Our advanced ammeter provides real-time measurement of electric currents, empowering you with instant and accurate data to optimize efficiency and ensure safe operations
A
A
Hardware Overview
How does it work?
Ammeter Click is based on the AD8616, a precision 20MHz CMOS rail-to-rail input/output operational amplifier from Analog Devices. It is a dual single-supply amplifier featuring very low offset voltage, wide signal bandwidth, and low input voltage and current noise. The AD8616 uses a patented trimming technique that achieves superior precision without laser trimming. Two onboard screw terminals labeled probe+ and probe-are bringing in the current, which then passes through a shunt resistor. A voltage proportional to the strength of the current is generated across the resistor, which is then processed in the operational
amplifier. The voltage amplified through the AD8616 can be directly monitored through the AN pin of the mikroBUS™ socket. One of the main features of the Ammeter Click is the MCP3201, a 12-bit A/D converter with the SPI serial interface from Microchip. This A/D converter has a sampling rate of up to 100ksps and has an onboard sample and hold circuitry. It provides a single pseudo-differential input with maximum differential nonlinearity at ±1LSB. The AD8616 fed the amplified current to this A/D convertor, which gets the 2.048V reference voltage from the MAX6106, a micropower low-dropout high-output-current
voltage reference from Analog Devices. The MCP3201 outputs digital value through the mikroBUS™ socket SPI interface to the host MCU. This Click board™ can operate with either 3.3V or 5V logic voltage levels selected via the PWR SEL jumper. This way, both 3.3V and 5V capable MCUs can use the communication lines properly. Also, this Click board™ comes equipped with a library containing easy-to-use functions and an example code that can be used, as a reference, for further development.
Features overview
Development board
PIC32MZ Clicker is a compact starter development board that brings the flexibility of add-on Click boards™ to your favorite microcontroller, making it a perfect starter kit for implementing your ideas. It comes with an onboard 32-bit PIC32MZ microcontroller with FPU from Microchip, a USB connector, LED indicators, buttons, a mikroProg connector, and a header for interfacing with external electronics. Thanks to its compact design with clear and easy-recognizable silkscreen markings, it provides a fluid and immersive working experience, allowing access anywhere and under
any circumstances. Each part of the PIC32MZ Clicker development kit contains the components necessary for the most efficient operation of the same board. In addition to the possibility of choosing the PIC32MZ Clicker programming method, using USB HID mikroBootloader, or through an external mikroProg connector for PIC, dsPIC, or PIC32 programmer, the Clicker board also includes a clean and regulated power supply module for the development kit. The USB Micro-B connection can provide up to 500mA of current, which is more than enough to operate all onboard
and additional modules. All communication methods that mikroBUS™ itself supports are on this board, including the well-established mikroBUS™ socket, reset button, and several buttons and LED indicators. PIC32MZ Clicker is an integral part of the Mikroe ecosystem, allowing you to create a new application in minutes. Natively supported by Mikroe software tools, it covers many aspects of prototyping thanks to a considerable number of different Click boards™ (over a thousand boards), the number of which is growing every day.
Microcontroller Overview
MCU Card / MCU
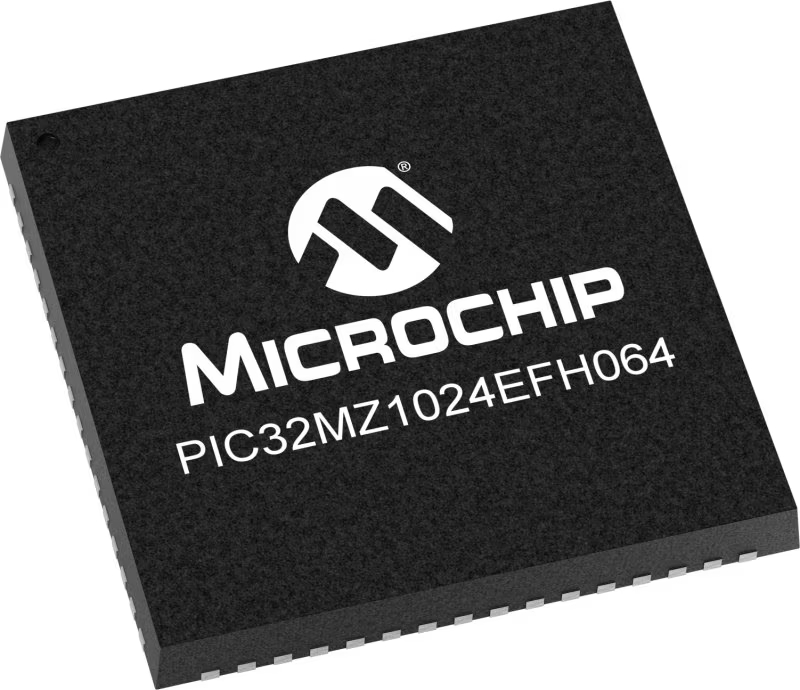
Architecture
PIC32
MCU Memory (KB)
1024
Silicon Vendor
Microchip
Pin count
64
RAM (Bytes)
524288
Used MCU Pins
mikroBUS™ mapper
Take a closer look
Click board™ Schematic
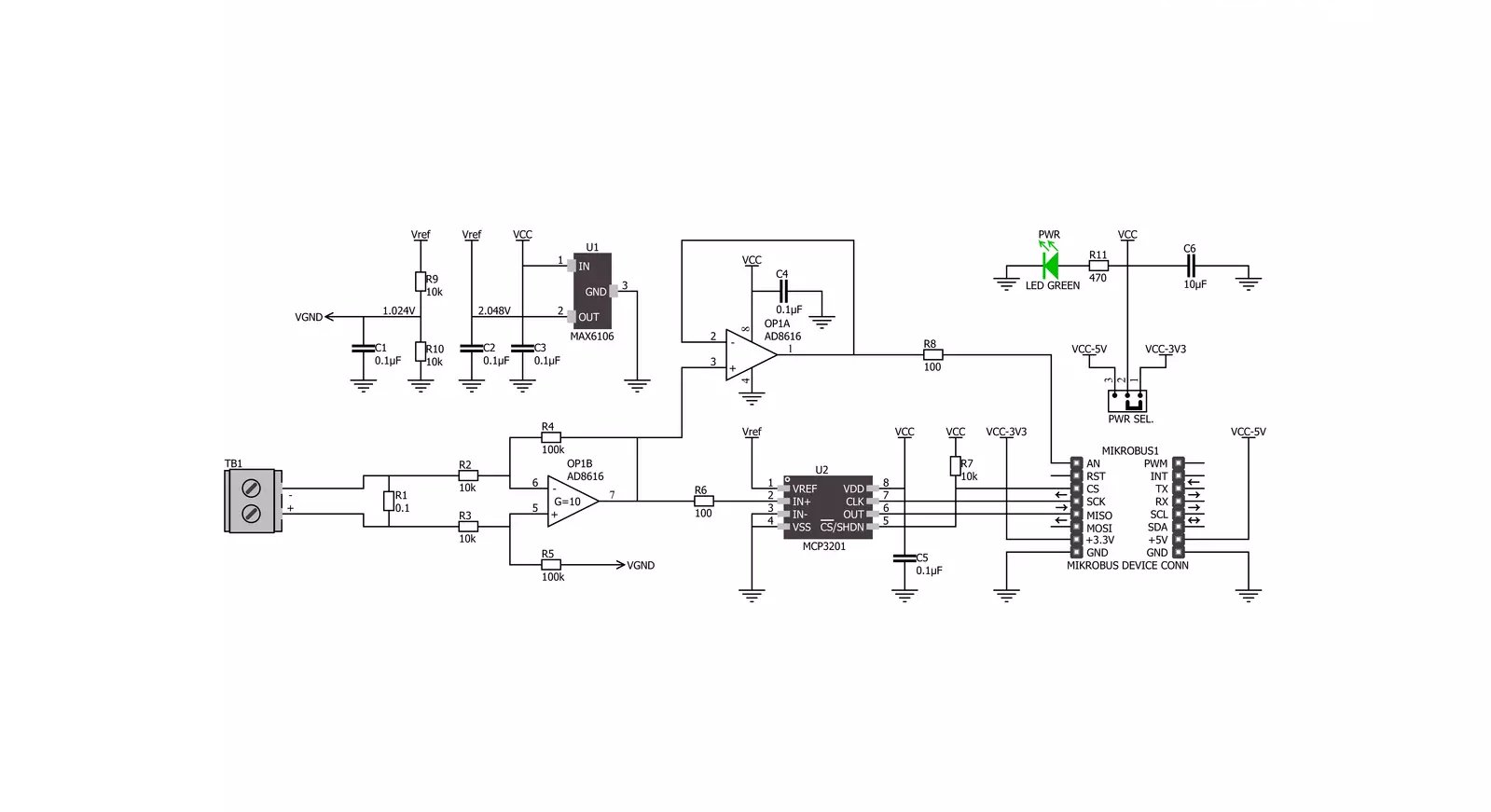
Step by step
Project assembly
Track your results in real time
Application Output
1. Application Output - In Debug mode, the 'Application Output' window enables real-time data monitoring, offering direct insight into execution results. Ensure proper data display by configuring the environment correctly using the provided tutorial.
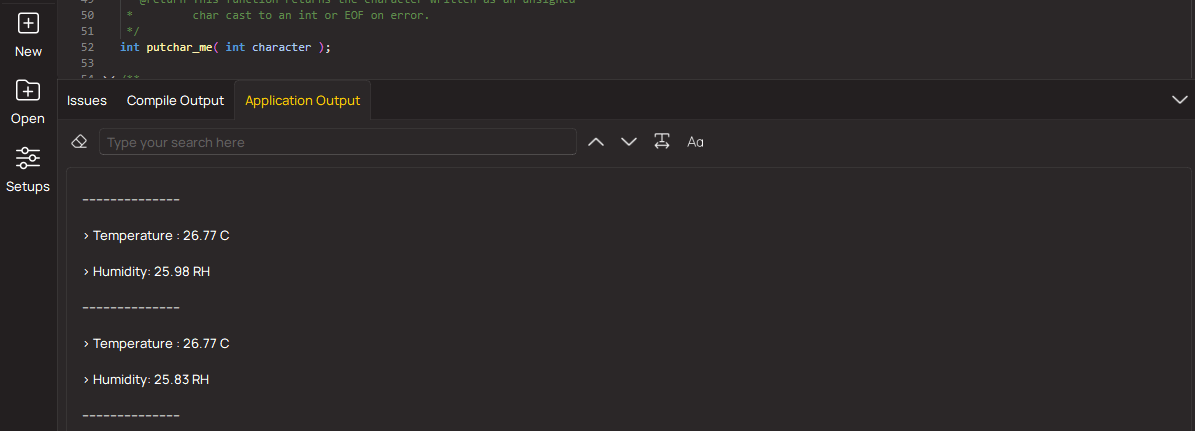
2. UART Terminal - Use the UART Terminal to monitor data transmission via a USB to UART converter, allowing direct communication between the Click board™ and your development system. Configure the baud rate and other serial settings according to your project's requirements to ensure proper functionality. For step-by-step setup instructions, refer to the provided tutorial.
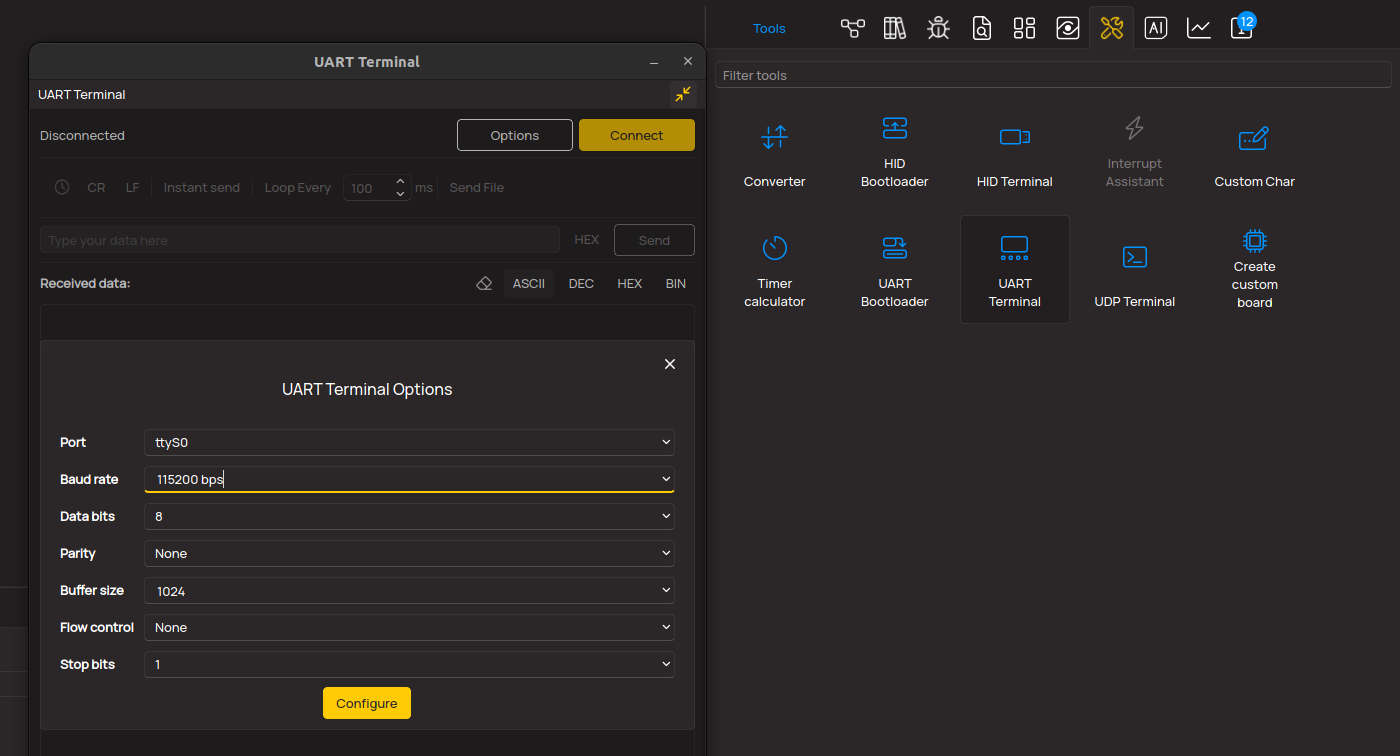
3. Plot Output - The Plot feature offers a powerful way to visualize real-time sensor data, enabling trend analysis, debugging, and comparison of multiple data points. To set it up correctly, follow the provided tutorial, which includes a step-by-step example of using the Plot feature to display Click board™ readings. To use the Plot feature in your code, use the function: plot(*insert_graph_name*, variable_name);. This is a general format, and it is up to the user to replace 'insert_graph_name' with the actual graph name and 'variable_name' with the parameter to be displayed.
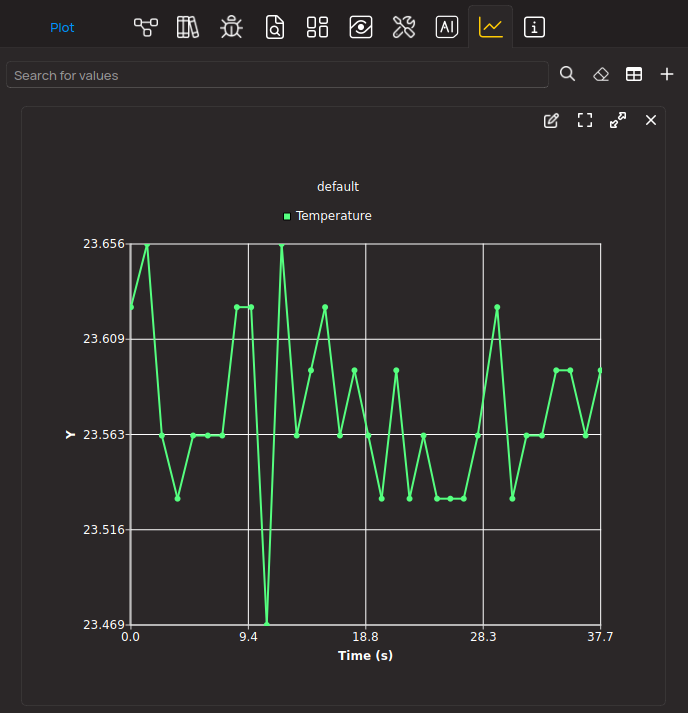
Software Support
Library Description
This library contains API for Ammeter Click driver.
Key functions:
ammeter_amperage
- Function is used to measure amperage of a power consumer connected to the Ammeter Click
Open Source
Code example
The complete application code and a ready-to-use project are available through the NECTO Studio Package Manager for direct installation in the NECTO Studio. The application code can also be found on the MIKROE GitHub account.
/*!
* \file
* \brief Ammeter Click example
*
* # Description
* Demo app measures and displays current by using Ammeter Click board.
*
* The demo application is composed of two sections :
*
* ## Application Init
* Initalizes SPI, LOG and Click drivers.
*
* ## Application Task
* This is an example that shows the capabilities of the Ammeter Click by
* measuring amperage in miliampers. Ammeter Click board can be used to saftly
* measure current up to 1A both AC and DC, in the case of AC,
* for peak to peak value.
*
* *note:*
* It is important to notice that this Click board has its' own electronic
* circuit, and may not be powered from the same source which we are measuring.
* Result will not be correct in that case.
*
* \author Jovan Stajkovic
*
*/
// ------------------------------------------------------------------- INCLUDES
#include "board.h"
#include "log.h"
#include "ammeter.h"
// ------------------------------------------------------------------ VARIABLES
static ammeter_t ammeter;
static log_t logger;
static float amperage;
// ------------------------------------------------------ APPLICATION FUNCTIONS
void application_init ( void )
{
log_cfg_t log_cfg;
ammeter_cfg_t cfg;
/**
* Logger initialization.
* Default baud rate: 115200
* Default log level: LOG_LEVEL_DEBUG
* @note If USB_UART_RX and USB_UART_TX
* are defined as HAL_PIN_NC, you will
* need to define them manually for log to work.
* See @b LOG_MAP_USB_UART macro definition for detailed explanation.
*/
LOG_MAP_USB_UART( log_cfg );
log_init( &logger, &log_cfg );
log_info( &logger, "---- Application Init ----" );
// Click initialization.
ammeter_cfg_setup( &cfg );
AMMETER_MAP_MIKROBUS( cfg, MIKROBUS_1 );
ammeter_init( &ammeter, &cfg );
log_printf( &logger, "-----------------------\r\n" );
log_printf( &logger, " Ammeter Click \r\n" );
log_printf( &logger, "-----------------------\r\n" );
}
void application_task ( void )
{
amperage = ammeter_amperage( &ammeter );
log_printf( &logger, " Current: %.2f mA\r\n", amperage );
log_printf( &logger, "-----------------------\r\n" );
Delay_ms ( 1000 );
}
int main ( void )
{
/* Do not remove this line or clock might not be set correctly. */
#ifdef PREINIT_SUPPORTED
preinit();
#endif
application_init( );
for ( ; ; )
{
application_task( );
}
return 0;
}
// ------------------------------------------------------------------------ END