Detect the presence or absence of objects within a 200mm range, ideal for gesture recognition and object avoidance applications
A
A
Hardware Overview
How does it work?
Proximity 20 Click is based on two VCNL36828Ps, fully integrated proximity sensors from Vishay Semiconductor, designed for low power consumption and short-range operation up to 200mm. Each VCNL36828P integrates a vertical-cavity surface-emitting laser (VCSEL), photodiode, and application-specific integrated circuit (ASIC) within a single package. Notable features include immunity to red glow thanks to the 940nm VCSEL, intelligent cancellation technology that minimizes cross talk, and a smart persistence scheme designed to reduce measurement response time. The VCNL36828P also features a smart dual slave address capability, enabling users to switch addresses by simply swapping the SCL and SDA pins. This flexibility is the reason why this Click board™ incorporates two identical sensors. Proximity 20 Click is designed in a unique format
supporting the newly introduced MIKROE feature called "Click Snap." Unlike the standardized version of Click boards, this feature allows the main IC area to become movable by breaking the PCB, opening up many new possibilities for implementation. Thanks to the Snap feature, the VCNL36828Ps can operate autonomously by accessing its signals directly on the pins marked 1-8. Additionally, the Snap part includes a specified and fixed screw hole position, enabling users to secure the Snap board in their desired location. This Click board™ uses a standard 2-wire I2C interface to communicate with the host MCU, supporting Standard mode with up to 400kHz of frequency clock. The I2C interface and registers allow for controlling various sensor functions, such as operating mode control, interrupt system management for interrupt signals available on INT
pin, and adjusting offset and threshold values for proximity sensor data. This flexibility ensures precise and customizable operations tailored to specific application needs. The VCNL36828Ps do not require a specific Power-Up sequence but require a voltage of 1.8V for its interface and logic part to work correctly. Therefore, a small regulating LDO, the AP2112, provides a 1.8V out of 3.3V mikroBUS™ power rail. This regulator can be activated via the EN pin of the mikroBUS™ socket, providing an enable function simultaneously. This Click board™ can be operated only with a 3.3V logic voltage level. The board must perform appropriate logic voltage level conversion before using MCUs with different logic levels. Also, it comes equipped with a library containing functions and an example code that can be used as a reference for further development.
Features overview
Development board
The 32L496GDISCOVERY Discovery kit serves as a comprehensive demonstration and development platform for the STM32L496AG microcontroller, featuring an Arm® Cortex®-M4 core. Designed for applications that demand a balance of high performance, advanced graphics, and ultra-low power consumption, this kit enables seamless prototyping for a wide range of embedded solutions. With its innovative energy-efficient
architecture, the STM32L496AG integrates extended RAM and the Chrom-ART Accelerator, enhancing graphics performance while maintaining low power consumption. This makes the kit particularly well-suited for applications involving audio processing, graphical user interfaces, and real-time data acquisition, where energy efficiency is a key requirement. For ease of development, the board includes an onboard ST-LINK/V2-1
debugger/programmer, providing a seamless out-of-the-box experience for loading, debugging, and testing applications without requiring additional hardware. The combination of low power features, enhanced memory capabilities, and built-in debugging tools makes the 32L496GDISCOVERY kit an ideal choice for prototyping advanced embedded systems with state-of-the-art energy efficiency.
Microcontroller Overview
MCU Card / MCU
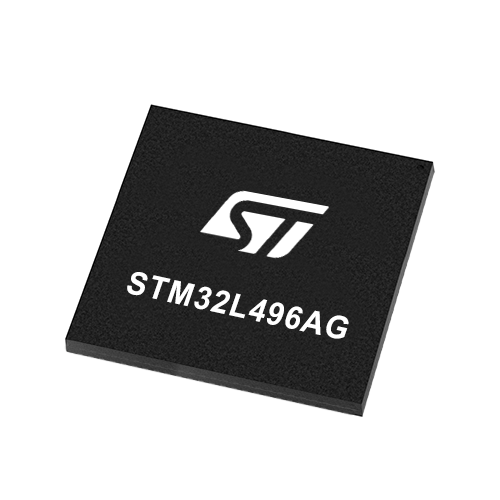
Architecture
ARM Cortex-M4
MCU Memory (KB)
1024
Silicon Vendor
STMicroelectronics
Pin count
169
RAM (Bytes)
327680
Used MCU Pins
mikroBUS™ mapper
Take a closer look
Click board™ Schematic
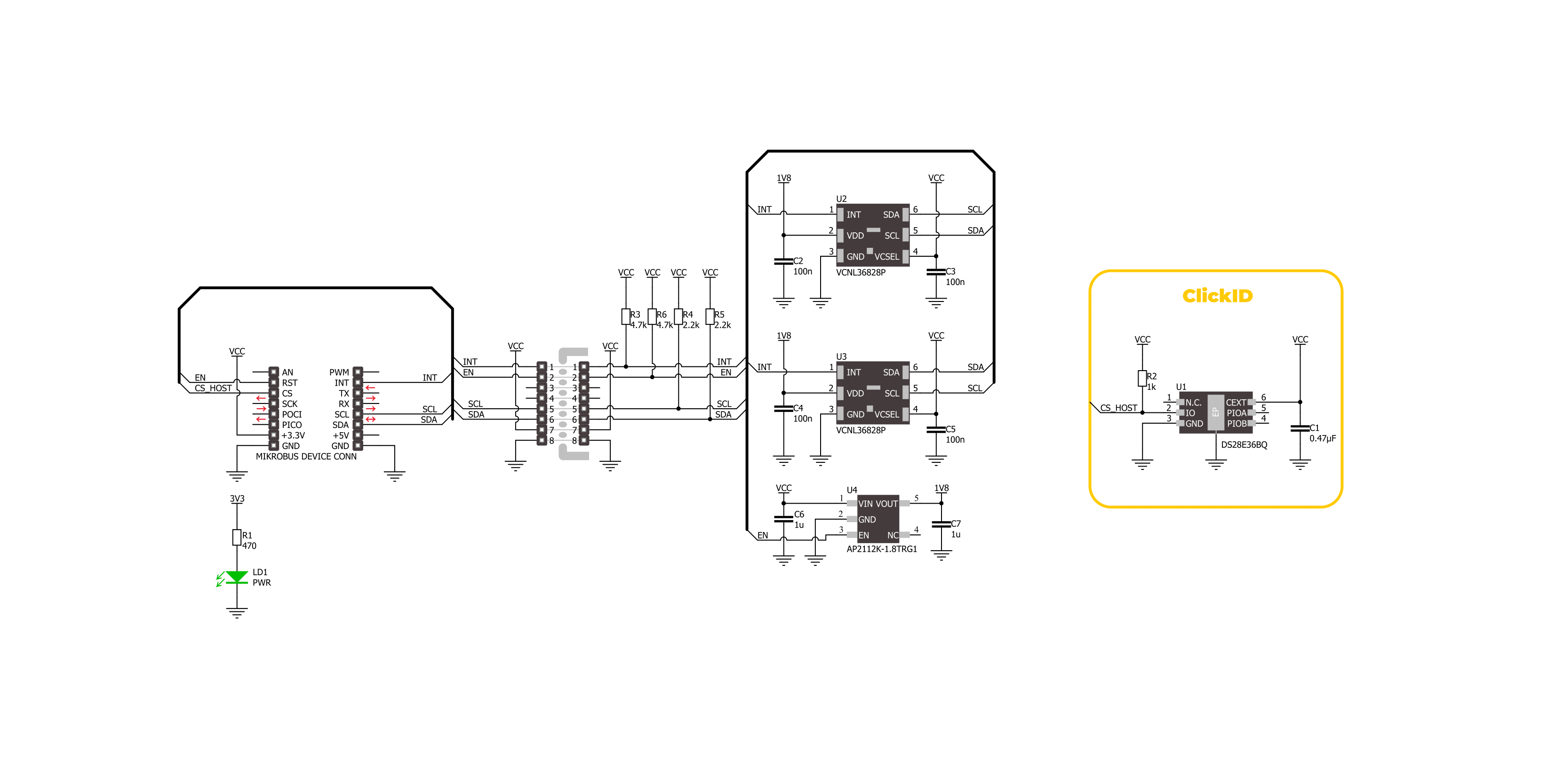
Step by step
Project assembly
Track your results in real time
Application Output
1. Application Output - In Debug mode, the 'Application Output' window enables real-time data monitoring, offering direct insight into execution results. Ensure proper data display by configuring the environment correctly using the provided tutorial.
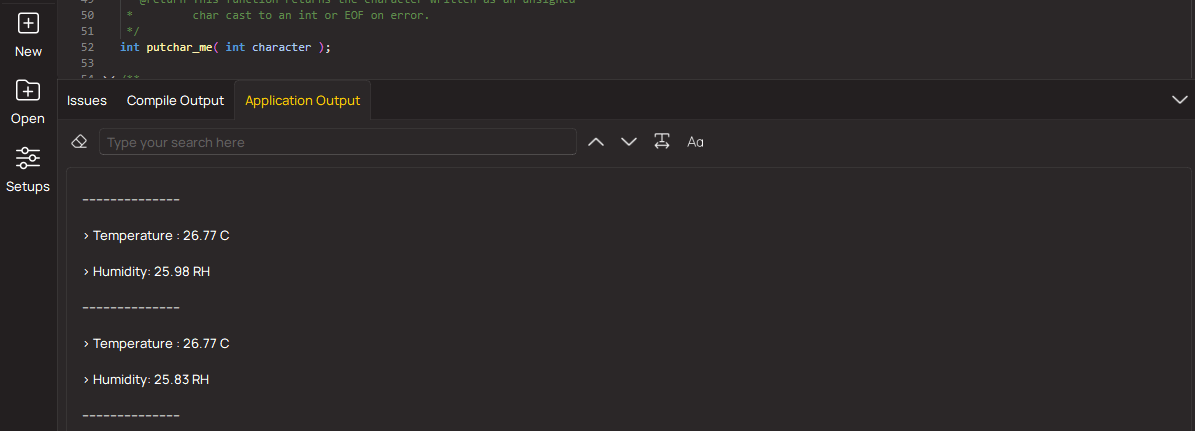
2. UART Terminal - Use the UART Terminal to monitor data transmission via a USB to UART converter, allowing direct communication between the Click board™ and your development system. Configure the baud rate and other serial settings according to your project's requirements to ensure proper functionality. For step-by-step setup instructions, refer to the provided tutorial.
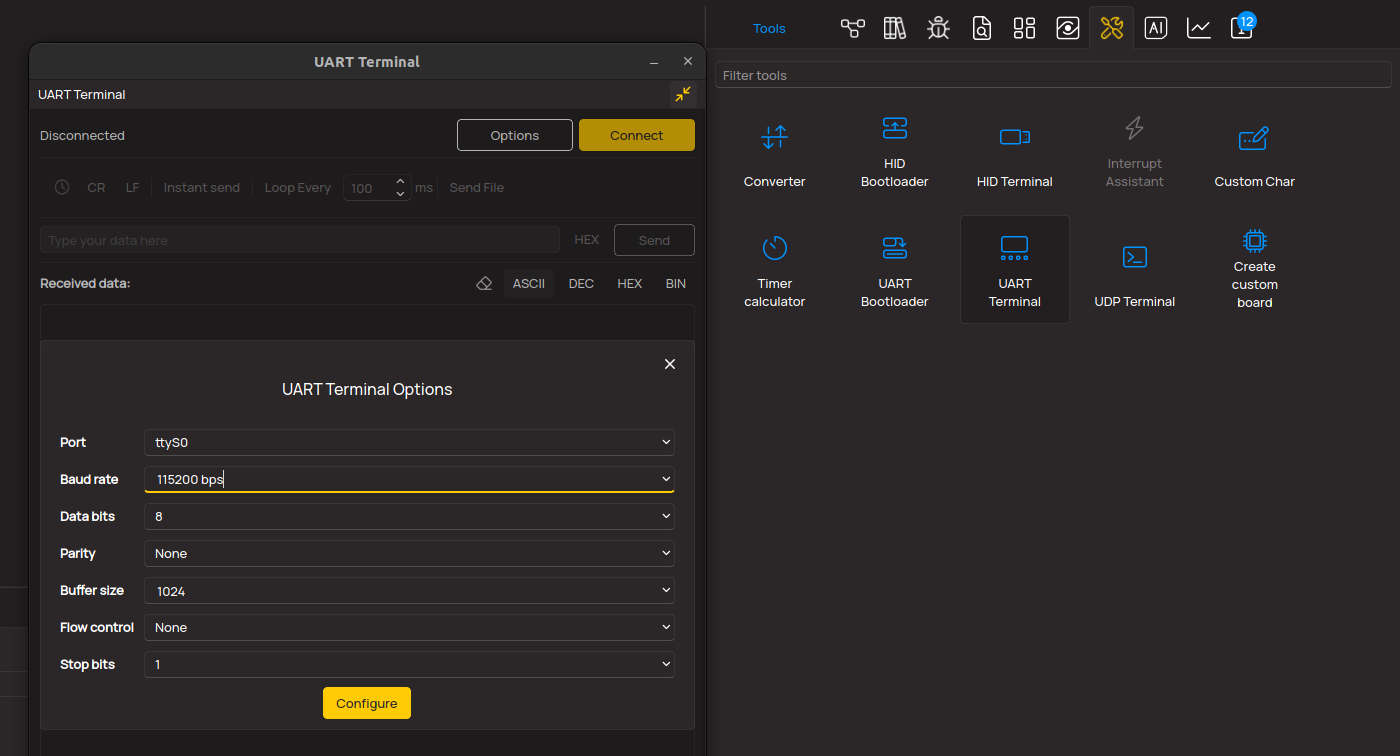
3. Plot Output - The Plot feature offers a powerful way to visualize real-time sensor data, enabling trend analysis, debugging, and comparison of multiple data points. To set it up correctly, follow the provided tutorial, which includes a step-by-step example of using the Plot feature to display Click board™ readings. To use the Plot feature in your code, use the function: plot(*insert_graph_name*, variable_name);. This is a general format, and it is up to the user to replace 'insert_graph_name' with the actual graph name and 'variable_name' with the parameter to be displayed.
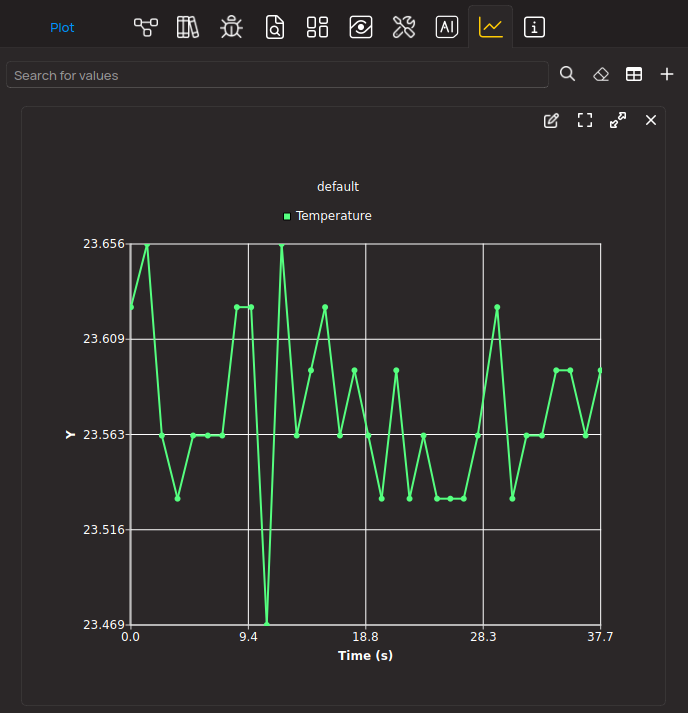
Software Support
Library Description
This library contains API for Proximity 20 Click driver.
Key functions:
proximity20_read_proximity
- This function reads the proximity data from U2 and U3 sensors.proximity20_set_device_address
- This function sets the device slave address.proximity20_enable_device
- This function enables the device by setting the EN pin to high logic state.
Open Source
Code example
The complete application code and a ready-to-use project are available through the NECTO Studio Package Manager for direct installation in the NECTO Studio. The application code can also be found on the MIKROE GitHub account.
/*!
* @file main.c
* @brief Proximity 20 Click example
*
* # Description
* This example demonstrates the use of Proximity 20 Click board by reading and
* displaying the proximity data on the USB UART.
*
* The demo application is composed of two sections :
*
* ## Application Init
* Initializes the driver and logger, and performs the Click default configuration.
*
* ## Application Task
* Reads the proximity data from 2 sensors and displays the results on the USB UART every 200ms.
* The higher the proximity value, the closer the detected object.
*
* @author Stefan Filipovic
*
*/
#include "board.h"
#include "log.h"
#include "proximity20.h"
static proximity20_t proximity20;
static log_t logger;
void application_init ( void )
{
log_cfg_t log_cfg; /**< Logger config object. */
proximity20_cfg_t proximity20_cfg; /**< Click config object. */
/**
* Logger initialization.
* Default baud rate: 115200
* Default log level: LOG_LEVEL_DEBUG
* @note If USB_UART_RX and USB_UART_TX
* are defined as HAL_PIN_NC, you will
* need to define them manually for log to work.
* See @b LOG_MAP_USB_UART macro definition for detailed explanation.
*/
LOG_MAP_USB_UART( log_cfg );
log_init( &logger, &log_cfg );
log_info( &logger, " Application Init " );
// Click initialization.
proximity20_cfg_setup( &proximity20_cfg );
PROXIMITY20_MAP_MIKROBUS( proximity20_cfg, MIKROBUS_1 );
if ( I2C_MASTER_ERROR == proximity20_init( &proximity20, &proximity20_cfg ) )
{
log_error( &logger, " Communication init." );
for ( ; ; );
}
if ( PROXIMITY20_ERROR == proximity20_default_cfg ( &proximity20 ) )
{
log_error( &logger, " Default configuration." );
for ( ; ; );
}
log_info( &logger, " Application Task " );
}
void application_task ( void )
{
uint16_t ps_data_u2 = 0;
uint16_t ps_data_u3 = 0;
if ( PROXIMITY20_OK == proximity20_read_proximity ( &proximity20, &ps_data_u2, &ps_data_u3 ) )
{
log_printf ( &logger, " PS data [U2]: %u\r\n", ps_data_u2 );
log_printf ( &logger, " PS data [U3]: %u\r\n\n", ps_data_u3 );
Delay_ms ( 200 );
}
}
int main ( void )
{
/* Do not remove this line or clock might not be set correctly. */
#ifdef PREINIT_SUPPORTED
preinit();
#endif
application_init( );
for ( ; ; )
{
application_task( );
}
return 0;
}
// ------------------------------------------------------------------------ END
Additional Support
Resources
Category:Proximity