Fast and non-volatile magneto-resistive random-access memory
A
A
Hardware Overview
How does it work?
MRAM 3 Click is based on the AS3001204, a 1Mb MRAM memory with an SPI interface and Write Protection feature from Avalanche Technology. The AS3001204 is organized as 128K words of 8 bits each and benefits from 1.000.000 years of data retention combining their unprecedented data storage with excellent energy efficiency. It is highly reliable, lasting 1014 full-memory read/write/erase cycles, which makes this Click board™ suitable for high-reliability applications as a non-volatile storage media or temporary RAM expansion for storing data in any embedded application. The AS3001204 is an accurate random-access memory that allows both reads and writes to occur randomly. It offers low latency, low power, and scalable non-volatile memory
technology. The MRAM technology is analog to Flash technology with SRAM-compatible read/write timings (Persistent SRAM, P-SRAM), where data is always non-volatile. MRAM 3 Click communicates with MCU using the SPI serial interface that supports the Dual/Quad SPI and the two most common modes, SPI Mode 0 and 3, with a maximum SPI frequency of 108MHz. Alongside an SPI-compatible bus interface, the AS3001204 also features an eXecute-In-Place (XIP) functionality which allows completing a series of reading and writing instructions without having to individually load the read or write command for each instruction and hardware/software-based data protection mechanisms. Hardware Write Protection function, labeled and routed to the WP pin
of the mikroBUS™ socket, allows the user to freeze the entire memory area, thus protecting it from writing instructions. The IO3 pin of the mikroBUS™ socket is bidirectional I/O that transfers data into and out of the device in Dual and Quad SPI modes. This Click board™ can only be operated from a 3.3V logic voltage level. Therefore, the board must perform appropriate logic voltage conversion before using MCUs with different logic levels. However, the Click board™ comes equipped with a library containing functions and an example code that can be used as a reference for further development.
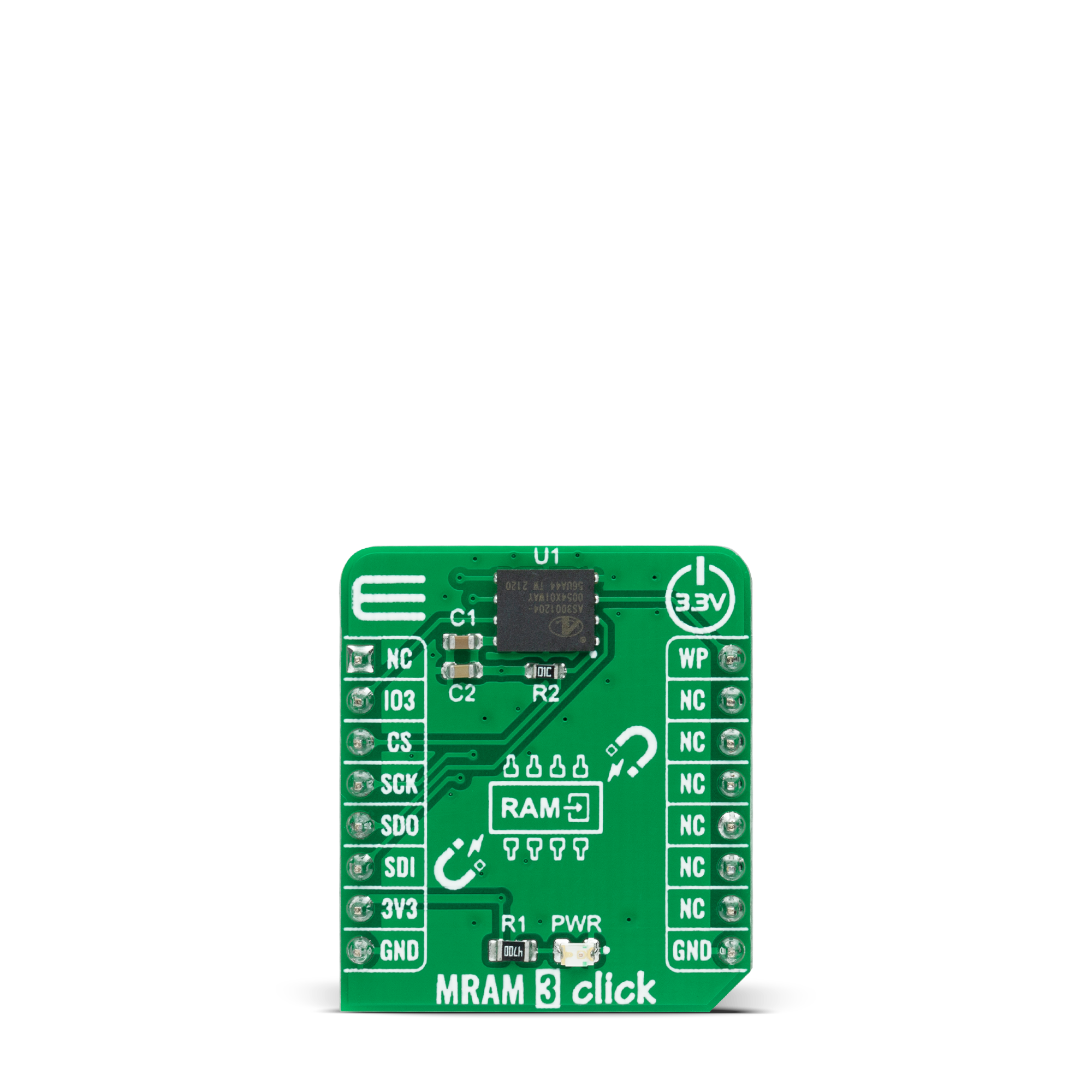
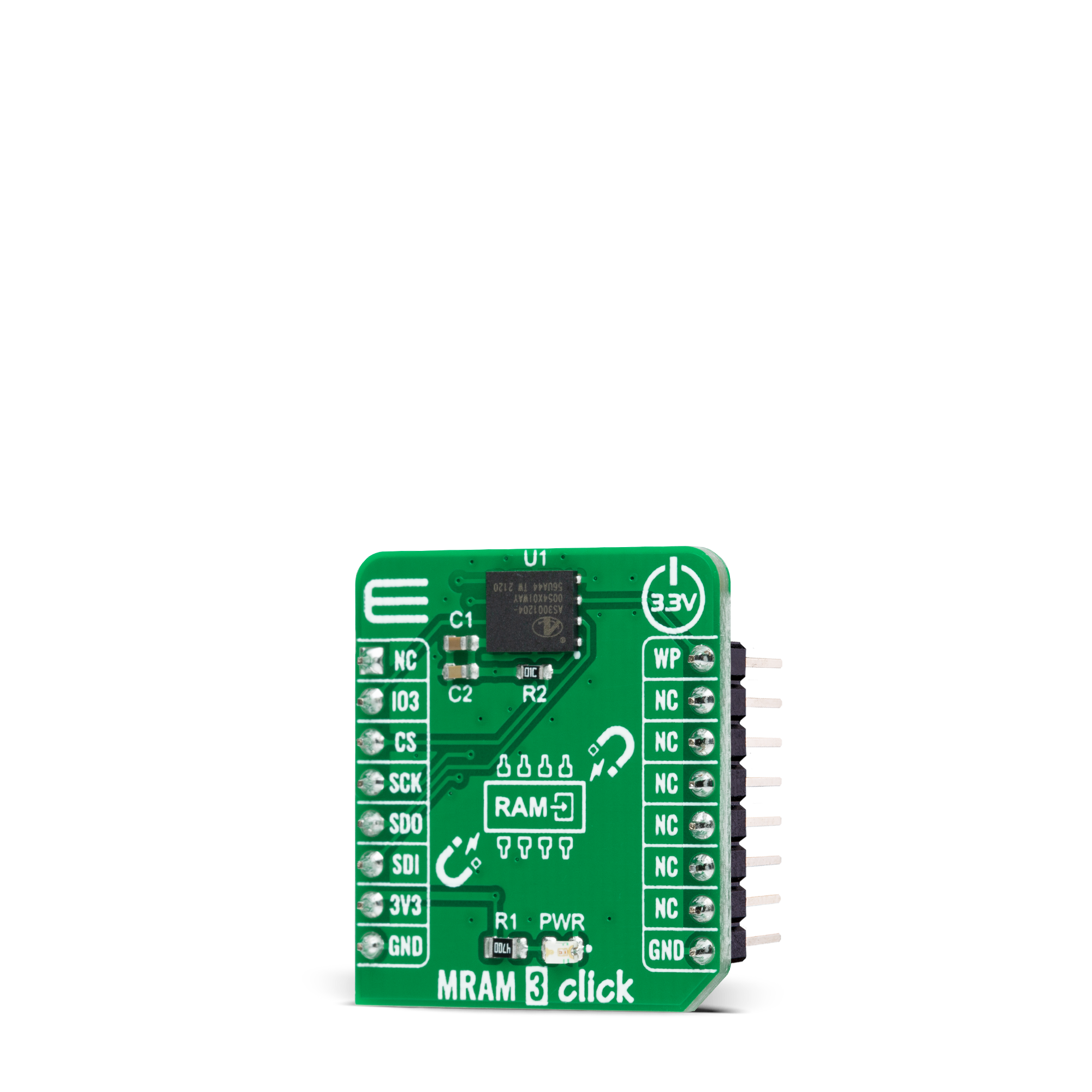

Features overview
Development board
Arduino Mega 2560 is a robust microcontroller platform built around the ATmega 2560 chip. It has extensive capabilities and boasts 54 digital input/output pins, including 15 PWM outputs, 16 analog inputs, and 4 UARTs. With a 16MHz crystal
oscillator ensuring precise timing, it offers seamless connectivity via USB, a convenient power jack, an ICSP header, and a reset button. This all-inclusive board simplifies microcontroller projects; connect it to your computer via USB or power it up
using an AC-to-DC adapter or battery. Notably, the Mega 2560 maintains compatibility with a wide range of shields crafted for the Uno, Duemilanove, or Diecimila boards, ensuring versatility and ease of integration.
Microcontroller Overview
MCU Card / MCU
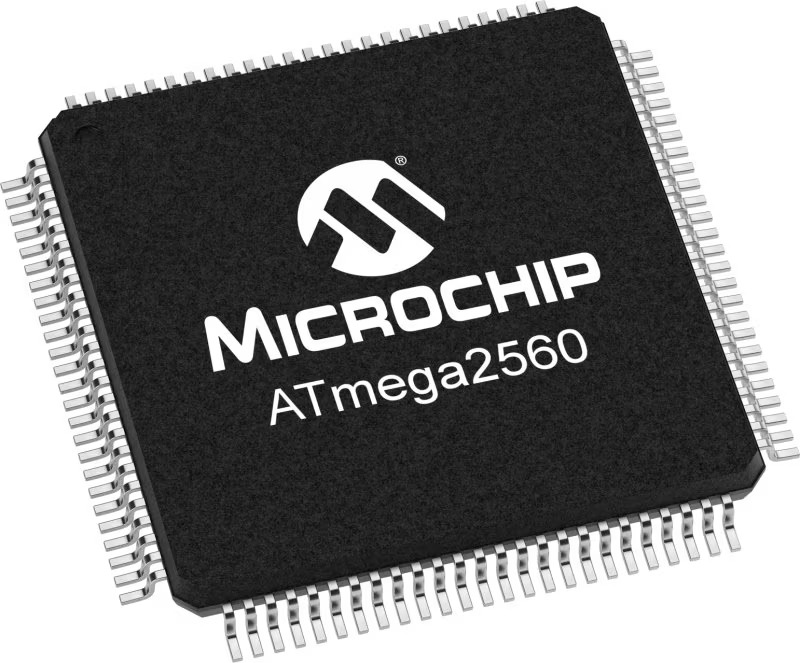
Architecture
AVR
MCU Memory (KB)
256
Silicon Vendor
Microchip
Pin count
100
RAM (Bytes)
8192
You complete me!
Accessories
Click Shield for Arduino Mega comes equipped with four mikroBUS™ sockets, with two in the form of a Shuttle connector, allowing all the Click board™ devices to be interfaced with the Arduino Mega board with no effort. Featuring an AVR 8-bit microcontroller with advanced RISC architecture, 54 digital I/O pins, and Arduino™ compatibility, the Arduino Mega board offers limitless possibilities for prototyping and creating diverse applications. This board is controlled and powered conveniently through a USB connection to program and debug the Arduino Mega board efficiently out of the box, with an additional USB cable connected to the USB B port on the board. Simplify your project development with the integrated ATmega16U2 programmer and unleash creativity using the extensive I/O options and expansion capabilities. There are eight switches, which you can use as inputs, and eight LEDs, which can be used as outputs of the MEGA2560. In addition, the shield features the MCP1501, a high-precision buffered voltage reference from Microchip. This reference is selected by default over the EXT REF jumper at the bottom of the board. You can choose an external one, as you would usually do with an Arduino Mega board. There is also a GND hook for testing purposes. Four additional LEDs are PWR, LED (standard pin D13), RX, and TX LEDs connected to UART1 (mikroBUS™ 1 socket). This Click Shield also has several switches that perform functions such as selecting the logic levels of analog signals on mikroBUS™ sockets and selecting logic voltage levels of the mikroBUS™ sockets themselves. Besides, the user is offered the possibility of using any Click board™ with the help of existing bidirectional level-shifting voltage translators, regardless of whether the Click board™ operates at a 3.3V or 5V logic voltage level. Once you connect the Arduino Mega board with Click Shield for Arduino Mega, you can access hundreds of Click boards™, working with 3.3V or 5V logic voltage levels.
Used MCU Pins
mikroBUS™ mapper
Take a closer look
Click board™ Schematic
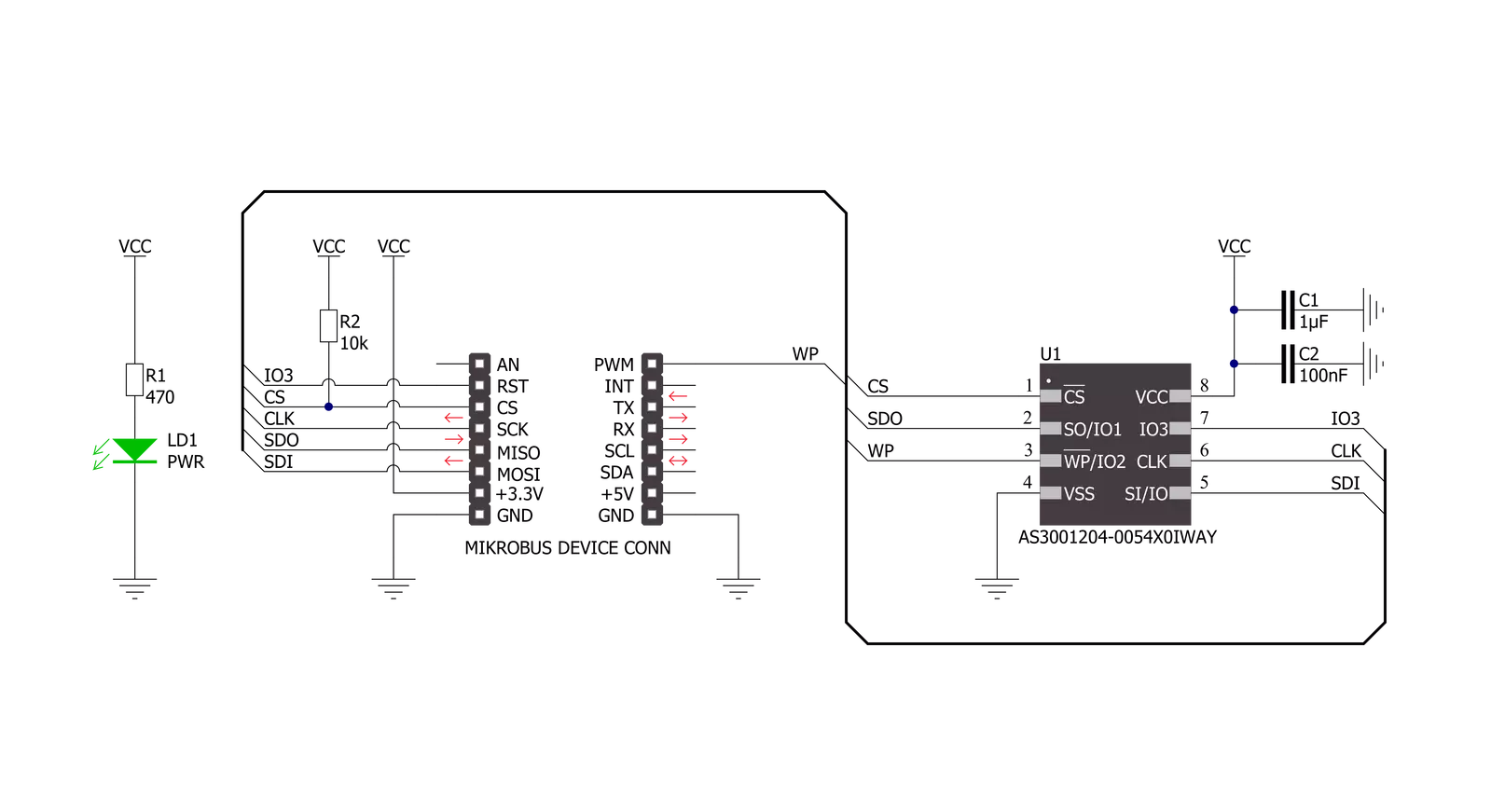
Step by step
Project assembly
Track your results in real time
Application Output
1. Application Output - In Debug mode, the 'Application Output' window enables real-time data monitoring, offering direct insight into execution results. Ensure proper data display by configuring the environment correctly using the provided tutorial.
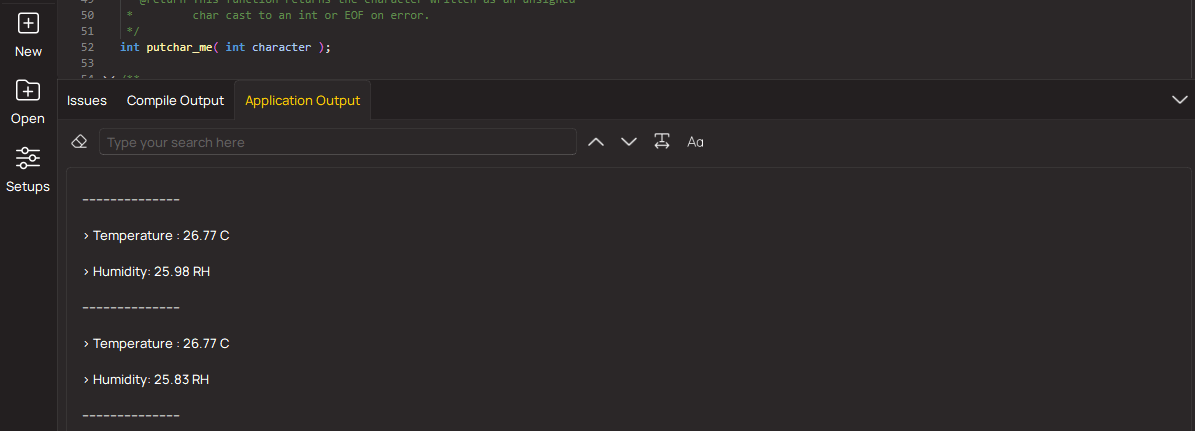
2. UART Terminal - Use the UART Terminal to monitor data transmission via a USB to UART converter, allowing direct communication between the Click board™ and your development system. Configure the baud rate and other serial settings according to your project's requirements to ensure proper functionality. For step-by-step setup instructions, refer to the provided tutorial.
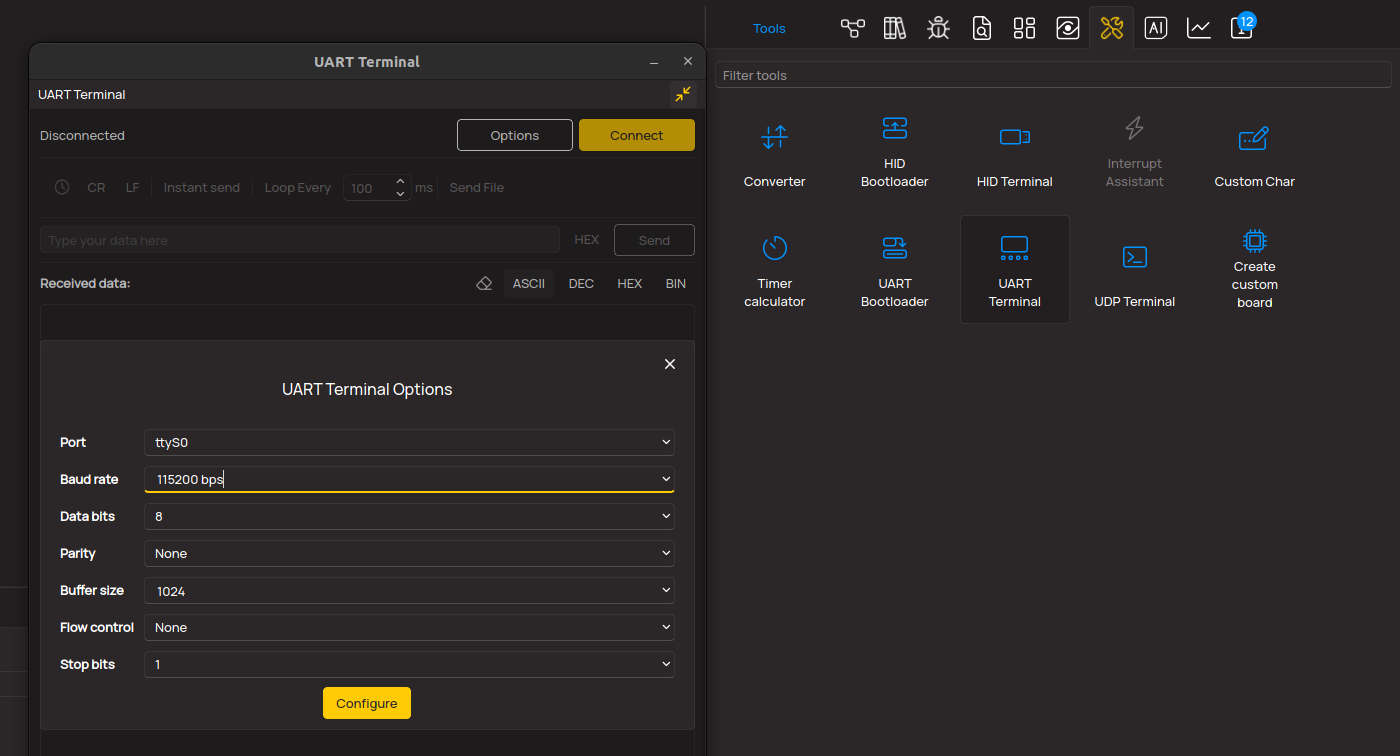
3. Plot Output - The Plot feature offers a powerful way to visualize real-time sensor data, enabling trend analysis, debugging, and comparison of multiple data points. To set it up correctly, follow the provided tutorial, which includes a step-by-step example of using the Plot feature to display Click board™ readings. To use the Plot feature in your code, use the function: plot(*insert_graph_name*, variable_name);. This is a general format, and it is up to the user to replace 'insert_graph_name' with the actual graph name and 'variable_name' with the parameter to be displayed.
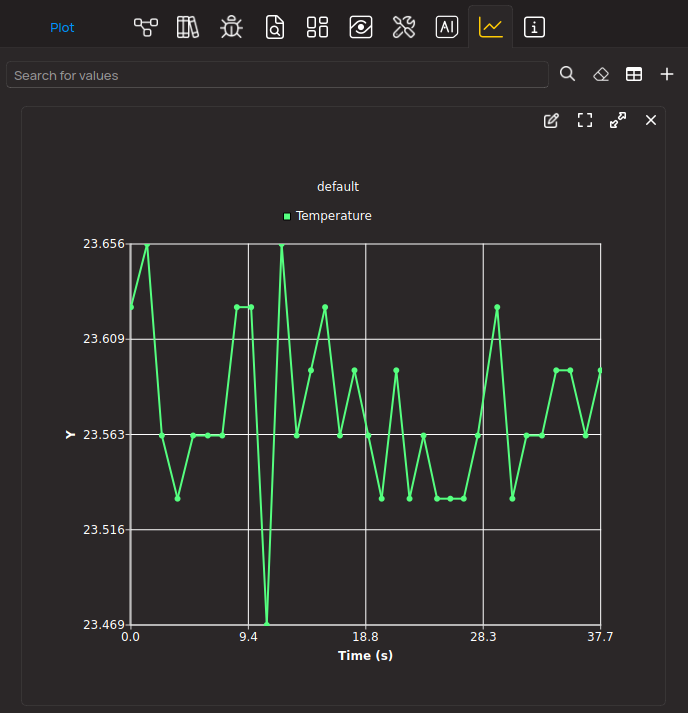
Software Support
Library Description
This library contains API for MRAM 3 Click driver.
Key functions:
mram3_memory_write
This function writes a desired number of data bytes starting from the selected memory address.mram3_memory_read
This function reads a desired number of data bytes starting from the selected memory address.mram3_aug_memory_write
This function writes a desired number of data bytes starting from the selected augmented memory address.
Open Source
Code example
The complete application code and a ready-to-use project are available through the NECTO Studio Package Manager for direct installation in the NECTO Studio. The application code can also be found on the MIKROE GitHub account.
/*!
* @file main.c
* @brief MRAM3 Click example
*
* # Description
* This example demonstrates the use of MRAM 3 Click board by writing specified data to
* the memory and reading it back.
*
* The demo application is composed of two sections :
*
* ## Application Init
* Initializes the driver and performs the Click default configuration.
*
* ## Application Task
* Writes a desired number of bytes to the memory and then verifies if it is written correctly
* by reading from the same memory location and displaying the memory content on the USB UART.
*
* @author Stefan Filipovic
*
*/
#include "board.h"
#include "log.h"
#include "mram3.h"
static mram3_t mram3;
static log_t logger;
#define DEMO_TEXT_MESSAGE_1 "MikroE"
#define DEMO_TEXT_MESSAGE_2 "MRAM 3 Click"
#define STARTING_ADDRESS 0x01234
void application_init ( void )
{
log_cfg_t log_cfg; /**< Logger config object. */
mram3_cfg_t mram3_cfg; /**< Click config object. */
/**
* Logger initialization.
* Default baud rate: 115200
* Default log level: LOG_LEVEL_DEBUG
* @note If USB_UART_RX and USB_UART_TX
* are defined as HAL_PIN_NC, you will
* need to define them manually for log to work.
* See @b LOG_MAP_USB_UART macro definition for detailed explanation.
*/
LOG_MAP_USB_UART( log_cfg );
log_init( &logger, &log_cfg );
log_info( &logger, " Application Init " );
// Click initialization.
mram3_cfg_setup( &mram3_cfg );
MRAM3_MAP_MIKROBUS( mram3_cfg, MIKROBUS_1 );
if ( SPI_MASTER_ERROR == mram3_init( &mram3, &mram3_cfg ) )
{
log_error( &logger, " Communication init." );
for ( ; ; );
}
if ( MRAM3_ERROR == mram3_default_cfg ( &mram3 ) )
{
log_error( &logger, " Default configuration." );
for ( ; ; );
}
log_info( &logger, " Application Task " );
}
void application_task ( void )
{
uint8_t data_buf[ 128 ] = { 0 };
memcpy ( data_buf, DEMO_TEXT_MESSAGE_1, strlen ( DEMO_TEXT_MESSAGE_1 ) );
if ( MRAM3_OK == mram3_memory_write ( &mram3, STARTING_ADDRESS,
data_buf, sizeof ( data_buf ) ) )
{
log_printf ( &logger, "Data written to address 0x%.5LX: %s\r\n", ( uint32_t ) STARTING_ADDRESS,
data_buf );
}
memset ( data_buf, 0, sizeof ( data_buf ) );
if ( MRAM3_OK == mram3_memory_read ( &mram3, STARTING_ADDRESS,
data_buf, sizeof ( data_buf ) ) )
{
log_printf ( &logger, "Data read from address 0x%.5LX: %s\r\n", ( uint32_t ) STARTING_ADDRESS,
data_buf );
Delay_ms ( 1000 );
Delay_ms ( 1000 );
Delay_ms ( 1000 );
}
memcpy ( data_buf, DEMO_TEXT_MESSAGE_2, strlen ( DEMO_TEXT_MESSAGE_2 ) );
if ( MRAM3_OK == mram3_memory_write ( &mram3, STARTING_ADDRESS,
data_buf, sizeof ( data_buf ) ) )
{
log_printf ( &logger, "Data written to address 0x%.5LX: %s\r\n", ( uint32_t ) STARTING_ADDRESS,
data_buf );
}
memset ( data_buf, 0, sizeof ( data_buf ) );
if ( MRAM3_OK == mram3_memory_read ( &mram3, STARTING_ADDRESS,
data_buf, sizeof ( data_buf ) ) )
{
log_printf ( &logger, "Data read from address 0x%.5LX: %s\r\n\n", ( uint32_t ) STARTING_ADDRESS,
data_buf );
Delay_ms ( 1000 );
Delay_ms ( 1000 );
Delay_ms ( 1000 );
}
}
int main ( void )
{
/* Do not remove this line or clock might not be set correctly. */
#ifdef PREINIT_SUPPORTED
preinit();
#endif
application_init( );
for ( ; ; )
{
application_task( );
}
return 0;
}
// ------------------------------------------------------------------------ END
Additional Support
Resources
Category:MRAM