Experience the pinnacle of control and power with our cutting-edge solution used to drive a solenoid or DC brush motor
A
A
Hardware Overview
How does it work?
H-Bridge 5 Click is based on the MP6515, an H-bridge motor driver from Monolithic Power Systems (MPS). This Click board™ operates from a supply voltage of up to 30V and delivers a motor current of up to 1.5A. Its main applications include solenoid and DC brush motor driving. Its internal safety features include over-current protection, input over-voltage protection, undervoltage lockout (UVLO), and thermal shutdown. The MP6515 integrates four N-channel power MOSFETs with 2.8A peak current capability. It is designed to drive DC brush motors, solenoids, or other loads. Regarding current sensing, the current flowing in the two low-side MOSFETs is sensed with an internal current sensing circuit. A voltage that is proportional to the output
current is sourced on VISEN. Current is sensed when one of the low-side MOSFETs is turned on, including during slow decay (brake) mode. The load current applied to VISEN should be kept below 2mA, with no more than 500pF of capacitance. The H-Bridge 5 click also contains the PCA9538A, a low-voltage 8-bit General Purpose Input/Output (GPIO) expander from NXP with interrupt and reset for I2C-bus/SMBus applications. NXP I/O expander provides a simple solution when additional I/Os are needed while keeping interconnections to a minimum. Expanders provide communication between MP6515 and MCU, MCU control expander with I2C communication, and set output logic level for I/O pins. Data is exchanged
between the master and PCA9538A through write and read commands using I2C-bus. The two communication lines are a serial data line (SDA) and a serial clock line (SCL). Both lines must be connected to a positive supply via a pull-up resistor when connected to the output stages of a device. Data transfer may be initiated only when the bus is not busy. This Click board™ can operate with either 3.3V or 5V logic voltage levels selected via the VCC SEL jumper. This way, both 3.3V and 5V capable MCUs can use the communication lines properly. However, the Click board™ comes equipped with a library containing easy-to-use functions and an example code that can be used, as a reference, for further development.
Features overview
Development board
Arduino Mega 2560 is a robust microcontroller platform built around the ATmega 2560 chip. It has extensive capabilities and boasts 54 digital input/output pins, including 15 PWM outputs, 16 analog inputs, and 4 UARTs. With a 16MHz crystal
oscillator ensuring precise timing, it offers seamless connectivity via USB, a convenient power jack, an ICSP header, and a reset button. This all-inclusive board simplifies microcontroller projects; connect it to your computer via USB or power it up
using an AC-to-DC adapter or battery. Notably, the Mega 2560 maintains compatibility with a wide range of shields crafted for the Uno, Duemilanove, or Diecimila boards, ensuring versatility and ease of integration.
Microcontroller Overview
MCU Card / MCU
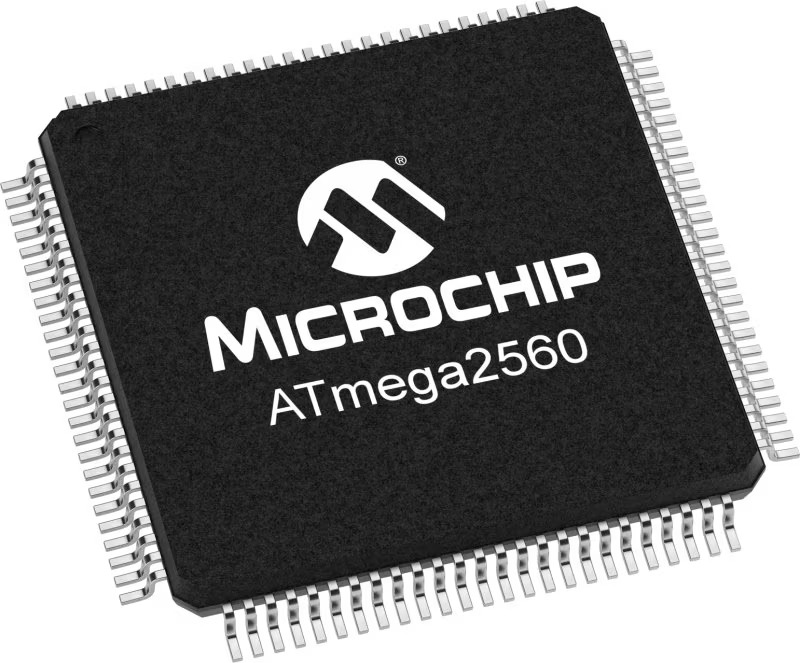
Architecture
AVR
MCU Memory (KB)
256
Silicon Vendor
Microchip
Pin count
100
RAM (Bytes)
8192
You complete me!
Accessories
Click Shield for Arduino Mega comes equipped with four mikroBUS™ sockets, with two in the form of a Shuttle connector, allowing all the Click board™ devices to be interfaced with the Arduino Mega board with no effort. Featuring an AVR 8-bit microcontroller with advanced RISC architecture, 54 digital I/O pins, and Arduino™ compatibility, the Arduino Mega board offers limitless possibilities for prototyping and creating diverse applications. This board is controlled and powered conveniently through a USB connection to program and debug the Arduino Mega board efficiently out of the box, with an additional USB cable connected to the USB B port on the board. Simplify your project development with the integrated ATmega16U2 programmer and unleash creativity using the extensive I/O options and expansion capabilities. There are eight switches, which you can use as inputs, and eight LEDs, which can be used as outputs of the MEGA2560. In addition, the shield features the MCP1501, a high-precision buffered voltage reference from Microchip. This reference is selected by default over the EXT REF jumper at the bottom of the board. You can choose an external one, as you would usually do with an Arduino Mega board. There is also a GND hook for testing purposes. Four additional LEDs are PWR, LED (standard pin D13), RX, and TX LEDs connected to UART1 (mikroBUS™ 1 socket). This Click Shield also has several switches that perform functions such as selecting the logic levels of analog signals on mikroBUS™ sockets and selecting logic voltage levels of the mikroBUS™ sockets themselves. Besides, the user is offered the possibility of using any Click board™ with the help of existing bidirectional level-shifting voltage translators, regardless of whether the Click board™ operates at a 3.3V or 5V logic voltage level. Once you connect the Arduino Mega board with Click Shield for Arduino Mega, you can access hundreds of Click boards™, working with 3.3V or 5V logic voltage levels.
DC Gear Motor - 430RPM (3-6V) represents an all-in-one combination of a motor and gearbox, where the addition of gear leads to a reduction of motor speed while increasing the torque output. This gear motor has a spur gearbox, making it a highly reliable solution for applications with lower torque and speed requirements. The most critical parameters for gear motors are speed, torque, and efficiency, which are, in this case, 520RPM with no load and 430RPM at maximum efficiency, alongside a current of 60mA and a torque of 50g.cm. Rated for a 3-6V operational voltage range and clockwise/counterclockwise rotation direction, this motor represents an excellent solution for many functions initially performed by brushed DC motors in robotics, medical equipment, electric door locks, and much more.
Used MCU Pins
mikroBUS™ mapper
Take a closer look
Click board™ Schematic
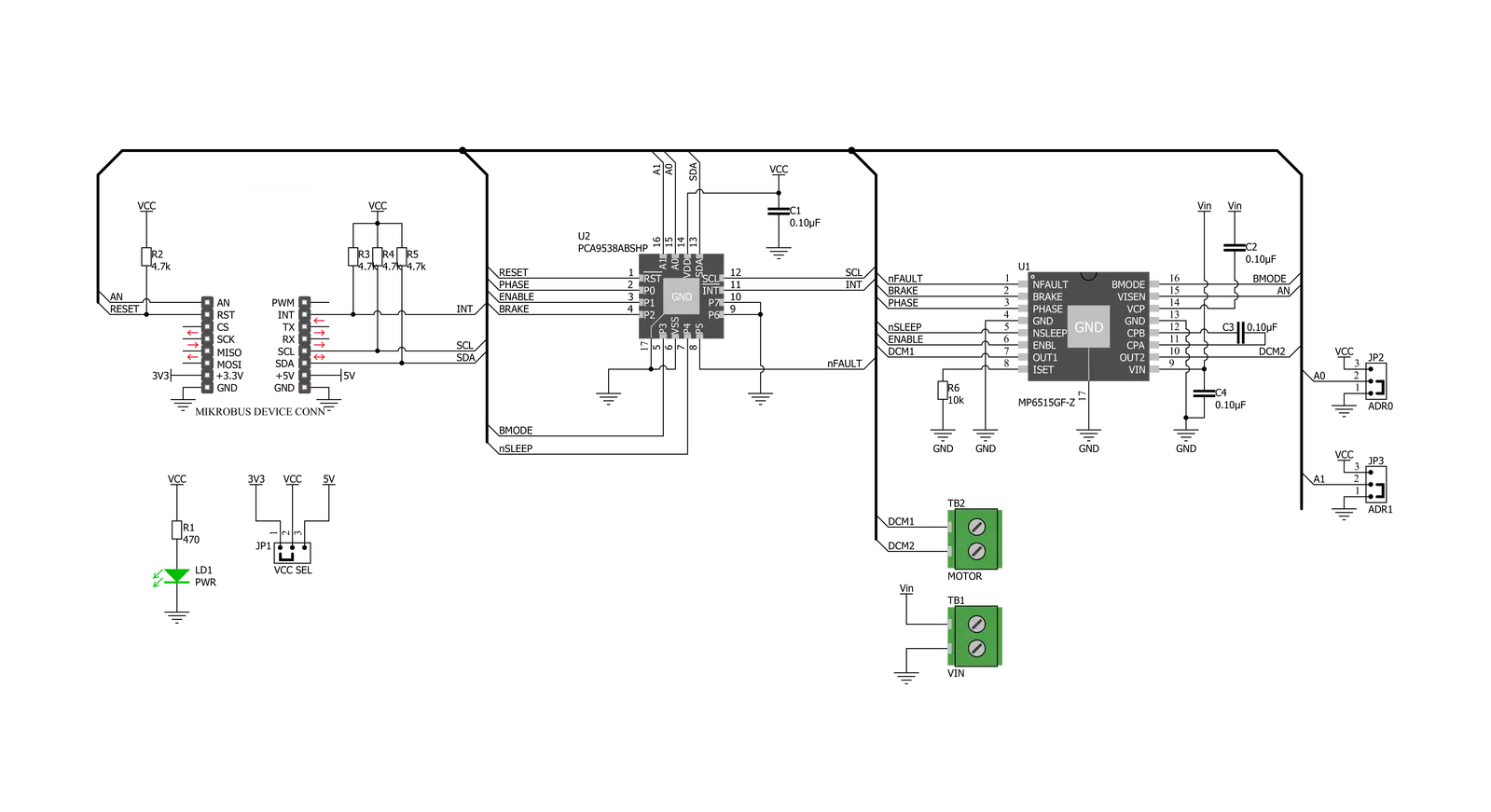
Step by step
Project assembly
Track your results in real time
Application Output
1. Application Output - In Debug mode, the 'Application Output' window enables real-time data monitoring, offering direct insight into execution results. Ensure proper data display by configuring the environment correctly using the provided tutorial.
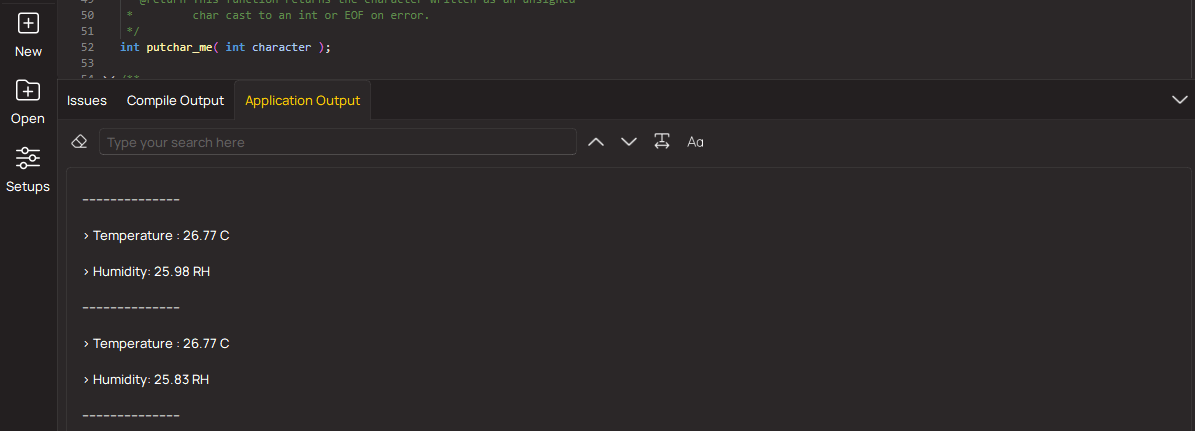
2. UART Terminal - Use the UART Terminal to monitor data transmission via a USB to UART converter, allowing direct communication between the Click board™ and your development system. Configure the baud rate and other serial settings according to your project's requirements to ensure proper functionality. For step-by-step setup instructions, refer to the provided tutorial.
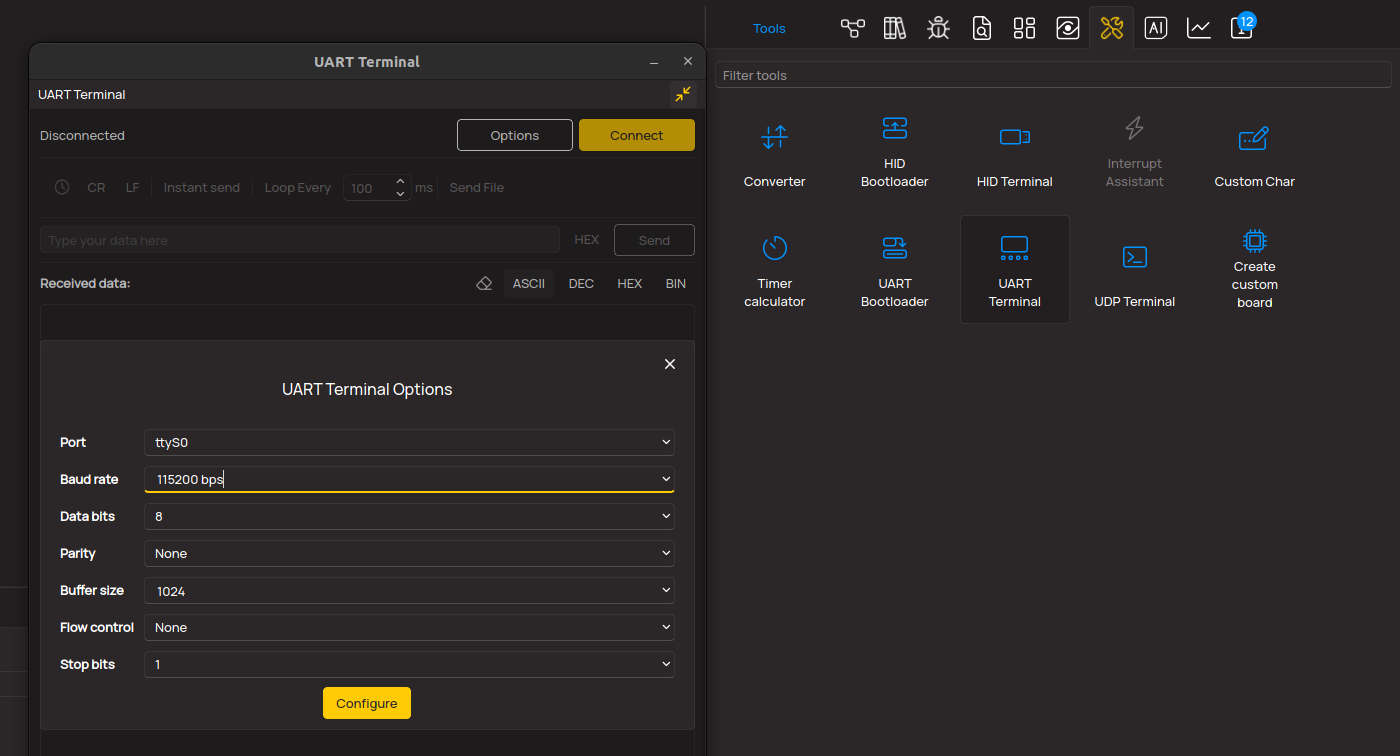
3. Plot Output - The Plot feature offers a powerful way to visualize real-time sensor data, enabling trend analysis, debugging, and comparison of multiple data points. To set it up correctly, follow the provided tutorial, which includes a step-by-step example of using the Plot feature to display Click board™ readings. To use the Plot feature in your code, use the function: plot(*insert_graph_name*, variable_name);. This is a general format, and it is up to the user to replace 'insert_graph_name' with the actual graph name and 'variable_name' with the parameter to be displayed.
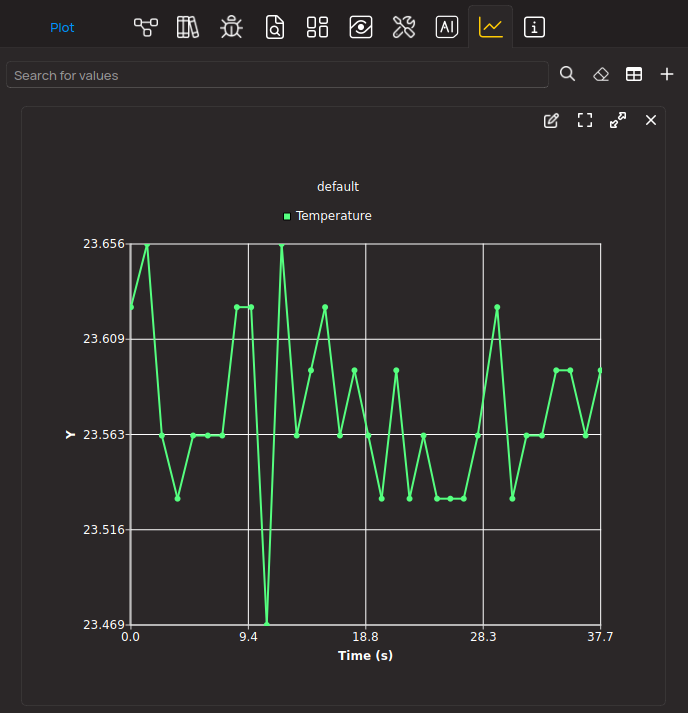
Software Support
Library Description
This library contains API for H-Bridge 5 Click driver.
Key functions:
hbridge5_set_port
- Function sets port.hbridge5_reverse
- Puts motor into reverse motion.hbridge5_foreward
- Puts motor into foreward motion.
Open Source
Code example
The complete application code and a ready-to-use project are available through the NECTO Studio Package Manager for direct installation in the NECTO Studio. The application code can also be found on the MIKROE GitHub account.
/*!
* \file
* \brief HBridge5 Click example
*
* # Description
* This application controls DC motors and inductive loads.
*
* The demo application is composed of two sections :
*
* ## Application Init
* Initalizes I2C driver, configures all ports as output and writes an initial log.
*
* ## Application Task
* This example demonstrates the use of H-Bridge 5 Click board, by running dc motor forward,
* then stoping and then running it in reverse and stoping again.
*
* \author MikroE Team
*
*/
// ------------------------------------------------------------------- INCLUDES
#include "board.h"
#include "log.h"
#include "hbridge5.h"
// ------------------------------------------------------------------ VARIABLES
static hbridge5_t hbridge5;
static log_t logger;
// ------------------------------------------------------ APPLICATION FUNCTIONS
void application_init ( void )
{
log_cfg_t log_cfg;
hbridge5_cfg_t cfg;
/**
* Logger initialization.
* Default baud rate: 115200
* Default log level: LOG_LEVEL_DEBUG
* @note If USB_UART_RX and USB_UART_TX
* are defined as HAL_PIN_NC, you will
* need to define them manually for log to work.
* See @b LOG_MAP_USB_UART macro definition for detailed explanation.
*/
LOG_MAP_USB_UART( log_cfg );
log_init( &logger, &log_cfg );
log_info( &logger, "---- Application Init ----" );
// Click initialization.
hbridge5_cfg_setup( &cfg );
HBRIDGE5_MAP_MIKROBUS( cfg, MIKROBUS_1 );
hbridge5_init( &hbridge5, &cfg );
hbridge5_default_cfg( &hbridge5 );
}
void application_task ( void )
{
log_printf( &logger, "Mode - FORWARD\r\n" );
hbridge5_forward( &hbridge5 );
Delay_ms ( 1000 );
Delay_ms ( 1000 );
Delay_ms ( 1000 );
log_printf( &logger, "Mode - SLEEP\r\n" );
hbridge5_sleep( &hbridge5, HBRIDGE5_DISABLE_ALL_OUTPUT_PORT );
Delay_ms ( 1000 );
Delay_ms ( 1000 );
Delay_ms ( 1000 );
log_printf( &logger, "Mode - REVERSE\r\n" );
hbridge5_reverse( &hbridge5 );
Delay_ms ( 1000 );
Delay_ms ( 1000 );
Delay_ms ( 1000 );
log_printf( &logger, "Mode - SLEEP\r\n" );
hbridge5_sleep( &hbridge5, HBRIDGE5_DISABLE_ALL_OUTPUT_PORT );
Delay_ms ( 1000 );
Delay_ms ( 1000 );
Delay_ms ( 1000 );
}
int main ( void )
{
/* Do not remove this line or clock might not be set correctly. */
#ifdef PREINIT_SUPPORTED
preinit();
#endif
application_init( );
for ( ; ; )
{
application_task( );
}
return 0;
}
// ------------------------------------------------------------------------ END
Additional Support
Resources
Category:Brushed