Discover how linear magnetic displacement sensors redefine precision in countless industries, offering a world of opportunities for accurate position tracking and control
A
A
Hardware Overview
How does it work?
Magnetic linear Click is based on the HMC1501, a linear magnetic displacement sensor from Honeywell. The key feature of the HMC1501 IC is the high accuracy of the magnetic field sensing. Unlike most of the magnetic sensors on the market which rely on the Hall-effect, the integrated sensors of the HMC1501 IC are produced using the Honeywell’s proprietary Anisotropic Magneto-Resistive (AMR) technology, which yields an absolute magnetic angle sensing with the angular error of only 0.07° in the range of ±45°. The magneto-resistive sensing elements form a single saturated-mode Wheatstone bridge, positioned in the XZ plane (parallel with the surface of the IC). The bridge is positioned towards the edge of the IC casing, allowing which is the optimal position for linear sensing applications. The IC outputs an analog differential voltage with respect to the angle of the magnetic field. The voltage from the selected mikroBUS™ power rail is directly applied to the internal Wheatstone bridge
of the HMC1501. By construction, in the absence of the magnetic field, its outputs will be set at half the supply voltage (with the small offset of 3mV/V typically). The same applies if there is a magnetic field present, but it is positioned at 0° (zero-crossing) in respect to the bridge. In both cases all the magneto-resistive elements forming the bridge, will have identical resistances. Once the magnetic field is applied in any direction in the range of ±45°, the bridge will become unbalanced, resulting with voltage change on the outputs. Outputs of the Wheatstone bridge are routed to the operational amplifier, which serves as the buffer for the A/D converter. For this purpose, only a single channel of the MCP6022, a dual rail-to-rail op-amp from Microchip, is used. This op-amp is biased to half the power supply voltage and has a gain of 25. This buffered signal is then used as the input for the A/D converter. Magnetic linear click uses the MCP3201, a 12-bit A/D converter (ADC) with the SPI Interface, produced by Microchip. This
ADC has a high resolution which can be used even for more demanding applications. At 0°, the ADC will output half of its full-scale (FS) value, and it will swing towards 0 if the angle of the magnetic field is positioned towards the negative direction, and 4095 if the angle of the magnetic field is positioned towards the positive direction. This ADC has a dedicated voltage reference input pin, allowing ADC conversion within the range of the input signal. The converted output value can be read via the SPI interface, routed to the mikroBUS™ SPI pins for easy interfacing with a vast number of different microcontrollers (MCUs). This Click board™ can operate with either 3.3V or 5V logic voltage levels selected via the PWR SEL jumper. This way, both 3.3V and 5V capable MCUs can use the communication lines properly. Also, this Click board™ comes equipped with a library containing easy-to-use functions and an example code that can be used as a reference for further development.
Features overview
Development board
Nucleo 32 with STM32F031K6 MCU board provides an affordable and flexible platform for experimenting with STM32 microcontrollers in 32-pin packages. Featuring Arduino™ Nano connectivity, it allows easy expansion with specialized shields, while being mbed-enabled for seamless integration with online resources. The
board includes an on-board ST-LINK/V2-1 debugger/programmer, supporting USB reenumeration with three interfaces: Virtual Com port, mass storage, and debug port. It offers a flexible power supply through either USB VBUS or an external source. Additionally, it includes three LEDs (LD1 for USB communication, LD2 for power,
and LD3 as a user LED) and a reset push button. The STM32 Nucleo-32 board is supported by various Integrated Development Environments (IDEs) such as IAR™, Keil®, and GCC-based IDEs like AC6 SW4STM32, making it a versatile tool for developers.
Microcontroller Overview
MCU Card / MCU
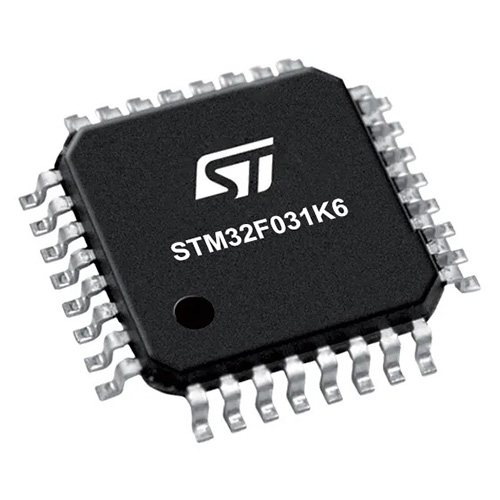
Architecture
ARM Cortex-M0
MCU Memory (KB)
32
Silicon Vendor
STMicroelectronics
Pin count
32
RAM (Bytes)
4096
You complete me!
Accessories
Click Shield for Nucleo-32 is the perfect way to expand your development board's functionalities with STM32 Nucleo-32 pinout. The Click Shield for Nucleo-32 provides two mikroBUS™ sockets to add any functionality from our ever-growing range of Click boards™. We are fully stocked with everything, from sensors and WiFi transceivers to motor control and audio amplifiers. The Click Shield for Nucleo-32 is compatible with the STM32 Nucleo-32 board, providing an affordable and flexible way for users to try out new ideas and quickly create prototypes with any STM32 microcontrollers, choosing from the various combinations of performance, power consumption, and features. The STM32 Nucleo-32 boards do not require any separate probe as they integrate the ST-LINK/V2-1 debugger/programmer and come with the STM32 comprehensive software HAL library and various packaged software examples. This development platform provides users with an effortless and common way to combine the STM32 Nucleo-32 footprint compatible board with their favorite Click boards™ in their upcoming projects.
Used MCU Pins
mikroBUS™ mapper
Take a closer look
Click board™ Schematic
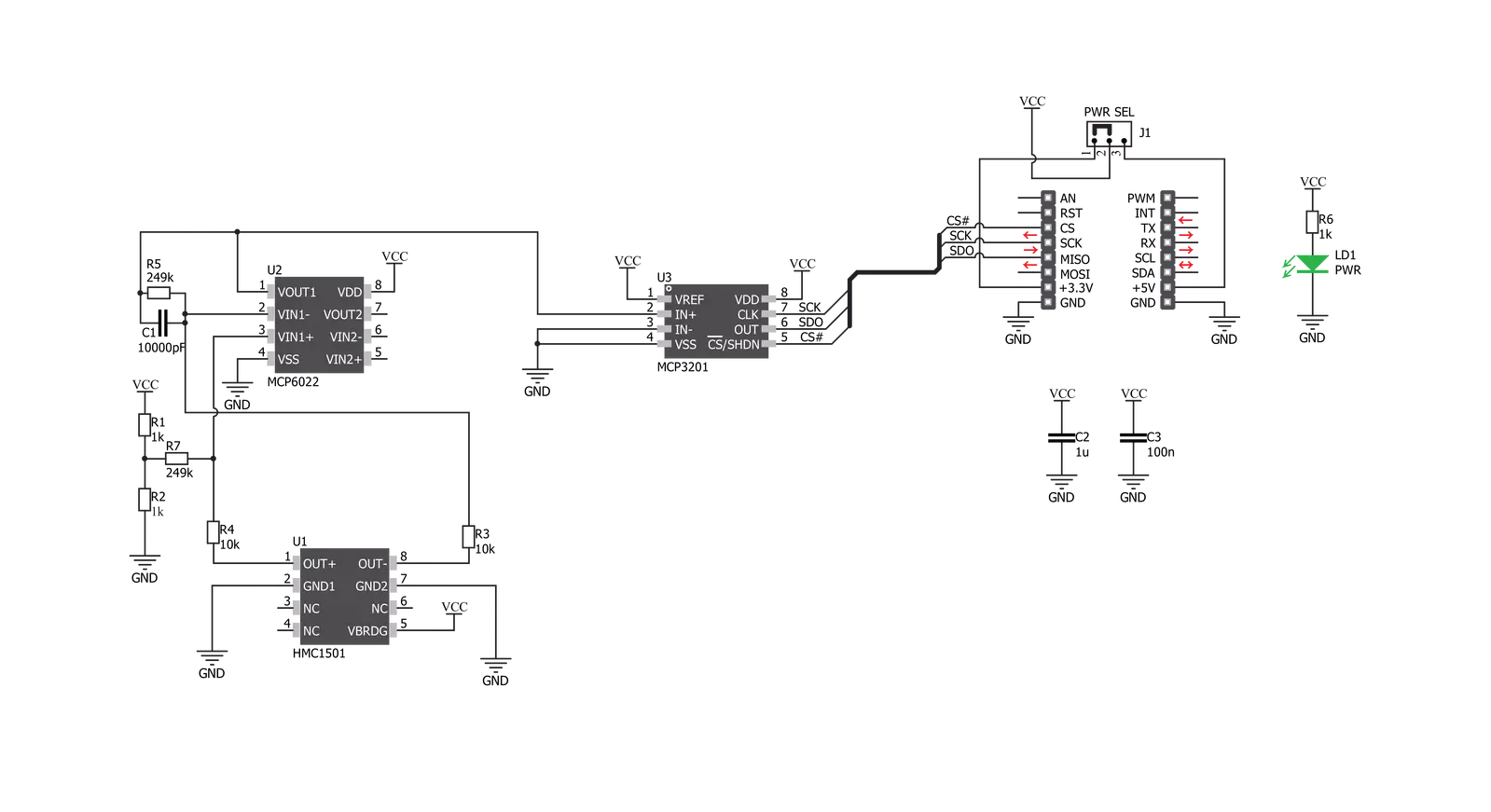
Step by step
Project assembly
Track your results in real time
Application Output
1. Application Output - In Debug mode, the 'Application Output' window enables real-time data monitoring, offering direct insight into execution results. Ensure proper data display by configuring the environment correctly using the provided tutorial.
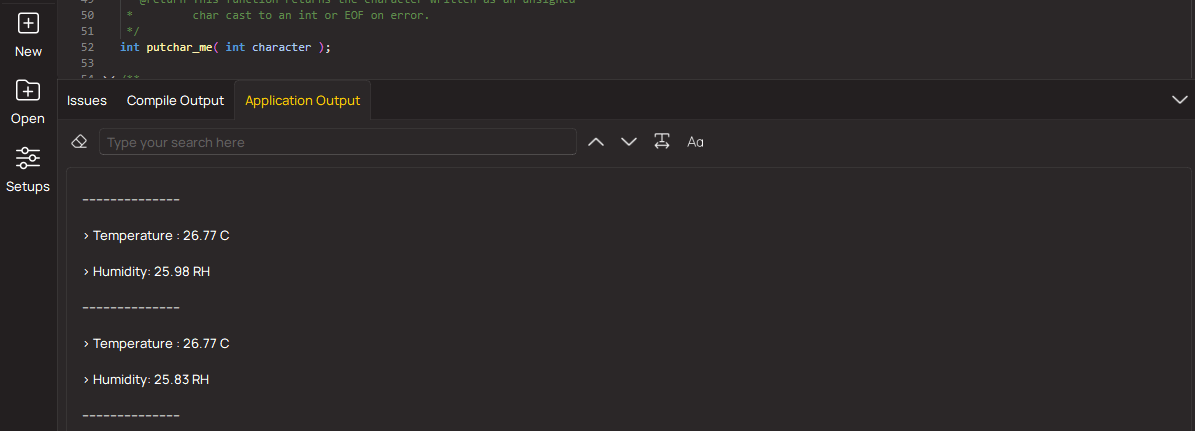
2. UART Terminal - Use the UART Terminal to monitor data transmission via a USB to UART converter, allowing direct communication between the Click board™ and your development system. Configure the baud rate and other serial settings according to your project's requirements to ensure proper functionality. For step-by-step setup instructions, refer to the provided tutorial.
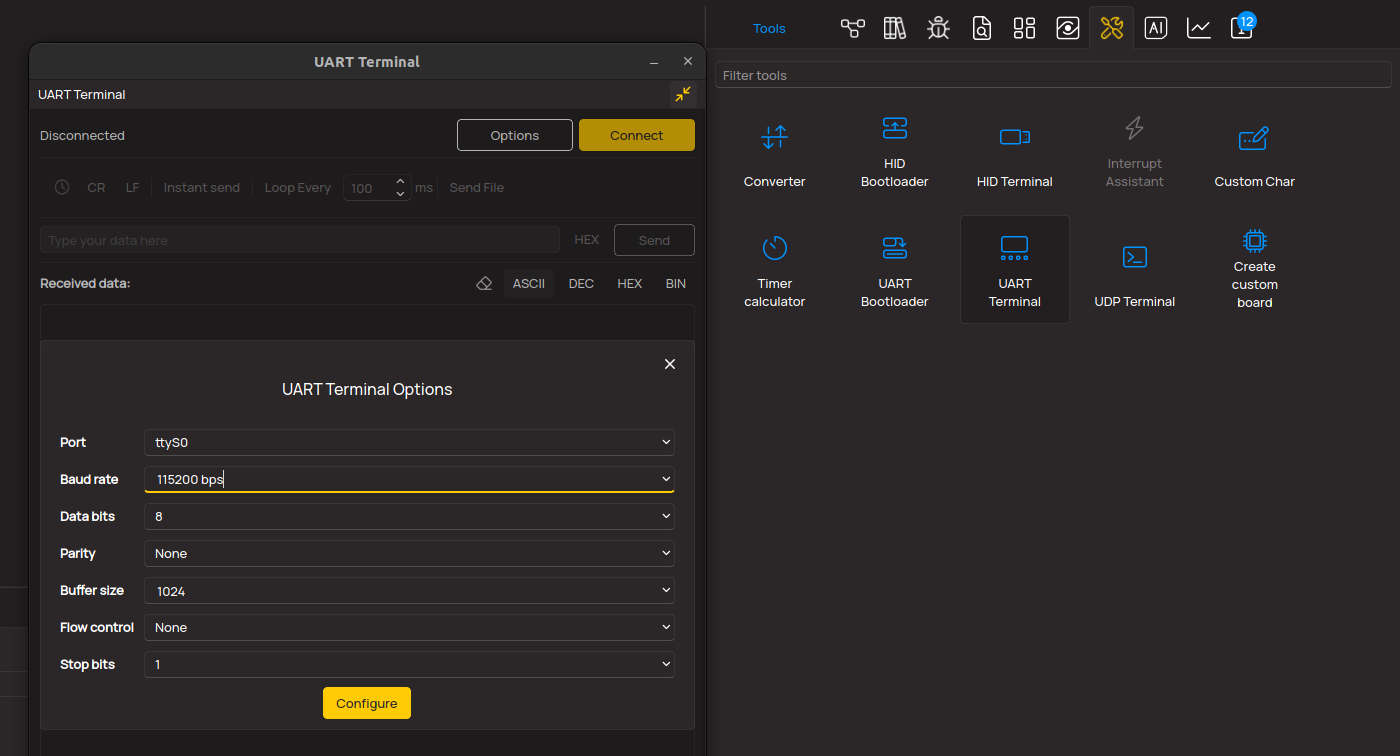
3. Plot Output - The Plot feature offers a powerful way to visualize real-time sensor data, enabling trend analysis, debugging, and comparison of multiple data points. To set it up correctly, follow the provided tutorial, which includes a step-by-step example of using the Plot feature to display Click board™ readings. To use the Plot feature in your code, use the function: plot(*insert_graph_name*, variable_name);. This is a general format, and it is up to the user to replace 'insert_graph_name' with the actual graph name and 'variable_name' with the parameter to be displayed.
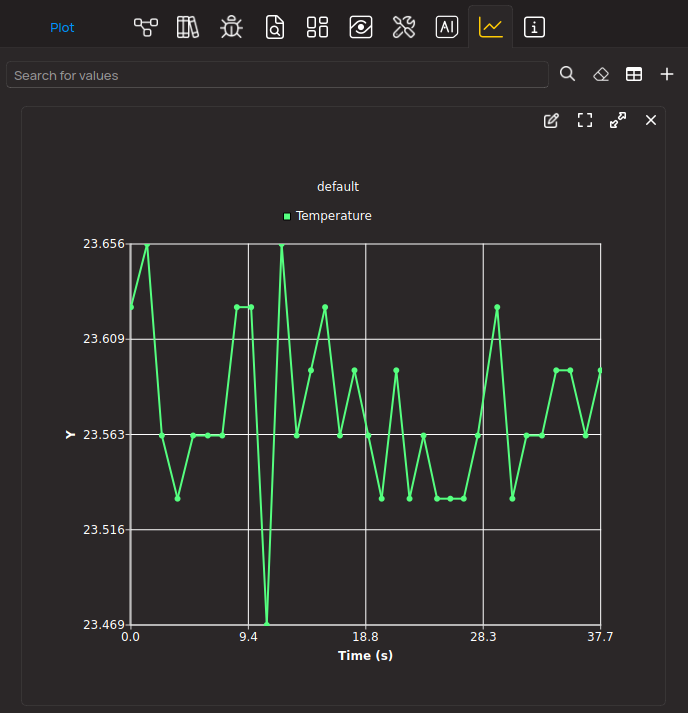
Software Support
Library Description
This library contains API for Magnetic linear Click driver.
Key functions:
magneticlinear_read_data
- This function reads Magnetics Linear data
Open Source
Code example
The complete application code and a ready-to-use project are available through the NECTO Studio Package Manager for direct installation in the NECTO Studio. The application code can also be found on the MIKROE GitHub account.
/*!
* \file
* \brief Magneticlinear Click example
*
* # Description
* This application reads magnetics linear data.
*
* The demo application is composed of two sections :
*
* ## Application Init
* Device initialization.
*
* ## Application Task
* Reads magnetic linear data and logs it to USB UART every 500ms.
*
* \author MikroE Team
*
*/
// ------------------------------------------------------------------- INCLUDES
#include "board.h"
#include "log.h"
#include "magneticlinear.h"
// ------------------------------------------------------------------ VARIABLES
static magneticlinear_t magneticlinear;
static log_t logger;
// ------------------------------------------------------ APPLICATION FUNCTIONS
void application_init ( void )
{
log_cfg_t log_cfg;
magneticlinear_cfg_t cfg;
/**
* Logger initialization.
* Default baud rate: 115200
* Default log level: LOG_LEVEL_DEBUG
* @note If USB_UART_RX and USB_UART_TX
* are defined as HAL_PIN_NC, you will
* need to define them manually for log to work.
* See @b LOG_MAP_USB_UART macro definition for detailed explanation.
*/
LOG_MAP_USB_UART( log_cfg );
log_init( &logger, &log_cfg );
log_info( &logger, "---- Application Init ----" );
// Click initialization.
magneticlinear_cfg_setup( &cfg );
MAGNETICLINEAR_MAP_MIKROBUS( cfg, MIKROBUS_1 );
magneticlinear_init( &magneticlinear, &cfg );
}
void application_task ( void )
{
uint16_t magnetic_data;
magnetic_data = magneticlinear_read_data( &magneticlinear );
log_printf( &logger, " Magnetic Linear data : %u\r\n", magnetic_data );
Delay_ms ( 500 );
}
int main ( void )
{
/* Do not remove this line or clock might not be set correctly. */
#ifdef PREINIT_SUPPORTED
preinit();
#endif
application_init( );
for ( ; ; )
{
application_task( );
}
return 0;
}
// ------------------------------------------------------------------------ END
Additional Support
Resources
Category:Magnetic