Develop top-of-the-line alcohol breath tester and early fire and gas leakage detection applications easily
A
A
Hardware Overview
How does it work?
Alcohol 3 Click is based on the MiCS-5524 sensor, a compact MOS sensor from SGX Sensortech. This sensor comprises a micromachined metal oxide semiconductor diaphragm with an integrated heating resistor. The resistor produces heat, which catalyzes the reaction, affecting the electrical resistance of the oxide layer itself. The temperature of the heater is quite high: it ranges from 350 °C to 550 °C. After the initial preheating period, the sensor can detect gas changes in intervals below two seconds. The resistance of the MiCS-5524 sensor does not change linearly with the gas concentration, so a proper calibration must be performed before using it for absolute gas concentration measurement applications. The impedance changes the most when used with low gas concentrations. As the atmosphere gets saturated with gas, the impedance changes slowly. This should be considered, especially when
developing applications for estimating blood alcohol content (BAC) from a breath sample (also known as a breathalyzer). The MiCS-5524 sensor is a simple device: it has only four connections. Two pins are the connections of the internal heating element, while the other two are the MOS sensor connections. The application is reduced to calculating a proper resistor for the voltage divider. The datasheet of the MiCS-5524 sensor offers typical values for its resistance when used in clean air (artificial conditions). The sensitivity is then expressed as the ratio between the sensor's resistance in clean air and resistance at a concentration of 60 ppm CO. The middle tap between the sensor (as a resistor) and the fixed resistance provides an output voltage. It depends on the sensor's resistance, allowing it to be used as the input into the MCP3221, a low-power 12-bit A/D converter with an I2C interface, from Microchip.
This ADC allows the output voltage to be translated into digital information, accessed over the I2C pins on the mikroBUS™ socket. By using the power supply voltage as the voltage reference for the conversion, this ADC further reduces the complexity of the design, still offering a good conversion quality, thanks to its low noise input. Due to the sensor's inert nature, this ADC is more than fast enough, although it can provide up to 22.3ksps when operated in the I2C Fast mode. This Click board™ can operate with either 3.3V or 5V logic voltage levels selected via the VCC SEL jumper. This way, both 3.3V and 5V capable MCUs can use the communication lines properly. Also, this Click board™ comes equipped with a library containing easy-to-use functions and an example code that can be used as a reference for further development.
Features overview
Development board
Flip&Click PIC32MZ is a compact development board designed as a complete solution that brings the flexibility of add-on Click boards™ to your favorite microcontroller, making it a perfect starter kit for implementing your ideas. It comes with an onboard 32-bit PIC32MZ microcontroller, the PIC32MZ2048EFH100 from Microchip, four mikroBUS™ sockets for Click board™ connectivity, two USB connectors, LED indicators, buttons, debugger/programmer connectors, and two headers compatible with Arduino-UNO pinout. Thanks to innovative manufacturing technology,
it allows you to build gadgets with unique functionalities and features quickly. Each part of the Flip&Click PIC32MZ development kit contains the components necessary for the most efficient operation of the same board. In addition, there is the possibility of choosing the Flip&Click PIC32MZ programming method, using the chipKIT bootloader (Arduino-style development environment) or our USB HID bootloader using mikroC, mikroBasic, and mikroPascal for PIC32. This kit includes a clean and regulated power supply block through the USB Type-C (USB-C) connector. All communication
methods that mikroBUS™ itself supports are on this board, including the well-established mikroBUS™ socket, user-configurable buttons, and LED indicators. Flip&Click PIC32MZ development kit allows you to create a new application in minutes. Natively supported by Mikroe software tools, it covers many aspects of prototyping thanks to a considerable number of different Click boards™ (over a thousand boards), the number of which is growing every day.
Microcontroller Overview
MCU Card / MCU

Architecture
PIC32
MCU Memory (KB)
2048
Silicon Vendor
Microchip
Pin count
100
RAM (Bytes)
524288
Used MCU Pins
mikroBUS™ mapper
Take a closer look
Click board™ Schematic
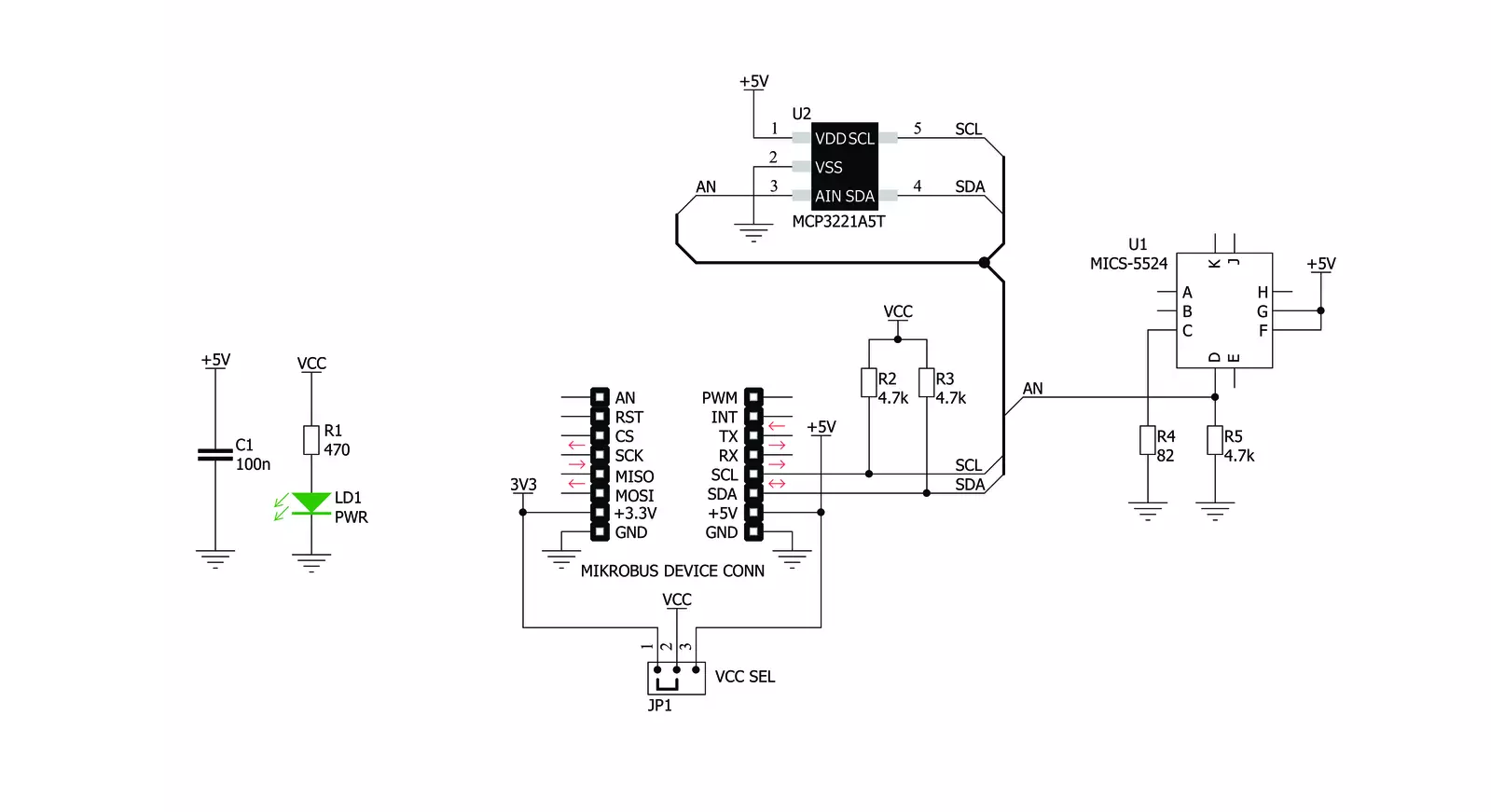
Step by step
Project assembly
Track your results in real time
Application Output
1. Application Output - In Debug mode, the 'Application Output' window enables real-time data monitoring, offering direct insight into execution results. Ensure proper data display by configuring the environment correctly using the provided tutorial.
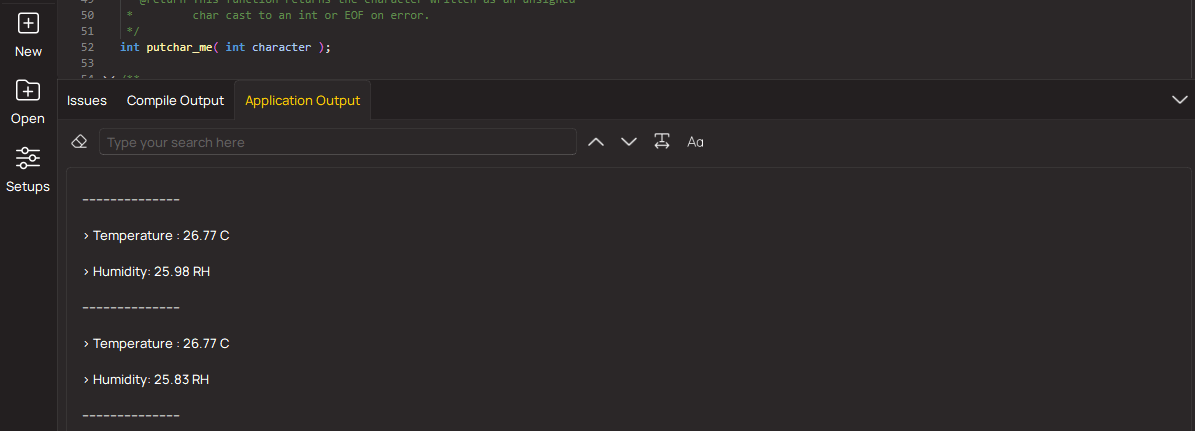
2. UART Terminal - Use the UART Terminal to monitor data transmission via a USB to UART converter, allowing direct communication between the Click board™ and your development system. Configure the baud rate and other serial settings according to your project's requirements to ensure proper functionality. For step-by-step setup instructions, refer to the provided tutorial.
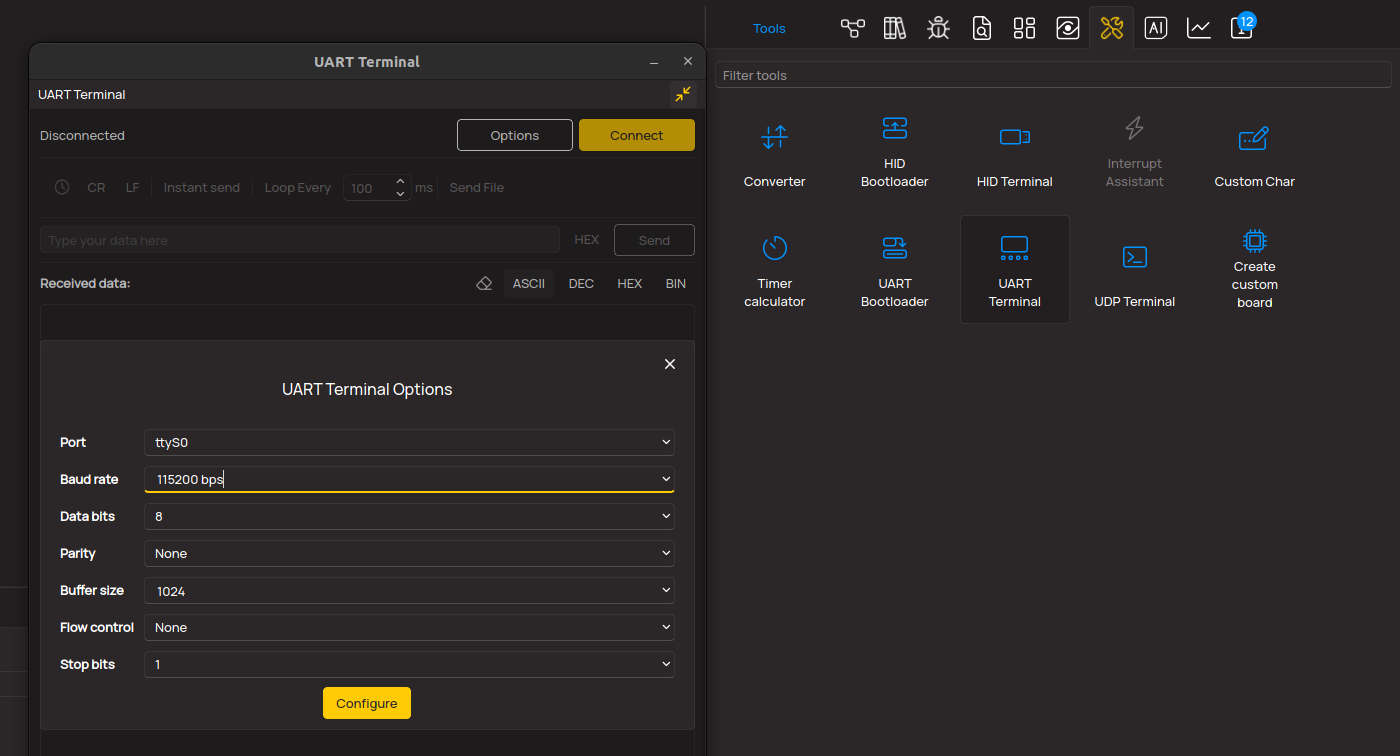
3. Plot Output - The Plot feature offers a powerful way to visualize real-time sensor data, enabling trend analysis, debugging, and comparison of multiple data points. To set it up correctly, follow the provided tutorial, which includes a step-by-step example of using the Plot feature to display Click board™ readings. To use the Plot feature in your code, use the function: plot(*insert_graph_name*, variable_name);. This is a general format, and it is up to the user to replace 'insert_graph_name' with the actual graph name and 'variable_name' with the parameter to be displayed.
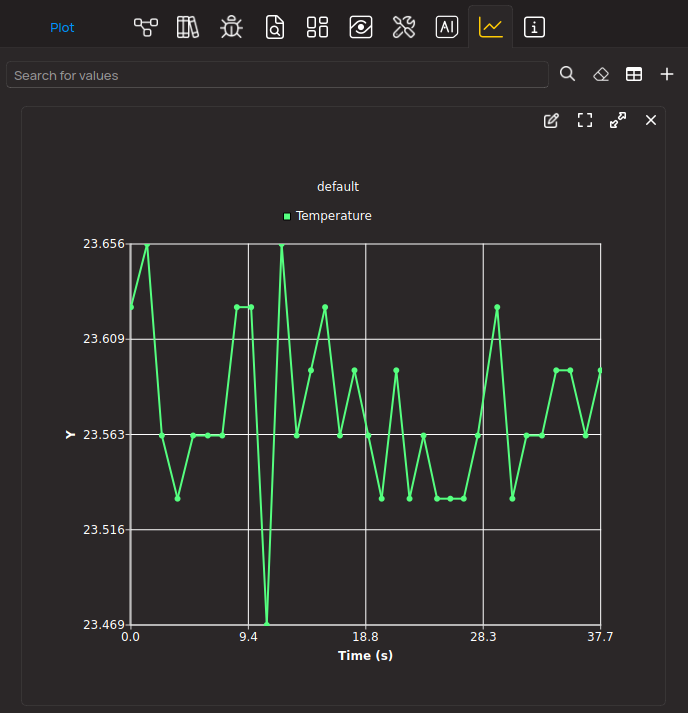
Software Support
Library Description
This library contains API for Alcohol 3 Click driver.
Key functions:
alcohol3_get_co_in_ppm
- This function reads CO (Carbon monoxide) data in ppm (1 ppm - 1000 ppm)alcohol3_get_percentage_bac
- This function reads percentage of alcohol in the blood (BAC)alcohol3_get_adc_data
- This function reads 12bit ADC value.
Open Source
Code example
The complete application code and a ready-to-use project are available through the NECTO Studio Package Manager for direct installation in the NECTO Studio. The application code can also be found on the MIKROE GitHub account.
/*!
* \file
* \brief Alcohol3 Click example
*
* # Description
* Code of this sensor reacts to the presence of deoxidizing and reducing gases,
* such as ethanol (also known as alcohol).
*
* The demo application is composed of two sections :
*
* ## Application Init
* Application Init performs Logger and Click initialization.
*
* ## Application Task
* Reads percentage of alcohol in the blood (BAC)
* and this data logs to USBUART every 1 sec.
*
* \author MikroE Team
*
*/
// ------------------------------------------------------------------- INCLUDES
#include "board.h"
#include "log.h"
#include "alcohol3.h"
// ------------------------------------------------------------------ VARIABLES
static alcohol3_t alcohol3;
static log_t logger;
// ------------------------------------------------------ APPLICATION FUNCTIONS
void application_init ( void )
{
log_cfg_t log_cfg;
alcohol3_cfg_t cfg;
/**
* Logger initialization.
* Default baud rate: 115200
* Default log level: LOG_LEVEL_DEBUG
* @note If USB_UART_RX and USB_UART_TX
* are defined as HAL_PIN_NC, you will
* need to define them manually for log to work.
* See @b LOG_MAP_USB_UART macro definition for detailed explanation.
*/
LOG_MAP_USB_UART( log_cfg );
log_init( &logger, &log_cfg );
log_info( &logger, "---- Application Init ----" );
Delay_ms ( 100 );
// Click initialization.
alcohol3_cfg_setup( &cfg );
ALCOHOL3_MAP_MIKROBUS( cfg, MIKROBUS_1 );
alcohol3_init( &alcohol3, &cfg );
log_printf( &logger, "--------------------------\r\n\n" );
log_printf( &logger, " ---- Alcohol 3 Click ----\r\n" );
log_printf( &logger, "--------------------------\r\n\n" );
Delay_ms ( 1000 );
log_printf( &logger, " ---- Initialization ---\r\n" );
log_printf( &logger, "--------------------------\r\n\n" );
Delay_ms ( 1000 );
}
void application_task ( void )
{
uint16_t co_ppm;
uint16_t p_bac;
float temp_bac;
// Task implementation.
log_printf( &logger, " --- Alcohol diagnostics ---- \r\n" );
co_ppm = alcohol3_get_co_in_ppm ( &alcohol3 );
log_printf( &logger, " co in ppm %d | \r\n", co_ppm );
temp_bac = alcohol3_get_percentage_bac( &alcohol3 );
p_bac = ( uint16_t )( temp_bac * 1000 );
if ( 10 > p_bac && p_bac < 100 )
{
log_printf( &logger, " BAC | 0.00%d\r\n", p_bac );
}
else if ( 100 <= p_bac && 1000 > p_bac )
{
log_printf( &logger, " BAC | 0.0%d\r\n", p_bac );
}
else if ( p_bac >= 1000 )
{
log_printf( &logger, " BAC | 0.%d\r\n", p_bac );
}
else
{
log_printf( &logger, " BAC | 0.0000\r\n" );
}
log_printf( &logger, " ---------------------------- \r\n" );
Delay_ms ( 1000 );
}
int main ( void )
{
/* Do not remove this line or clock might not be set correctly. */
#ifdef PREINIT_SUPPORTED
preinit();
#endif
application_init( );
for ( ; ; )
{
application_task( );
}
return 0;
}
// ------------------------------------------------------------------------ END