Monitors the state and health of your single-cell battery
A
A
Hardware Overview
How does it work?
BATT-MON 2 Click is based on the MAX17262, an ultra-low power fuel-gauge IC that implements the ModelGauge™ m5 algorithm from Analog Devices. It provides, at the same time, tolerance against battery diversity for most lithium batteries (providing good performance for most cell types) and applications. The MAX17262 features internal current measurement for up to 3.1A pulse currents and accurately measures voltage, current, and temperature to produce fuel gauge results. It shows the best performance for batteries with 100mAhr to 6Ahr capacity. The ModelGauge™ m5 EZ algorithm combines a Coulomb counter's short-term accuracy and linearity with the long-term stability of a voltage-based fuel gauge, along with temperature compensation, to provide industry-leading fuel-gauge accuracy.
The MAX17262 automatically compensates for cell aging, temperature, and discharge rate, providing accurate state-of-charge in percentage (%) and remaining capacity in milliampere-hours (mAh) over a wide range of operating conditions. As the battery approaches the critical region near empty, the ModelGauge™ m5 algorithm invokes a unique correction mechanism that eliminates errors. The MAX17262 accurately estimates time-to-empty and time-to-full through three methods for reporting the battery age: reduction in capacity, increase in battery resistance and cycle odometer. BATT-MON 2 Click communicates with MCU using the standard I2C 2-Wire interface to read data and configure settings with a maximum frequency of 400kHz. An alert/interrupt function is also available that outputs an interrupt signal
to the ALR pin of the mikroBUS™ socket, indicating fuel-gauge alerts. This feature is visually presented by a red LED marked as ALR. Besides, this Click board™ also features battery pack temperature sensing through an integrated temperature sensor or an external NTC thermistor which can be connected to the onboard terminal labeled TH. This Click board™ can operate with either 3.3V or 5V logic voltage levels selected via the VIO SEL jumper. This way, both 3.3V and 5V capable MCUs can use the communication lines properly. However, the Click board™ comes equipped with a library containing easy-to-use functions and an example code that can be used, as a reference, for further development.
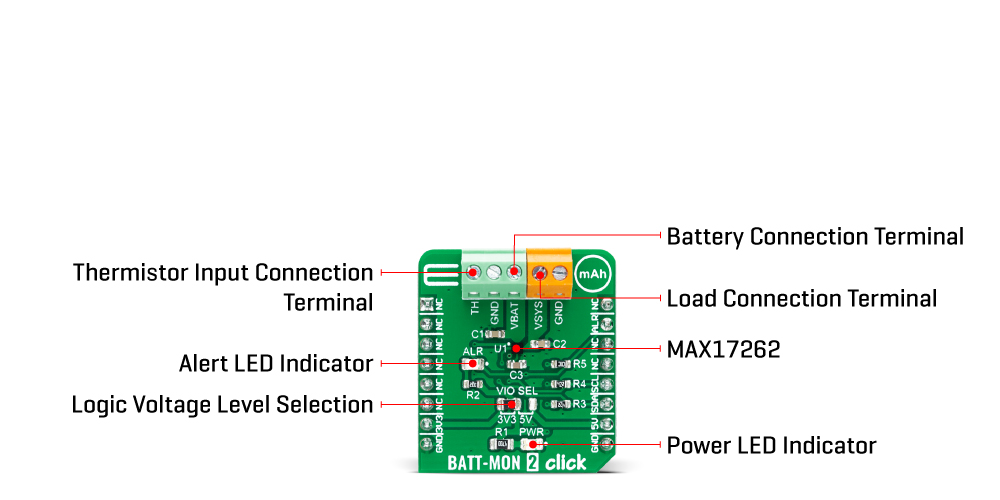
Features overview
Development board
Clicker 4 for STM32F3 is a compact development board designed as a complete solution, you can use it to quickly build your own gadgets with unique functionalities. Featuring a STM32F302VCT6, four mikroBUS™ sockets for Click boards™ connectivity, power managment, and more, it represents a perfect solution for the rapid development of many different types of applications. At its core, there is a STM32F302VCT6 MCU, a powerful microcontroller by STMicroelectronics, based on the high-
performance Arm® Cortex®-M4 32-bit processor core operating at up to 168 MHz frequency. It provides sufficient processing power for the most demanding tasks, allowing Clicker 4 to adapt to any specific application requirements. Besides two 1x20 pin headers, four improved mikroBUS™ sockets represent the most distinctive connectivity feature, allowing access to a huge base of Click boards™, growing on a daily basis. Each section of Clicker 4 is clearly marked, offering an intuitive and clean interface. This makes working with the development
board much simpler and thus, faster. The usability of Clicker 4 doesn’t end with its ability to accelerate the prototyping and application development stages: it is designed as a complete solution which can be implemented directly into any project, with no additional hardware modifications required. Four mounting holes [4.2mm/0.165”] at all four corners allow simple installation by using mounting screws. For most applications, a nice stylish casing is all that is needed to turn the Clicker 4 development board into a fully functional, custom design.
Microcontroller Overview
MCU Card / MCU
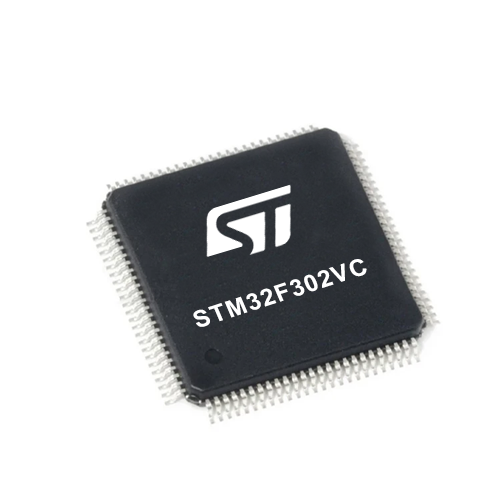
Architecture
ARM Cortex-M4
MCU Memory (KB)
256
Silicon Vendor
STMicroelectronics
Pin count
100
RAM (Bytes)
40960
You complete me!
Accessories
Li-Polymer Battery is the ideal solution for devices that demand a dependable and long-lasting power supply while emphasizing mobility. Its compatibility with mikromedia boards ensures easy integration without additional modifications. With a voltage output of 3.7V, the battery meets the standard requirements of many electronic devices. Additionally, boasting a capacity of 2000mAh, it can store a substantial amount of energy, providing sustained power for extended periods. This feature minimizes the need for frequent recharging or replacement. Overall, the Li-Polymer Battery is a reliable and autonomous power source, ideally suited for devices requiring a stable and enduring energy solution. You can find a more extensive choice of Li-Polymer batteries in our offer.
Used MCU Pins
mikroBUS™ mapper
Take a closer look
Click board™ Schematic
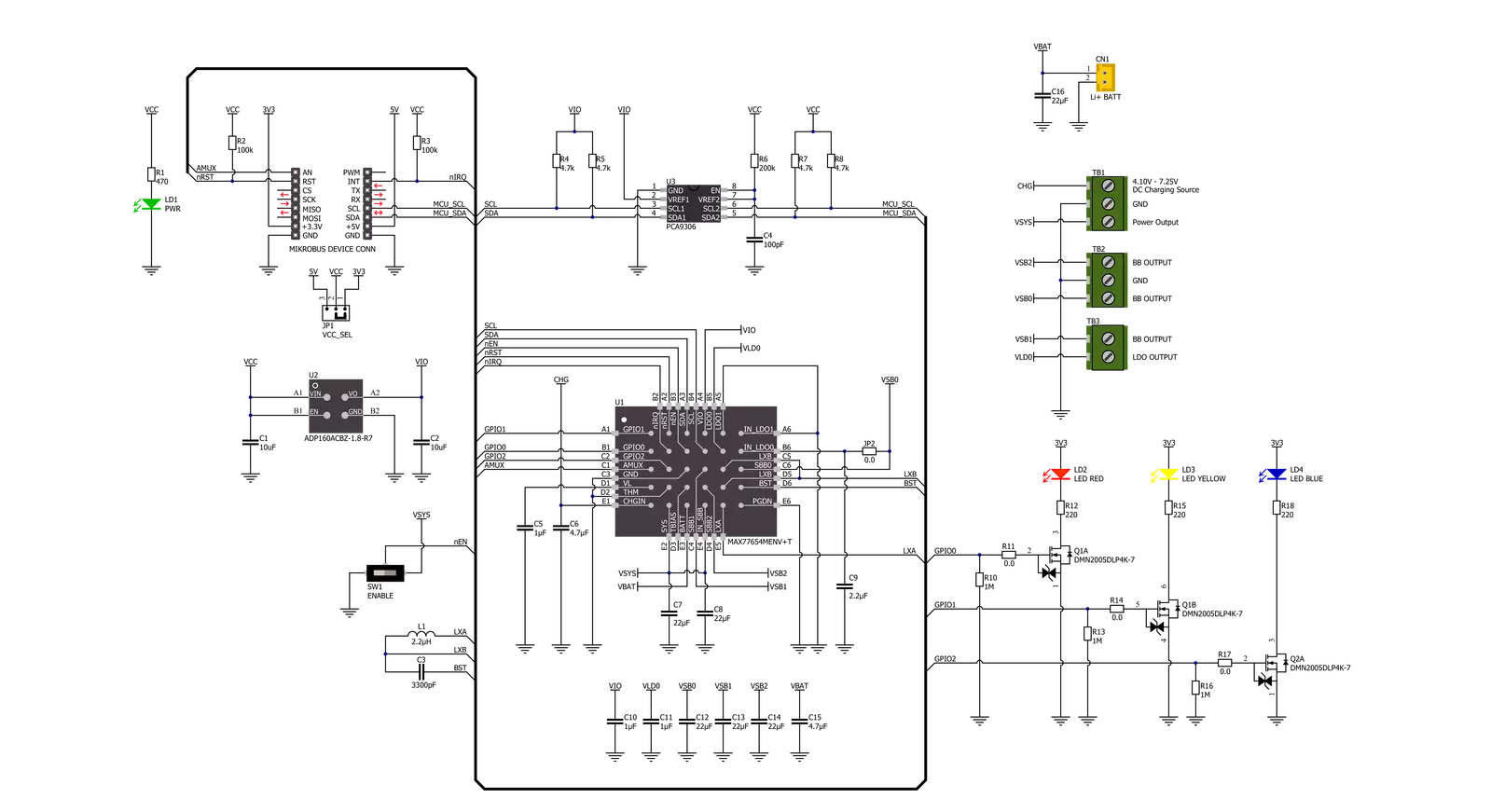
Step by step
Project assembly
Track your results in real time
Application Output
1. Application Output - In Debug mode, the 'Application Output' window enables real-time data monitoring, offering direct insight into execution results. Ensure proper data display by configuring the environment correctly using the provided tutorial.
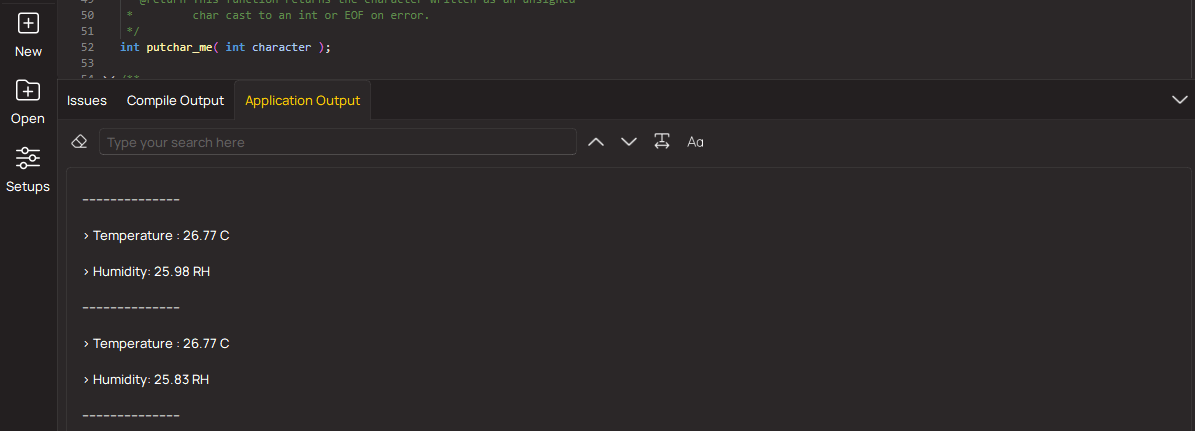
2. UART Terminal - Use the UART Terminal to monitor data transmission via a USB to UART converter, allowing direct communication between the Click board™ and your development system. Configure the baud rate and other serial settings according to your project's requirements to ensure proper functionality. For step-by-step setup instructions, refer to the provided tutorial.
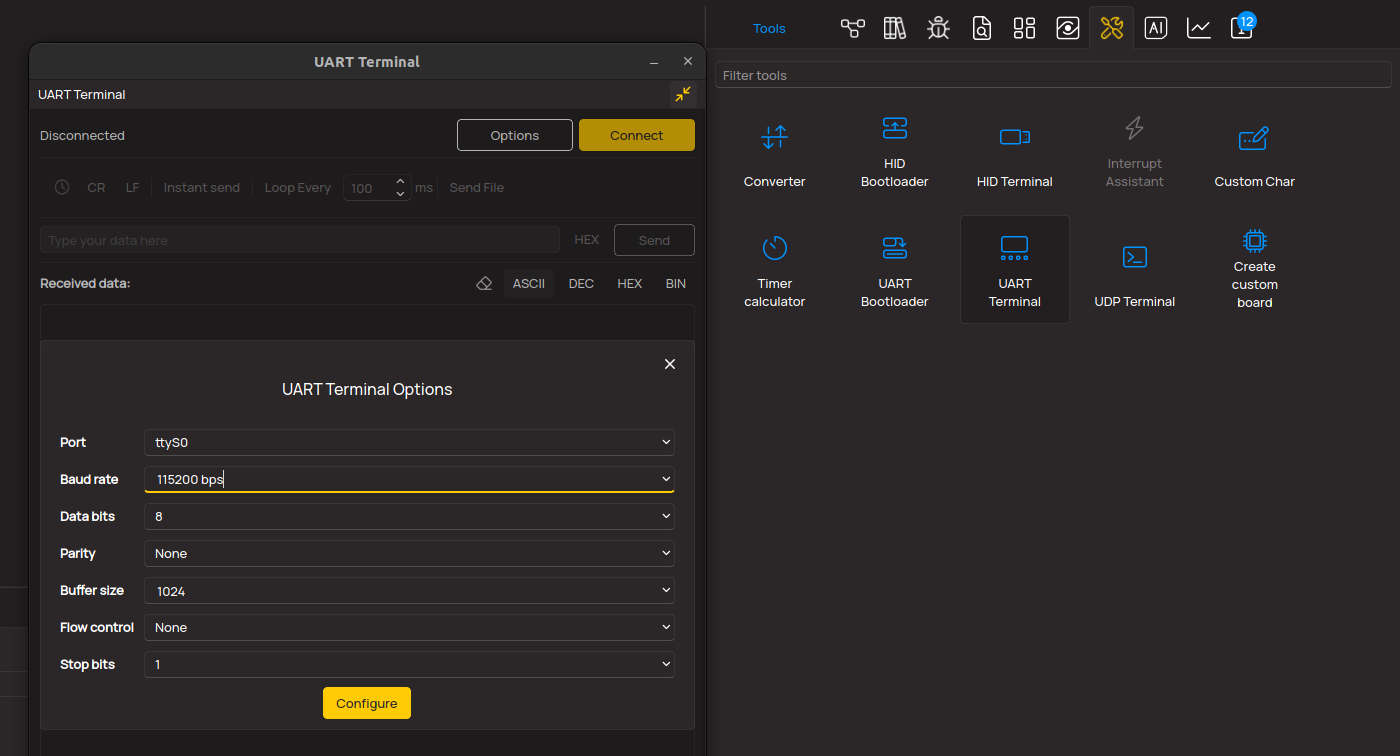
3. Plot Output - The Plot feature offers a powerful way to visualize real-time sensor data, enabling trend analysis, debugging, and comparison of multiple data points. To set it up correctly, follow the provided tutorial, which includes a step-by-step example of using the Plot feature to display Click board™ readings. To use the Plot feature in your code, use the function: plot(*insert_graph_name*, variable_name);. This is a general format, and it is up to the user to replace 'insert_graph_name' with the actual graph name and 'variable_name' with the parameter to be displayed.
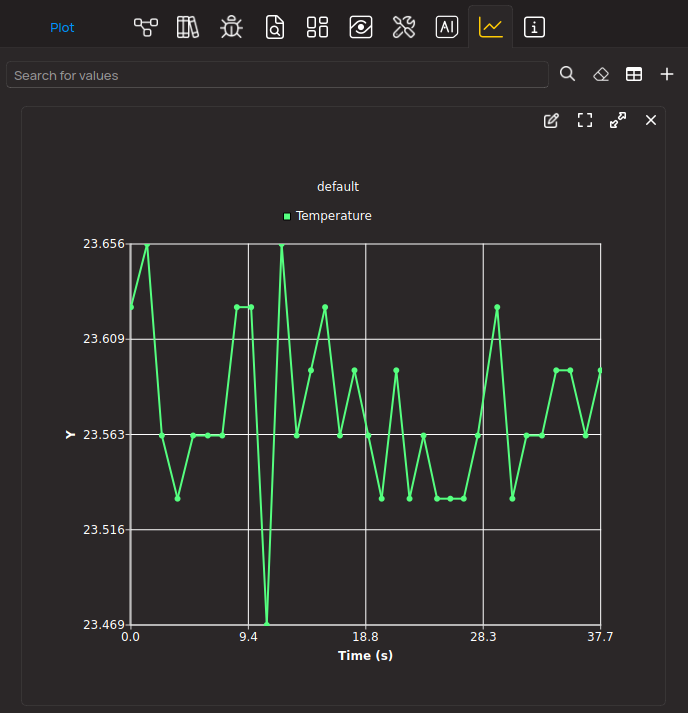
Software Support
Library Description
This library contains API for BATT-MON 2 Click driver.
Key functions:
battmon2_get_battery_voltage
This function reads the battery voltage in mV.battmon2_get_battery_current
This function reads the battery current in mA.battmon2_get_battery_percentage
This function reads the battery's remaining SOC percentage.
Open Source
Code example
The complete application code and a ready-to-use project are available through the NECTO Studio Package Manager for direct installation in the NECTO Studio. The application code can also be found on the MIKROE GitHub account.
/*!
* @file main.c
* @brief BATTMON2 Click example
*
* # Description
* This example demonstrates the use of BATT-MON 2 Click board by monitoring
* the measurements of battery voltage, current, capacity, percentage, time-to-empty or time-to-full,
* as well as the chip internal temperature.
*
* The demo application is composed of two sections :
*
* ## Application Init
* Initializes the driver and checks the communication by reading and verifying the device ID.
*
* ## Application Task
* Reads and displays on the USB UART the measurements of battery voltage, current, capacity, percentage,
* time-to-empty or time-to-full, as well as the chip internal temperature approximately once per second.
*
* @author Stefan Filipovic
*
*/
#include "board.h"
#include "log.h"
#include "battmon2.h"
static battmon2_t battmon2;
static log_t logger;
void application_init ( void )
{
log_cfg_t log_cfg; /**< Logger config object. */
battmon2_cfg_t battmon2_cfg; /**< Click config object. */
/**
* Logger initialization.
* Default baud rate: 115200
* Default log level: LOG_LEVEL_DEBUG
* @note If USB_UART_RX and USB_UART_TX
* are defined as HAL_PIN_NC, you will
* need to define them manually for log to work.
* See @b LOG_MAP_USB_UART macro definition for detailed explanation.
*/
LOG_MAP_USB_UART( log_cfg );
log_init( &logger, &log_cfg );
log_info( &logger, " Application Init " );
// Click initialization.
battmon2_cfg_setup( &battmon2_cfg );
BATTMON2_MAP_MIKROBUS( battmon2_cfg, MIKROBUS_1 );
if ( I2C_MASTER_ERROR == battmon2_init( &battmon2, &battmon2_cfg ) )
{
log_error( &logger, " Communication init." );
for ( ; ; );
}
if ( BATTMON2_ERROR == battmon2_check_communication ( &battmon2 ) )
{
log_error( &logger, " Check communication." );
for ( ; ; );
}
log_info( &logger, " Application Task " );
}
void application_task ( void )
{
float voltage, capacity, percentage, current, die_temp;
if ( BATTMON2_OK == battmon2_get_battery_voltage ( &battmon2, &voltage ) )
{
log_printf ( &logger, " Voltage: %.1f mV \r\n", voltage );
}
if ( BATTMON2_OK == battmon2_get_battery_current ( &battmon2, ¤t ) )
{
log_printf ( &logger, " Current: %.1f mA \r\n", current );
}
if ( BATTMON2_OK == battmon2_get_battery_capacity ( &battmon2, &capacity ) )
{
log_printf ( &logger, " Capacity: %.1f mAh \r\n", capacity );
}
if ( BATTMON2_OK == battmon2_get_battery_percentage ( &battmon2, &percentage ) )
{
log_printf ( &logger, " Percentage: %.1f %% \r\n", percentage );
}
if ( current > 0 )
{
uint32_t time_to_full;
if ( BATTMON2_OK == battmon2_get_battery_ttf ( &battmon2, &time_to_full ) )
{
log_printf ( &logger, " Time to full: %uh %umin %usec \r\n", ( uint16_t ) ( time_to_full / 3600 ),
( uint16_t ) ( time_to_full % 3600 ) / 60,
( uint16_t ) ( time_to_full % 60 ) );
}
}
else if ( current < 0 )
{
uint32_t time_to_empty;
if ( BATTMON2_OK == battmon2_get_battery_tte ( &battmon2, &time_to_empty ) )
{
log_printf ( &logger, " Time to empty: %uh %umin %usec \r\n", ( uint16_t ) ( time_to_empty / 3600 ),
( uint16_t ) ( time_to_empty % 3600 ) / 60,
( uint16_t ) ( time_to_empty % 60 ) );
}
}
if ( BATTMON2_OK == battmon2_get_die_temperature ( &battmon2, &die_temp ) )
{
log_printf ( &logger, " Internal temperature: %.2f C \r\n\n", die_temp );
}
Delay_ms ( 1000 );
}
int main ( void )
{
/* Do not remove this line or clock might not be set correctly. */
#ifdef PREINIT_SUPPORTED
preinit();
#endif
application_init( );
for ( ; ; )
{
application_task( );
}
return 0;
}
// ------------------------------------------------------------------------ END
Additional Support
Resources
Category:Battery charger