Redesign your approach to precision control by integrating our digital potentiometers, achieving unparalleled customization and stability
A
A
Hardware Overview
How does it work?
DIGI POT 4 Click is based on the MAX5494, a 10-bit dual, non-volatile, linear taper digital potentiometer from Analog Devices. This IC consists of the control logic and a resistors stream (i.e., 1024 equal resistors serially connected) through which the wiper moves. The end-to-end resistance of the resistors on the used IC is 10KΩ. The wiper movement is done by writing 10-bit data into the wiper registers, resulting in 1024 discrete positions the wiper can take. All three terminals of the digital pot are routed to the IC terminals and the onboard connectors for easy and secure connection to the rest of the circuit.
The MAX5494 contains two such potentiometers routed to the click board™ screw terminals. The voltage drop may occur while switching positions depending on the output impedance to which the wiper is connected. Therefore, it is not recommended to use it as the variable resistor. After the power is on, the content of the EEPROM NV memory will be copied to the volatile RAM, used as the shift register for the wiper position. This volatile memory register directly controls the wiper position. The wiper can be positioned by writing data into this register. The EEPROM NV registers are only written if requested using the
specific write command. This way, the EEPROM lifecycle is prolonged, although it can withstand up to 200000 read/write cycles. All the communication with the control logic of the MAX5494 is done through the SPI, so all the SPI signals are routed to the appropriate mikroBUS™ pins. The CS pin is held high, preventing the SPI communication, so as always - to initialize the SPI communication, the CS pin needs to be pulled LOW by the MCU. Besides two connectors used to connect the potentiometer terminals, the click board™ is equipped with the SMD jumper to choose between the 3.3V or 5V operating voltage.
Features overview
Development board
Fusion for TIVA v8 is a development board specially designed for the needs of rapid development of embedded applications. It supports a wide range of microcontrollers, such as different 32-bit ARM® Cortex®-M based MCUs from Texas Instruments, regardless of their number of pins, and a broad set of unique functions, such as the first-ever embedded debugger/programmer over a WiFi network. The development board is well organized and designed so that the end-user has all the necessary elements, such as switches, buttons, indicators, connectors, and others, in one place. Thanks to innovative manufacturing technology, Fusion for TIVA v8 provides a fluid and immersive working experience, allowing access
anywhere and under any circumstances at any time. Each part of the Fusion for TIVA v8 development board contains the components necessary for the most efficient operation of the same board. An advanced integrated CODEGRIP programmer/debugger module offers many valuable programming/debugging options, including support for JTAG, SWD, and SWO Trace (Single Wire Output)), and seamless integration with the Mikroe software environment. Besides, it also includes a clean and regulated power supply module for the development board. It can use a wide range of external power sources, including a battery, an external 12V power supply, and a power source via the USB Type-C (USB-C) connector.
Communication options such as USB-UART, USB HOST/DEVICE, CAN (on the MCU card, if supported), and Ethernet is also included. In addition, it also has the well-established mikroBUS™ standard, a standardized socket for the MCU card (SiBRAIN standard), and two display options for the TFT board line of products and character-based LCD. Fusion for TIVA v8 is an integral part of the Mikroe ecosystem for rapid development. Natively supported by Mikroe software tools, it covers many aspects of prototyping and development thanks to a considerable number of different Click boards™ (over a thousand boards), the number of which is growing every day.
Microcontroller Overview
MCU Card / MCU
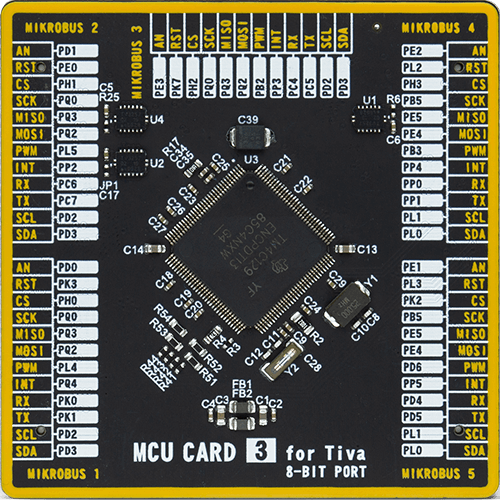
Type
8th Generation
Architecture
ARM Cortex-M4
MCU Memory (KB)
512
Silicon Vendor
Texas Instruments
Pin count
128
RAM (Bytes)
262144
Used MCU Pins
mikroBUS™ mapper
Take a closer look
Click board™ Schematic
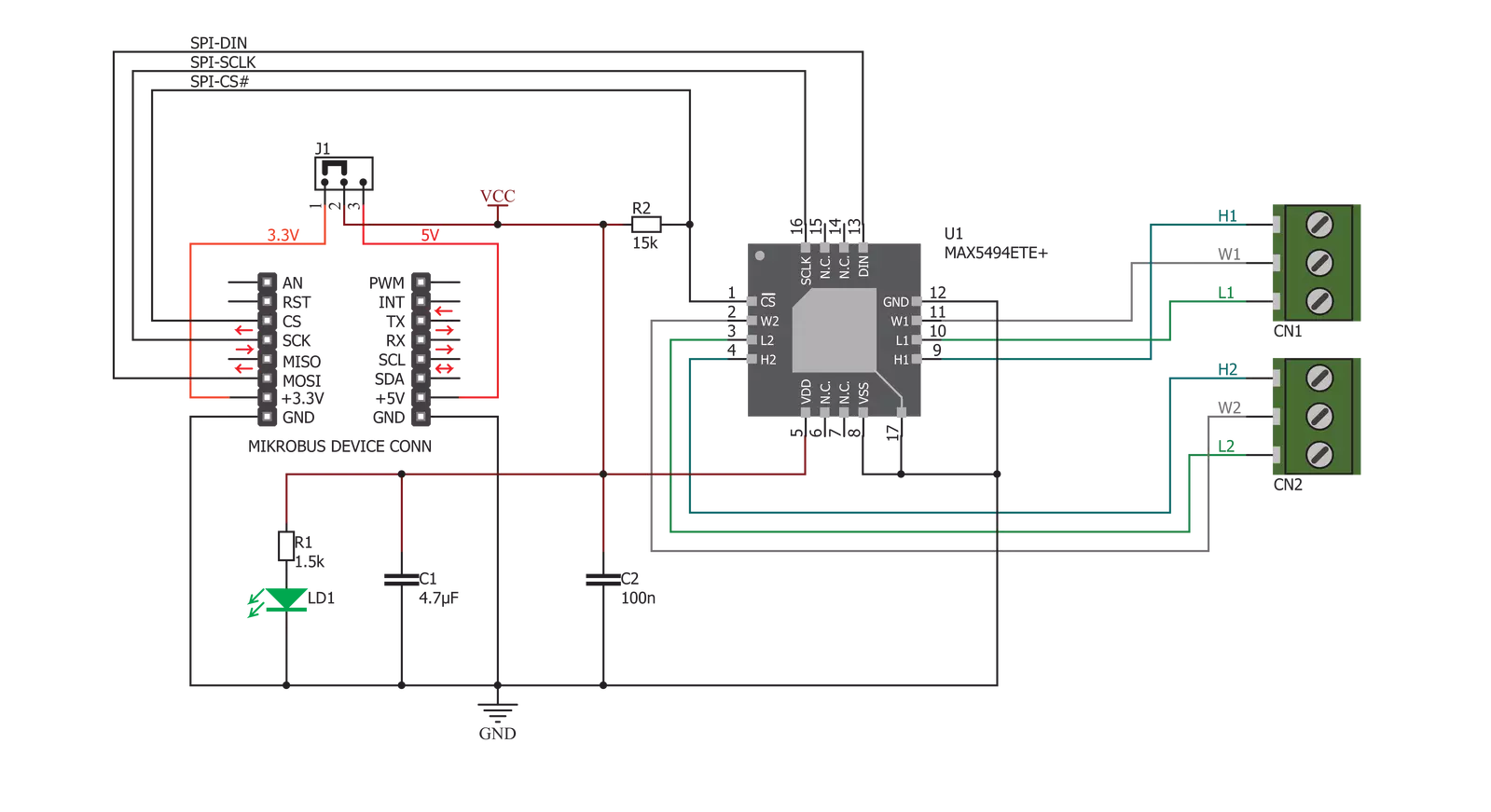
Step by step
Project assembly
Track your results in real time
Application Output
1. Application Output - In Debug mode, the 'Application Output' window enables real-time data monitoring, offering direct insight into execution results. Ensure proper data display by configuring the environment correctly using the provided tutorial.
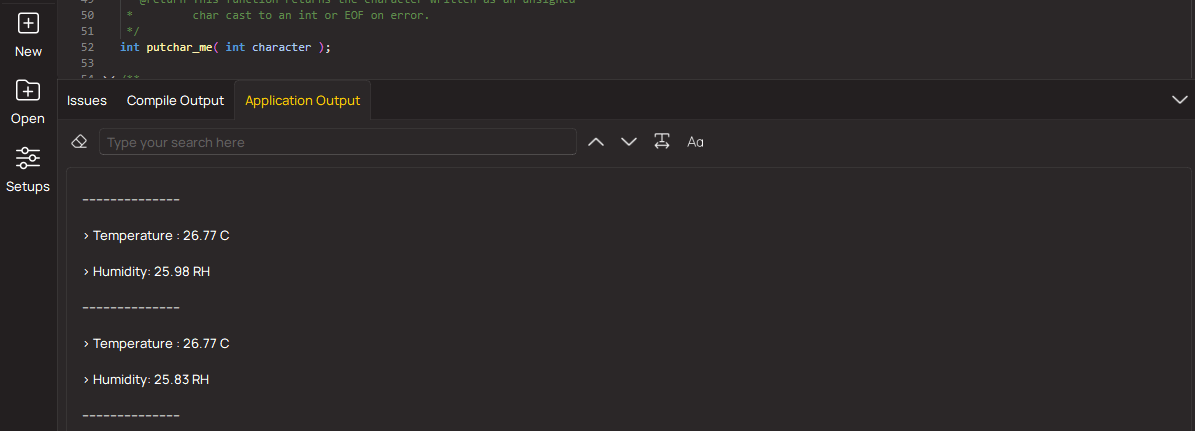
2. UART Terminal - Use the UART Terminal to monitor data transmission via a USB to UART converter, allowing direct communication between the Click board™ and your development system. Configure the baud rate and other serial settings according to your project's requirements to ensure proper functionality. For step-by-step setup instructions, refer to the provided tutorial.
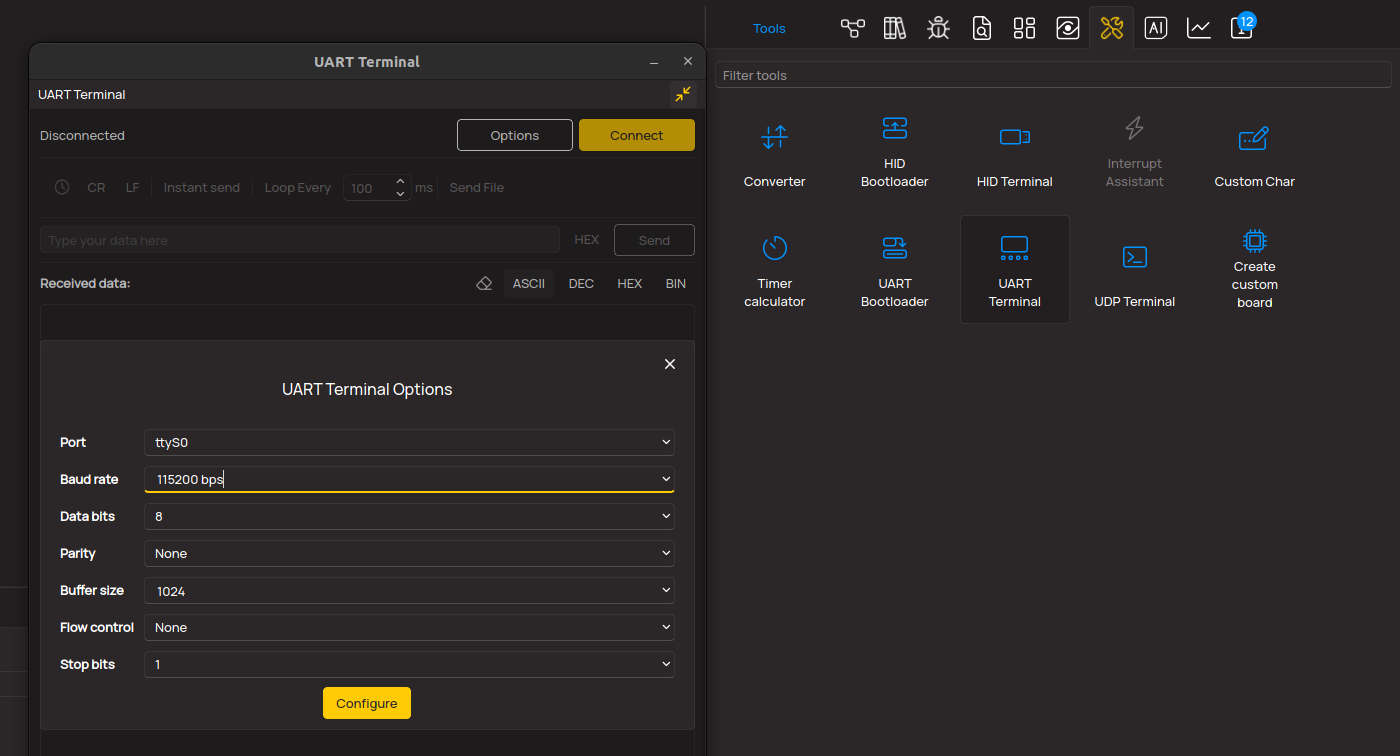
3. Plot Output - The Plot feature offers a powerful way to visualize real-time sensor data, enabling trend analysis, debugging, and comparison of multiple data points. To set it up correctly, follow the provided tutorial, which includes a step-by-step example of using the Plot feature to display Click board™ readings. To use the Plot feature in your code, use the function: plot(*insert_graph_name*, variable_name);. This is a general format, and it is up to the user to replace 'insert_graph_name' with the actual graph name and 'variable_name' with the parameter to be displayed.
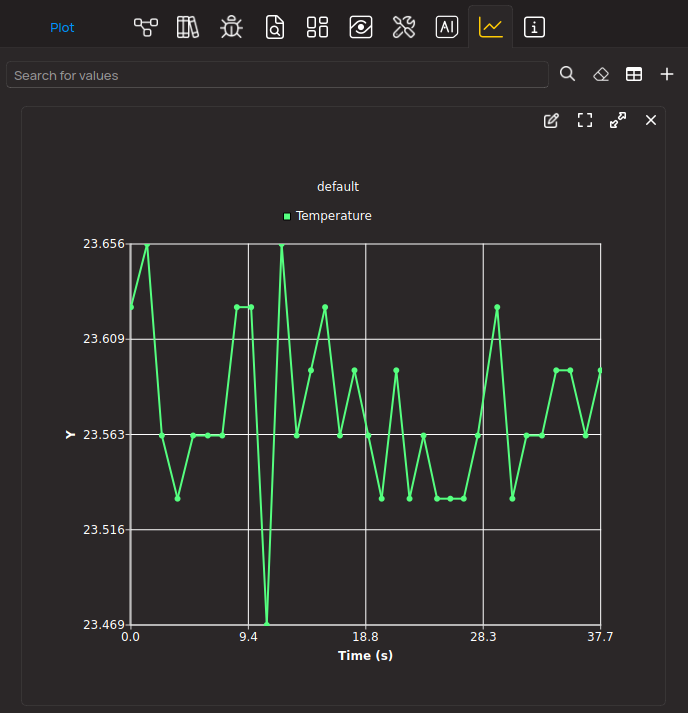
Software Support
Library Description
This library contains API for DIGI POT 4 Click driver.
Key functions:
digipot4_write_reg
- This function writes data in wiper register and NV registerdigipot4_copy_reg
- This function is used to copy the data from the wipers to the NV memory and from the NV memory it wipers
Open Source
Code example
The complete application code and a ready-to-use project are available through the NECTO Studio Package Manager for direct installation in the NECTO Studio. The application code can also be found on the MIKROE GitHub account.
/*!
* \file
* \brief DigiPot4 Click example
*
* # Description
* This application is a digitally controlled dual potentiometer.
*
* The demo application is composed of two sections :
*
* ## Application Init
* Driver intialization
*
* ## Application Task
* Set the wiper position.
*
* \author MikroE Team
*
*/
// ------------------------------------------------------------------- INCLUDES
#include "board.h"
#include "log.h"
#include "digipot4.h"
// ------------------------------------------------------------------ VARIABLES
static digipot4_t digipot4;
static log_t logger;
// ------------------------------------------------------ APPLICATION FUNCTIONS
void application_init ( void )
{
log_cfg_t log_cfg;
digipot4_cfg_t cfg;
/**
* Logger initialization.
* Default baud rate: 115200
* Default log level: LOG_LEVEL_DEBUG
* @note If USB_UART_RX and USB_UART_TX
* are defined as HAL_PIN_NC, you will
* need to define them manually for log to work.
* See @b LOG_MAP_USB_UART macro definition for detailed explanation.
*/
LOG_MAP_USB_UART( log_cfg );
log_init( &logger, &log_cfg );
log_info( &logger, "---- Application Init ----" );
// Click initialization.
digipot4_cfg_setup( &cfg );
DIGIPOT4_MAP_MIKROBUS( cfg, MIKROBUS_1 );
digipot4_init( &digipot4, &cfg );
}
void application_task ( void )
{
// Task implementation.
digipot4_write_reg( &digipot4, DIGIPOT4_WIPER_REG_1, 0 );
digipot4_write_reg( &digipot4, DIGIPOT4_WIPER_REG_2, 0 );
Delay_1sec( );
digipot4_write_reg( &digipot4, DIGIPOT4_WIPER_REG_1, 512 );
digipot4_write_reg( &digipot4, DIGIPOT4_WIPER_REG_2, 512 );
Delay_1sec( );
digipot4_write_reg( &digipot4, DIGIPOT4_WIPER_REG_1, 1023 );
digipot4_write_reg( &digipot4, DIGIPOT4_WIPER_REG_2, 1023 );
Delay_1sec( );
}
int main ( void )
{
/* Do not remove this line or clock might not be set correctly. */
#ifdef PREINIT_SUPPORTED
preinit();
#endif
application_init( );
for ( ; ; )
{
application_task( );
}
return 0;
}
// ------------------------------------------------------------------------ END