Accurate rotation angle and speed control using pulse signals
A
A
Hardware Overview
How does it work?
Stepper 12 Click is based on the TB67S549FTG, a two-phase bipolar stepping motor driver designed to control one bipolar stepping motor with resistorless current sensing owing to the built-in function of Advanced Current Detect System (ACDS) from Toshiba Semiconductor. The TB67S549FTG incorporates low on-resistance DMOS FETs, which can deliver a 1.5A maximum current with a motor output voltage rating of 40V and integrated protection mechanisms such as over-current, over-temperature, and under-voltage lockout for error detection (LO LED indicator). It supports full-step to 1/32 steps resolution for less motor noise and smoother control, with a built-in Advanced Dynamic Mixed Decay (ADMD) function that helps stabilize the current waveforms. Thanks to the many steps that TB67S549FTG supports, motor noise can be significantly reduced with smoother operation and more precise control. It is suited to various applications such as office automation and commercial and industrial equipment. The current value in the PWM constant-current mode is set by the reference voltage obtained by the MCP1501, a high-precision voltage regulator. Also, the current threshold point of the TB67S549FTG, alongside MCP1501, can be set manually using an onboard trimmer labeled VR.
In addition to the I2C communication, several GPIO pins connected to the mikroBUS™ socket pins are also used to forward the information to the MCU associated with the PCA9555A port expander. The PCA9555A also allows choosing the least significant bit (LSB) of its I2C slave address by positioning SMD jumpers labeled as ADDR SEL to an appropriate position marked as 0 and 1, alongside its interrupt feature routed to the INT pin of the mikroBUS™ socket. The CLK clock signal, routed to the PWM pin of the mikroBUS™ socket, shifts the current step and electrical angle of the motor with its every up-edge, while the Enable pin, labeled as EN and routed to the CS pin of the mikroBUS™ socket, controls the state of the output A and B stepping motor drive channels. The normal constant current control is started by turning the motor drive ON (HIGH level), while by setting the motor drive OFF, the outputs are turned high impedance because the MOSFETs are set to OFF (LOW level). Besides, all circuits can be stopped using the Sleep function and thus enable power saving mode. A simple DIR pin routed to the AN pin on the mikroBUS™ socket allows MCU to manage the direction of the stepper motor (clockwise or counterclockwise), while the RST pin of the mikroBUS™ socket
initializes an electrical angle in the internal counter to set an initial position. Achieving an initial position is indicated via onboard orange LED labeled as MO. A specific addition to this Click board™ is a multifunctional switch that allows the user, by selecting a particular switch, to set appropriate features such as 1 – Sleep Mode Activation; 2, 3 – Motor Torque Setting; 5 – Decay Control; 6, 7, 8 – Step Resolution Setting. In addition to this physical way of setting these functions, the user can select them digitally via the I2C interface. The Stepper 12 Click supports an external power supply for the TB67S549FTG, which can be connected to the input terminal labeled as VM and should be within the range of 4.5V to 34V, while the stepper motor coils can be connected to the terminals labeled as B+, B-, A-, and A+. This Click board™ can operate with either 3.3V or 5V logic voltage levels selected via the VCC SEL jumper. This way, both 3.3V and 5V capable MCUs can use the communication lines properly. However, the Click board™ comes equipped with a library containing easy-to-use functions and an example code that can be used, as a reference, for further development.
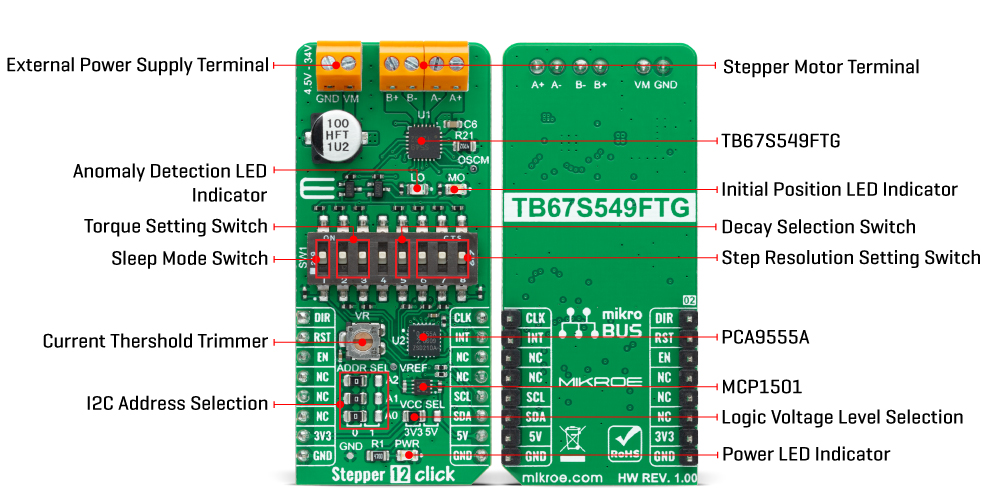
Features overview
Development board
Clicker 2 for PIC24 is a compact starter development board that brings the flexibility of add-on Click boards™ to your favorite microcontroller, making it a perfect starter kit for implementing your ideas. It comes with an onboard 16-bit PIC microcontroller, the PIC24FJ1024GB610 from Microchip, two mikroBUS™ sockets for Click board™ connectivity, a USB connector, LED indicators, buttons, a mikroProg programmer connector, and two 26-pin headers for interfacing with external electronics. Its compact design with clear and easily recognizable silkscreen markings allows you to build gadgets with unique
functionalities and features quickly. Each part of the Clicker 2 for PIC24 development kit contains the components necessary for the most efficient operation of the same board. In addition to the possibility of choosing the Clicker 2 for PIC24 programming method, using a USB HID mikroBootloader or an external mikroProg connector for PIC24 programmer, the Clicker 2 board also includes a clean and regulated power supply module for the development kit. It provides two ways of board-powering; through the USB Micro-B cable, where onboard voltage regulators provide the appropriate voltage levels to each
component on the board, or using a Li-Polymer battery via an onboard battery connector. All communication methods that mikroBUS™ itself supports are on this board, including the well-established mikroBUS™ socket, reset button, and several user-configurable buttons and LED indicators. Clicker 2 for PIC24 is an integral part of the Mikroe ecosystem, allowing you to create a new application in minutes. Natively supported by Mikroe software tools, it covers many aspects of prototyping thanks to a considerable number of different Click boards™ (over a thousand boards), the number of which is growing every day.
Microcontroller Overview
MCU Card / MCU
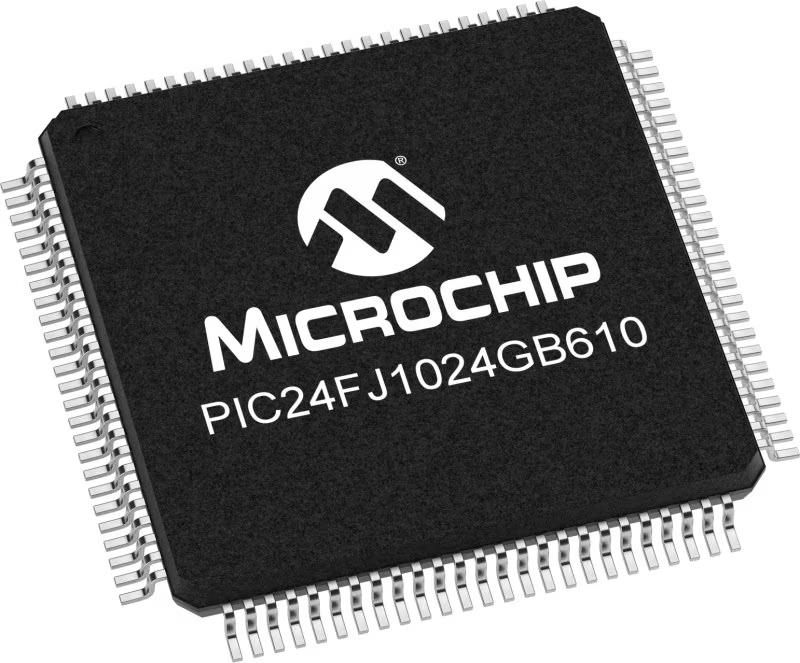
Architecture
dsPIC
MCU Memory (KB)
1024
Silicon Vendor
Microchip
Pin count
100
RAM (Bytes)
32768
Used MCU Pins
mikroBUS™ mapper
Take a closer look
Click board™ Schematic
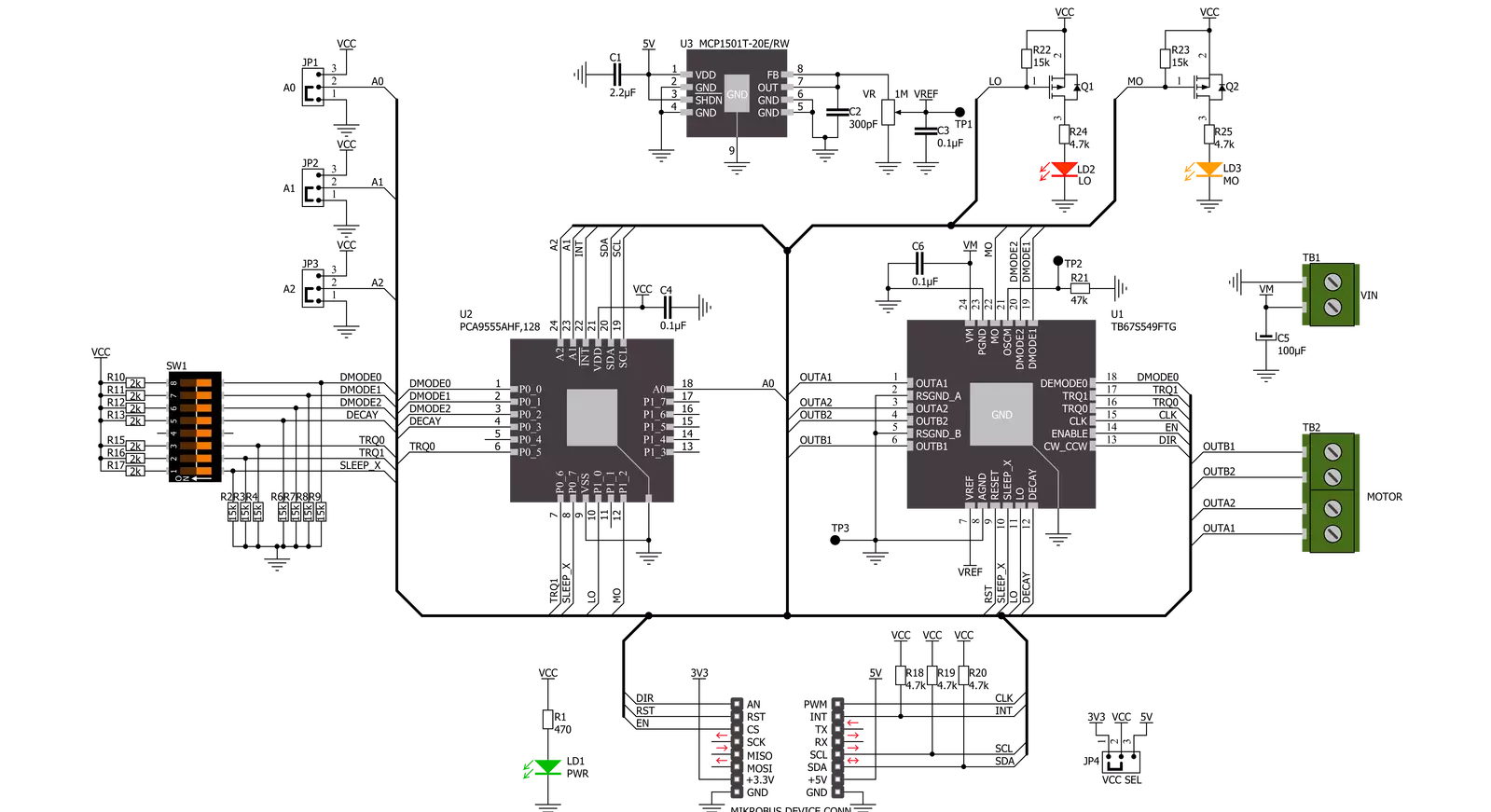
Step by step
Project assembly
Track your results in real time
Application Output
1. Application Output - In Debug mode, the 'Application Output' window enables real-time data monitoring, offering direct insight into execution results. Ensure proper data display by configuring the environment correctly using the provided tutorial.
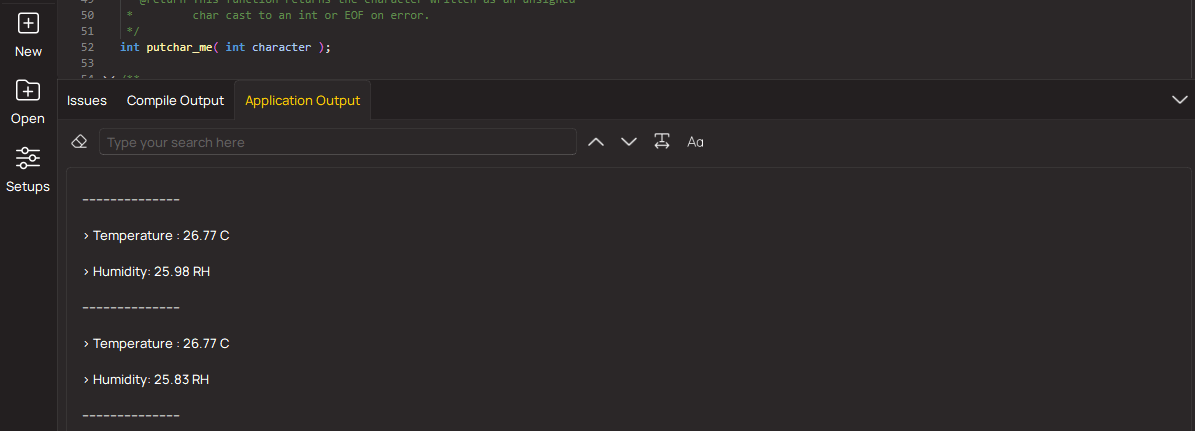
2. UART Terminal - Use the UART Terminal to monitor data transmission via a USB to UART converter, allowing direct communication between the Click board™ and your development system. Configure the baud rate and other serial settings according to your project's requirements to ensure proper functionality. For step-by-step setup instructions, refer to the provided tutorial.
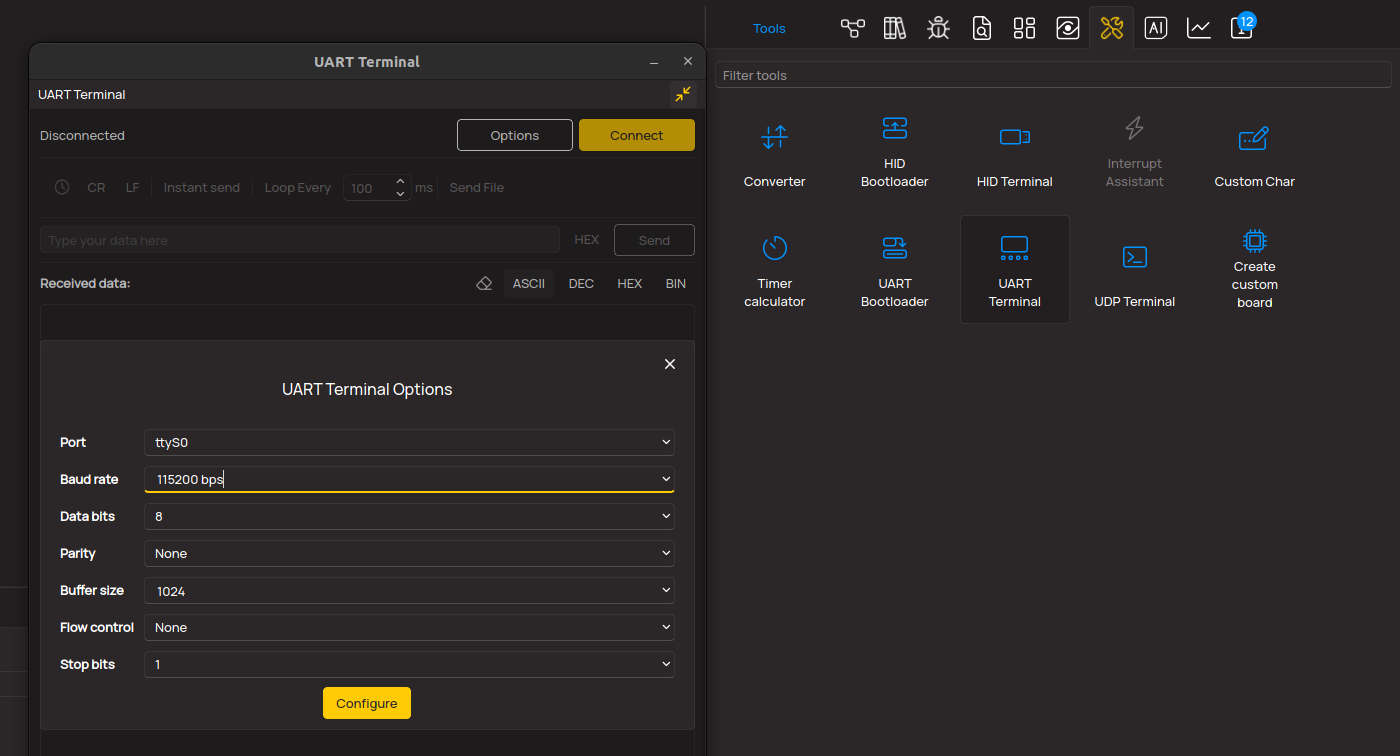
3. Plot Output - The Plot feature offers a powerful way to visualize real-time sensor data, enabling trend analysis, debugging, and comparison of multiple data points. To set it up correctly, follow the provided tutorial, which includes a step-by-step example of using the Plot feature to display Click board™ readings. To use the Plot feature in your code, use the function: plot(*insert_graph_name*, variable_name);. This is a general format, and it is up to the user to replace 'insert_graph_name' with the actual graph name and 'variable_name' with the parameter to be displayed.
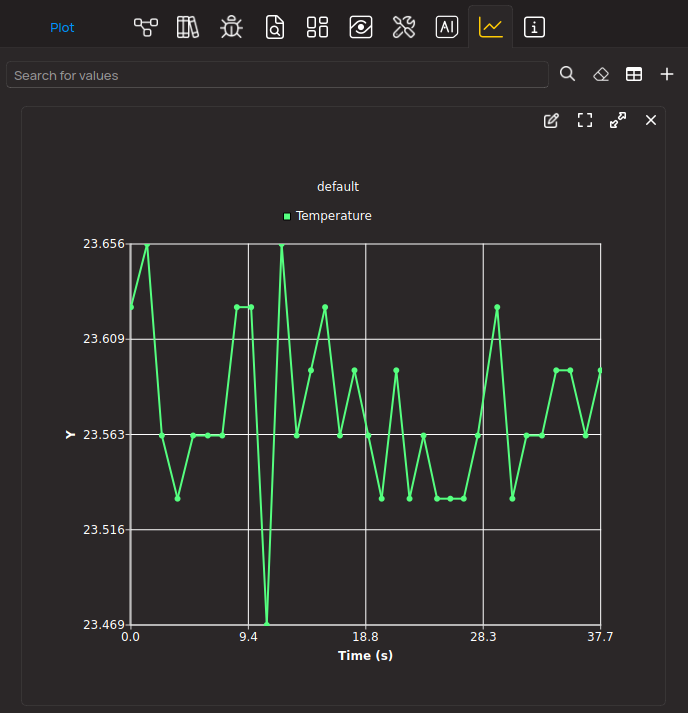
Software Support
Library Description
This library contains API for Stepper 12 Click driver.
Key functions:
stepper12_set_direction
This function sets the motor direction by setting the DIR pin logic state.stepper12_drive_motor
This function drives the motor for a specific number of steps at the selected speed.stepper12_set_step_mode
This function sets the step mode resolution settings.
Open Source
Code example
The complete application code and a ready-to-use project are available through the NECTO Studio Package Manager for direct installation in the NECTO Studio. The application code can also be found on the MIKROE GitHub account.
/*!
* @file main.c
* @brief Stepper 12 Click example
*
* # Description
* This example demonstrates the use of the Stepper 12 click board by driving the
* motor in both directions for a desired number of steps.
*
* The demo application is composed of two sections :
*
* ## Application Init
* Initializes the driver and performs the click default configuration.
*
* ## Application Task
* Drives the motor clockwise for 200 full steps and then counter-clockiwse for 400 quarter
* steps with 2 seconds delay before changing the direction. All data is being logged on
* the USB UART where you can track the program flow.
*
* @author Stefan Filipovic
*
*/
#include "board.h"
#include "log.h"
#include "stepper12.h"
static stepper12_t stepper12;
static log_t logger;
void application_init ( void )
{
log_cfg_t log_cfg; /**< Logger config object. */
stepper12_cfg_t stepper12_cfg; /**< Click config object. */
/**
* Logger initialization.
* Default baud rate: 115200
* Default log level: LOG_LEVEL_DEBUG
* @note If USB_UART_RX and USB_UART_TX
* are defined as HAL_PIN_NC, you will
* need to define them manually for log to work.
* See @b LOG_MAP_USB_UART macro definition for detailed explanation.
*/
LOG_MAP_USB_UART( log_cfg );
log_init( &logger, &log_cfg );
log_info( &logger, " Application Init " );
// Click initialization.
stepper12_cfg_setup( &stepper12_cfg );
STEPPER12_MAP_MIKROBUS( stepper12_cfg, MIKROBUS_1 );
if ( I2C_MASTER_ERROR == stepper12_init( &stepper12, &stepper12_cfg ) )
{
log_error( &logger, " Communication init." );
for ( ; ; );
}
if ( STEPPER12_ERROR == stepper12_default_cfg ( &stepper12 ) )
{
log_error( &logger, " Default configuration." );
for ( ; ; );
}
log_info( &logger, " Application Task " );
}
void application_task ( void )
{
log_printf ( &logger, " Move 200 full steps clockwise \r\n\n" );
stepper12_set_step_mode ( &stepper12, STEPPER12_MODE_FULL_STEP );
stepper12_set_direction ( &stepper12, STEPPER12_DIR_CW );
stepper12_drive_motor ( &stepper12, 200, STEPPER12_SPEED_FAST );
Delay_ms ( 2000 );
log_printf ( &logger, " Move 400 quarter steps counter-clockwise \r\n\n" );
stepper12_set_step_mode ( &stepper12, STEPPER12_MODE_QUARTER_STEP );
stepper12_set_direction ( &stepper12, STEPPER12_DIR_CCW );
stepper12_drive_motor ( &stepper12, 400, STEPPER12_SPEED_FAST );
Delay_ms ( 2000 );
}
void main ( void )
{
application_init( );
for ( ; ; )
{
application_task( );
}
}
// ------------------------------------------------------------------------ END