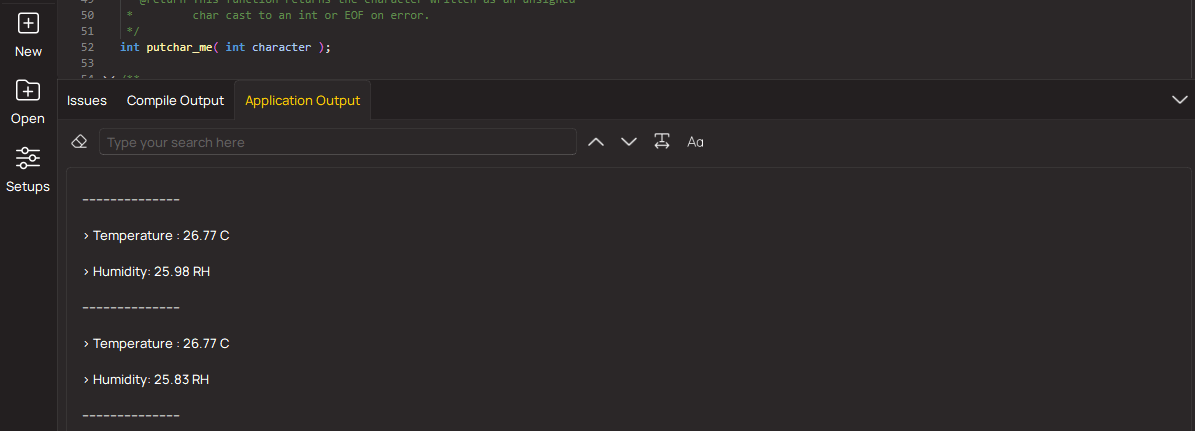
2. UART Terminal - Use the UART Terminal to monitor data transmission via a USB to UART converter, allowing direct communication between the Click board™ and your development system. Configure the baud rate and other serial settings according to your project's requirements to ensure proper functionality. For step-by-step setup instructions, refer to the provided tutorial.
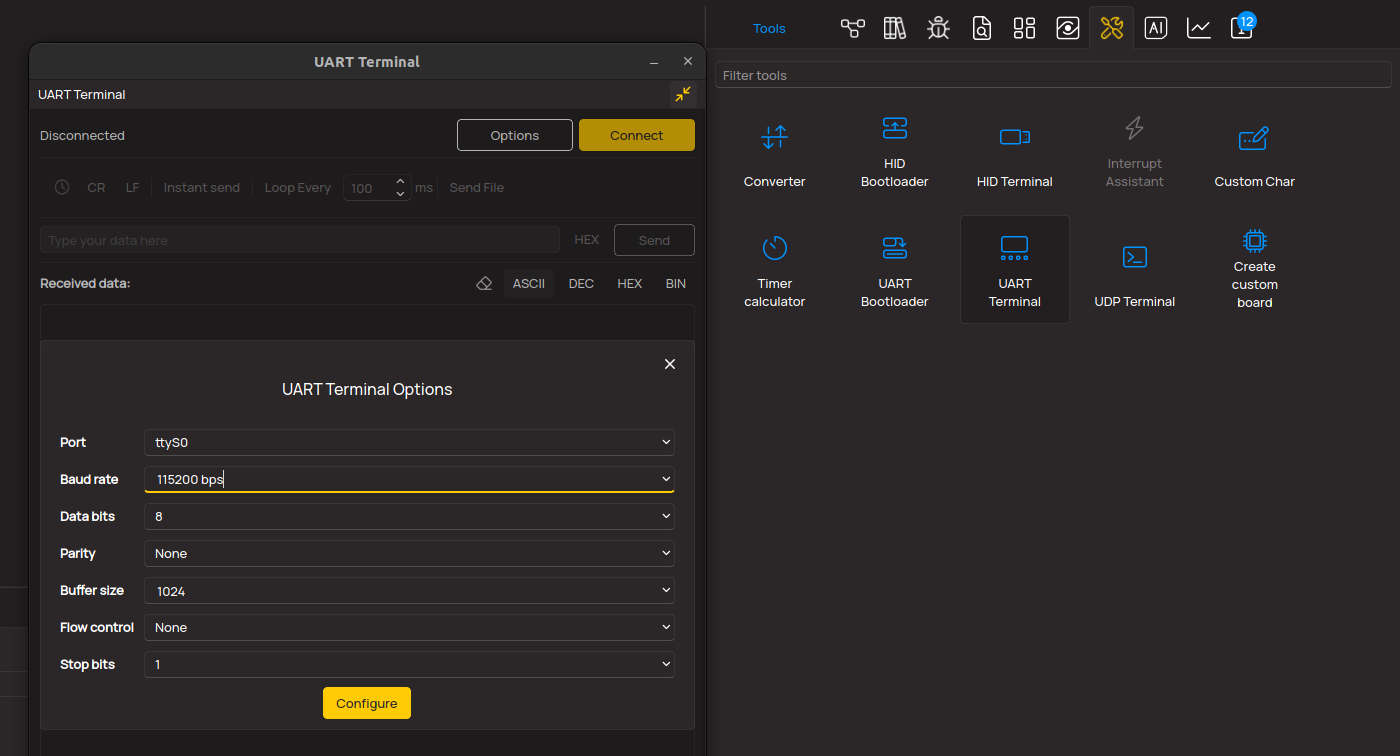
3. Plot Output - The Plot feature offers a powerful way to visualize real-time sensor data, enabling trend analysis, debugging, and comparison of multiple data points. To set it up correctly, follow the provided tutorial, which includes a step-by-step example of using the Plot feature to display Click board™ readings. To use the Plot feature in your code, use the function: plot(*insert_graph_name*, variable_name);. This is a general format, and it is up to the user to replace 'insert_graph_name' with the actual graph name and 'variable_name' with the parameter to be displayed.
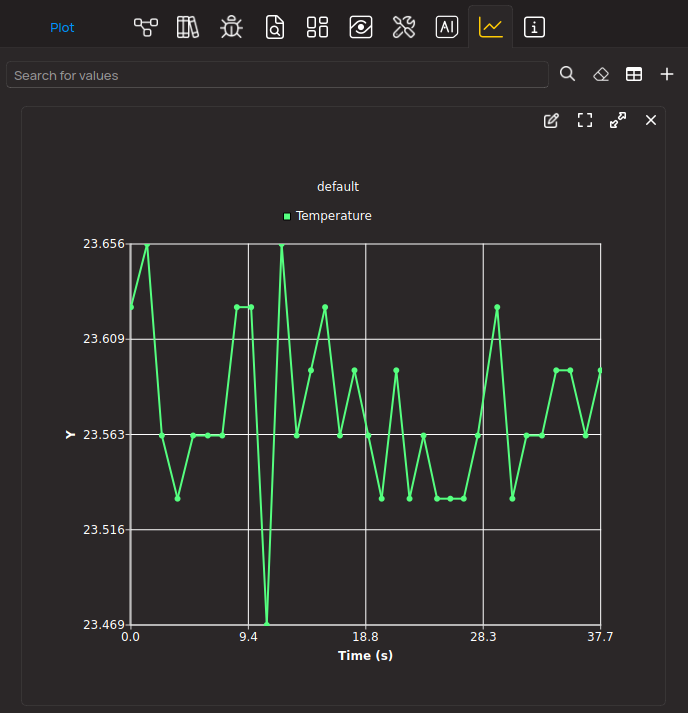
Software Support
Library Description
This library contains API for EEPROM 4 Click driver.
Key functions:
eeprom4_write_status_reg
- Status register write functioneeprom4_write_memory
- Memory array write functioneeprom4_read_memory
- Memory array read function
Open Source
Code example
The complete application code and a ready-to-use project are available through the NECTO Studio Package Manager for direct installation in the NECTO Studio. The application code can also be found on the MIKROE GitHub account.
/*!
* \file
* \brief Eeprom4 Click example
*
* # Description
* This Click reads and writes memory.
*
* The demo application is composed of two sections :
*
* ## Application Init
* Initializes Click driver and configures Click that all memory block > is unprotected.
* Also configures that HOLD operation is disabled, and the memory and > status register are writable.
*
* ## Application Task
* Enables writting to memory array, writes data from buffer to memory,
* checks if the part is in a write cycle, and if is not reads data > > from memory array and stores data to buffer.
* Storaged data shows on USB UART.
*
* \author MikroE Team
*
*/
// ------------------------------------------------------------------- INCLUDES
#include "board.h"
#include "log.h"
#include "eeprom4.h"
// ------------------------------------------------------------------ VARIABLES
static eeprom4_t eeprom4;
static log_t logger;
// ------------------------------------------------------ APPLICATION FUNCTIONS
void application_init ( void )
{
log_cfg_t log_cfg;
eeprom4_cfg_t cfg;
/**
* Logger initialization.
* Default baud rate: 115200
* Default log level: LOG_LEVEL_DEBUG
* @note If USB_UART_RX and USB_UART_TX
* are defined as HAL_PIN_NC, you will
* need to define them manually for log to work.
* See @b LOG_MAP_USB_UART macro definition for detailed explanation.
*/
LOG_MAP_USB_UART( log_cfg );
log_init( &logger, &log_cfg );
log_info( &logger, "---- Application Init ----" );
// Click initialization.
eeprom4_cfg_setup( &cfg );
EEPROM4_MAP_MIKROBUS( cfg, MIKROBUS_1 );
eeprom4_init( &eeprom4, &cfg );
eeprom4_default_cfg( &eeprom4 );
}
void application_task ( )
{
uint8_t data_write[ 13 ] = { 'M', 'i', 'K', 'r', 'O', 'e', 0 };
uint8_t data_read[ 255 ] = { 0 };
uint8_t cnt;
uint8_t check_state;
eeprom4_send_command( &eeprom4, EEPROM4_SET_WRITE_ENABLE_LATCH_COMMAND );
eeprom4_write_memory( &eeprom4, EEPROM4_FIRST_MEMORY_LOCATION, data_write, 6 );
cnt = eeprom4_check_status_reg( &eeprom4, EEPROM4_READY_BIT );
check_state = eeprom4_send_command( &eeprom4, EEPROM4_LOW_POWER_WRITE_POLL_COMMAND );
while ( cnt | check_state )
{
cnt = eeprom4_check_status_reg( &eeprom4, EEPROM4_READY_BIT );
check_state = eeprom4_send_command( &eeprom4, EEPROM4_LOW_POWER_WRITE_POLL_COMMAND );
}
eeprom4_read_memory( &eeprom4, 0x00000000, data_read, 6 );
for ( cnt = 0; cnt < 6; cnt++ )
{
log_printf( &logger, " %c ", data_read[cnt] );
}
log_printf( &logger, "----- \r\n" );
Delay_ms ( 1000 );
Delay_ms ( 1000 );
}
int main ( void )
{
/* Do not remove this line or clock might not be set correctly. */
#ifdef PREINIT_SUPPORTED
preinit();
#endif
application_init( );
for ( ; ; )
{
application_task( );
}
return 0;
}
// ------------------------------------------------------------------------ END