Navigate, scroll, and zoom effortlessly with intuitive finger movements
A
A
Hardware Overview
How does it work?
Touchpad 3 Click is based on the MTCH6301, a turnkey capacitive touch controller that allows users to quickly and easily integrate projected capacitive touch into their applications from Microchip. The MTCH6301 is characterized by a multitouch function that allows up to 10 pad touches, gesture detection, reporting, single and dual touch drawing, self or mutual signal acquisition, and built-in noise detection and filtering. Single-finger gestures are a fast and intuitive way to navigate a feature-rich human-machine interface. It supports 11 single-finger gestures natively without requiring interaction from the master processor. On the front side of the Touchpad 3 Click, there is a clearly defined field that represents a touchpad area. This area is a matrix of conductive electrodes on the PCB, electrically isolated from each other, arranged as rows and columns of X and Y. An electrode
consists of multiple diamond-shaped elements, each connected to the next with a conductive neck. Touchpad 3 Click communicates with MCU using the standard I2C 2-Wire interface that can operate at a maximum speed of 400kbps. The MTCH6301 I2C protocol follows a serial streaming format, not a register-based protocol. For accomplished I2C protocol, the device will assert the active-high INT pin, which is held low during all other activities whenever a new packet of data is ready to be transmitted to the host. This event can happen under two conditions: when a command has been sent to the controller, when the new touch or gesture data is available, or when the response to this command is ready. As mentioned before, the INT pin routed on the INT pin of the mikroBUS™ socket is utilized by MTCH6301 to signal when the data is available and that the master controller should invoke a master
read. Alongside this feature, this Click board™ also has a Reset function routed on the RST pin of the mikroBUS™ socket that will reset the MTCH6301 by driving the RST pin low. When released, the device will assert the INT pin until it has finished initialization routines. For ease of use, the MTCH6301 has the recommended Start-Up sequence that can also be found in the example code that MIKROE offers to its users. This Click board™ is designed to be operated only with a 3.3V logic voltage level. A proper logic voltage level conversion should be performed before the Click board™ is used with MCUs with different logic levels. However, the Click board™ comes equipped with a library that contains easy-to-use functions and an example code that can be used as a reference for further development.
Features overview
Development board
UNI Clicker is a compact development board designed as a complete solution that brings the flexibility of add-on Click boards™ to your favorite microcontroller, making it a perfect starter kit for implementing your ideas. It supports a wide range of microcontrollers, such as different ARM, PIC32, dsPIC, PIC, and AVR from various vendors like Microchip, ST, NXP, and TI (regardless of their number of pins), four mikroBUS™ sockets for Click board™ connectivity, a USB connector, LED indicators, buttons, a debugger/programmer connector, and two 26-pin headers for interfacing with external electronics. Thanks to innovative manufacturing technology, it allows you to build
gadgets with unique functionalities and features quickly. Each part of the UNI Clicker development kit contains the components necessary for the most efficient operation of the same board. In addition to the possibility of choosing the UNI Clicker programming method, using a third-party programmer or CODEGRIP/mikroProg connected to onboard JTAG/SWD header, the UNI Clicker board also includes a clean and regulated power supply module for the development kit. It provides two ways of board-powering; through the USB Type-C (USB-C) connector, where onboard voltage regulators provide the appropriate voltage levels to each component on the board, or using a Li-Po/Li
Ion battery via an onboard battery connector. All communication methods that mikroBUS™ itself supports are on this board (plus USB HOST/DEVICE), including the well-established mikroBUS™ socket, a standardized socket for the MCU card (SiBRAIN standard), and several user-configurable buttons and LED indicators. UNI Clicker is an integral part of the Mikroe ecosystem, allowing you to create a new application in minutes. Natively supported by Mikroe software tools, it covers many aspects of prototyping thanks to a considerable number of different Click boards™ (over a thousand boards), the number of which is growing every day.
Microcontroller Overview
MCU Card / MCU
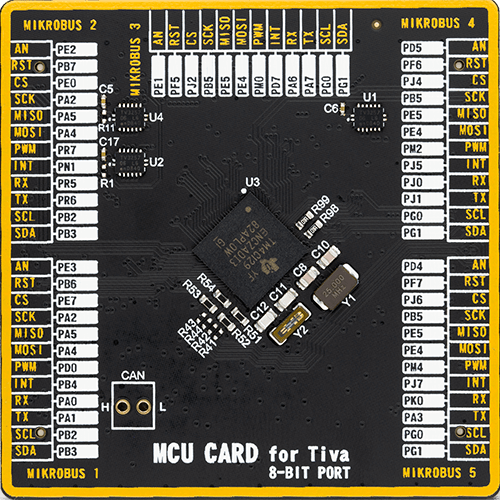
Type
8th Generation
Architecture
ARM Cortex-M4
MCU Memory (KB)
1024
Silicon Vendor
Texas Instruments
Pin count
212
RAM (Bytes)
262144
Used MCU Pins
mikroBUS™ mapper
Take a closer look
Click board™ Schematic
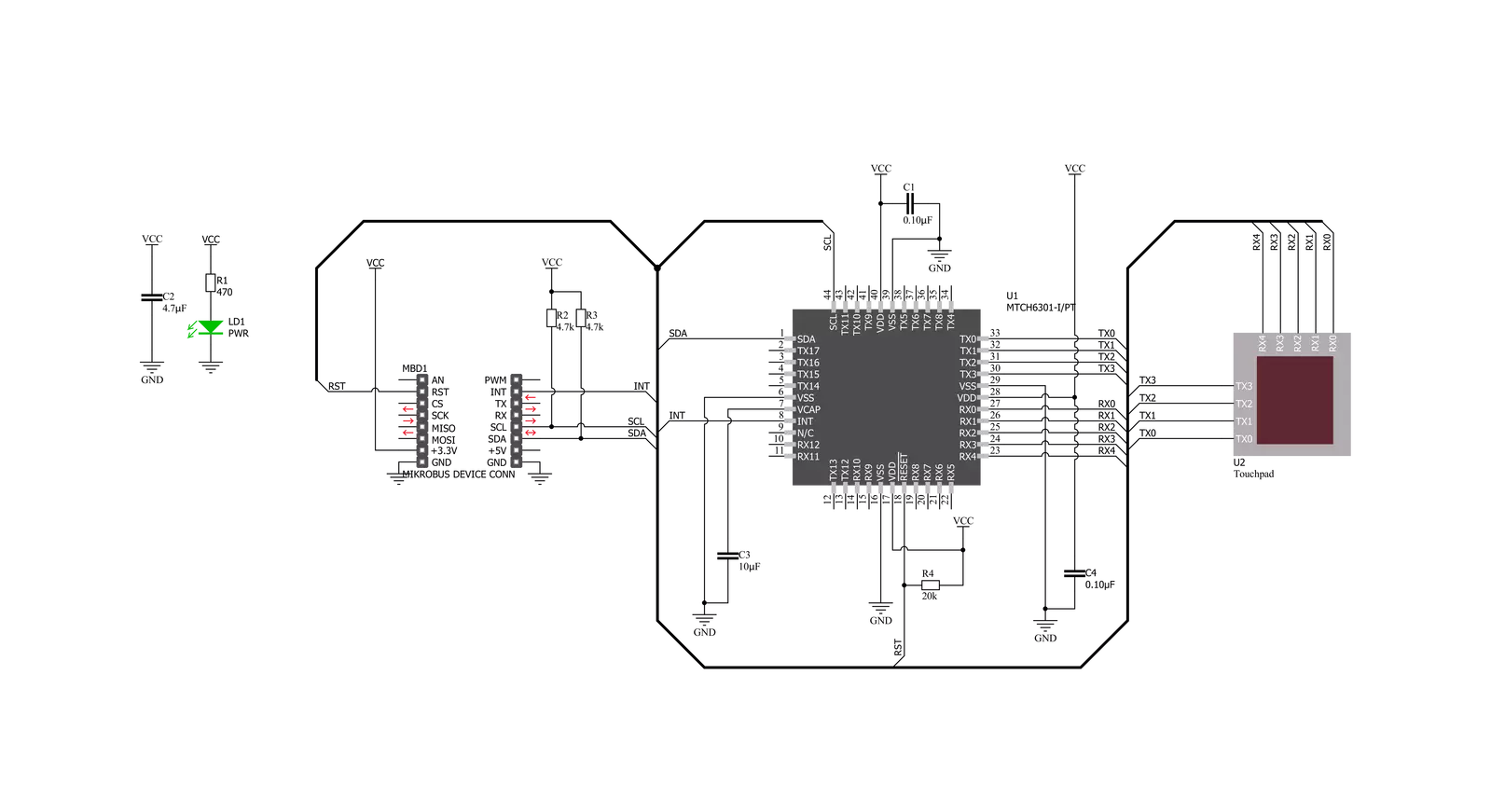
Step by step
Project assembly
Track your results in real time
Application Output
1. Application Output - In Debug mode, the 'Application Output' window enables real-time data monitoring, offering direct insight into execution results. Ensure proper data display by configuring the environment correctly using the provided tutorial.
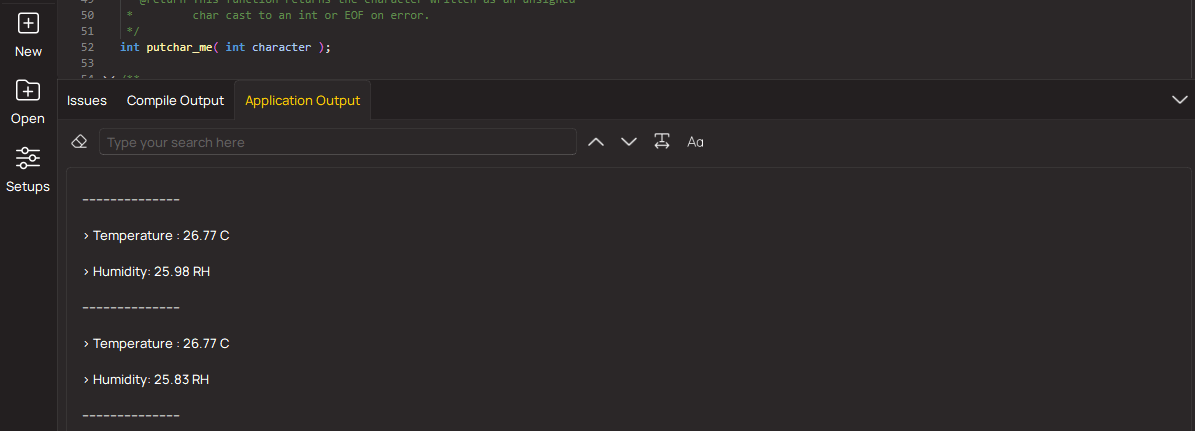
2. UART Terminal - Use the UART Terminal to monitor data transmission via a USB to UART converter, allowing direct communication between the Click board™ and your development system. Configure the baud rate and other serial settings according to your project's requirements to ensure proper functionality. For step-by-step setup instructions, refer to the provided tutorial.
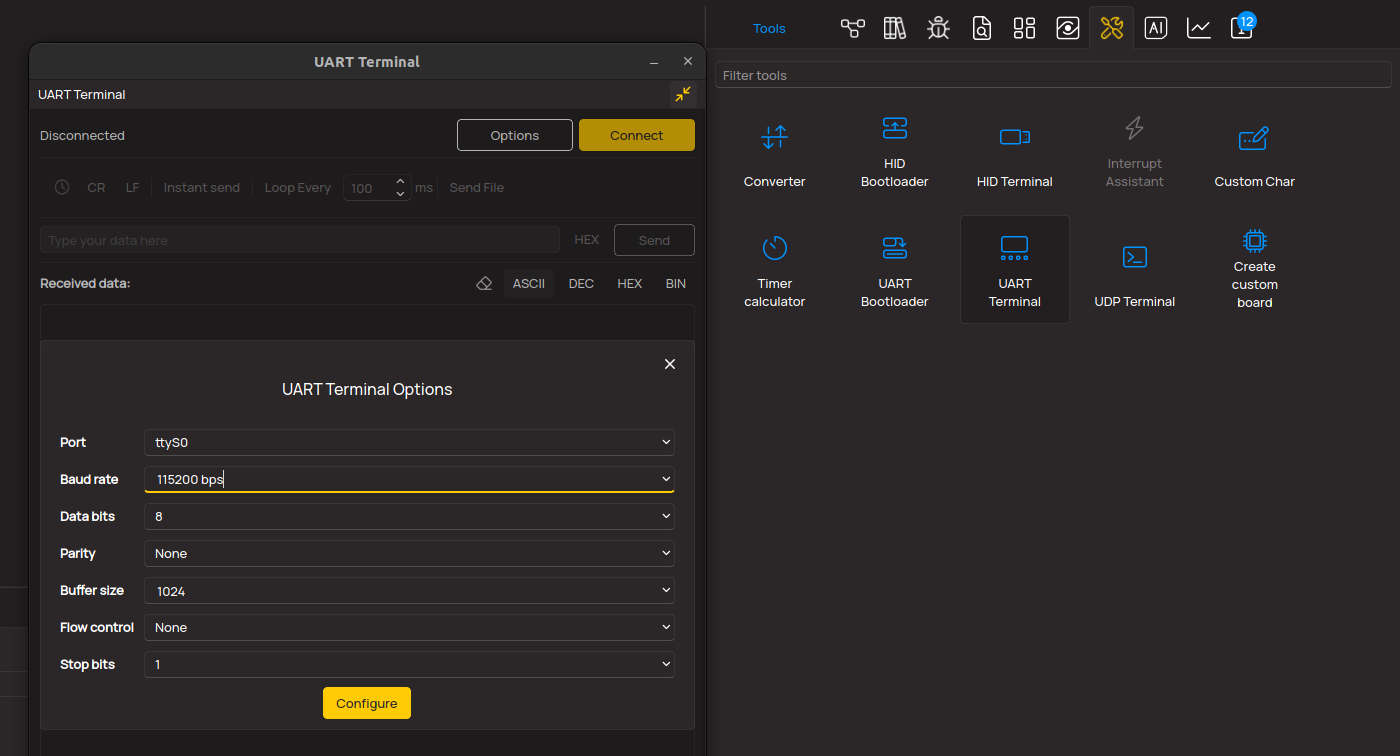
3. Plot Output - The Plot feature offers a powerful way to visualize real-time sensor data, enabling trend analysis, debugging, and comparison of multiple data points. To set it up correctly, follow the provided tutorial, which includes a step-by-step example of using the Plot feature to display Click board™ readings. To use the Plot feature in your code, use the function: plot(*insert_graph_name*, variable_name);. This is a general format, and it is up to the user to replace 'insert_graph_name' with the actual graph name and 'variable_name' with the parameter to be displayed.
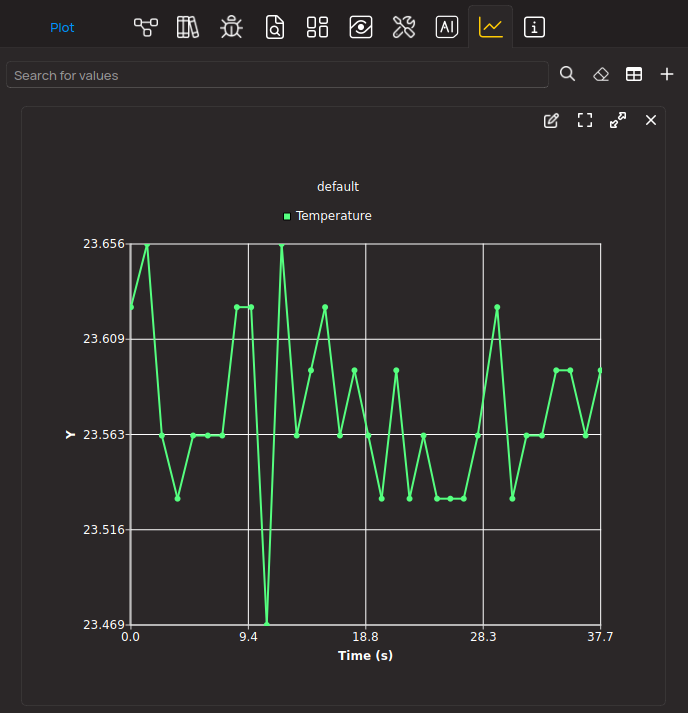
Software Support
Library Description
This library contains API for Touchpad 3 Click driver.
Key functions:
touchpad3_general_configuration
- The function performs the general configuration of the MTCH6301touchpad3_decoding_configuration
- The function performs the decoding configuration of the MTCH6301touchpad3_sensor_mapping_configuration
- The function configures the sensor mapping of the MTCH6301
Open Source
Code example
The complete application code and a ready-to-use project are available through the NECTO Studio Package Manager for direct installation in the NECTO Studio. The application code can also be found on the MIKROE GitHub account.
/*!
* @file main.c
* @brief Touchpad3 Click example
*
* # Description
* This example prints the coordinate points of the position we touch on a Click. We use RST and INT
* pins. The whole project is done through i2c communication.
*
* The demo application is composed of two sections :
*
* ## Application Init
* Initialization driver enables - Initializes I2C, set RST pin as an output, set INT pin as input and start to write log.
* I2C, perform a hardware reset, configuration (general, decoding, sensor mapping), get device ID and enable the touch, also write log.
*
* ## Application Task
* This is an example that demonstrates the use of the TouchPad 3 Click board. TouchPad 3 Click board uses USB UART log to display
* X and Y coordinates of the touch, depending on the selected Touch ID.
*
* @author Jelena Milosavljevic
*
*/
#include "board.h"
#include "log.h"
#include "touchpad3.h"
static touchpad3_t touchpad3;
static log_t logger;
uint8_t touch_id_state;
uint8_t status_data;
uint16_t x_axis;
uint16_t y_axis;
uint32_t device_id;
touch_data_t touch_data;
void display_status ( void ) {
switch ( status_data ) {
case ( TOUCHPAD3_CMD_STATUS_SUCCESS ) : {
log_printf( &logger, " Command execution successful " );
Delay_ms ( 10 );
break;
}
case ( TOUCHPAD3_CMD_STATUS_PARAM_OUT_OF_RANGE ) : {
log_printf( &logger, " Parameter out of range " );
Delay_ms ( 10 );
break;
}
case TOUCHPAD3_CMD_STATUS_TIMEOUT: {
log_printf( &logger," Timeout : " );
log_printf( &logger, " not enough bytes received " );
Delay_ms ( 10 );
break;
}
case TOUCHPAD3_CMD_STATUS_UNRECOGNIZED: {
log_printf( &logger, " Unrecognized command ");
Delay_ms ( 10 );
break;
}
case TOUCHPAD3_CMD_STATUS_INVALID_PARAM: {
log_printf( &logger, " Invalid parameter " );
Delay_ms ( 10 );
break;
}
case TOUCHPAD3_CMD_STATUS_MISSING_OR_EXTRA_PARAM: {
log_printf( &logger, " Missing or extra parameter " );
Delay_ms ( 10 );
break;
}
default: {
break;
}
}
}
void application_init ( void ) {
log_cfg_t log_cfg; /**< Logger config object. */
touchpad3_cfg_t touchpad3_cfg; /**< Click config object. */
/**
* Logger initialization.
* Default baud rate: 115200
* Default log level: LOG_LEVEL_DEBUG
* @note If USB_UART_RX and USB_UART_TX
* are defined as HAL_PIN_NC, you will
* need to define them manually for log to work.
* See @b LOG_MAP_USB_UART macro definition for detailed explanation.
*/
LOG_MAP_USB_UART( log_cfg );
log_init( &logger, &log_cfg );
log_info( &logger, " Application Init " );
// Click initialization.
touchpad3_cfg_setup( &touchpad3_cfg );
TOUCHPAD3_MAP_MIKROBUS( touchpad3_cfg, MIKROBUS_1 );
err_t init_flag = touchpad3_init( &touchpad3, &touchpad3_cfg );
if ( I2C_MASTER_ERROR == init_flag ) {
log_error( &logger, " Application Init Error. " );
log_info( &logger, " Please, run program again... " );
for ( ; ; );
}
touchpad3_default_cfg ( &touchpad3 );
touch_id_state = 0;
log_printf( &logger, "------------------------------\r\n" );
device_id = touchpad3_get_device_id( &touchpad3 );
Delay_ms ( 100 );
log_printf( &logger, " Get Device ID : %d \r\n ", device_id );
log_printf( &logger, "------------------------------\r\n" );
Delay_ms ( 100 );
log_info( &logger, " Application Task " );
Delay_ms ( 100 );
status_data = touchpad3_config_touch( &touchpad3, TOUCHPAD3_TOUCH_GESTURE_ENABLE );
log_printf( &logger, " Touch Enable Status: \r\n");
display_status( );
log_printf( &logger, "------------------------------\r\n" );
Delay_ms ( 100 );
}
void application_task ( void ) {
if ( touchpad3_get_int( &touchpad3 ) == TOUCHPAD3_INT_STATUS_HIGH ) {
touchpad3_get_touch( &touchpad3, &touch_data, &x_axis, &y_axis );
Delay_ms ( 100 );
if ( ( touch_data.tch_state == TOUCHPAD3_STATE_TCH ) && ( touch_data.touch_id == touch_id_state ) ) {
log_printf( &logger, " X Coordinate : %d \r\n" , x_axis );
log_printf( &logger, " Y Coordinate : %d \r\n" , y_axis );
log_printf( &logger, "------------------------------\r\n" );
Delay_ms ( 100 );
}
}
}
int main ( void )
{
/* Do not remove this line or clock might not be set correctly. */
#ifdef PREINIT_SUPPORTED
preinit();
#endif
application_init( );
for ( ; ; )
{
application_task( );
}
return 0;
}
// ------------------------------------------------------------------------ END