Achieve stable DC-DC conversion with precise voltage control perfect for factory automation, data centers, and motor drives
A
A
Hardware Overview
How does it work?
Step Down 12 Click is based on the TPS62902, a synchronous step-down DC-DC converter from Texas Instruments. This converter uses the DCS-Control topology, an advanced control architecture that merges the strengths of hysteretic, voltage mode, and current mode control. DCS-Control enables rapid response to output voltage changes by sending feedback to a fast comparator stage, ensuring constant switching frequency under stable conditions and fast adaptability during dynamic load changes. This Click board™ accommodates a wide input voltage range from 3V to 17V through its VIN terminal, making it suitable for various standard power sources, including 12V supply lines, single or multiple Li-Ion cells, and 5V or 3.3V rails. It is suitable for numerous use cases, including factory automation, building automation, data center systems, enterprise computing, motor
drive applications, and beyond. It is designed with precision and delivers an output voltage accuracy of ±1% due to its DCS-Control-based regulation. Additionally, the TPS62902 enters power save mode during light loads to maximize efficiency, backed by a low quiescent current of just 4µA, ideal for energy-conscious applications. This Click board™ integrates the MCP4661, enabling the host MCU to configure 16 fixed output voltages on the VOUT terminal, adjustable from 0.7V to 5.5V. The MCP4661 communicates through a 2-wire I2C interface that supports clock speeds up to 3.4MHz, with I2C addresses adjustable via the onboard ADDR SEL jumpers. The MD pin allows users to select the TPS62902’s operational mode, enabling flexible configuration. This pin offers options for fixed PWM or automatic PFM/PWM mode with AEE functionality and settings for switching frequency,
internal/external feedback, output discharge, and PFM/PWM selection. The EN pin functions as the converter’s enable control, while the PG (Power Good) pin is an open-drain signal to confirm if the output voltage has reached its target. It also indicates when the device is turned off due to undervoltage lockout (UVLO) or thermal shutdown, enhancing system protection and operational feedback. This Click board™ can operate with either 3.3V or 5V logic voltage levels selected via the VCC SEL jumper. This way, both 3.3V and 5V capable MCUs can use the communication lines properly. Also, this Click board™ comes equipped with a library containing easy-to-use functions and an example code that can be used as a reference for further development.
Features overview
Development board
Arduino UNO is a versatile microcontroller board built around the ATmega328P chip. It offers extensive connectivity options for various projects, featuring 14 digital input/output pins, six of which are PWM-capable, along with six analog inputs. Its core components include a 16MHz ceramic resonator, a USB connection, a power jack, an
ICSP header, and a reset button, providing everything necessary to power and program the board. The Uno is ready to go, whether connected to a computer via USB or powered by an AC-to-DC adapter or battery. As the first USB Arduino board, it serves as the benchmark for the Arduino platform, with "Uno" symbolizing its status as the
first in a series. This name choice, meaning "one" in Italian, commemorates the launch of Arduino Software (IDE) 1.0. Initially introduced alongside version 1.0 of the Arduino Software (IDE), the Uno has since become the foundational model for subsequent Arduino releases, embodying the platform's evolution.
Microcontroller Overview
MCU Card / MCU
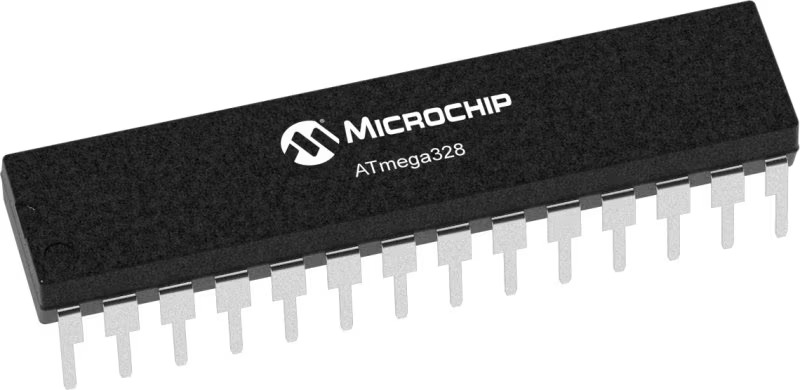
Architecture
AVR
MCU Memory (KB)
32
Silicon Vendor
Microchip
Pin count
32
RAM (Bytes)
2048
You complete me!
Accessories
Click Shield for Arduino UNO has two proprietary mikroBUS™ sockets, allowing all the Click board™ devices to be interfaced with the Arduino UNO board without effort. The Arduino Uno, a microcontroller board based on the ATmega328P, provides an affordable and flexible way for users to try out new concepts and build prototypes with the ATmega328P microcontroller from various combinations of performance, power consumption, and features. The Arduino Uno has 14 digital input/output pins (of which six can be used as PWM outputs), six analog inputs, a 16 MHz ceramic resonator (CSTCE16M0V53-R0), a USB connection, a power jack, an ICSP header, and reset button. Most of the ATmega328P microcontroller pins are brought to the IO pins on the left and right edge of the board, which are then connected to two existing mikroBUS™ sockets. This Click Shield also has several switches that perform functions such as selecting the logic levels of analog signals on mikroBUS™ sockets and selecting logic voltage levels of the mikroBUS™ sockets themselves. Besides, the user is offered the possibility of using any Click board™ with the help of existing bidirectional level-shifting voltage translators, regardless of whether the Click board™ operates at a 3.3V or 5V logic voltage level. Once you connect the Arduino UNO board with our Click Shield for Arduino UNO, you can access hundreds of Click boards™, working with 3.3V or 5V logic voltage levels.
Used MCU Pins
mikroBUS™ mapper
Take a closer look
Click board™ Schematic
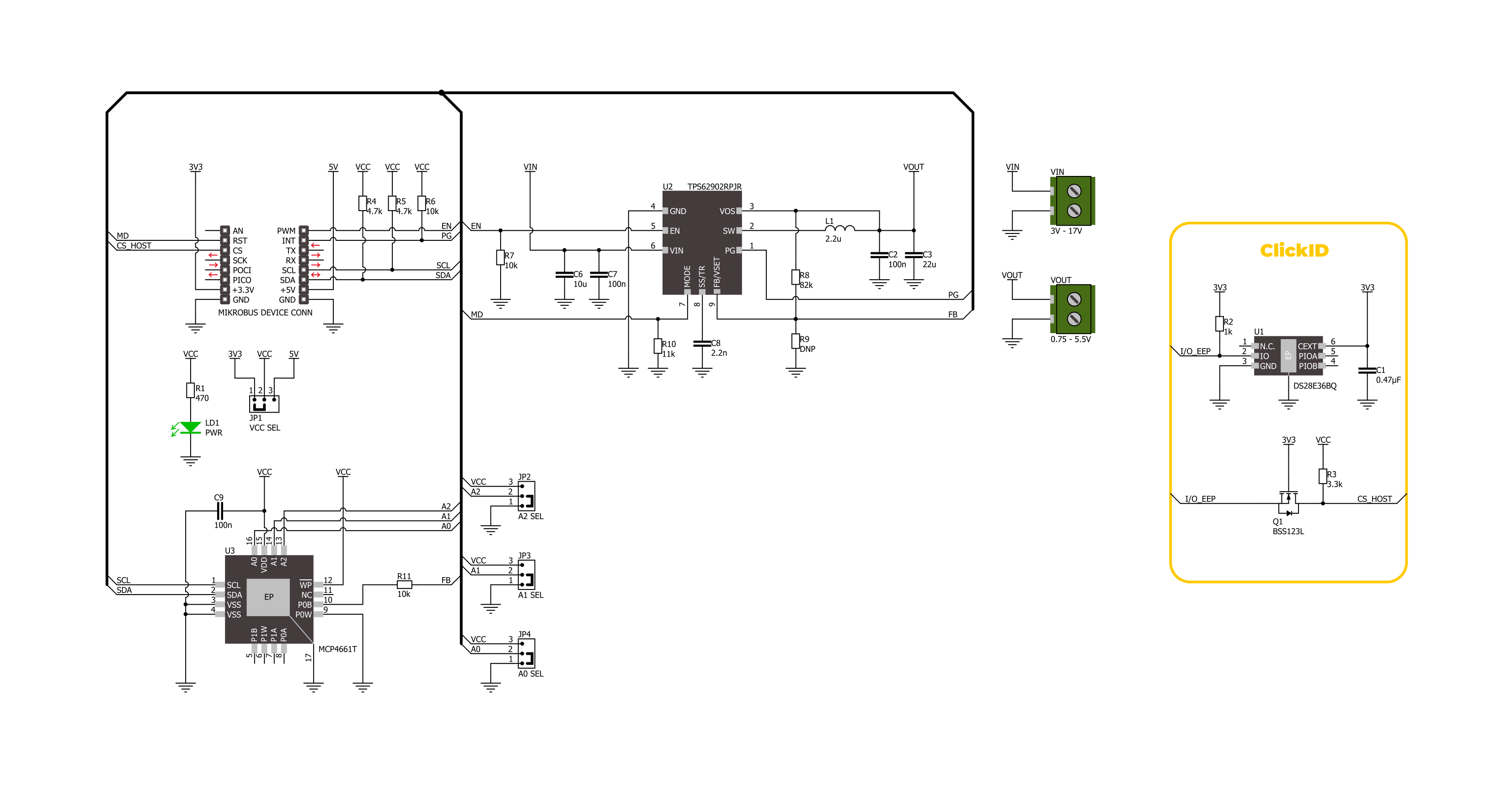
Step by step
Project assembly
Track your results in real time
Application Output
1. Application Output - In Debug mode, the 'Application Output' window enables real-time data monitoring, offering direct insight into execution results. Ensure proper data display by configuring the environment correctly using the provided tutorial.
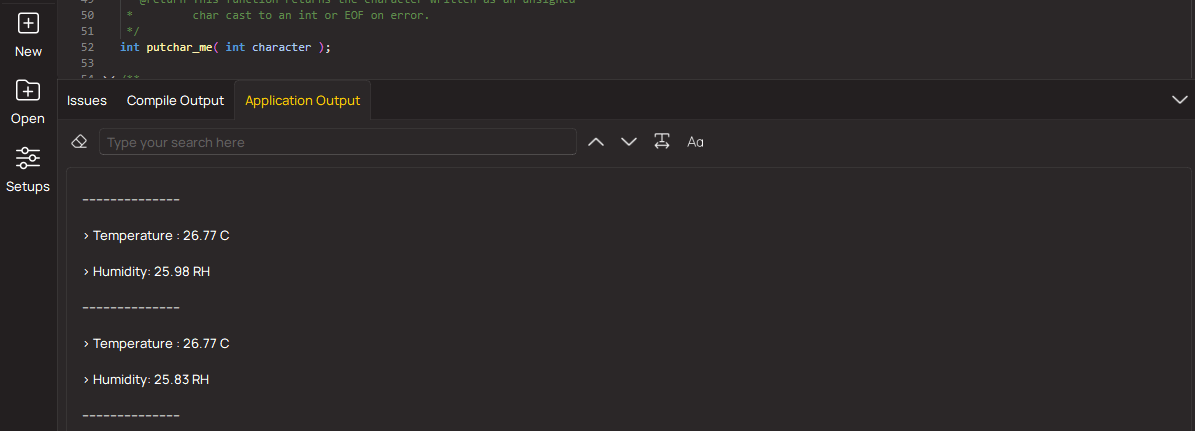
2. UART Terminal - Use the UART Terminal to monitor data transmission via a USB to UART converter, allowing direct communication between the Click board™ and your development system. Configure the baud rate and other serial settings according to your project's requirements to ensure proper functionality. For step-by-step setup instructions, refer to the provided tutorial.
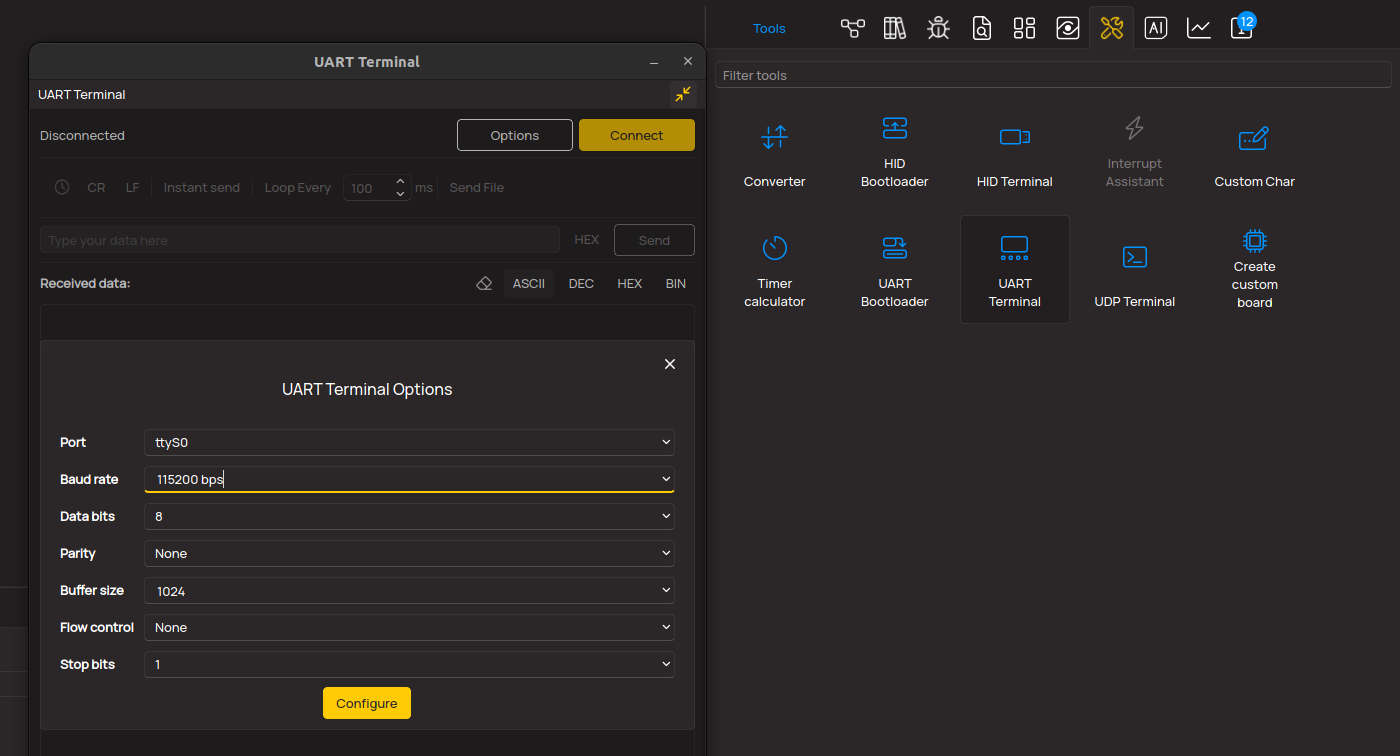
3. Plot Output - The Plot feature offers a powerful way to visualize real-time sensor data, enabling trend analysis, debugging, and comparison of multiple data points. To set it up correctly, follow the provided tutorial, which includes a step-by-step example of using the Plot feature to display Click board™ readings. To use the Plot feature in your code, use the function: plot(*insert_graph_name*, variable_name);. This is a general format, and it is up to the user to replace 'insert_graph_name' with the actual graph name and 'variable_name' with the parameter to be displayed.
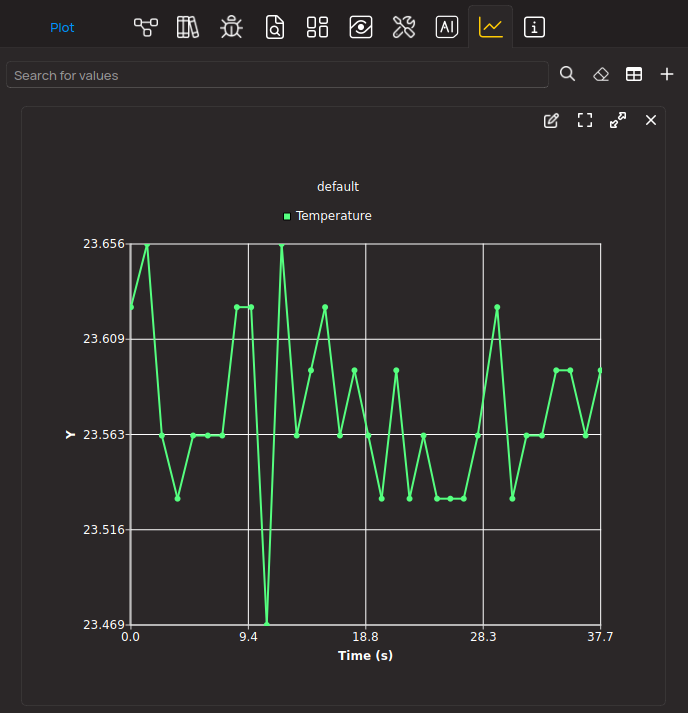
Software Support
Library Description
This library contains API for Step Down 12 Click driver.
Key functions:
stepdown12_get_pg_pin
- This function returns the power good (PG) pin logic state.stepdown12_set_vout
- This function sets the voltage output by setting the digipot wiper resistance.stepdown12_enable_device
- This function enables the device by setting the EN pin to high logic state.
Open Source
Code example
The complete application code and a ready-to-use project are available through the NECTO Studio Package Manager for direct installation in the NECTO Studio. The application code can also be found on the MIKROE GitHub account.
/*!
* @file main.c
* @brief Step Down 12 Click example
*
* # Description
* This example demonstrates the use of Step Down 12 Click board by
* changing the output voltage every 3 seconds.
*
* The demo application is composed of two sections :
*
* ## Application Init
* Initializes the driver and performs the Click default configuration.
*
* ## Application Task
* Changes the output voltage every 3 seconds from MAX (5.5V) to MIN (1.05V) in steps of 0.5V
* and displays the currently set voltage output value on the USB UART. It also monitors
* the power good fault indication.
*
* @author Stefan Filipovic
*
*/
#include "board.h"
#include "log.h"
#include "stepdown12.h"
static stepdown12_t stepdown12;
static log_t logger;
void application_init ( void )
{
log_cfg_t log_cfg; /**< Logger config object. */
stepdown12_cfg_t stepdown12_cfg; /**< Click config object. */
/**
* Logger initialization.
* Default baud rate: 115200
* Default log level: LOG_LEVEL_DEBUG
* @note If USB_UART_RX and USB_UART_TX
* are defined as HAL_PIN_NC, you will
* need to define them manually for log to work.
* See @b LOG_MAP_USB_UART macro definition for detailed explanation.
*/
LOG_MAP_USB_UART( log_cfg );
log_init( &logger, &log_cfg );
log_info( &logger, " Application Init " );
// Click initialization.
stepdown12_cfg_setup( &stepdown12_cfg );
STEPDOWN12_MAP_MIKROBUS( stepdown12_cfg, MIKROBUS_1 );
if ( I2C_MASTER_ERROR == stepdown12_init( &stepdown12, &stepdown12_cfg ) )
{
log_error( &logger, " Communication init." );
for ( ; ; );
}
stepdown12_default_cfg ( &stepdown12 );
log_info( &logger, " Application Task " );
}
void application_task ( void )
{
static float vout = STEPDOWN12_VOUT_MAX;
if ( !stepdown12_get_pg_pin ( &stepdown12 ) )
{
log_error( &logger, " Power Good Fault - Vout is below nominal regulation\r\n" );
}
if ( STEPDOWN12_OK == stepdown12_set_vout ( &stepdown12, vout ) )
{
log_printf( &logger, " Vout: %.3f V\r\n\n", vout );
vout -= 0.5;
if ( vout < STEPDOWN12_VOUT_MIN )
{
vout = STEPDOWN12_VOUT_MAX;
}
}
Delay_ms ( 1000 );
Delay_ms ( 1000 );
Delay_ms ( 1000 );
}
int main ( void )
{
/* Do not remove this line or clock might not be set correctly. */
#ifdef PREINIT_SUPPORTED
preinit();
#endif
application_init( );
for ( ; ; )
{
application_task( );
}
return 0;
}
// ------------------------------------------------------------------------ END
Additional Support
Resources
Category:Buck