Our single-wire CAN transceiver is designed to streamline communication in low-speed applications, reducing wiring complexity and achieving cost savings in automotive body control modules
A
A
Hardware Overview
How does it work?
Single Wire CAN Click is based on the NCV7356, a Single Wire CAN transceiver from ON Semiconductor, which operates from a supply voltage from 5V to 27V with a bus speed up to 40 kbps. It can access several modes such as Normal Mode with reduced dominant output voltage and reduced receiver input voltage, High-Speed, High Voltage Wake-Up, or Sleep Mode. The transmission bit rate in Normal communication is 33 Kbits/s, while a typical bit rate of 83 kbit/s is recommended for High-Speed communication. In Normal Transmission Mode, the Single Wire CAN Click supports controlled waveform rise and overshoot times, while the High−Speed Mode is only intended to be operational when the bus is attached to an off−board service node. The Single Wire CAN bus pin CANH comprises a pull−up
amplifier for driving this Click board™. The minimum output driver capability is 50 mA, but output shorts to the ground can reach 350 mA. Normal CANH output voltage is between 4.4 V and 5.1 V. These amplitudes increase to 9.9 V and 12.5 V for system selection in Wake−Up Mode. The bus Wake−Up from Sleep Input Voltage Threshold is between 6.6 V and 7.9 V, but to maintain normal communication, the threshold is 2.1 V. The CANH pin can also act as a bus read amplifier. The NCV7356D1R2G communicates with MCU using the UART interface at 9600 bps with commonly used UART RX and TX pins. It possesses additional functionality such as Operational Mode Selection MODE 0 and MODE 1 routed at RST and CS pins of the mikroBUS™, on whose selected logical states one of the four possible operational modes can be
selected. The transceiver provides a weak internal pulldown current on each of these pins, which causes the transceiver, on default, to enter sleep mode when not driven. Single Wire CAN Click can also re-enter the Sleep Mode if there is no mode change within typically 250 ms. This Click board™ communicates with MCU using the UART interface for the data transfer. The onboard SMD jumper labeled VCC SEL allows logic level voltage selection for interfacing with 3.3V and 5V MCUs. More information about the NCV7356D1R2G’s functionality, electrical specifications, and typical performance can be found in the attached datasheet. However, the Click board™ comes equipped with a library that contains easy-to-use functions and a usage example that may be used as a reference for the development.
Features overview
Development board
Discovery kit with STM32F303VC MCU streamlines application development with the STM32F3 Series microcontroller, harnessing the robustness of Arm® Cortex®-M4 architecture to provide an optimal development experience. It caters to both beginners and experts, offering essential components for swift initiation. Powered by the STM32F303VCT6, it boasts features like ST-
LINK/V2 or ST-LINK/V2-B for debugging, accelerometer, gyroscope, e-compass ST MEMS, USB connectivity, LED indicators, and push-buttons. Key specifications include a 256-Kbyte Flash memory, 48-Kbyte RAM, USB FS support, and a comprehensive array of motion sensors. The board includes ten LEDs for various statuses, including power indication and USB
communication. With user-friendly connectors and flexible power-supply options, it enables easy integration with prototype boards. Equipped with an on-board debugger/programmer and support for various Integrated Development Environments (IDEs) like IAR™, Keil®, and STM32CubeIDE, it ensures smooth and efficient development cycles.
Microcontroller Overview
MCU Card / MCU
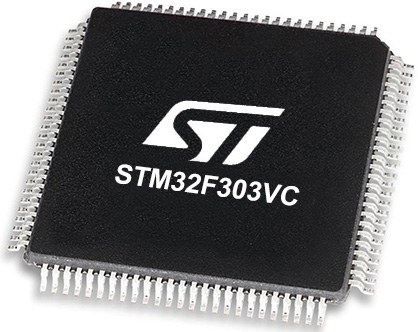
Architecture
ARM Cortex-M4
MCU Memory (KB)
256
Silicon Vendor
STMicroelectronics
Pin count
100
RAM (Bytes)
40960
You complete me!
Accessories
STM32F3 Discovery Shield is the perfect extension for your STM32F3 Discovery Board from STMicroelectronics. This versatile shield features four mikroBUS™ host sockets, a USB-UART module, and a CAN transceiver, expanding the capabilities of your Discovery board. Acting as a docking station, the STM32F3 Discovery Shield enables you to effortlessly transform your board into various applications, whether it's an RFID lock, SMS-triggered control switch, GPS tracking device, full-blown weather station, or any other idea you have in mind. With its seamless integration and enhanced functionality, this shield empowers you to explore endless possibilities and quickly bring your projects to life.
Used MCU Pins
mikroBUS™ mapper
Take a closer look
Click board™ Schematic
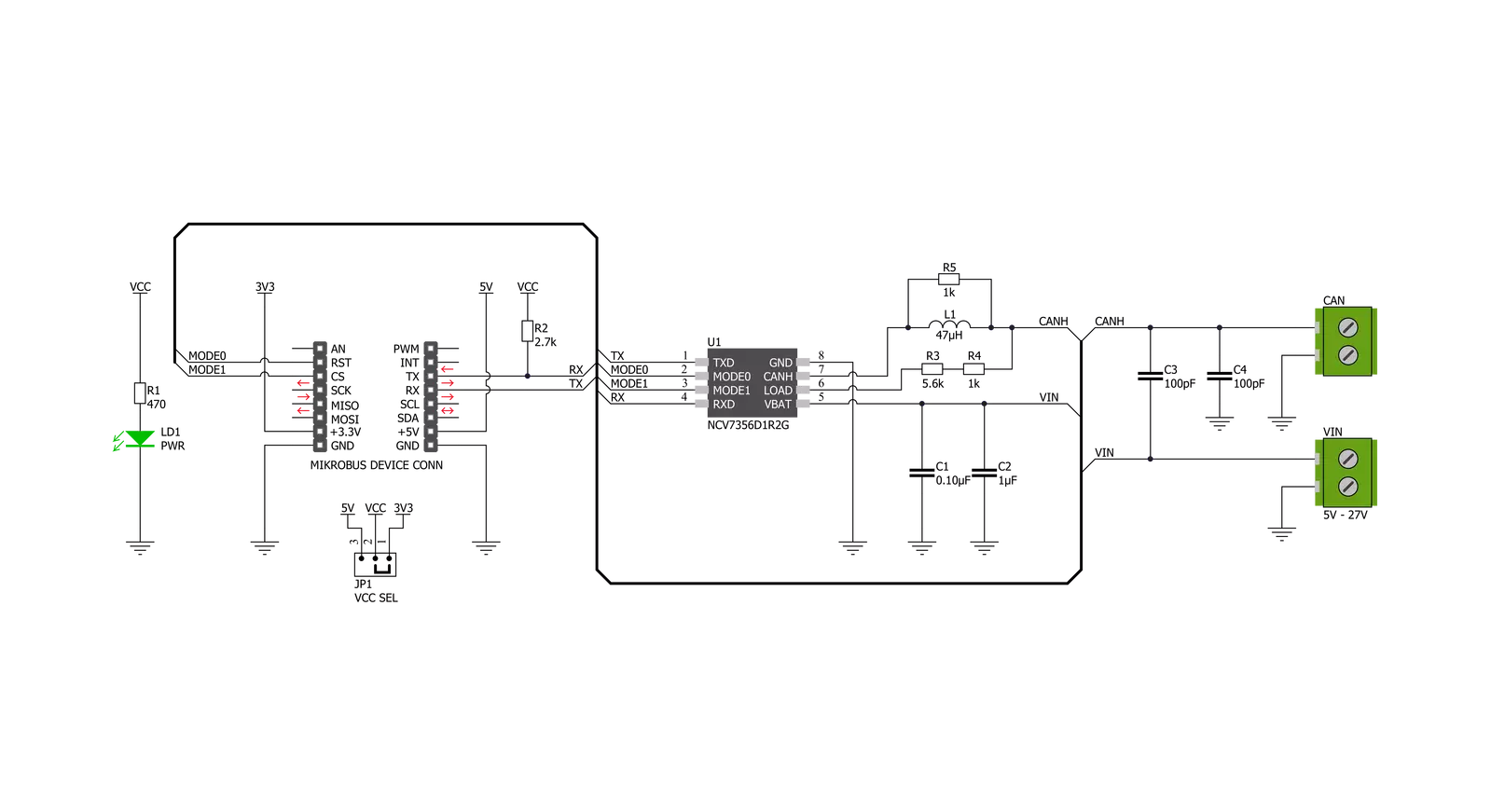
Step by step
Project assembly
Track your results in real time
Application Output
1. Application Output - In Debug mode, the 'Application Output' window enables real-time data monitoring, offering direct insight into execution results. Ensure proper data display by configuring the environment correctly using the provided tutorial.
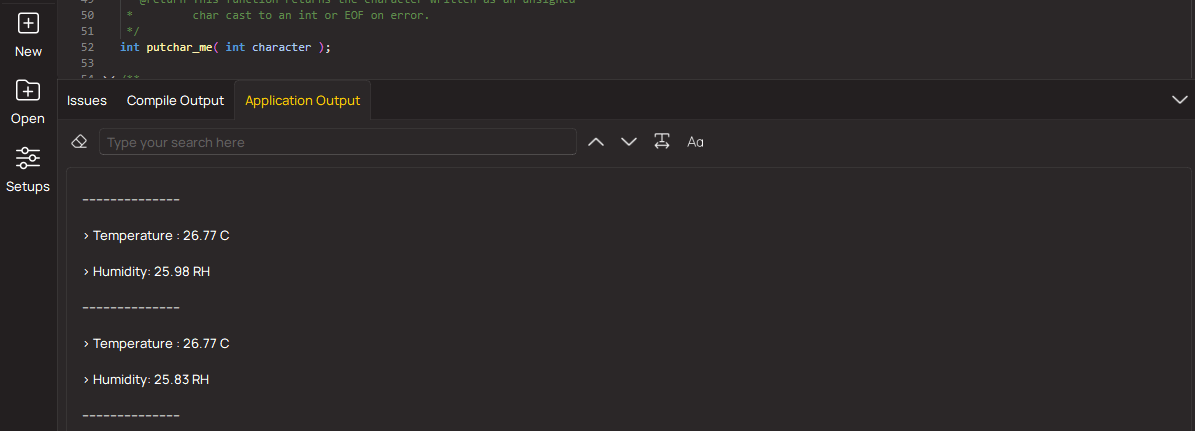
2. UART Terminal - Use the UART Terminal to monitor data transmission via a USB to UART converter, allowing direct communication between the Click board™ and your development system. Configure the baud rate and other serial settings according to your project's requirements to ensure proper functionality. For step-by-step setup instructions, refer to the provided tutorial.
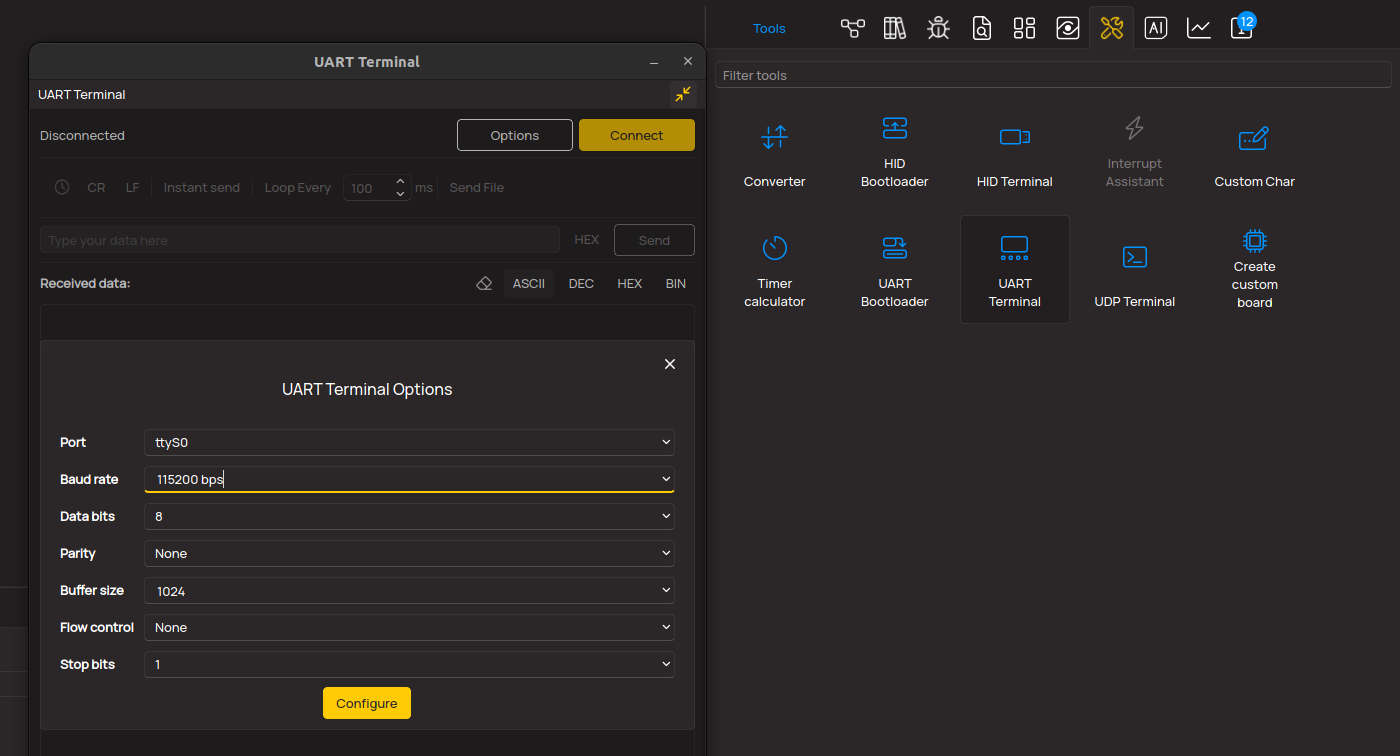
3. Plot Output - The Plot feature offers a powerful way to visualize real-time sensor data, enabling trend analysis, debugging, and comparison of multiple data points. To set it up correctly, follow the provided tutorial, which includes a step-by-step example of using the Plot feature to display Click board™ readings. To use the Plot feature in your code, use the function: plot(*insert_graph_name*, variable_name);. This is a general format, and it is up to the user to replace 'insert_graph_name' with the actual graph name and 'variable_name' with the parameter to be displayed.
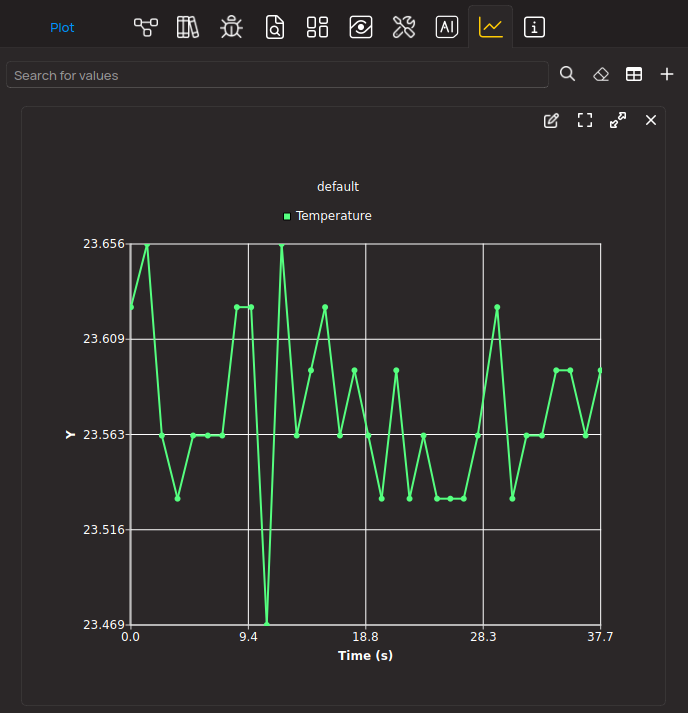
Software Support
Library Description
This library contains API for Single Wire CAN Click driver.
Key functions:
singlewirecan_set_operating_mode
- The function set desired operating mode of NCV7356 Single Wire CAN Transceiversinglewirecan_generic_write
- This function write specified number of bytessinglewirecan_generic_read
- This function reads a desired number of data bytes
Open Source
Code example
The complete application code and a ready-to-use project are available through the NECTO Studio Package Manager for direct installation in the NECTO Studio. The application code can also be found on the MIKROE GitHub account.
/*!
* \file
* \brief SingleWireCan Click example
*
* # Description
* This example demonstrate the use of Single Wire CAN Click board.
*
* The demo application is composed of two sections :
*
* ## Application Init
* Initializes the driver and configures the Click for the normal operation mode.
*
* ## Application Task
* Depending on the selected mode, it reads all the received data or sends the desired message
* every 2 seconds.
*
* ## Additional Function
* - singlewirecan_process ( ) - The general process of collecting the received data.
*
* \author MikroE Team
*
*/
// ------------------------------------------------------------------- INCLUDES
#include "board.h"
#include "log.h"
#include "singlewirecan.h"
#include "string.h"
#define PROCESS_RX_BUFFER_SIZE 500
#define TEXT_TO_SEND "MikroE\r\n"
// ------------------------------------------------------------------ VARIABLES
#define DEMO_APP_RECEIVER
// #define DEMO_APP_TRANSMITTER
static singlewirecan_t singlewirecan;
static log_t logger;
// ------------------------------------------------------- ADDITIONAL FUNCTIONS
static void singlewirecan_process ( void )
{
int32_t rsp_size;
char uart_rx_buffer[ PROCESS_RX_BUFFER_SIZE ] = { 0 };
uint8_t check_buf_cnt;
rsp_size = singlewirecan_generic_read( &singlewirecan, uart_rx_buffer, PROCESS_RX_BUFFER_SIZE );
if ( rsp_size >= strlen( TEXT_TO_SEND ) )
{
log_printf( &logger, "Received data: " );
for ( check_buf_cnt = 0; check_buf_cnt < rsp_size; check_buf_cnt++ )
{
log_printf( &logger, "%c", uart_rx_buffer[ check_buf_cnt ] );
}
}
Delay_ms ( 100 );
}
// ------------------------------------------------------ APPLICATION FUNCTIONS
void application_init ( void )
{
log_cfg_t log_cfg;
singlewirecan_cfg_t cfg;
/**
* Logger initialization.
* Default baud rate: 115200
* Default log level: LOG_LEVEL_DEBUG
* @note If USB_UART_RX and USB_UART_TX
* are defined as HAL_PIN_NC, you will
* need to define them manually for log to work.
* See @b LOG_MAP_USB_UART macro definition for detailed explanation.
*/
LOG_MAP_USB_UART( log_cfg );
log_init( &logger, &log_cfg );
log_info( &logger, "---- Application Init ----" );
// Click initialization.
singlewirecan_cfg_setup( &cfg );
SINGLEWIRECAN_MAP_MIKROBUS( cfg, MIKROBUS_1 );
singlewirecan_init( &singlewirecan, &cfg );
Delay_ms ( 100 );
singlewirecan_set_operating_mode( &singlewirecan, SINGLEWIRECAN_OPERATING_MODE_NORMAL );
log_info( &logger, "---- Normal Operation Mode ----" );
Delay_ms ( 100 );
}
void application_task ( void )
{
#ifdef DEMO_APP_RECEIVER
singlewirecan_process( );
#endif
#ifdef DEMO_APP_TRANSMITTER
singlewirecan_generic_write( &singlewirecan, TEXT_TO_SEND, 8 );
log_info( &logger, "---- Data sent ----" );
Delay_ms ( 1000 );
Delay_ms ( 1000 );
#endif
}
int main ( void )
{
/* Do not remove this line or clock might not be set correctly. */
#ifdef PREINIT_SUPPORTED
preinit();
#endif
application_init( );
for ( ; ; )
{
application_task( );
}
return 0;
}
// ------------------------------------------------------------------------ END