Unlock diverse communication capabilities with our Semper Flash solution's range of protocols, ensuring versatile and reliable data transfer
A
A
Hardware Overview
How does it work?
Semper Flash 2 Click is based on the S25HL512T, a 512 Mbit SPI Flash memory module from Infineon. Featuring both normal and double data rates over the standard, Dual/Quad SPI interface, the improved reliability of the stored information by utilizing the hardware Error Correction Code (ECC) generation, One-Time Programmable (OTP) memory block of 1024 bytes, advanced sector protection, AutoBoot, and much more, this Click board™ is a perfect solution for the mass storage option in various embedded applications. Due to its fast performance, Semper Flash Click 2 can also be used for code shadowing, execute-in-place (XIP), and data storage. An additional level translator IC allows Semper Flash Click 2 to be used with a wide range of MCUs. The device control logic is subdivided into two parallel operating sections: the Host Interface Controller (HIC) and the Embedded Algorithm Controller (EAC). The HIC monitors signal levels on the device inputs and drives outputs to complete read, program and write data transfers with the host system. The HIC delivers data from the currently entered address map on read transfers, places write transfer address and data information into the EAC command memory and notifies the EAC of power transition and write transfers. The EAC interrogates the command memory after a program or writes transfer for legal command sequences and performs the related Embedded
Algorithms. Executing code directly from Flash memory is often called Execute-In-Place (XIP). By using XIP with Semper Flash devices at the higher clock rates with Quad or DDR Quad SPI transactions, the data transfer rate can match or exceed traditional parallel or asynchronous NOR flash memories while reducing signal count dramatically. The advanced MirrorBit® technology allows storing two data bits in each memory array transistor (memory cell), effectively doubling the capacity of a single storage cell. The Eclipse™ architecture is responsible for the greatly improved erase and programming performance compared to other Flash modules of the previous generation. Due to a higher speed, an execute-in-place (XIP) and data shadowing is possible with the Semper Flash click. One of the S25HL512 T's key features is the AutoBoot feature. It allows the module to automatically initiate the memory transfer from the predefined location (memory read operation) after the reset cycle. Considering a typical communication scenario, where the READ command followed by one or more address bytes need to be used, AutoBoot allows the host MCU to pull down the #CS (Chip Select) pin and start receiving a data stream over the SPI interface for as long as the #CS pin is held LOW, without any wasted cycles. When the #CS pin is released, the S25HL512T returns to normal operation. Advanced Sector Protection (ASP) is a powerful protection
model that incorporates various software and hardware methods to turn programming on or off or erase operations within a sector or an entire memory. A specialized ASP OTP register offers password protection or a persistent protection mode, allowing increased flexibility in the protection. Using the OTP memory allows the protection mode to remain in place for the whole life-cycle of the device. The Semper Flash 2 Click board is carrying S25HL memory module with a 3.0V core and I/O voltage; if you are interested in the 1.8V version of the same part, please check our Semper Flash Click with the S25HS version. The SPI interface pins are routed to the mikroBUS™ so that the interfacing with the microcontroller unit (MCU) is easy and straightforward. Additional pins routed to the mikroBUS™ include the #WP/IO2 pin routed to the mikroBUS™ PWM pin and labeled as IO2 and the #HOLD/IO3 pin routed to the mikroBUS™ INT pin and labeled as IO3. There is also the RESET pin, routed to the RST pin of the mikroBUS™, which performs a reset of the Flash module, initiating an AutoBoot sequence if enabled. EnduraFlex Architecture allows system designers to customize the NOR Flash endurance and retention for their specific applications. The host defines partitions for high endurance or long retention, providing up to 1+ million cycles or 25 years of data retention.
Features overview
Development board
Flip&Click PIC32MZ is a compact development board designed as a complete solution that brings the flexibility of add-on Click boards™ to your favorite microcontroller, making it a perfect starter kit for implementing your ideas. It comes with an onboard 32-bit PIC32MZ microcontroller, the PIC32MZ2048EFH100 from Microchip, four mikroBUS™ sockets for Click board™ connectivity, two USB connectors, LED indicators, buttons, debugger/programmer connectors, and two headers compatible with Arduino-UNO pinout. Thanks to innovative manufacturing technology,
it allows you to build gadgets with unique functionalities and features quickly. Each part of the Flip&Click PIC32MZ development kit contains the components necessary for the most efficient operation of the same board. In addition, there is the possibility of choosing the Flip&Click PIC32MZ programming method, using the chipKIT bootloader (Arduino-style development environment) or our USB HID bootloader using mikroC, mikroBasic, and mikroPascal for PIC32. This kit includes a clean and regulated power supply block through the USB Type-C (USB-C) connector. All communication
methods that mikroBUS™ itself supports are on this board, including the well-established mikroBUS™ socket, user-configurable buttons, and LED indicators. Flip&Click PIC32MZ development kit allows you to create a new application in minutes. Natively supported by Mikroe software tools, it covers many aspects of prototyping thanks to a considerable number of different Click boards™ (over a thousand boards), the number of which is growing every day.
Microcontroller Overview
MCU Card / MCU

Architecture
PIC32
MCU Memory (KB)
2048
Silicon Vendor
Microchip
Pin count
100
RAM (Bytes)
524288
Used MCU Pins
mikroBUS™ mapper
Take a closer look
Click board™ Schematic
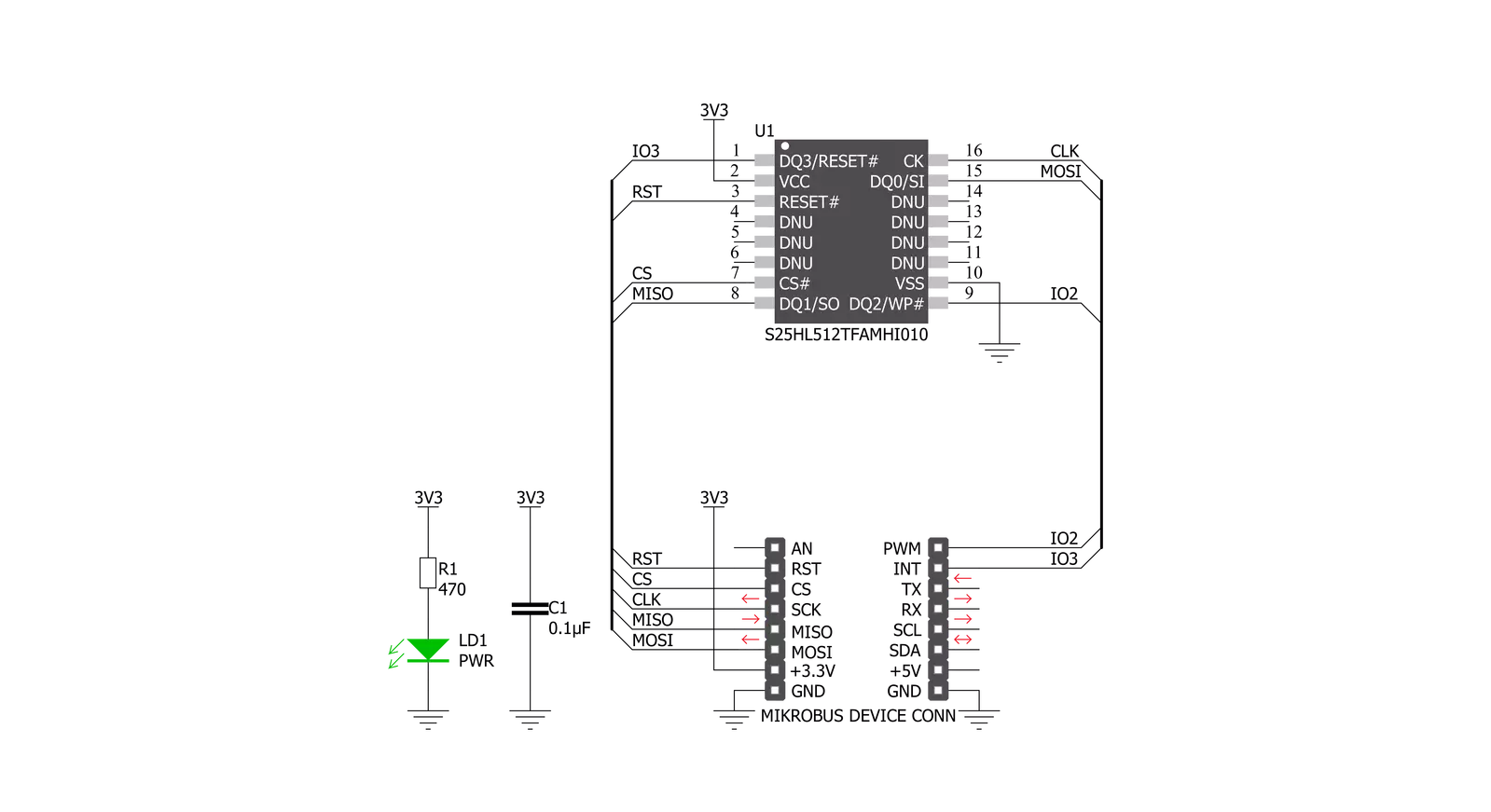
Step by step
Project assembly
Track your results in real time
Application Output
1. Application Output - In Debug mode, the 'Application Output' window enables real-time data monitoring, offering direct insight into execution results. Ensure proper data display by configuring the environment correctly using the provided tutorial.
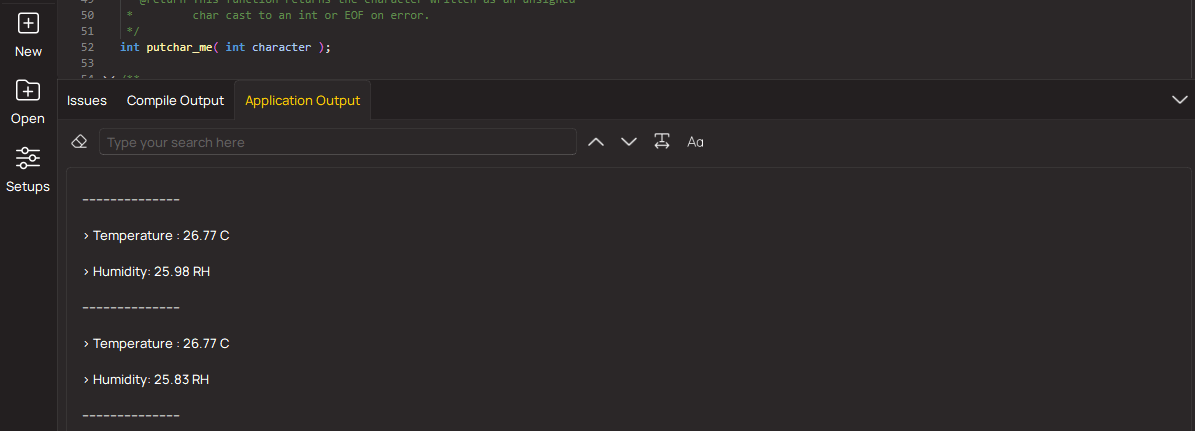
2. UART Terminal - Use the UART Terminal to monitor data transmission via a USB to UART converter, allowing direct communication between the Click board™ and your development system. Configure the baud rate and other serial settings according to your project's requirements to ensure proper functionality. For step-by-step setup instructions, refer to the provided tutorial.
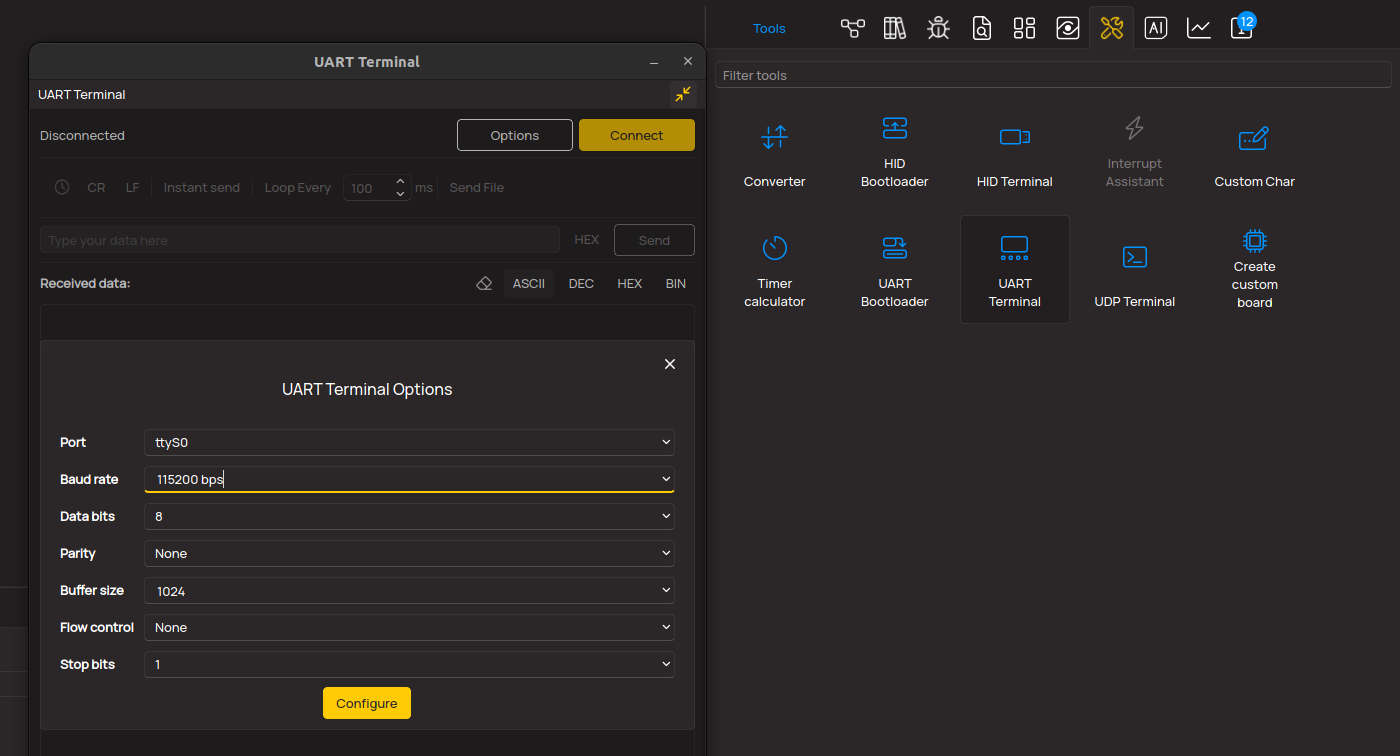
3. Plot Output - The Plot feature offers a powerful way to visualize real-time sensor data, enabling trend analysis, debugging, and comparison of multiple data points. To set it up correctly, follow the provided tutorial, which includes a step-by-step example of using the Plot feature to display Click board™ readings. To use the Plot feature in your code, use the function: plot(*insert_graph_name*, variable_name);. This is a general format, and it is up to the user to replace 'insert_graph_name' with the actual graph name and 'variable_name' with the parameter to be displayed.
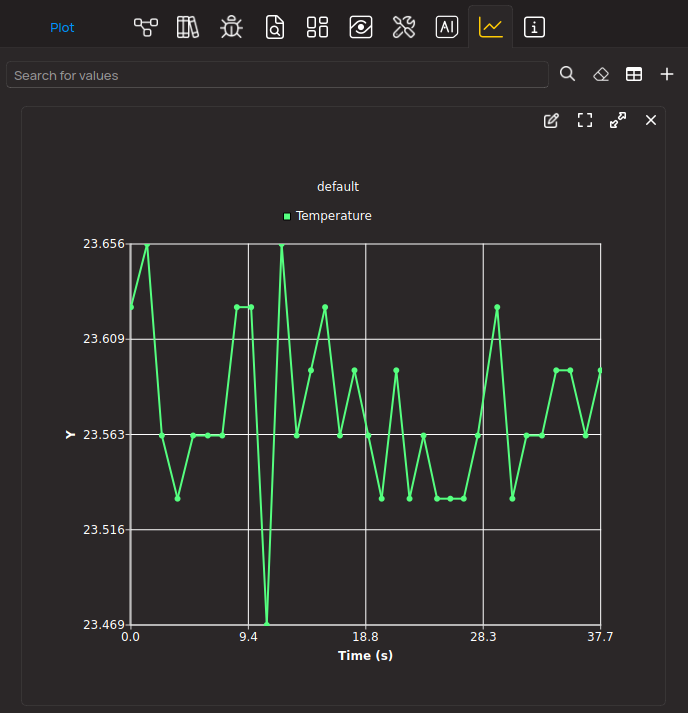
Software Support
Library Description
This library contains API for Semper Flash 2 Click driver.
Key functions:
semperflash2_write_memory
- This function writes data to the flash memorysemperflash2_read_memory
- This function reads data from the flash memorysemperflash2_get_device_id
- This function stores the device ID in the specified buffer
Open Source
Code example
The complete application code and a ready-to-use project are available through the NECTO Studio Package Manager for direct installation in the NECTO Studio. The application code can also be found on the MIKROE GitHub account.
/*!
* \file
* \brief SemperFlash2 Click example
*
* # Description
* This example showcases how to initialize and use the Semper Flash 2 Click. The Click
* is a 512 Mbit SPI Flash memory module. Data can be stored in and read from the flash
* memory. There's also the option of erasing it's contents. Here's how to do it.
*
* The demo application is composed of two sections :
*
* ## Application Init
* This function initializes and configures the Click and logger modules. Additional con-
* figuring is done in the default_cfg(...) function. The device ID should appear in the
* UART console if the setup finishes successfully.
*
* ## Application Task
* This function first erases the contents of the flash memory and then writes, reads and
* prints two strings in the UART console. It does so every 2 seconds.
*
* \author MikroE Team
*
*/
// ------------------------------------------------------------------- INCLUDES
#include "board.h"
#include "log.h"
#include "semperflash2.h"
// ------------------------------------------------------------------ VARIABLES
static semperflash2_t semperflash2;
static log_t logger;
uint8_t id_data[ 8 ];
uint8_t txt_flag;
uint8_t COMPANY_FLAG = 2;
uint8_t CLICK_FLAG = 3;
uint32_t ADRESS_MEMORY = 0x00001111;
// ------------------------------------------------------- ADDITIONAL FUNCTIONS
void error_handler ( uint8_t stat )
{
if ( SEMPERFLASH2_ID_ERROR == stat )
{
log_printf( &logger, "ID ERROR!" );
for ( ; ; );
}
else if ( SEMPERFLASH2_SIZE_ERROR == stat )
{
log_printf( &logger, "BUF SIZE ERROR!" );
for ( ; ; );
}
}
void id_check ( )
{
uint8_t cnt;
error_handler( semperflash2_check_manufacturer_id( &semperflash2 ) );
error_handler( semperflash2_get_device_id( &semperflash2, id_data ) );
log_printf( &logger, "DEVICE ID: 0x" );
for ( cnt = 0; cnt < SEMPERFLASH2_DEVICE_ID_BYTE_SIZE; cnt++ )
{
log_printf( &logger, "%x", ( uint16_t )id_data[ cnt ] );
}
log_printf( &logger, "\r\n\r\n" );
txt_flag = COMPANY_FLAG;
}
// ------------------------------------------------------ APPLICATION FUNCTIONS
void application_init ( )
{
log_cfg_t log_cfg;
semperflash2_cfg_t cfg;
/**
* Logger initialization.
* Default baud rate: 115200
* Default log level: LOG_LEVEL_DEBUG
* @note If USB_UART_RX and USB_UART_TX
* are defined as HAL_PIN_NC, you will
* need to define them manually for log to work.
* See @b LOG_MAP_USB_UART macro definition for detailed explanation.
*/
LOG_MAP_USB_UART( log_cfg );
log_init( &logger, &log_cfg );
log_info( &logger, "---- Application Init ----" );
Delay_ms ( 100 );
// Click initialization.
semperflash2_cfg_setup( &cfg );
SEMPERFLASH2_MAP_MIKROBUS( cfg, MIKROBUS_1 );
semperflash2_init( &semperflash2, &cfg );
semperflash2_default_cfg( &semperflash2 );
id_check( );
Delay_ms ( 500 );
}
void application_task ( )
{
char write_data_com[ 7 ] = "MikroE";
char write_data_clk[ 15 ] = "Semper Flash 2";
char read_buf_data[ 15 ] = { 0 };
semperflash2_send_cmd( &semperflash2, SEMPERFLASH2_WRITE_ENABLE );
semperflash2_erase_memory( &semperflash2, ADRESS_MEMORY );
if ( COMPANY_FLAG == txt_flag )
{
semperflash2_send_cmd( &semperflash2, SEMPERFLASH2_WRITE_ENABLE );
error_handler( semperflash2_write_memory( &semperflash2, ADRESS_MEMORY, write_data_com, 6 ) );
error_handler( semperflash2_read_memory( &semperflash2, ADRESS_MEMORY, read_buf_data, 6 ) );
log_printf( &logger, "%s\r\n", read_buf_data );
txt_flag = CLICK_FLAG;
}
else if ( CLICK_FLAG == txt_flag )
{
semperflash2_send_cmd( &semperflash2, SEMPERFLASH2_WRITE_ENABLE );
error_handler( semperflash2_write_memory( &semperflash2, ADRESS_MEMORY, write_data_clk, 14 ) );
error_handler( semperflash2_read_memory( &semperflash2, ADRESS_MEMORY, read_buf_data, 14 ) );
log_printf( &logger, "%s\r\n", read_buf_data );
txt_flag = COMPANY_FLAG;
}
log_printf( &logger, "....................\r\n" );
Delay_ms ( 1000 );
Delay_ms ( 1000 );
}
int main ( void )
{
/* Do not remove this line or clock might not be set correctly. */
#ifdef PREINIT_SUPPORTED
preinit();
#endif
application_init( );
for ( ; ; )
{
application_task( );
}
return 0;
}
// ------------------------------------------------------------------------ END