Best-in-class air-quality sensing solution
A
A
Hardware Overview
How does it work?
Air quality 9 Click is based on the ENS160, an indoor air quality sensor based on metal oxide (MOX) technology with four MOx sensor elements from ScioSense. This sensor has sophisticated fusion algorithms to produce measurement outputs better tuned to human occupants' natural responses. The multi-element TrueVOC™ technology, on which the ENS160 is based, is sensitive to oxidizing gases such as ozone which affect the quality of indoor air, as well as to a wide range of volatile organic compounds (VOCs) such as ethanol, toluene, as well as hydrogen and nitrogen dioxide with superior selectivity and accuracy. The ENS160 complies with worldwide Indoor Air Quality (IAQ) signal standards and is designed for high volume and reliability. For best performance, the sensor must be operated in normal indoor air at -5 to 60°C (typical: 25°C), while relative humidity ranges
from 20 to 80%RH (typical: 50%RH), non-condensing with no aggressive or poisonous gases present. Prolonged exposure to environments outside these conditions can affect the performance and lifetime of the sensor. This Click board™ allows using both I2C and SPI interfaces with a maximum frequency of 1MHz for I2C and 10MHz for SPI communication. The selection can be made by positioning SMD jumpers labeled COMM SEL appropriately. Note that all the jumpers' positions must be on the same side, or the Click board™ may become unresponsive. While the I2C interface is selected, the ENS160 allows choosing the least significant bit (LSB) of its I2C slave address using the SMD jumper labeled ADDR SEL. This Click board™ also possesses an additional interrupt signal, routed on the INT pin of the mikroBUS™ socket labeled as INT, indicating
the status of the measurement process itself. The ENS160 also requires a supply voltage of 1.8V to work regularly. Therefore, a small LDO regulator, AP2112 from Diodes Incorporated, provides a 1.8V out of mikroBUS™ 3V3 power rail. This LDO can be enabled or disabled through the EN pin routed to the PWM pin of the mikroBUS™ socket, hence, offering a switch operation to turn ON/OFF power delivery to the ENS160. This Click board™ can only be operated with a 3.3V logic voltage level. The board must perform appropriate logic voltage level conversion before using MCUs with different logic levels. However, the Click board™ comes equipped with a library containing functions and an example code that can be used as a reference for further development.
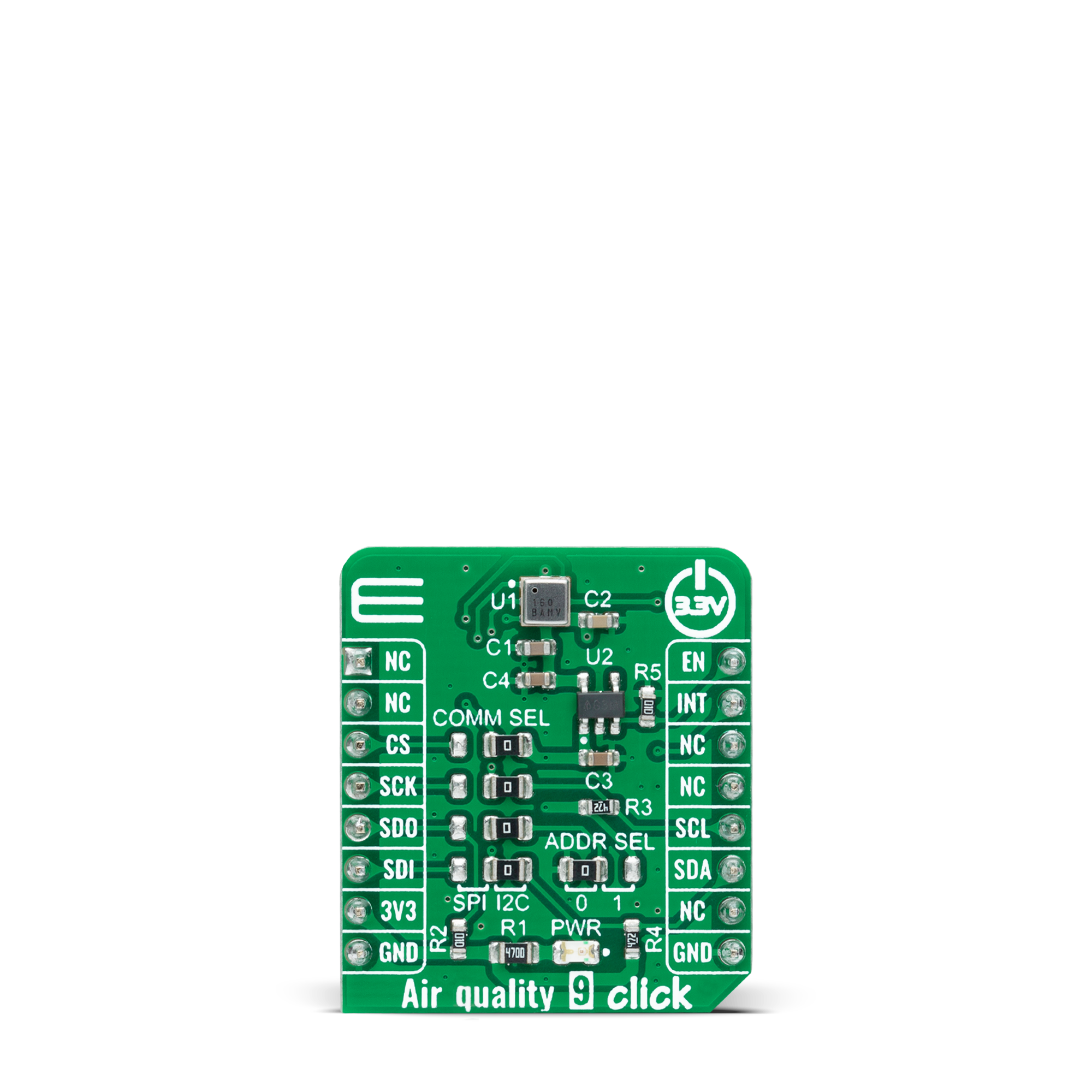
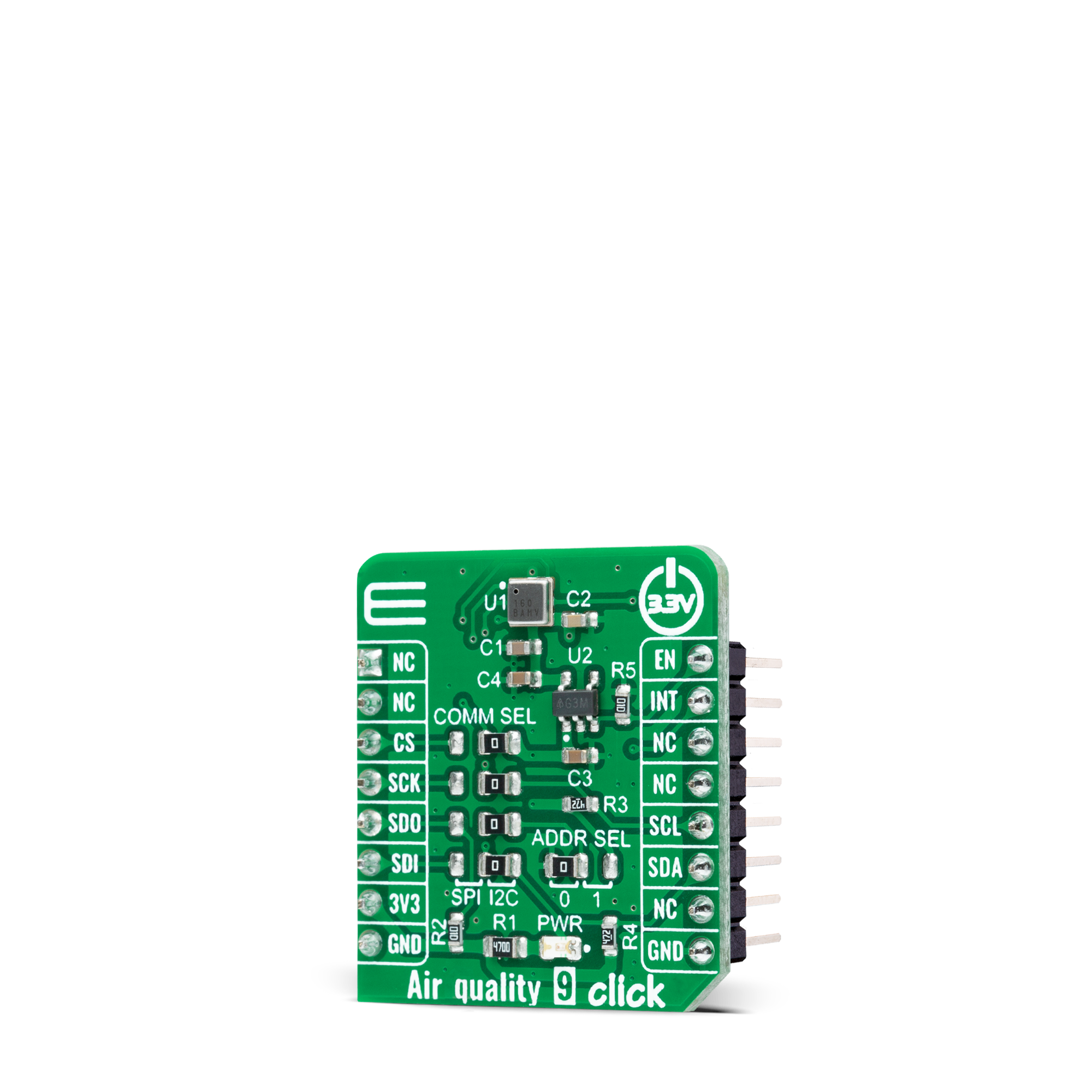
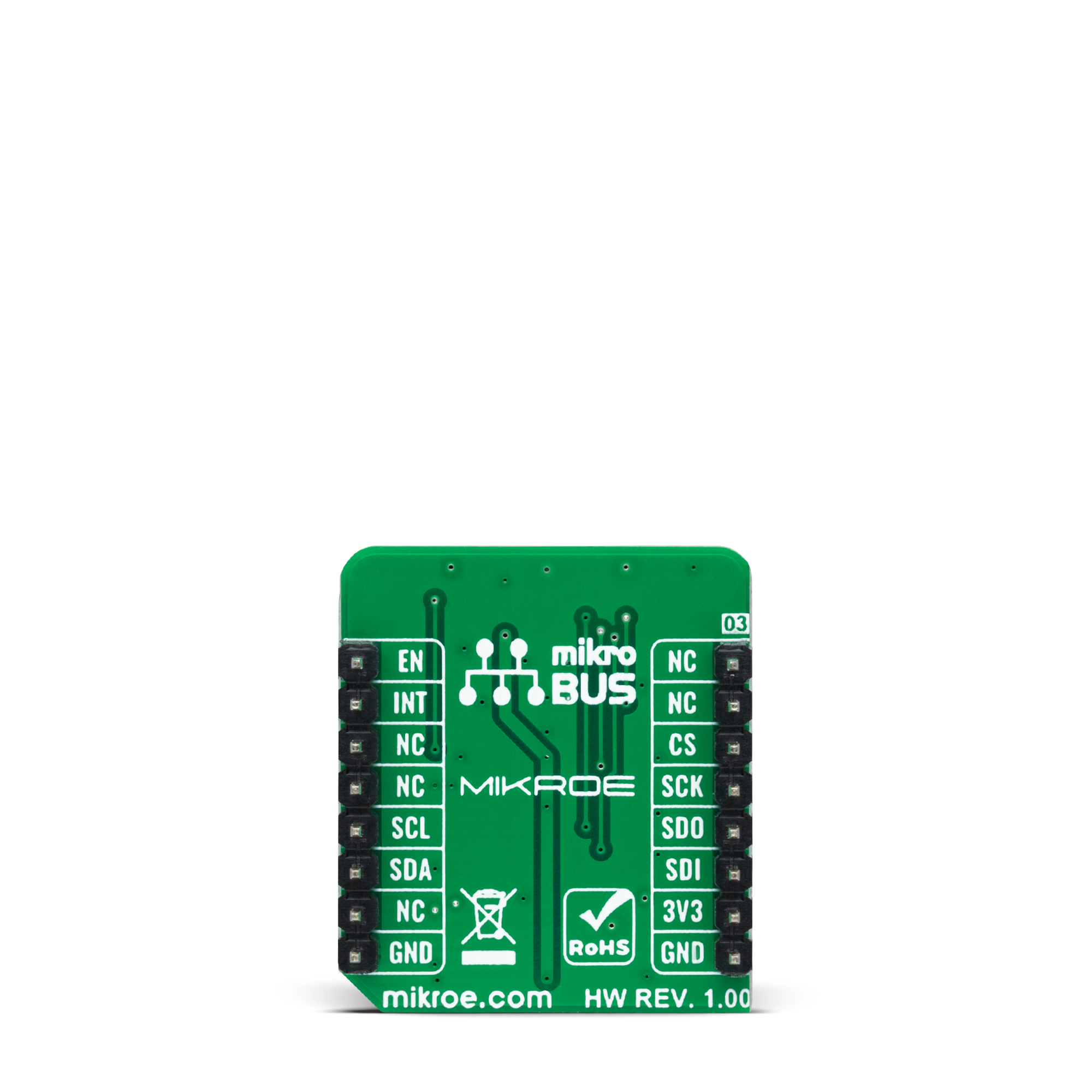
Features overview
Development board
Fusion for TIVA v8 is a development board specially designed for the needs of rapid development of embedded applications. It supports a wide range of microcontrollers, such as different 32-bit ARM® Cortex®-M based MCUs from Texas Instruments, regardless of their number of pins, and a broad set of unique functions, such as the first-ever embedded debugger/programmer over a WiFi network. The development board is well organized and designed so that the end-user has all the necessary elements, such as switches, buttons, indicators, connectors, and others, in one place. Thanks to innovative manufacturing technology, Fusion for TIVA v8 provides a fluid and immersive working experience, allowing access
anywhere and under any circumstances at any time. Each part of the Fusion for TIVA v8 development board contains the components necessary for the most efficient operation of the same board. An advanced integrated CODEGRIP programmer/debugger module offers many valuable programming/debugging options, including support for JTAG, SWD, and SWO Trace (Single Wire Output)), and seamless integration with the Mikroe software environment. Besides, it also includes a clean and regulated power supply module for the development board. It can use a wide range of external power sources, including a battery, an external 12V power supply, and a power source via the USB Type-C (USB-C) connector.
Communication options such as USB-UART, USB HOST/DEVICE, CAN (on the MCU card, if supported), and Ethernet is also included. In addition, it also has the well-established mikroBUS™ standard, a standardized socket for the MCU card (SiBRAIN standard), and two display options for the TFT board line of products and character-based LCD. Fusion for TIVA v8 is an integral part of the Mikroe ecosystem for rapid development. Natively supported by Mikroe software tools, it covers many aspects of prototyping and development thanks to a considerable number of different Click boards™ (over a thousand boards), the number of which is growing every day.
Microcontroller Overview
MCU Card / MCU
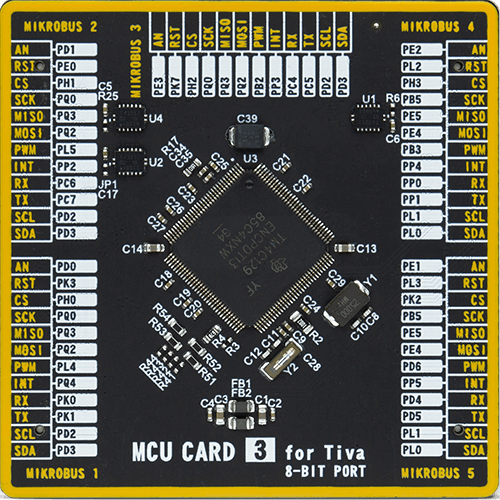
Type
8th Generation
Architecture
ARM Cortex-M4
MCU Memory (KB)
1024
Silicon Vendor
Texas Instruments
Pin count
128
RAM (Bytes)
262144
Used MCU Pins
mikroBUS™ mapper
Take a closer look
Click board™ Schematic
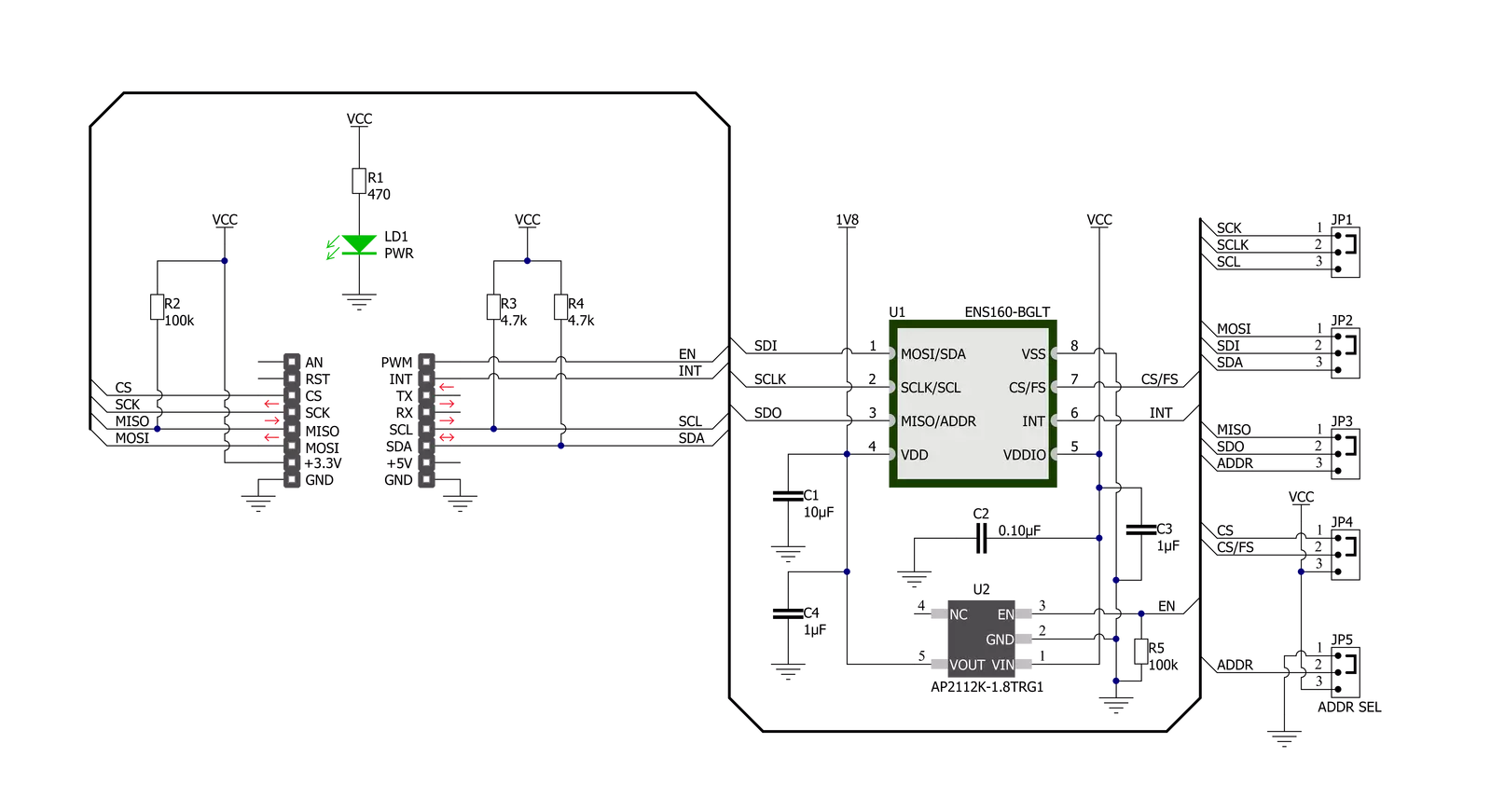
Step by step
Project assembly
Track your results in real time
Application Output
1. Application Output - In Debug mode, the 'Application Output' window enables real-time data monitoring, offering direct insight into execution results. Ensure proper data display by configuring the environment correctly using the provided tutorial.
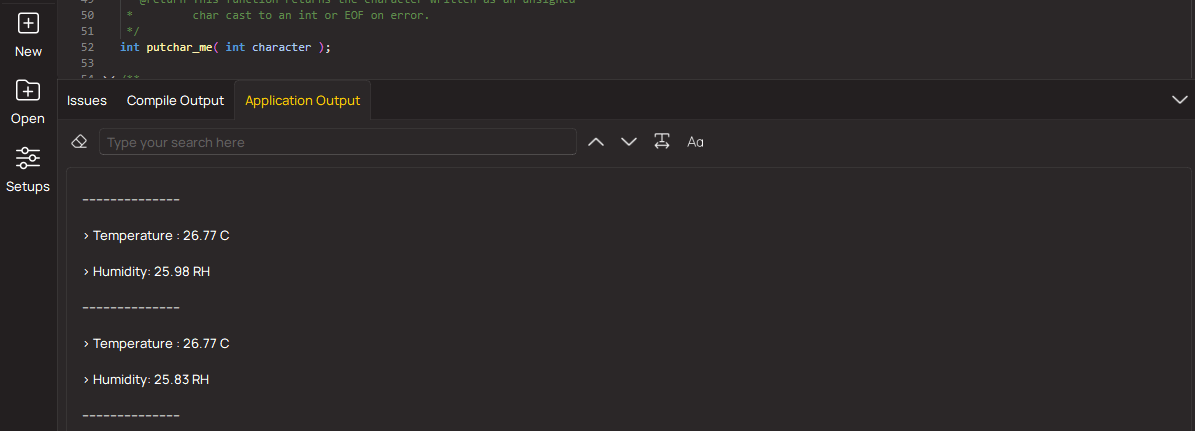
2. UART Terminal - Use the UART Terminal to monitor data transmission via a USB to UART converter, allowing direct communication between the Click board™ and your development system. Configure the baud rate and other serial settings according to your project's requirements to ensure proper functionality. For step-by-step setup instructions, refer to the provided tutorial.
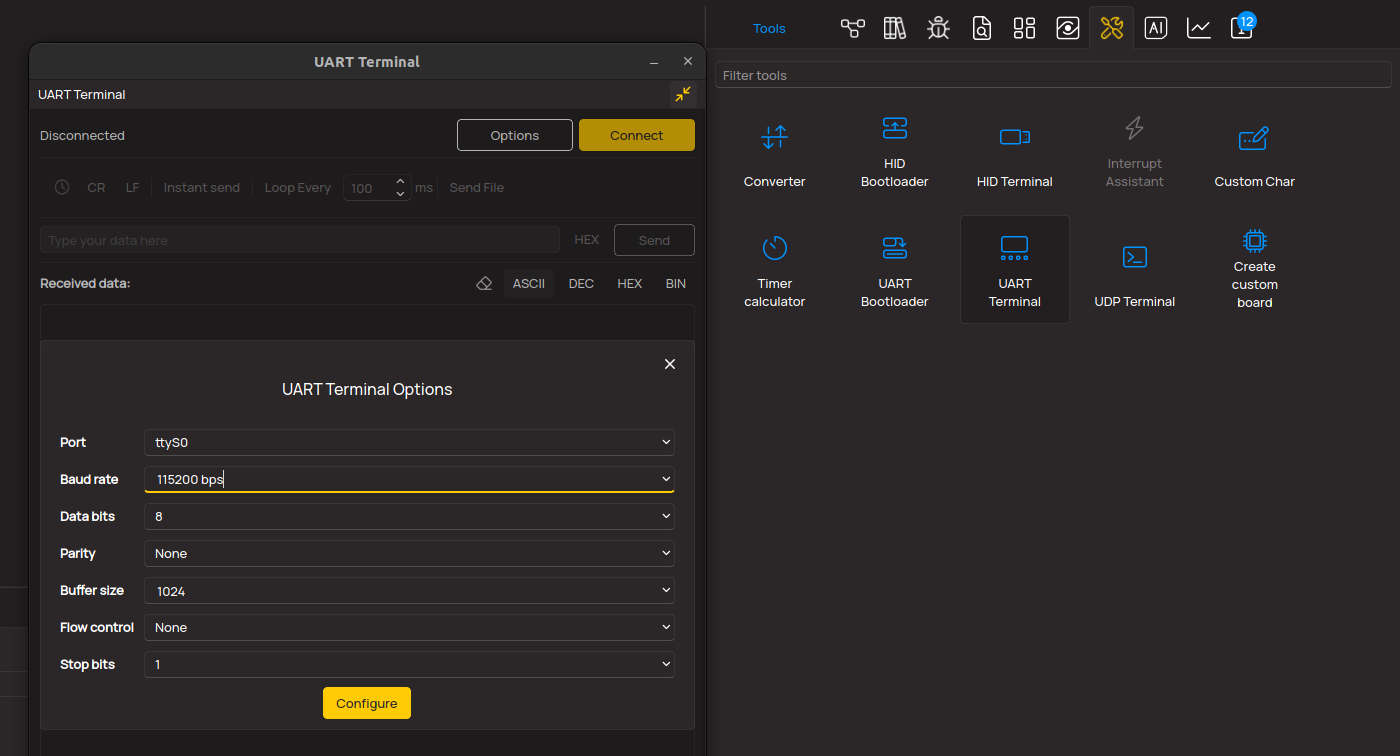
3. Plot Output - The Plot feature offers a powerful way to visualize real-time sensor data, enabling trend analysis, debugging, and comparison of multiple data points. To set it up correctly, follow the provided tutorial, which includes a step-by-step example of using the Plot feature to display Click board™ readings. To use the Plot feature in your code, use the function: plot(*insert_graph_name*, variable_name);. This is a general format, and it is up to the user to replace 'insert_graph_name' with the actual graph name and 'variable_name' with the parameter to be displayed.
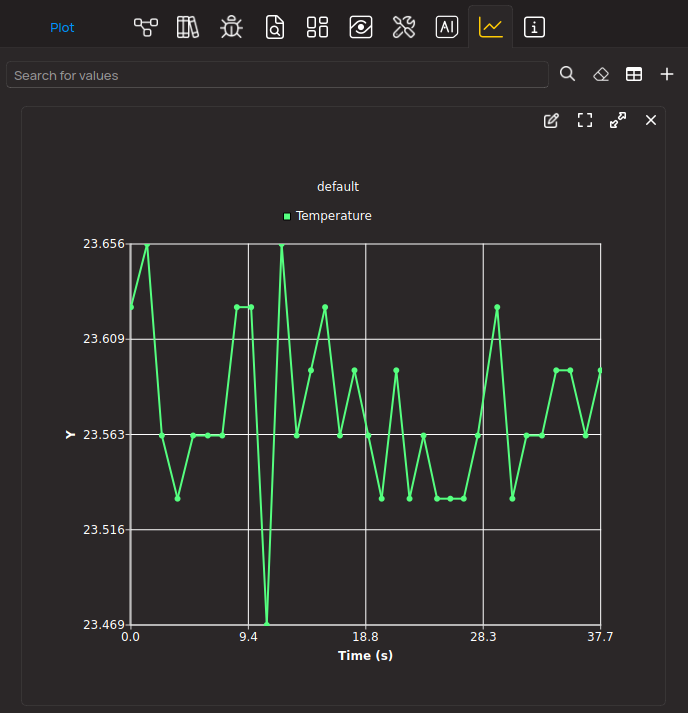
Software Support
Library Description
This library contains API for Air quality 9 Click driver.
Key functions:
airquality9_read_aqi_uba
This function reads the Air quality Index per UBA (AQI-UBA).airquality9_read_tvoc
This function reads the calculated Total Volatile Organic Compounds (TVOC) concentration per ppb.airquality9_read_eco2
This function reads the calculated Equivalent CO2 (eCO2) concentration per ppm.
Open Source
Code example
The complete application code and a ready-to-use project are available through the NECTO Studio Package Manager for direct installation in the NECTO Studio. The application code can also be found on the MIKROE GitHub account.
/*!
* @file main.c
* @brief AirQuality9 Click example
*
* # Description
* This example demonstrates the use of Air Quality 9 Click board by reading and displaying
* outputs such as eCO2, TVOC and AQI in compliance with worldwide IAQ standards.
*
* The demo application is composed of two sections :
*
* ## Application Init
* Initializes the driver and logger and performs the Click default configuration.
*
* ## Application Task
* Waits for the new data interrupt which triggers once per second,
* and then reads the validity status, TVOC, eCO2, and AQI-UBA values.
* All values are being displayed on the USB UART where you can track their changes.
*
* @author Stefan Filipovic
*
*/
#include "board.h"
#include "log.h"
#include "airquality9.h"
static airquality9_t airquality9;
static log_t logger;
/**
* @brief Air Quality 9 display status validity function.
* @details This function parses the status validity from status byte and displays it on the USB UART.
* @param[in] status : Data status byte.
* @return None.
* @note None.
*/
void airquality9_display_status_validity ( uint8_t status );
/**
* @brief Air Quality 9 display aqi uba function.
* @details This function parses the Air Quality Index per UBA (AQI-UBA) value and displays it on the USB UART.
* @param[in] aqi_uba : AQI-UBA value.
* @return None.
* @note None.
*/
void airquality9_display_aqi_uba ( uint8_t aqi_uba );
void application_init ( void )
{
log_cfg_t log_cfg; /**< Logger config object. */
airquality9_cfg_t airquality9_cfg; /**< Click config object. */
/**
* Logger initialization.
* Default baud rate: 115200
* Default log level: LOG_LEVEL_DEBUG
* @note If USB_UART_RX and USB_UART_TX
* are defined as HAL_PIN_NC, you will
* need to define them manually for log to work.
* See @b LOG_MAP_USB_UART macro definition for detailed explanation.
*/
LOG_MAP_USB_UART( log_cfg );
log_init( &logger, &log_cfg );
log_info( &logger, " Application Init " );
// Click initialization.
airquality9_cfg_setup( &airquality9_cfg );
AIRQUALITY9_MAP_MIKROBUS( airquality9_cfg, MIKROBUS_1 );
err_t init_flag = airquality9_init( &airquality9, &airquality9_cfg );
if ( ( I2C_MASTER_ERROR == init_flag ) || ( SPI_MASTER_ERROR == init_flag ) )
{
log_error( &logger, " Communication init." );
for ( ; ; );
}
if ( AIRQUALITY9_ERROR == airquality9_default_cfg ( &airquality9 ) )
{
log_error( &logger, " Default configuration." );
for ( ; ; );
}
log_info( &logger, " Application Task " );
}
void application_task ( void )
{
if ( airquality9_get_int_pin ( &airquality9 ) )
{
uint8_t status, aqi_uba;
uint16_t tvoc, eco2;
if ( AIRQUALITY9_OK == airquality9_read_status ( &airquality9, &status ) )
{
airquality9_display_status_validity ( status );
}
if ( AIRQUALITY9_OK == airquality9_read_tvoc ( &airquality9, &tvoc ) )
{
log_printf ( &logger, " TVOC: %u ppb\r\n", tvoc );
}
if ( AIRQUALITY9_OK == airquality9_read_eco2 ( &airquality9, &eco2 ) )
{
log_printf ( &logger, " ECO2: %u ppm\r\n", eco2 );
}
if ( AIRQUALITY9_OK == airquality9_read_aqi_uba ( &airquality9, &aqi_uba ) )
{
airquality9_display_aqi_uba ( aqi_uba );
}
}
}
int main ( void )
{
/* Do not remove this line or clock might not be set correctly. */
#ifdef PREINIT_SUPPORTED
preinit();
#endif
application_init( );
for ( ; ; )
{
application_task( );
}
return 0;
}
void airquality9_display_status_validity ( uint8_t status )
{
switch ( status & AIRQUALITY_STATUS_VALID_FLAG_BITS )
{
case AIRQUALITY_STATUS_VALID_NORMAL_OP:
{
log_printf ( &logger, " Status: Normal operation\r\n" );
break;
}
case AIRQUALITY_STATUS_VALID_WARM_UP:
{
log_printf ( &logger, " Status: Warm-Up phase\r\n" );
break;
}
case AIRQUALITY_STATUS_VALID_INIT_START_UP:
{
log_printf ( &logger, " Status: Initial Start-Up phase\r\n" );
break;
}
case AIRQUALITY_STATUS_VALID_INVALID:
{
log_printf ( &logger, " Status: Invalid output\r\n" );
break;
}
}
}
void airquality9_display_aqi_uba ( uint8_t aqi_uba )
{
switch ( aqi_uba )
{
case AIRQUALITY9_AQI_UBA_EXELLENT:
{
log_printf ( &logger, " AQI-UBA Rating: Exellent\r\n" );
log_printf ( &logger, " Recommendation: Target\r\n" );
log_printf ( &logger, " Exposure Limit: No limit\r\n\n" );
break;
}
case AIRQUALITY9_AQI_UBA_GOOD:
{
log_printf ( &logger, " AQI-UBA Rating: Good\r\n" );
log_printf ( &logger, " Recommendation: Sufficient ventilation\r\n" );
log_printf ( &logger, " Exposure Limit: No limit\r\n\n" );
break;
}
case AIRQUALITY9_AQI_UBA_MODERATE:
{
log_printf ( &logger, " AQI-UBA Rating: Moderate\r\n" );
log_printf ( &logger, " Recommendation: Increased ventilation - Search for sources\r\n" );
log_printf ( &logger, " Exposure Limit: <12 months\r\n\n" );
break;
}
case AIRQUALITY9_AQI_UBA_POOR:
{
log_printf ( &logger, " AQI-UBA Rating: Poor\r\n" );
log_printf ( &logger, " Recommendation: Intensified ventilation - Search for sources\r\n" );
log_printf ( &logger, " Exposure Limit: <1 month\r\n\n" );
break;
}
case AIRQUALITY9_AQI_UBA_UNHEALTHY:
{
log_printf ( &logger, " AQI-UBA Rating: Unhealthy\r\n" );
log_printf ( &logger, " Recommendation: Use only if unavoidable - Intensified ventilation\r\n" );
log_printf ( &logger, " Exposure Limit: No limit\r\n\n" );
break;
}
default:
{
log_printf ( &logger, " AQI-UBA Rating: Unknown\r\n\n" );
break;
}
}
}
// ------------------------------------------------------------------------ END