Compact and versatile, our buck step-down converter is essential in portable devices, extending battery life and enhancing usability
A
A
Hardware Overview
How does it work?
Buck 12 Click is based on the MPQ8632, a synchronous step-down converter from Monolithic Power Systems (MPS). This advanced integrated step-down converter requires a minimum number of external components readily available on the market. It utilizes a peak-current-mode control architecture, ensuring good efficiency and automatic switch-mode switching. The MPQ8632 buck converter features over-current, under-voltage, and thermal protection, making Buck 12 click a robust and reliable power supply solution. The feedback voltage on the FB pin determines the output voltage. The output voltage is set to 3.3V, making it usable with most embedded applications, allowing them to be powered from the same source, like the rest of the application, which may use a higher voltage for its operation. This is a common-case scenario in various field applications requiring a relatively high voltage, i.e., for servos, step motors, displays, and more. When there is an overload at the output, the low-side MOSFET will allow the inductor current to drop.
It will remain open until the current through the inductor falls below the limit. Suppose the FB voltage drops too much during the overload. In that case, the device enters the hiccup mode, which turns off the output power stage, discharges the soft-start capacitor, and automatically retries the soft-start. The MPQ8632 can automatically switch between different operating modes, depending on the current through the load. At very light loads, the device is operated in skip mode. In this mode, HS-FET turns on for a fixed interval determined by the one-shot on-timer. When the HS-FET turns off, the LS-FET turns on until the inductor current reaches zero. The LS-FET driver turns into a tri-state (high Z) whenever the inductor current reaches zero. This way, the device is idle while the light load consumes energy stored within the coil. This greatly improves the efficiency when a light load is used. This is also called discontinuous conduction mode (DCM). The MPQ8632 automatically switches to heavy load operation or continuous
conduction mode (CCM) when heavily loaded. In this mode, when VFB is below VREF, HS-FET turns on for a fixed interval determined by the one-shot on-timer. When the HS-FET turns off, the LS-FET turns on until the next period. In CCM operation, the switching frequency is fairly constant and called PWM mode. Packed in QFN casing (3X4mm), the MPQ8632 occupies a small area on the PCB. Combined with the low count of external components it requires, the MPQ8632 leaves enough space for an additional IC to be used. This click uses the MCP3202, a Dual Channel 12-Bit A/D Converter which uses the SPI interface from Microchip. It allows monitoring of the input and output voltages over the SPI interface. This ADC is powered by the +5V mikroBUS™ power rail. The same voltage is used as a reference. The Click board™ itself requires an external power supply to be connected at the input terminal, labeled as VIN. The VOUT terminal provides the connected load with the regulated 3.3V voltage.
Features overview
Development board
The 32L496GDISCOVERY Discovery kit serves as a comprehensive demonstration and development platform for the STM32L496AG microcontroller, featuring an Arm® Cortex®-M4 core. Designed for applications that demand a balance of high performance, advanced graphics, and ultra-low power consumption, this kit enables seamless prototyping for a wide range of embedded solutions. With its innovative energy-efficient
architecture, the STM32L496AG integrates extended RAM and the Chrom-ART Accelerator, enhancing graphics performance while maintaining low power consumption. This makes the kit particularly well-suited for applications involving audio processing, graphical user interfaces, and real-time data acquisition, where energy efficiency is a key requirement. For ease of development, the board includes an onboard ST-LINK/V2-1
debugger/programmer, providing a seamless out-of-the-box experience for loading, debugging, and testing applications without requiring additional hardware. The combination of low power features, enhanced memory capabilities, and built-in debugging tools makes the 32L496GDISCOVERY kit an ideal choice for prototyping advanced embedded systems with state-of-the-art energy efficiency.
Microcontroller Overview
MCU Card / MCU
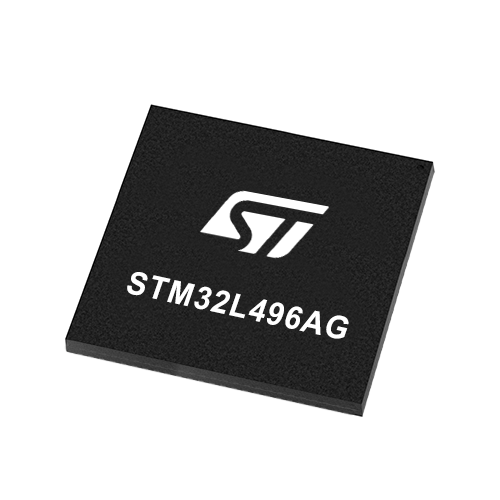
Architecture
ARM Cortex-M4
MCU Memory (KB)
1024
Silicon Vendor
STMicroelectronics
Pin count
169
RAM (Bytes)
327680
Used MCU Pins
mikroBUS™ mapper
Take a closer look
Click board™ Schematic
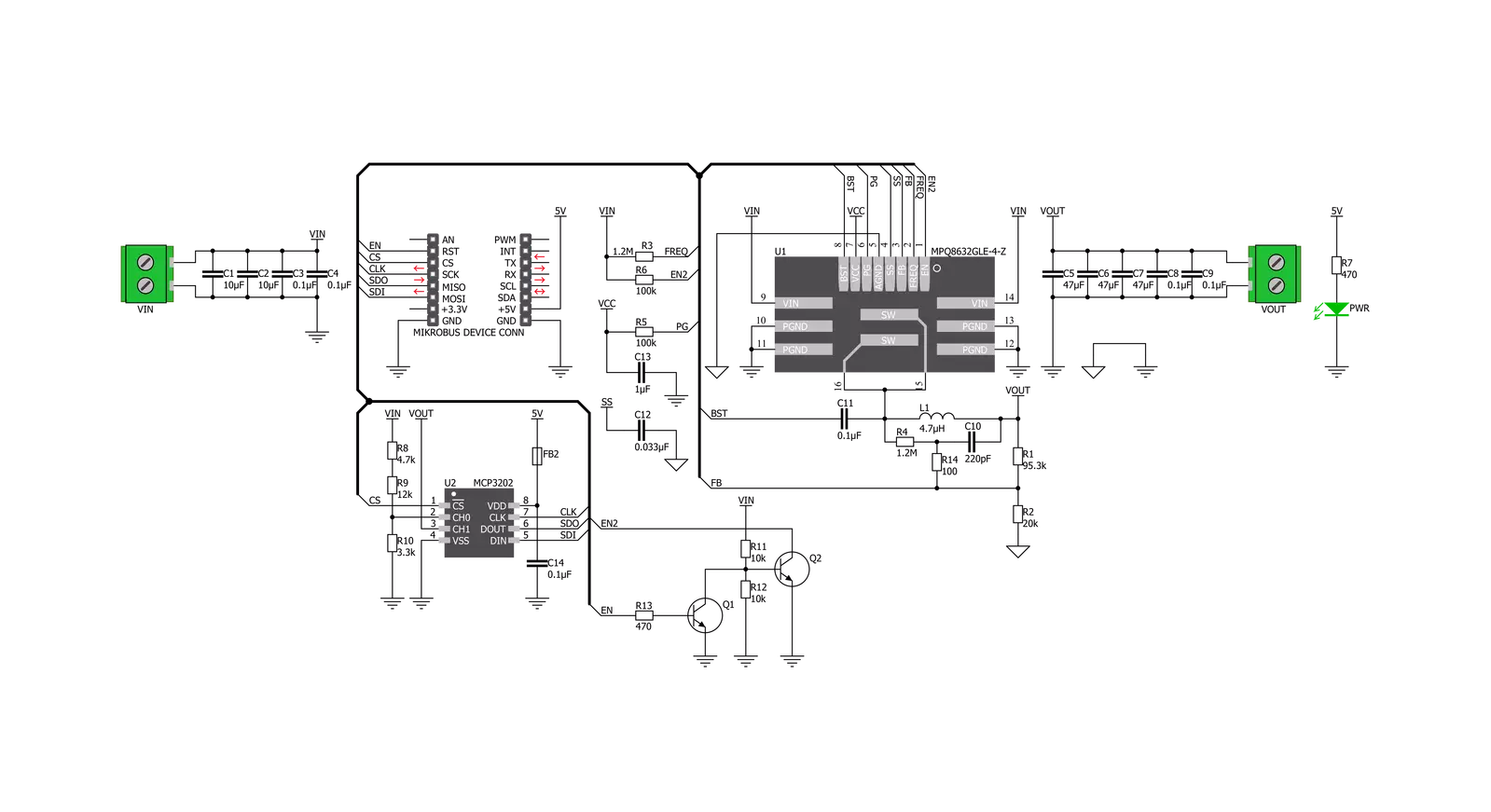
Step by step
Project assembly
Track your results in real time
Application Output
1. Application Output - In Debug mode, the 'Application Output' window enables real-time data monitoring, offering direct insight into execution results. Ensure proper data display by configuring the environment correctly using the provided tutorial.
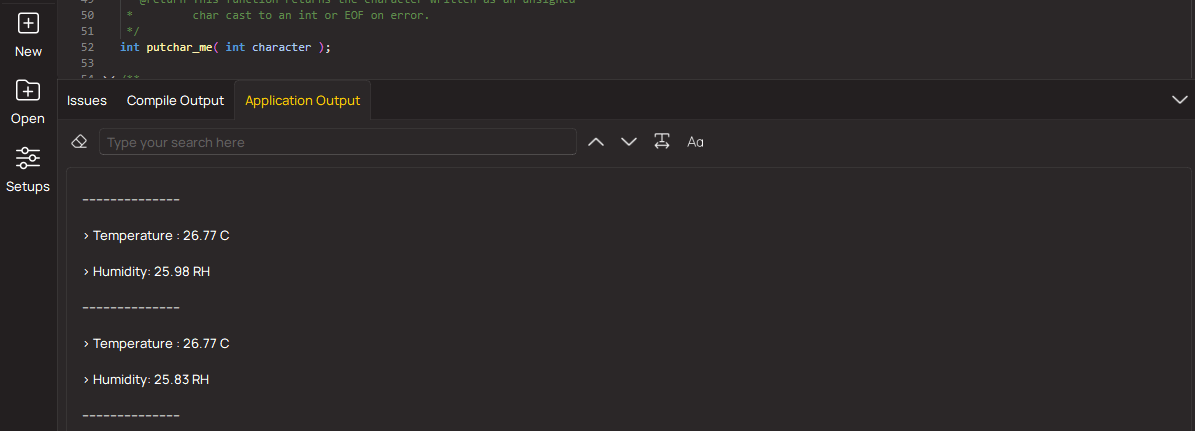
2. UART Terminal - Use the UART Terminal to monitor data transmission via a USB to UART converter, allowing direct communication between the Click board™ and your development system. Configure the baud rate and other serial settings according to your project's requirements to ensure proper functionality. For step-by-step setup instructions, refer to the provided tutorial.
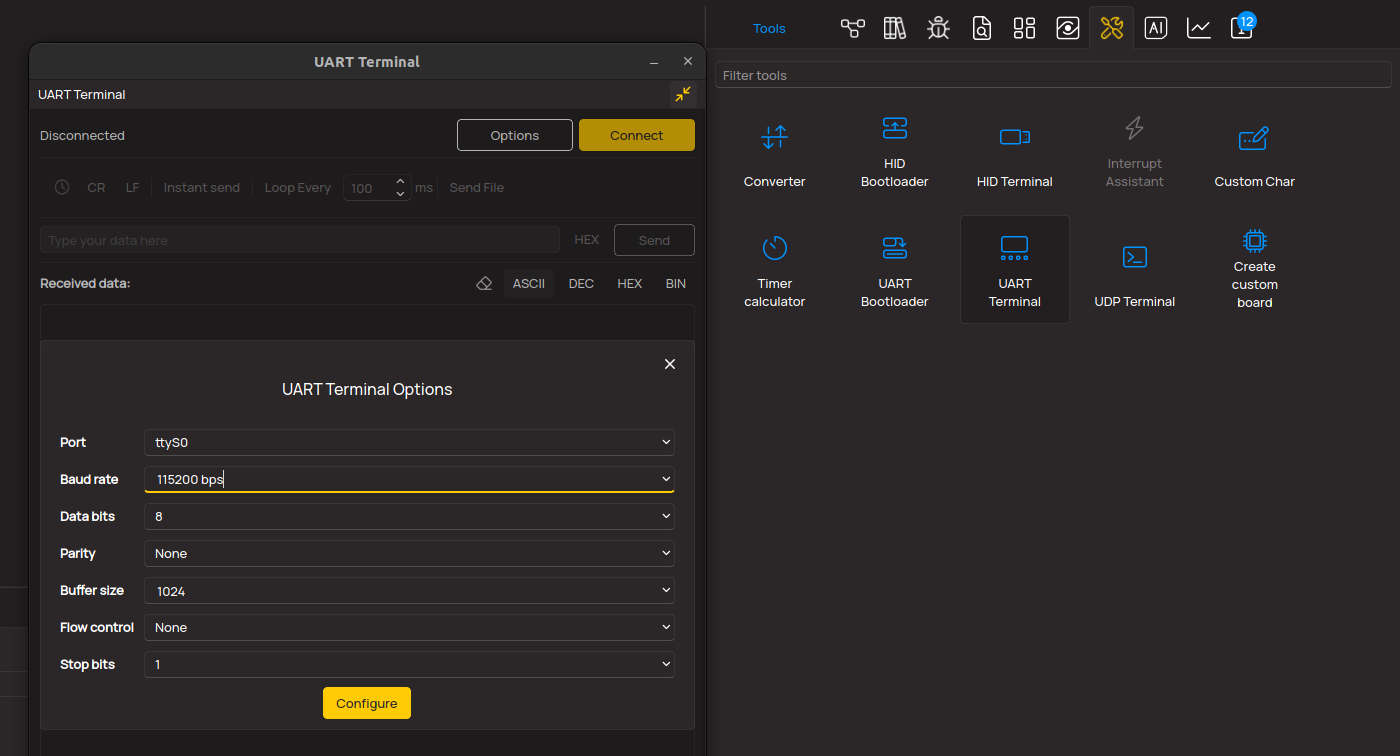
3. Plot Output - The Plot feature offers a powerful way to visualize real-time sensor data, enabling trend analysis, debugging, and comparison of multiple data points. To set it up correctly, follow the provided tutorial, which includes a step-by-step example of using the Plot feature to display Click board™ readings. To use the Plot feature in your code, use the function: plot(*insert_graph_name*, variable_name);. This is a general format, and it is up to the user to replace 'insert_graph_name' with the actual graph name and 'variable_name' with the parameter to be displayed.
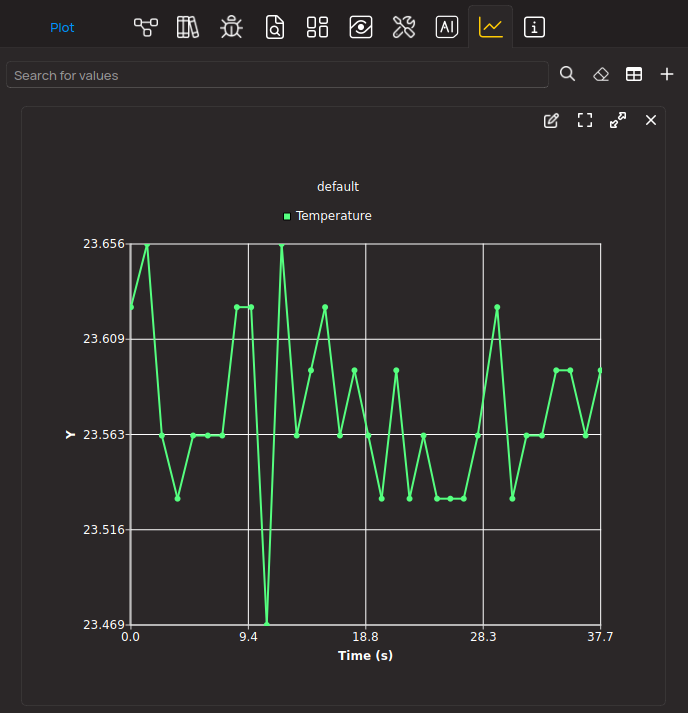
Software Support
Library Description
This library contains API for Buck 12 Click driver.
Key functions:
buck12_control
- This function for enable or disable devicebuck12_get_channel_adc
- This function reads ADC on the channelbuck12_get_voltage
- This function gets voltage
Open Source
Code example
The complete application code and a ready-to-use project are available through the NECTO Studio Package Manager for direct installation in the NECTO Studio. The application code can also be found on the MIKROE GitHub account.
/*!
* \file
* \brief Buck12 Click example
*
* # Description
* This demo application reads the voltage in [mV] at the input and output terminals.
*
* The demo application is composed of two sections :
*
* ## Application Init
* Configuring Clicks and log objects.
*
* ## Application Task
* Reads the voltage in [mV] at the input and output terminals.
* This data logs to the USBUART every 2 sec.
*
* \author MikroE Team
*
*/
// ------------------------------------------------------------------- INCLUDES
#include "board.h"
#include "log.h"
#include "buck12.h"
// ------------------------------------------------------------------ VARIABLES
static buck12_t buck12;
static log_t logger;
// ------------------------------------------------------ APPLICATION FUNCTIONS
void application_init ( void )
{
log_cfg_t log_cfg;
buck12_cfg_t cfg;
/**
* Logger initialization.
* Default baud rate: 115200
* Default log level: LOG_LEVEL_DEBUG
* @note If USB_UART_RX and USB_UART_TX
* are defined as HAL_PIN_NC, you will
* need to define them manually for log to work.
* See @b LOG_MAP_USB_UART macro definition for detailed explanation.
*/
LOG_MAP_USB_UART( log_cfg );
log_init( &logger, &log_cfg );
log_info( &logger, "---- Application Init ----" );
// Click initialization.
buck12_cfg_setup( &cfg );
BUCK12_MAP_MIKROBUS( cfg, MIKROBUS_1 );
buck12_init( &buck12, &cfg );
buck12_control( &buck12, BUCK12_ENABLE );
Delay_ms ( 1000 );
Delay_ms ( 1000 );
}
void application_task ( void )
{
float voltage;
voltage = buck12_get_voltage( &buck12, BUCK12_INPUT_VOLTAGE );
log_printf( &logger, "* Vin : %f mV \r\n ", voltage);
voltage = buck12_get_voltage( &buck12, BUCK12_OUTPUT_VOLTAGE );
log_printf( &logger, "* Vout : %f mV \r\n ", voltage);
log_printf( &logger, "--------------------------\r\n");
Delay_ms ( 1000 );
Delay_ms ( 1000 );
}
int main ( void )
{
/* Do not remove this line or clock might not be set correctly. */
#ifdef PREINIT_SUPPORTED
preinit();
#endif
application_init( );
for ( ; ; )
{
application_task( );
}
return 0;
}
// ------------------------------------------------------------------------ END
Additional Support
Resources
Category:Buck