Enhance your solution by incorporating an advanced health monitoring feature that offers real-time heart rate and blood oxygen saturation data
A
A
Hardware Overview
How does it work?
Oximeter 2 Click is based on the ADPD144RI, a highly integrated, photometric front end optimized for photoplethysmography (PPG) detection of blood oxygenation from Analog Devices. It combines highly efficient red and infrared LED emitters, with 660nm red and 880nm IR wavelengths, and a sensitive 4-channel photodiode with a custom ASIC that provides optical isolation between the integrated LED emitters and the detection photodiodes to improve the signal-to-noise ratio. It uses synchronous detection of optical pulses to enhance the rejection of ambient light in addition to low power consumption. The Oximeter 2 Click is designed for ultralow direct optical reflections, with independent AFE settings per channel and I2C control interface. The integrated LED emitters produce light
pulses in sync with the active sampling period of the AFE, which consists of a programmable TIA, a band-pass filter, and an integrator. The processed analog signals are digitized by a 14-bit ADC and summed by the 20-bit burst accumulator. Four simultaneous sampling channels are matrixed into two independent time slots (one for each LED wavelength). An adjustable number of pulses per sample, accumulation, and averaging can be applied to multiple samples to increase the dynamic range to 27 bits. Oximeter 2 Click communicates with MCU using the standard I2C 2-Wire interface, with a typical clock frequency of 400kHz. A high-speed I2C interface reads data from output registers directly or through a FIFO buffer. All register writes are single words only and
require 16 bits of data. It also comes with a programmable interrupt line, labeled as INT and routed on the INT pin of the mikroBUS™ socket that simplifies timely data access. The ADPD144RI does not require a specific Power-Up sequence but requires a supply voltage of 1.8V to work properly. Therefore, a small regulating LDO, the ADP160 from Analog Devices, provides a 1.8V out of 3.3V mikroBUS™ rail. This Click board™ can only be operated with a 3.3V logic voltage level. The board must perform appropriate logic voltage level conversion before using MCUs with different logic levels. However, the Click board™ comes equipped with a library containing functions and an example code that can be used as a reference for further development.
Features overview
Development board
Clicker 2 for Kinetis is a compact starter development board that brings the flexibility of add-on Click boards™ to your favorite microcontroller, making it a perfect starter kit for implementing your ideas. It comes with an onboard 32-bit ARM Cortex-M4F microcontroller, the MK64FN1M0VDC12 from NXP Semiconductors, two mikroBUS™ sockets for Click board™ connectivity, a USB connector, LED indicators, buttons, a JTAG programmer connector, and two 26-pin headers for interfacing with external electronics. Its compact design with clear and easily recognizable silkscreen markings allows you to build gadgets with unique functionalities and
features quickly. Each part of the Clicker 2 for Kinetis development kit contains the components necessary for the most efficient operation of the same board. In addition to the possibility of choosing the Clicker 2 for Kinetis programming method, using a USB HID mikroBootloader or an external mikroProg connector for Kinetis programmer, the Clicker 2 board also includes a clean and regulated power supply module for the development kit. It provides two ways of board-powering; through the USB Micro-B cable, where onboard voltage regulators provide the appropriate voltage levels to each component on the board, or
using a Li-Polymer battery via an onboard battery connector. All communication methods that mikroBUS™ itself supports are on this board, including the well-established mikroBUS™ socket, reset button, and several user-configurable buttons and LED indicators. Clicker 2 for Kinetis is an integral part of the Mikroe ecosystem, allowing you to create a new application in minutes. Natively supported by Mikroe software tools, it covers many aspects of prototyping thanks to a considerable number of different Click boards™ (over a thousand boards), the number of which is growing every day.
Microcontroller Overview
MCU Card / MCU
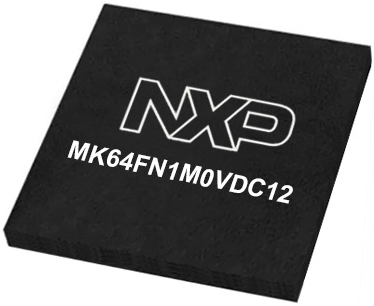
Architecture
ARM Cortex-M4
MCU Memory (KB)
1024
Silicon Vendor
NXP
Pin count
121
RAM (Bytes)
262144
Used MCU Pins
mikroBUS™ mapper
Take a closer look
Click board™ Schematic
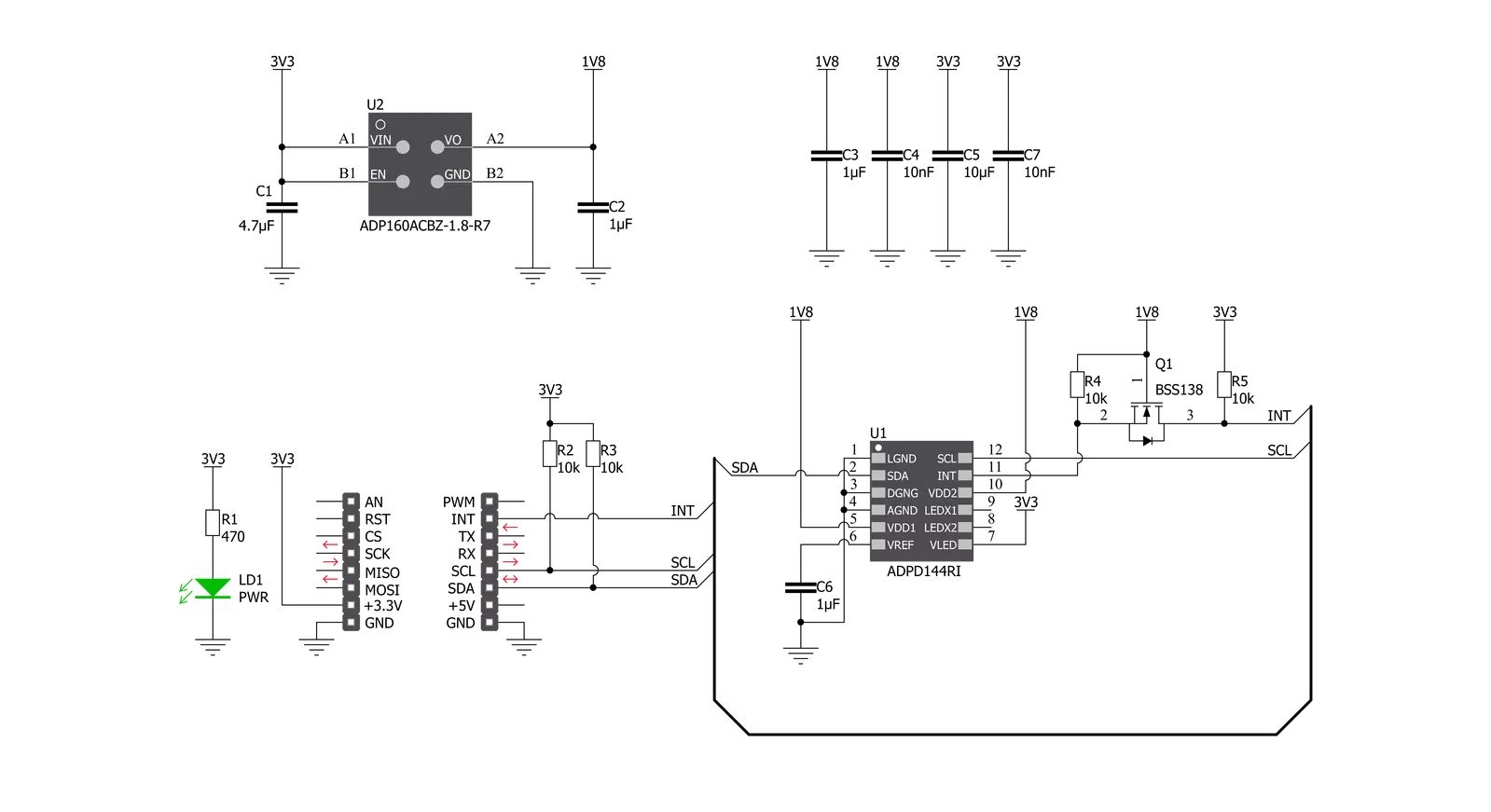
Step by step
Project assembly
Track your results in real time
Application Output
1. Application Output - In Debug mode, the 'Application Output' window enables real-time data monitoring, offering direct insight into execution results. Ensure proper data display by configuring the environment correctly using the provided tutorial.
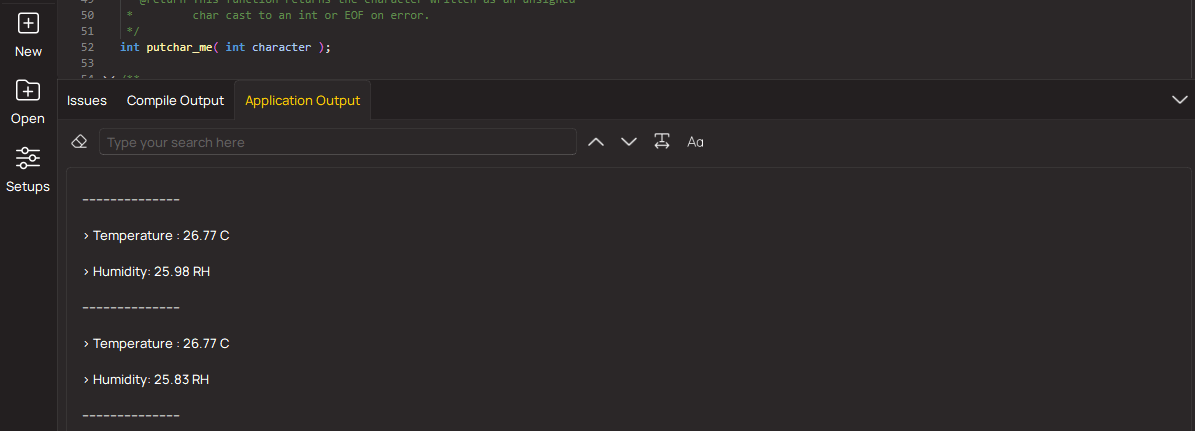
2. UART Terminal - Use the UART Terminal to monitor data transmission via a USB to UART converter, allowing direct communication between the Click board™ and your development system. Configure the baud rate and other serial settings according to your project's requirements to ensure proper functionality. For step-by-step setup instructions, refer to the provided tutorial.
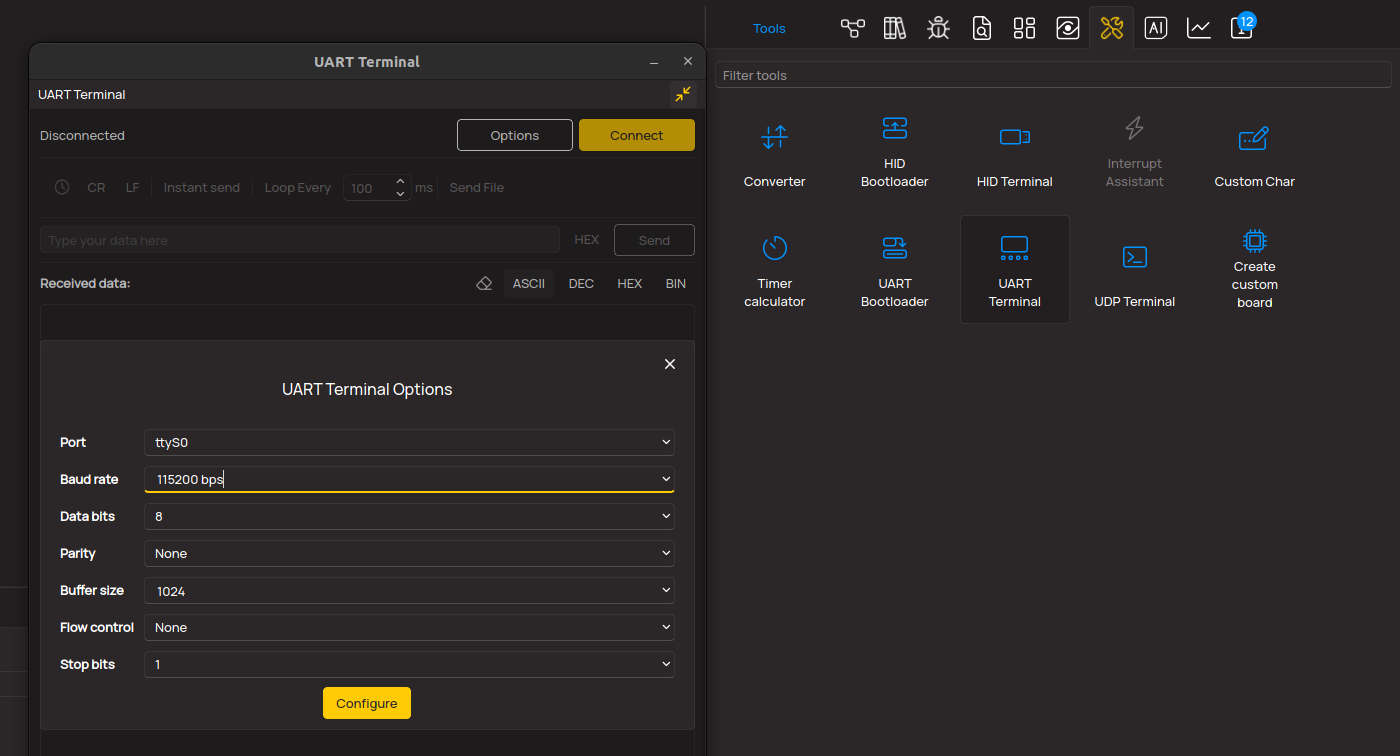
3. Plot Output - The Plot feature offers a powerful way to visualize real-time sensor data, enabling trend analysis, debugging, and comparison of multiple data points. To set it up correctly, follow the provided tutorial, which includes a step-by-step example of using the Plot feature to display Click board™ readings. To use the Plot feature in your code, use the function: plot(*insert_graph_name*, variable_name);. This is a general format, and it is up to the user to replace 'insert_graph_name' with the actual graph name and 'variable_name' with the parameter to be displayed.
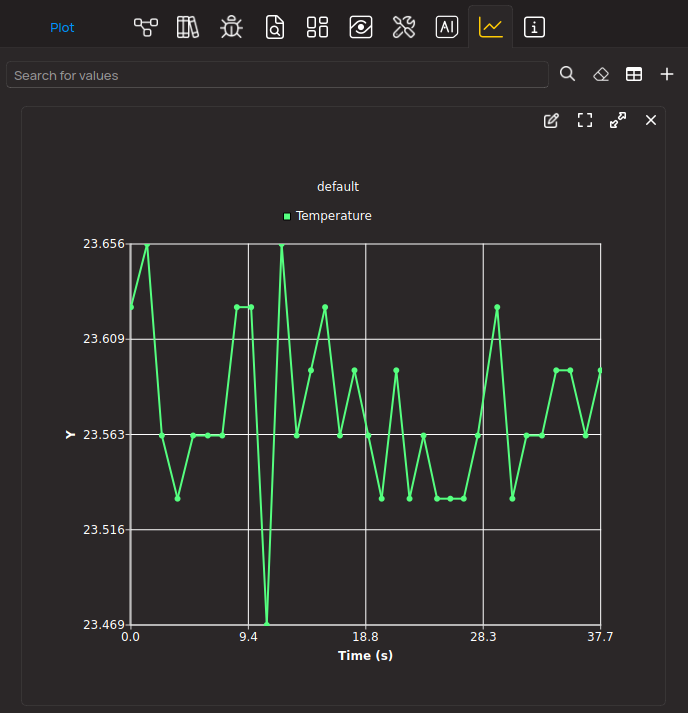
Software Support
Library Description
This library contains API for Oximeter 2 Click driver.
Key functions:
void oximeter2_cfg_setup ( oximeter2_cfg_t *cfg );
- Config Object Initialization function.OXIMETER2_RETVAL oximeter2_init ( oximeter2_t *ctx, oximeter2_cfg_t *cfg );
- Initialization function.
Open Source
Code example
The complete application code and a ready-to-use project are available through the NECTO Studio Package Manager for direct installation in the NECTO Studio. The application code can also be found on the MIKROE GitHub account.
/*!
* \file main.c
* \brief Oximeter2 Click example
*
* # Description
* This application collects data from the sensor, calculates it and then logs
* the result.
*
* The demo application is composed of two sections :
*
* ## Application Init
* Initializes driver and performs the device configuration which puts Time Slot A
* and Time Slot B modes to active state.
* Before the device configuration, the SW reset will be performed, which puts
* the registers in their initial state.
*
* ## Application Task
* Application measures value of oxygen level in human's blood.
*
*
* \author MikroE Team
*
*/
// ------------------------------------------------------------------- INCLUDES
#include "board.h"
#include "log.h"
#include "oximeter2.h"
// ------------------------------------------------------------------ VARIABLES
// Oximeter 2 context instance declaration.
static oximeter2_t oximeter2;
// Logger context instance declaration.
static log_t logger;
// Result storage.
static uint32_t res_slot[ 100 ];
// ------------------------------------------------------ APPLICATION FUNCTIONS
void oximeter2_write_res ( uint32_t data_write )
{
log_printf( &logger, "%u\r\n", data_write );
}
void oximeter2_logs_results( void )
{
uint8_t final_result;
oximeter2_read_data( &oximeter2, &res_slot[ 0 ] );
log_printf( &logger, "Average result per photodiode is: \r\n" );
switch ( oximeter2.enabled_channel )
{
case OXIMETER2_CH3_CH4_SELECTED:
{
log_printf( &logger, "PD3: " );
oximeter2_write_res( res_slot[ 2 ] );
log_printf( &logger, "PD4: " );
oximeter2_write_res( res_slot[ 3 ] );
final_result = ( res_slot[ 2 ] + res_slot[ 3 ] ) / 1000;
break;
}
case OXIMETER2_ALL_CHANNELS_SELECTED:
{
log_printf( &logger, "PD1: " );
oximeter2_write_res( res_slot[ 0 ] );
log_printf( &logger, "PD2: " );
oximeter2_write_res( res_slot[ 1 ] );
log_printf( &logger, "PD3: " );
oximeter2_write_res( res_slot[ 2 ] );
log_printf( &logger, "PD4: " );
oximeter2_write_res( res_slot[ 3 ]);
final_result = ( res_slot[ 0 ] + res_slot [ 1 ] + res_slot[ 2 ] + res_slot[ 3 ] ) / 1000;
break;
}
default:
{
break;
}
}
if (final_result > 100)
{
final_result = 100;
}
log_printf( &logger, "Average result, in percentage: %u\r\n", ( uint16_t )final_result );
log_printf( &logger, "-------------------------\r\n" );
Delay_ms ( 300 );
}
void application_init ( void )
{
log_cfg_t log_cfg;
oximeter2_cfg_t cfg;
/**
* Logger initialization.
* Default baud rate: 115200
* Default log level: LOG_LEVEL_DEBUG
* @note If USB_UART_RX and USB_UART_TX
* are defined as HAL_PIN_NC, you will
* need to define them manually for log to work.
* See @b LOG_MAP_USB_UART macro definition for detailed explanation.
*/
LOG_MAP_USB_UART( log_cfg );
log_init( &logger, &log_cfg );
log_info( &logger, "---- Application Init ----" );
// Click initialization.
oximeter2_cfg_setup( &cfg );
OXIMETER2_MAP_MIKROBUS( cfg, MIKROBUS_1 );
oximeter2_init( &oximeter2, &cfg );
oximeter2_default_cfg( &oximeter2 );
}
void application_task ( void )
{
oximeter2_logs_results();
}
int main ( void )
{
/* Do not remove this line or clock might not be set correctly. */
#ifdef PREINIT_SUPPORTED
preinit();
#endif
application_init( );
for ( ; ; )
{
application_task( );
}
return 0;
}
// ------------------------------------------------------------------------ END