Your quest for precise angle information ends here – our solution, powered by magnetic insight, is your go-to tool for obtaining accurate and instantaneous measurements in any environment.
A
A
Hardware Overview
How does it work?
Magneto 14 Click is based on the MA735, a contactless angle sensor with ABZ and PWM output from Monolithic Power Systems. It can detect the absolute angular position of a permanent magnet, typically a diametrically magnetized cylinder on a rotating shaft. The adjustable digital filtering can optimize control loop performance when used in servo applications. In addition, the sensor features magnetic field strength detection with a programmable threshold and on-chip non-volatile memory. This memory can store configuration parameters, including magnetic field detection thresholds, ABZ encoder settings, and reference zero-angle positions. The frequency of the PWM output of the sensor is up to 1090Hz with a 14-bit resolution. The MA735 uses integrated Hall devices to detect the magnetic field, while the angle is measured using MPS’s proprietary Spinaxis™
method. This method is based on phase detection and digitizes the direction of the field directly, generating a sinusoidal signal with a phase that represents the angle of the field. The angle is obtained from a signal by a time-to-digital converter, and the digital number proportional to the magnetic field is delivered at a rate of 1MHz. Two headers on this Click board™ allow additional functionalities. The SSI header with SSD and SCK pins is a 2-wire synchronous serial interface for data reading only and can be used for angle reading operation. The INC OUT header is an incremental output encoder with A, B, and Z pins. The ABZ encoder emulates a 12-bit incremental encoder (like an optical encoder), providing logic pulses per turn from 1 to 1024 in quadrature. A unique addition to this board is a position for a Rotary Magnet Holder designed to be used alongside a magnetic contactless angle sensor,
allowing fast prototyping and quick measurements during development. The Magneto 14 Click uses a standard 4-Wire SPI serial interface with a maximum supported clock rate of 25MHz. The PWM absolute output provides a logic signal with a duty cycle proportional to the angle of the magnetic field on the pin PWM of the mikroBUS™ socket. This sensor has two thresholds, MGL and MGH, for low and high magnetic fields. The magnetic field high threshold (MFHT) is indicated over the MGH interrupt pin, together with an additional MGH red LED. This Click board™ can be operated only with a 3.3V logic voltage level. The board must perform appropriate logic voltage level conversion before using MCUs with different logic levels. Also, it comes equipped with a library containing functions and an example code that can be used as a reference for further development.
Features overview
Development board
Clicker 4 for PIC18F is a compact development board designed as a complete solution to build your own gadgets with unique functionalities quickly. It features a PIC18F97J94MCU, four mikroBUS™ sockets for Click boards™ connectivity, power management, and more, and it is a perfect solution for the rapid development of many different types of applications. At its core is an 8-bit PIC18F97J94 MCU, a powerful microcontroller produced by Microchip, based on the high-performance CPU with two external clock modes, up to 64MHz. It
provides sufficient processing power for the most demanding tasks, allowing Clicker 4 to adapt to any specific application requirements. Besides two 1x20 pin headers, four improved mikroBUS™ sockets represent the most distinctive connectivity feature, allowing access to a huge base of Click boards™, growing on a daily basis. Each section of Clicker 4 is clearly marked, offering an intuitive and clean interface. This makes working with the development board much simpler and, thus, faster. The usability of Clicker 4 doesn’t end with its ability
to accelerate the prototyping and application development stages: it is designed as a complete solution that can be implemented directly into any project, with no additional hardware modifications required. Four mounting holes [4.2mm/0.165”] at all four corners allow simple installation by using mounting screws. For most applications, a nice, stylish casing is all that is needed to turn the Clicker 4 development board into a fully functional, custom design.
Microcontroller Overview
MCU Card / MCU
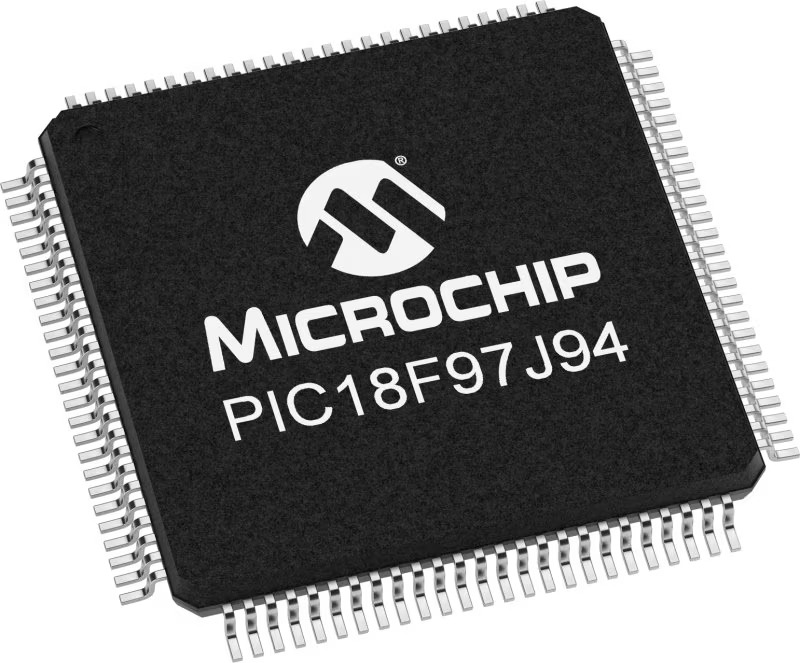
Architecture
PIC
MCU Memory (KB)
128
Silicon Vendor
Microchip
Pin count
100
RAM (Bytes)
3862
You complete me!
Accessories
Rotary Magnetic Holder is an addition designed for use alongside a magnetic rotary position sensor. It comes with a plastic stand measuring 22x16x10 millimeters (L x W x H), as well as an adjustable shaft with a 6mm diameter magnet. The plastic frame has four round feet that fit into holes in the board near the magnetic rotary position sensor, with a 6mm diameter hole on top to match the adjustable shaft that carries the magnet. This shaft has a height adjustment screw on it, allowing the user to adjust it between 18 and 22 millimeters. This way, fast prototyping and quick measurements of the magnet characteristics are allowed during development.
Used MCU Pins
mikroBUS™ mapper
Take a closer look
Click board™ Schematic
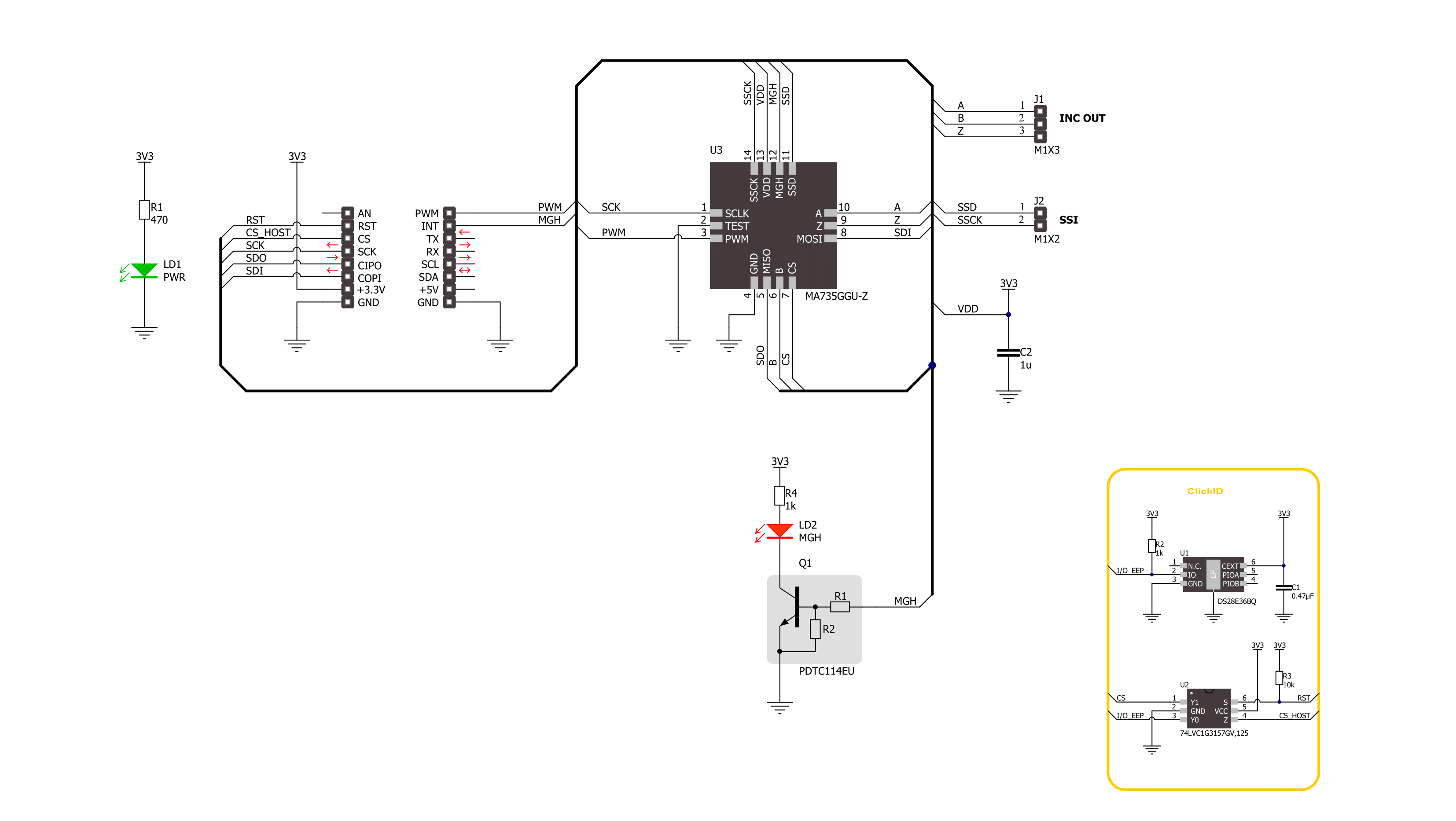
Step by step
Project assembly
Track your results in real time
Application Output
1. Application Output - In Debug mode, the 'Application Output' window enables real-time data monitoring, offering direct insight into execution results. Ensure proper data display by configuring the environment correctly using the provided tutorial.
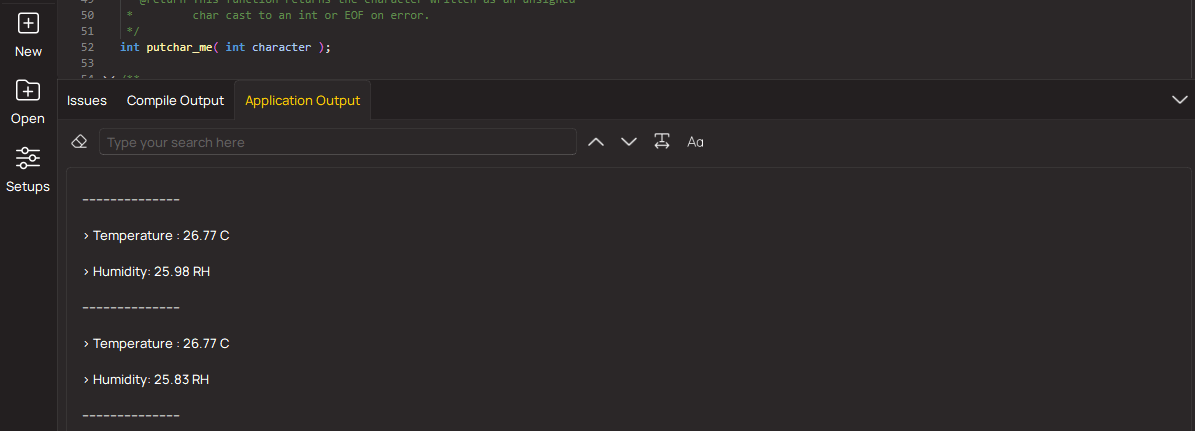
2. UART Terminal - Use the UART Terminal to monitor data transmission via a USB to UART converter, allowing direct communication between the Click board™ and your development system. Configure the baud rate and other serial settings according to your project's requirements to ensure proper functionality. For step-by-step setup instructions, refer to the provided tutorial.
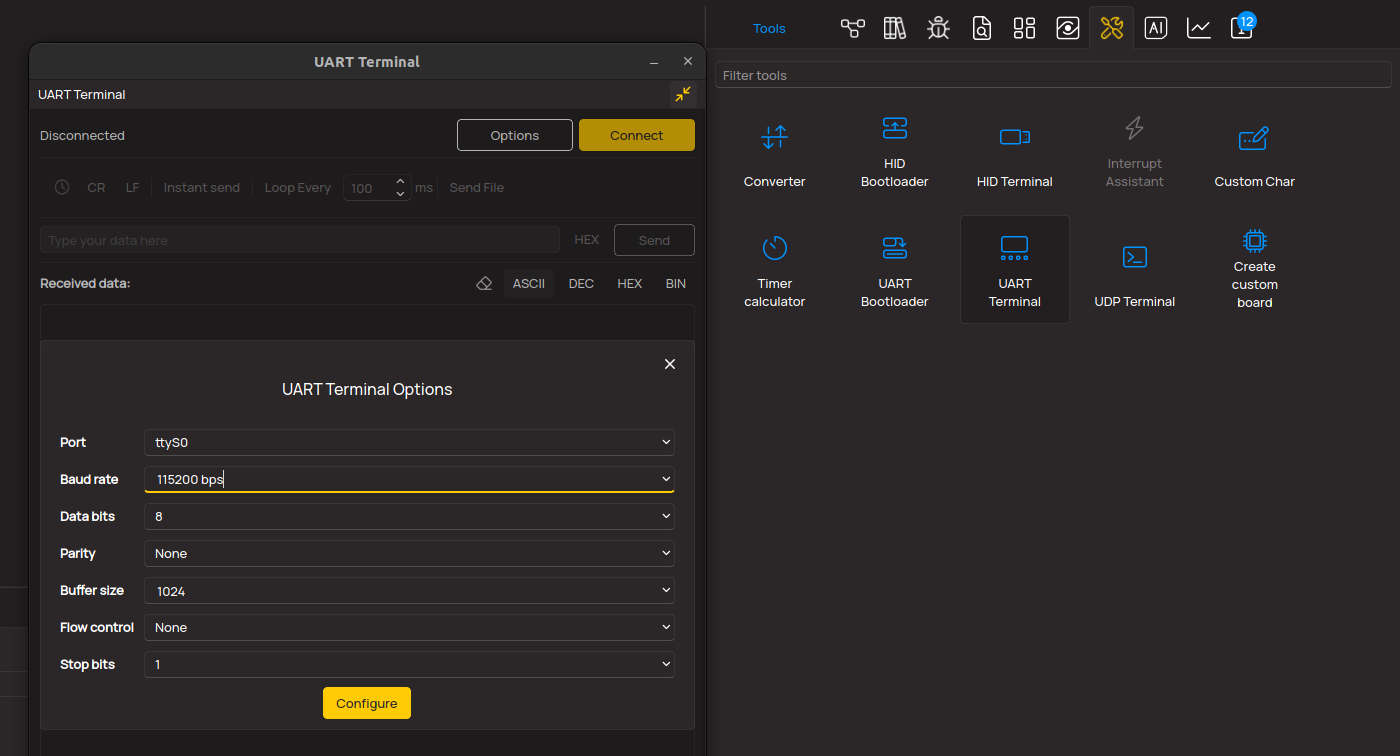
3. Plot Output - The Plot feature offers a powerful way to visualize real-time sensor data, enabling trend analysis, debugging, and comparison of multiple data points. To set it up correctly, follow the provided tutorial, which includes a step-by-step example of using the Plot feature to display Click board™ readings. To use the Plot feature in your code, use the function: plot(*insert_graph_name*, variable_name);. This is a general format, and it is up to the user to replace 'insert_graph_name' with the actual graph name and 'variable_name' with the parameter to be displayed.
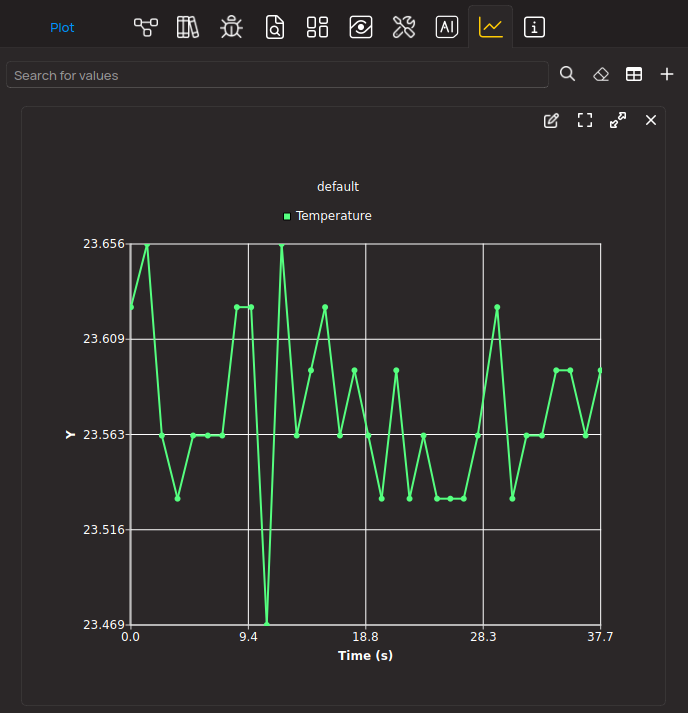
Software Support
Library Description
This library contains API for Magneto 14 Click driver.
Key functions:
magneto14_get_angle
- Magneto 14 gets the angular position function.magneto14_get_field_strength
- Magneto 14 gets the magnetic field strength function.magneto14_get_mgh
- Magneto 14 gets the MGH function.
Open Source
Code example
The complete application code and a ready-to-use project are available through the NECTO Studio Package Manager for direct installation in the NECTO Studio. The application code can also be found on the MIKROE GitHub account.
/*!
* @file main.c
* @brief Magneto 14 Click example
*
* # Description
* This library contains API for the Magneto 14 Click driver.
* The demo application reads and displays
* the magnet's angular position in degrees.
*
* The demo application is composed of two sections :
*
* ## Application Init
* Initialization of SPI module and log UART.
* After driver initialization, the app executes a default configuration.
*
* ## Application Task
* This example demonstrates the use of the Magneto 14 Click board™.
* Reads and displays the magnet's angular position in degrees.
* Results are being sent to the UART Terminal, where you can track their changes.
*
* @author Nenad Filipovic
*
*/
#include "board.h"
#include "log.h"
#include "magneto14.h"
static magneto14_t magneto14;
static log_t logger;
void application_init ( void )
{
log_cfg_t log_cfg; /**< Logger config object. */
magneto14_cfg_t magneto14_cfg; /**< Click config object. */
/**
* Logger initialization.
* Default baud rate: 115200
* Default log level: LOG_LEVEL_DEBUG
* @note If USB_UART_RX and USB_UART_TX
* are defined as HAL_PIN_NC, you will
* need to define them manually for log to work.
* See @b LOG_MAP_USB_UART macro definition for detailed explanation.
*/
LOG_MAP_USB_UART( log_cfg );
log_init( &logger, &log_cfg );
log_info( &logger, " Application Init " );
// Click initialization.
magneto14_cfg_setup( &magneto14_cfg );
MAGNETO14_MAP_MIKROBUS( magneto14_cfg, MIKROBUS_1 );
if ( SPI_MASTER_ERROR == magneto14_init( &magneto14, &magneto14_cfg ) )
{
log_error( &logger, " Communication init." );
for ( ; ; );
}
if ( MAGNETO14_ERROR == magneto14_default_cfg ( &magneto14 ) )
{
log_error( &logger, " Default configuration." );
for ( ; ; );
}
log_info( &logger, " Application Task " );
log_printf( &logger, " -------------------- \r\n" );
Delay_ms ( 100 );
}
void application_task ( void )
{
static uint8_t field_strength = 0;
static float angle = 0;
if ( MAGNETO14_OK == magneto14_get_field_strength( &magneto14, &field_strength ) )
{
if ( ( MAGNETO14_FLD_ST_OK == field_strength ) &&
( MAGNETO14_MGH_ST_OK == magneto14_get_mgh( &magneto14 ) ) &&
( MAGNETO14_OK == magneto14_get_angle( &magneto14, &angle ) ) )
{
log_printf( &logger, " Angle: %.2f [deg]\r\n", angle );
log_printf( &logger, " -------------------- \r\n" );
Delay_ms ( 1000 );
}
}
}
int main ( void )
{
/* Do not remove this line or clock might not be set correctly. */
#ifdef PREINIT_SUPPORTED
preinit();
#endif
application_init( );
for ( ; ; )
{
application_task( );
}
return 0;
}
// ------------------------------------------------------------------------ END